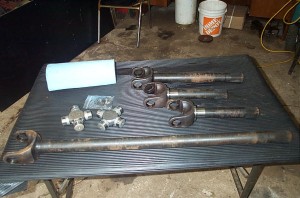 |
That, my friends, is the
"beef".
The guts of an ultimate Dana
60 front axle.
A great combo - Superiors and
CTMs |
|
 |
Old stock Spicer
30 spline stub top, below it the massive 35 Spline Superior Cr-Mo alloy
stub. |
|
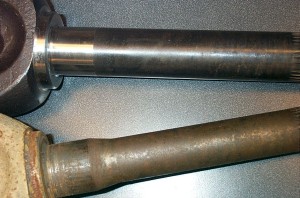 |
Maximum size - maximum strength. |
|
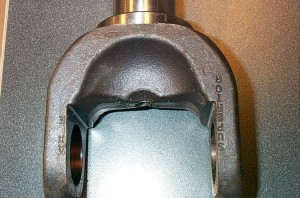 |
Recognize the genuine article
by looking for the word SUPERIOR AXLE stamped on the yokes. |
|
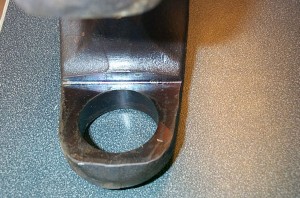 |
Yokes are pre-machined for full-circle
snaprings. |
|
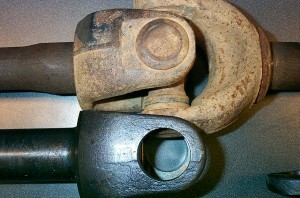 |
Here you can clearly see the
extra material around the U-joint bore - a critical area. |
|
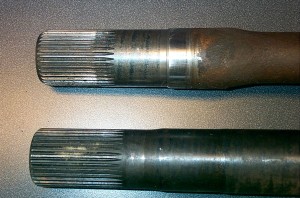 |
Spicer 35 spline inner shaft
top, Superior Cr-Mo shaft bottom. |
|
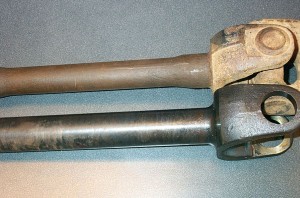 |
Comparison of Spicer (top) and
Superior 35 spline short-side inner axle shafts. |
|
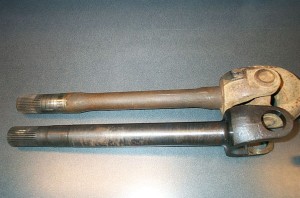 |
With better material, dual heat
treating, and much greater size the Superior shafts are vastly stronger
than stock axles. |
|
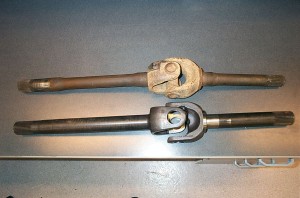 |
Comparison of short-side combo. |
|
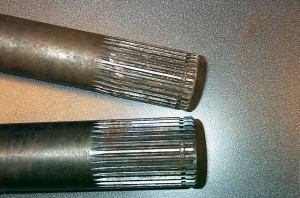 |
Comparison of stub-shaft
splines. Spicer top and Superior bottom.
Note: To meet the deadline
for this article, my stub axles had the splines hobbed, normal production
Dana 60 stub shafts will have rolled splines. |
|
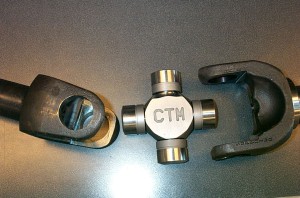 |
Like peanut butter and jelly... |
|
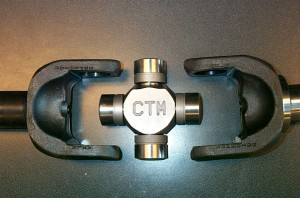 |
...pizza and beer... |
|
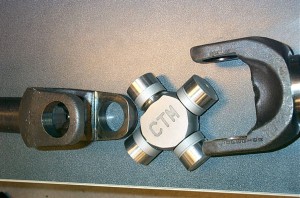 |
...the perfect combination!
