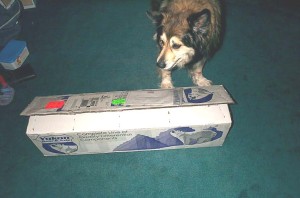 |
All of the gear
I ordered arrived in 2 large, heavy, well packaged boxes. Step one was to
have "Bear" give it the old once-over to make sure everything
looked good. She gave an enthusiastic "paws-up". |
|
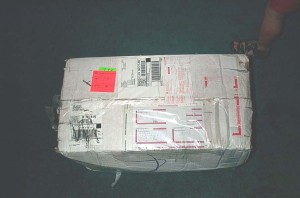 |
This box contained the stub
axles, U-joints, Warn 35 spline drive flange kit, kingpin rebuild kits,
stickers, and a Yukon catalogue. |
|
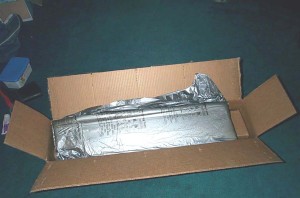 |
This box contained the inner
axle shafts. The shafts were wrapped in anti-corrosion paper, placed inside
boxes, those boxes were surrounded by packing foam, and placed inside another
box. Everything arrived in flawless condition - no shipping damage at all
- and that's all the way from Texas to Nova Scotia! I've said it before
many times - but I'm such a fan of well packaged goods. |
|
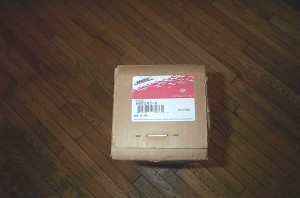 |
Actually, the parts themselves
came inside Dana/Spicer boxes that were inside the Yukon boxes. This box
contains the long-side inner shaft. |
|
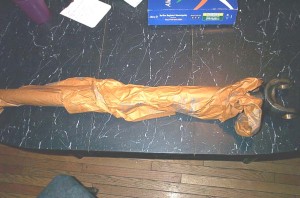 |
This is the long-side inner
shaft wrapped in its protective paper. It's also lying on the kitchen table
- I have such a wonderful, understanding wife! |
|
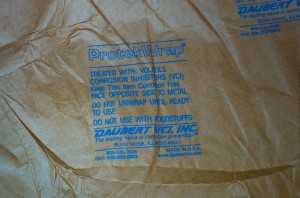 |
The wrapping is called ProtekWrap
and contains Volatile Corrosion Inhibitors... |
|
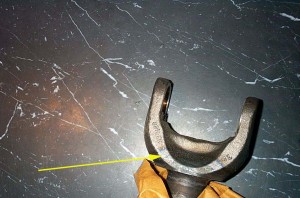 |
...whatever that means - it
works, there wasn't a spot of rust on the shafts, despite the raw machined
steel. |
|
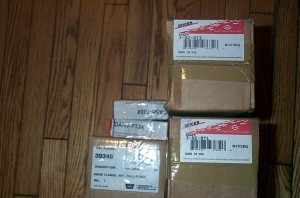 |
Here's the contents of the
35 Spline upgrade "kit":
- (2) 35 Spline stub shafts
(D70) Spicer part #: 3-82-871
- (2) Spicer "Life Series"
greasable 1480 series U-joints, Spicer part #: 5-733X
- (1) Warn 35 Spline Drive
Flange kit, Warn part # 39346
|
|
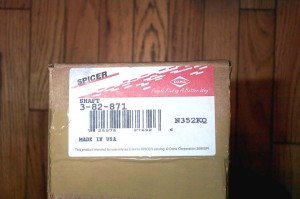 |
35 Spline stub shafts (D70)
Spicer part #: 3-82-871 |
|
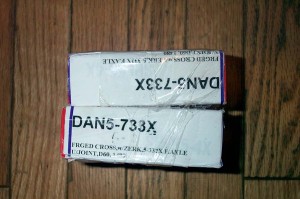 |
Spicer "Life Series"
greasable 1480 series U-joints, Spicer part #: 5-733X. This is the same
as part # SPL55-4x |
|
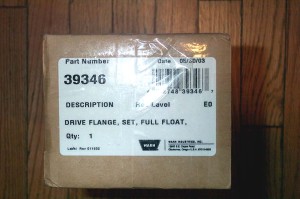 |
Warn 35 Spline Drive Flange
kit, Warn part # 39346 |
|
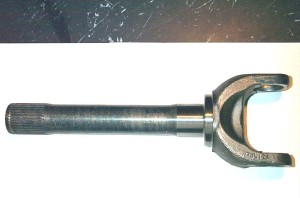 |
This is the 35 spline stub shaft.
It is HUGE compared to the stock 30 spline stub shaft, and should net an
approximate 40% increase in strength over the old stub. This is calculated
using the formula:