Superior and CTM. |
|
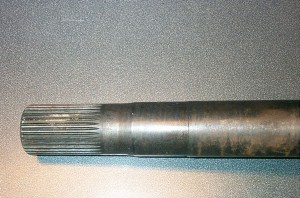 |
Splined end of Superior Cr-Mo
alloy Dana 60 axle, short-side inner; showing exclusive "torque equalizing"
profile (more dimensions and comparisons below)
The result is that the 2 different
length front axle shafts have much more similar load carrying capabilities
than the stock configuration; meaning ultimately that the whole assembly
is more durable and reliable. |
|
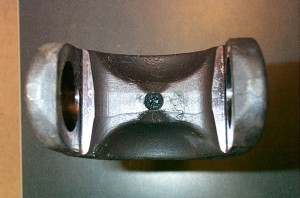 |
Maximum material retained in
the critical yoke are for strength and reliability. |
|
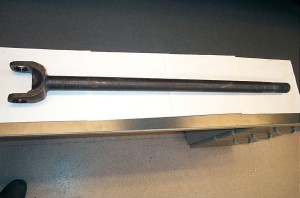 |
Superior Cr-Mo alloy Chevy Dana
60 long-side inner axle shaft. |
|
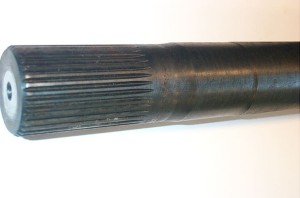 |
Splines and profile of Superior
Cr-Mo alloy Chevy Dana 60 long-side inner axle shaft .
To meet production schedules,
these axles were hobbed. Normal, non-custom length inner axles may
have rolled or hobbed splines, depending on production schedules. |
|
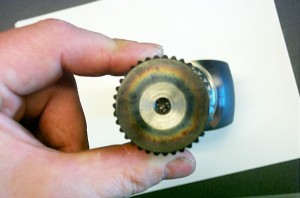 |
Cool picture of "rainbow
effect" caused by through-hardening process; seen on stub shaft. |
|
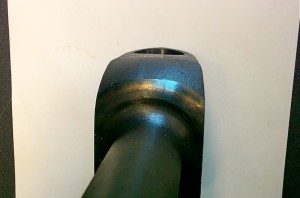 |
Look closely and you will
see the rainbow-effect of the heat treatment of the yokes (which few,
if any, other companies can or will do) - this is a major contributor
to the strength of the Superior shafts.
Non-hardened axle shaft yokes
deform under hardcore 4x4 loads, bearing caps spit out, U-joints break
and shafts rupture. For serious use, you need through hardened yokes. |
|
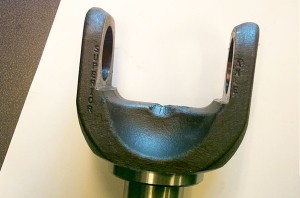
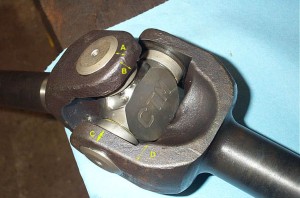
|
Yoke strength - not only THE
most critical aspect of a front axle shaft - but also where the Superior
shafts shine the most.
Space inside the knuckle is
extremely limited, but Superior found a way to add even more material
to the yokes in the most critical areas.
They are larger than Spicer
D60 shafts in every dimension I measured. The following pic and table
show the results of my measuring:
|
Spicer
35 spline |
Superior
Alloy |
A |
0.248" |
0.431" |
B |
0.517" |
0.589" |
C |
0.517" |
0.539" |
D |
0.482" |
0.489" |
|
|
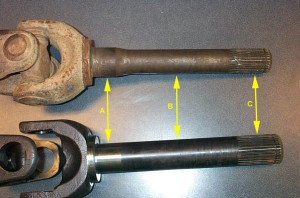
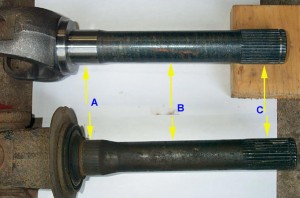
|
Here's a comparison
shot of the Dana60 30 spline stub shaft, the stock Spicer 35 Spline Dana70
stub shaft and the Superior Cr-Mo Alloy stub shaft. The dimensions in
the pic are:
|
stock 30
spline |
Spicer
35 spline |
Superior
Alloy |
A |
1.500" |
1.500" |
1.500" |
B |
1.258" |
1.377" |
1.494" |
C |
1.281" |
1.472" |
1.497" |
|
|
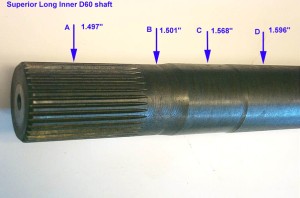 |
Comparison of Old Spicer,
New Spicer, and Superior Alloy Axle long-side inner shafts. Pic illustrates
Superior shaft.
|
Old 35
spline |
Spicer
35 spline |
Superior
Alloy |
A |
1.492" |
1.473" |
1.497" |
B |
1.494" |
1.441" |
1.501" |
C |
1.568" |
1.566" |
1.568" |
D |
1.318" |
1.584" |
1.596 |
|
|
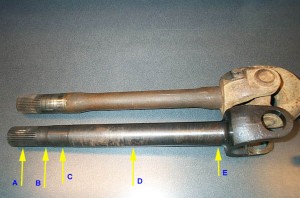 |
Comparison of old, Spicer,
and new Superior Alloy Axle short-side inner shafts:
|
Old 35
spline |
Spicer
35 spline |
Superior
Alloy |
A |
1.495" |
1.475" |
1.497" |
B |
1.495" |
1.445" |
1.497" |
C |
1.567" |
1.565" |
1.565" |
D |
1.318" |
1.590" |
1.595" |
E |
1.568" |
1.601" |
1.597" |
|
The Superior Alloy axles come with
a 2 year warranty.
Most, if not all, warranties are
designed to protect the consumer from defects in material or workmanship. fair
and simple. They are not designed to be "wear out" or "abuse"
insurance. It's reasonable to expect any MANUFACTURING defect to appear within
2 years - after that - you're on your own, and you got what you paid for.
That said, EVERY other component
used to date in the BV-60 and reviewed in this article comes with a no-question,
no quibble LIFETIME guaranty - essentially, if you break it, they replace it.
Period. That kind of guaranty says a huge amount about the companies confidence
in their product, and certainly makes it easier to pay the premium price commanded
for all these premium products.
I am sure that Superior have their
reasons for offering only a 2 year warranty, and it is, after all, purely their
business decision - but my opinion is that I and other consumers would be better
served by a longer, if not lifetime, warranty - the same as Poly Performance,
CTM, and Crane do.
Compared
to the Alternatives
Great products speak for themselves
- However, there
has been a bunch of talk recently about a newcomer to the Dana 60 alloy axle
playing field. A notorious "re-boxer" company have entered the
fray with what they describe as a "4340 Chrom-moly axle."
Now, I have bought re-boxed products before, and as long as I got parts from
an actual manufacturer I recognized and approved of, I couldn't care what box
they come in. In the case of these alloy axle offerings, things are not
so clear. No actual manufacturing company or plant or even location has
been made clear - at least certainly not to me; though it does seem almost certain
that they are being "manufactured" over-seas - likely in India or
other Asian location.
The thing is - these shafts are being
offered by big-name retailers at prices substantially lower than those of the
Superior shafts. So the immediate question is - how can they do this?
I immediately wanted to know so I did a little sleuthing, and came up with some
pics and info that pretty much answers the question: |
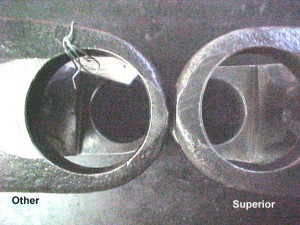 |
It seems the way to cut manufacturing
costs, and therefore retail prices, is to skimp on the material, process
and/or quality control.
Here we see the cheap offering
next to the Superior shaft. Note the lack of material around the yoke
bore in the other shaft. Worse than that - several of these other
shafts have ben measured by reputable sources, and it has been found that
the dimensions in areas like the material surrounding the yoke bore vary
by as much as 0.100" between samples....that's a TENTH of an inch
! |
|
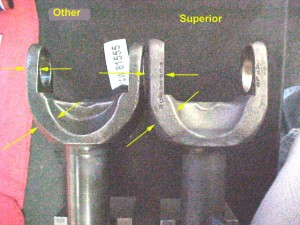 |
See for yourself
the differences, particularly in the area of the yellow arrows, as indicated. |
|
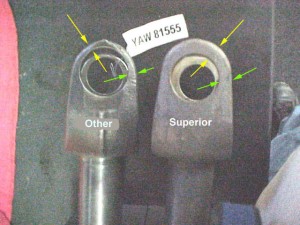 |
Again, the difference is
obvious.
So my question now becomes,
if design is substandard, manufacturing tolerance poorly controlled, and
the product made in some un-named place by an un-named company - what
assurance do I have that material selection and grade are up to par and
properly controlled - to say nothing of the complex machining and heat-treating
processes.
Answer is - it turns out Grandma
was right - nothing in life is free, and you get what you pay for.
I'll stick with Superior! |
Superior
Alloy axle and CTM U-joint Assembly
Naming Conventions |
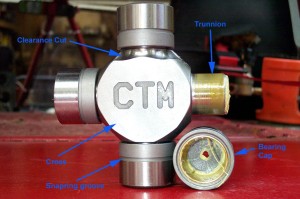 |
For clarity I have illustrated
the names I shall use for the parts of the CTM U-joint and kit in the
following pics to the left.
Here is a front view of the
joint... |
|
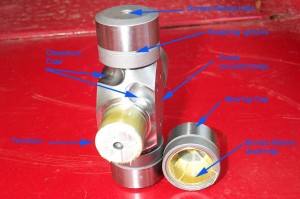 |
...a side view of the joint.
The main body I will call the
"cross", the bearing journals "trunnion", and the
bearing caps "caps". |
|
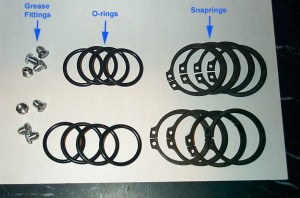 |
The supplied hardware kit.
Simple stuff, sure enough,
but by now you know I'm a fanatic for clarity and accuracy. |
|
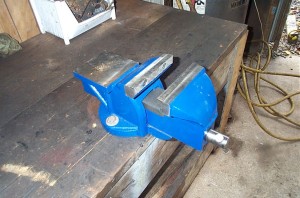 |
In the "tools
needed" section of the official instructions with the CTMs say "shop
press or good machine vice." I had a piece of junk bolted to
the bench where a vice should go, so I took this opportunity to rationalize
the purchase of a nice new vice.
Hey - when Axle Jack says get
a good vice...you get a good vice!
You'll want one with jaws that
open at least " |
|
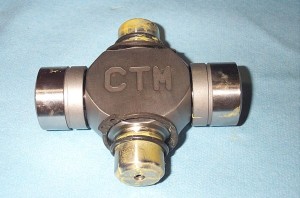 |
1. Take a joint, remove
a pair of opposing bearing caps, and onto each trunnion place a snapring
followed by an O-ring. |
|
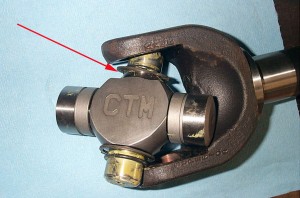 |
2. Hold the cross so the
CTM label faces you and the cut-out is at the top facing you. Place
the snapring in the cut out area (red arrow) and slip this trunnion into
the yoke first. |
|
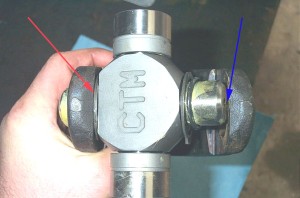 |
3. Even with the snapring
in the cutout (red arrow) clearance at the opposite trunnion will be very
tight (blue arrow). |
|
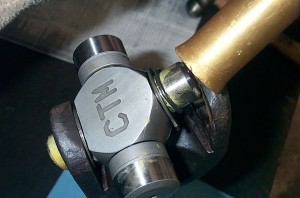 |
4. Use a brass or hardwood
drift to GENTLY tap the trunnion past the yoke... |
|
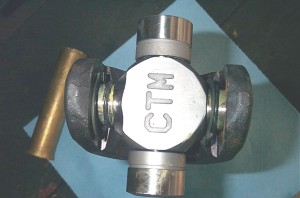 |
... until the U-joint sits fully
in the axle yoke. |
|
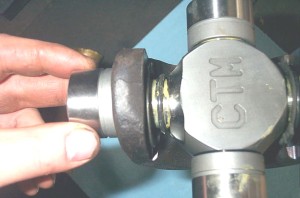 |
5. Carefully install a
bearing cap on the trunnion by pressing it through the hole in the axle
yoke. |
|
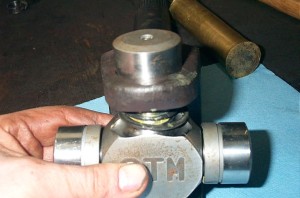 |
Start by using your fingers,
being extra careful to keep he trunnions, caps, and yoke bores all lined
up, and making sure the O-rings and snaprings aren't pinched or caught up... |
|
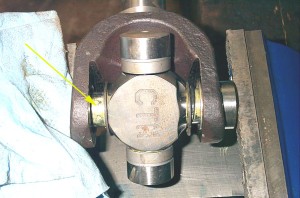 |
6. Once the cap is lined
up and finger tight proceed to press it in using your vice or shop press.
When doing the first one, be sure to use a rag to protect the end of the
opposite trunnion (yellow arrow) from being marred by the jaws of the vice. |
|
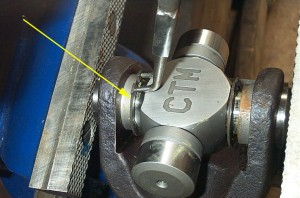 |
7. Pause partway once
the cap protrudes past the inside flat of the yoke. Spread the snapring
with pliers and slip it over the cap (yellow arrow). |
|
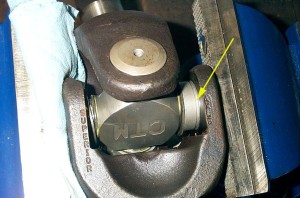 |
8. Continue to press the
cap on until the snapring groove (yellow arrow) is fully inside the yoke. |
|
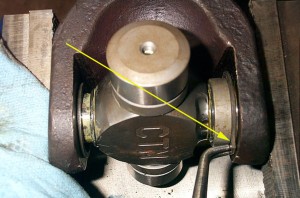 |
9. Install snapring in snapring
groove using snapring pliers (yellow arrow)
(snapring, snapring, snapring.....hmm,
funny - after you say it to yourself 36 times the word loses all meaning!) |
|
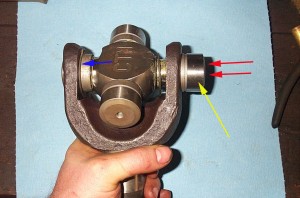 |
10. Place the other cap
on its trunnion (yellow arrow) and using the brass or hardwood drift tap
the joint in the direction indicted by the red arrows to seat the snapring
(blue arrow) tightly between the flat on the inside of the yoke and the
snapring groove in the cap. Set the cap and snapring in this manner
so that you cannot spin the snapring in its groove with finger pressure. |
|
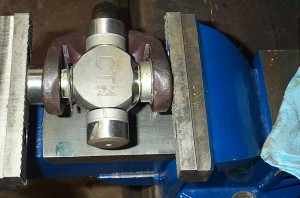 |
11. Continue pressing
the second cap on with your vice or press and continue as per the first
cap install. |
|
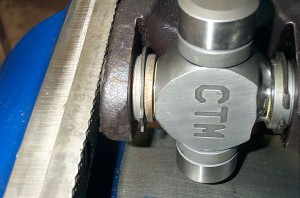 |
12. Remember to pause
and slip the snapring over the cap, press cap until snapring groove is visible
inside yoke, and insert snapring in groove. |
|
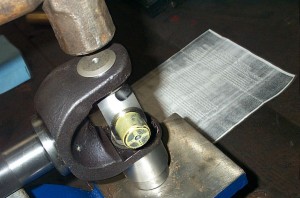 |
13. You must also press
joint back in opposite direction to seat cap and snapring. I found
it necessary to place cap over a large socket and tap the opposite cap to
seat the snapring. |
|
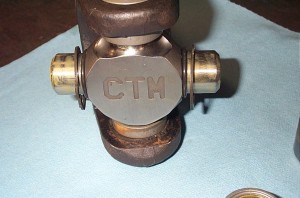 |
When you have finished installing
both snaprings and clips, the cross should rotate freely in the bearing
caps with no hint of bind, but you shouldn't be able to spin either snapring
in its groove just by trying to turn them with your fingers. |
|
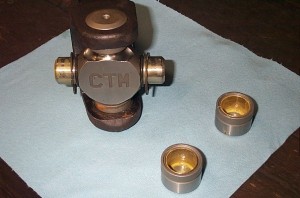 |
14. Continue by removing
the cpas from the remaining 2 trunnions, and installing an O-ring followed
by snapring onto both. |
|
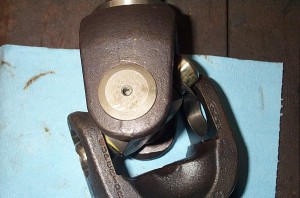 |
15. The trickiest part
of the CTM installation is getting the cross in the second yoke. Because
of the size of both the U-joints and the Superior Alloy shafts clearances
are quite tight. You will have to carefully align the trunnions with
the yoke bores... |
|
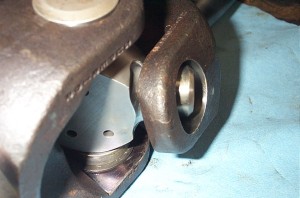 |
...and make use of the second
clearance cut-out (yellow arrow)... |
|
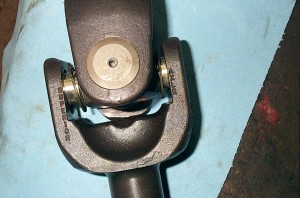 |
...too get the trunnions
to pop through the bores. But it will fit, just be patient, and
don;t hammer or force anything but feel free to apply a little persuasion
with a brass drift.
Not only is this trickiness
more than made up for by the fact that there are NO needle bearings do
drop, crush, get trapped etc - but if you're struggling, remember
that the parts fit tightly because of their maximum size and strength
- which is exactly what you want! |
|
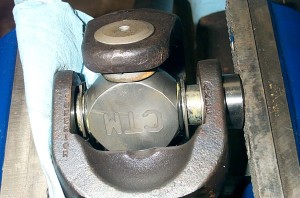 |
16. Once the cross is
situated in the yoke of the second axle, proceed as above to press on the
first cap. |
|
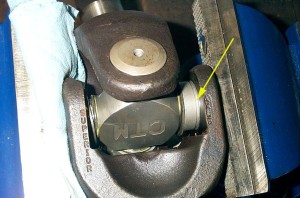 |
17. Stop when the snapring
groove is inside the yoke
Don't forget to frequently
pause and admire the amazing beef of your super-cool new axles and U-joints
;-) |
|
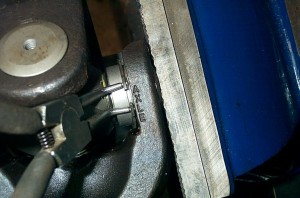 |
18. Install the snapring. |
|
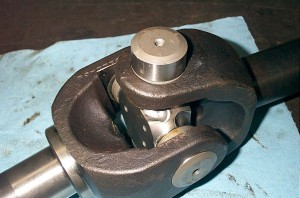 |
19. Install the final
cap. |
|
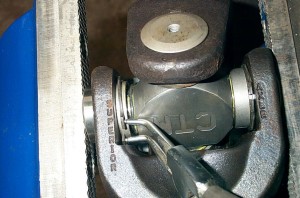 |
20. Final snapring in place. |
|
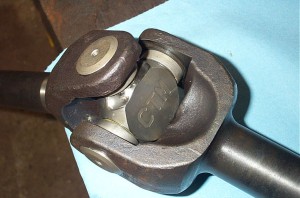 |
AWESOME!
Very cool, VERY beefy, - form
and function in one sweet package.
installing the CTM's was a
JOY! I have never had such an easy time installing U-joints. I didn't
have to force anything, no dropped needles, no getting the whole thing
assembled and one cap wont sit right and you realize a needle has fallen
over and you have trapped it - jeez I hated that! I love these joints.
Down with needle bearings I say! |
|
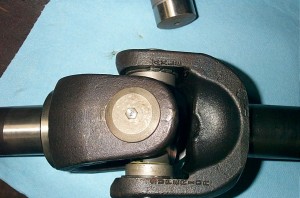 |
21. Install the grease
fittings in the ends of each of the caps and grease the U-joint at each
cap with a high quality synthetic grease. |
|
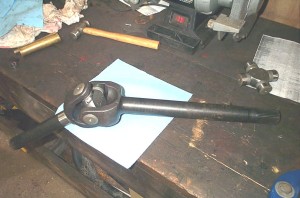 |
22. Before installing
the axle assemblies into the axle housing - do a final check that all yokes
move smoothly and freely with no binding; that all caps are greased and
grease fittings are installed; and that all snaprings are firmly seated
in the groove and do not spin under finger pressure. |
Corrosion
Protection |
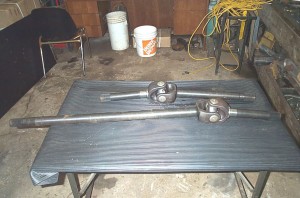 |
Corrosion protection
is extremely important for mechanical assemblies subjected to cyclical
loads and subject to fatigue, because small surface imperfections and
corrosion form stress raisers, from which fatigue cracks can develop.
Despite the "anti-corrosion"
black oxide coating the Superior axles come with, they are subject to
corrosion. After just a couple of weeks in my shop they bagan to
show light surface rusting.
This is nothing new - I'm convinced
it's a California thing - how could a Cali company develop a corrosion
resistant coating sufficient for the North Atlantic Canadian coast?
I live in one of the most corrosive environments there is - if you don't,
be thankful - EVERYTHING rusts here! |
|
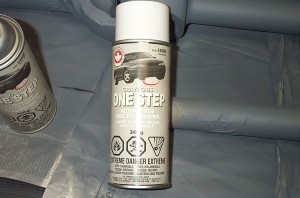 |
As such, I decided to take
the extra protective step of painting my axle shaft assemblies before
installing them.
To paint the steel in a meaningful
manner that has any hope of lasting, it is VERY important to use a high
quality self-etching zinc primer first. It costs 3-4 times what
the cheap grey primer does, but if you skimp here, you may as well not
bother as only the self-etching primer will properly adhere. |
|
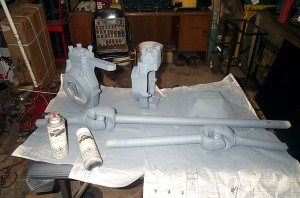 |
I did my knuckles, steering
arms, diff cover, and axles at the same time. |
|
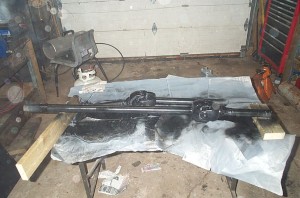 |
And then top-coated with a good
quality gloss black rust paint. |
Installation
My intent was never to make this
article a detailed installation article - I'm assuming that we're pretty comfortable
with axle R&R at this stage. However, should you wish to review or
study detailed information regarding the building of a D60 front axle, that
information is readily available in several articles I have written.
You can check out:
The
original Spicer D60 front axle maintenance manual
The
one ton axle tech manual compiled from US military manuals
The
Dana light axle service manual (torque and setup specs)
The
Dana 60 Bible
and my other tech articles:
Dana
60 front axle kingpin rebuild
Dana
60 front axle teardown
That said, here are a few pics of
the Superior/CTM assemblies being installed in the BV-60. |
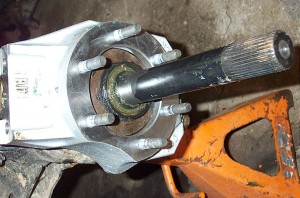 |
Slide axle assembly
through knuckle and into housing. Take care not to disturb the inner axle
seal with the inner end of the shaft.
There is a caution in the official
CTM installation instructions that mentions the possibility of having
to remove the grease fittings from the ends of the caps prior to installing
the assembly through the knuckle and into the housing. I found that
this wasn't necessary on my axle (1980ish Chevy D60 outfitted with Crane
knuckles.) |
|
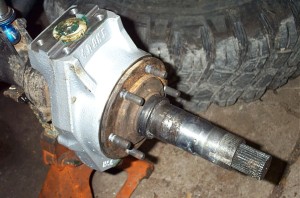 |
Install spindle over stub shaft. |
|
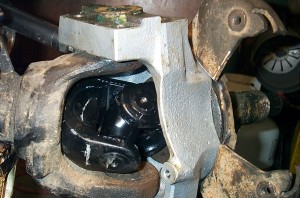 |
It is critical that you carefully
check clearances once everything is installed.
The knuckle must be cycled
from lock to lock while the axle is being rotated (a helper is enormously
useful here) while you carefully check to make sure that the axle/U-joint
assembly doesn't contact any part of the knuckle or axle housing at any
time. |
|
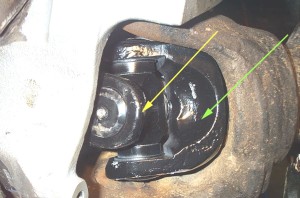 |
And also check to make sure
that there is no contact possible between the top of the yoke ears (yellow
arrow) and the bottom of the yoke on the opposite shaft (green arrow).
If there is any interference,
you will be able to see, hear, and feel it, and you must adjust your steering
stops to eliminate it. It is wise to allow a little extra clearance
to make sure nothing contacts under hard use where things may compress
a bit. |
FAQ
Q: Can I have these made in
custom lengths?
A: That is the cool thing about
these, they are available in custom lengths, but still have splines hobbed and
then heat treated, they are not just a cut-n-spline axle blank, it is truly
a custom made axle.
Q: Will these be available
for the '99-newer Ford Super duties, that run the seals and unitized bearing?
A: Yes, these axles will soon
be available for the newer SD front ends.
Q: why so spendy?
A: Ron Stobaugh, President of Superior
Axle & Gear Answers: We spent over three years and paid cash over $12,000
for forge dies and tooling for this admittedly low volume project. It was the
only way to make them right - no corners cut. We custom make these in a plant
that makes production runs of hundreds at a time - same amount of set-up on
all forging, CNCs, spline rolling machine, heat treat programs, precision grinding,
etc. except instead of hundreds of axles to amortize the set-up costs, we have
one or two at a time. The cost question is valid - I invite you to a free factory
tour - and then I believe you'll see for yourself. Bottom line: we made these
for hard core competition, and we know they'll do the job! |
|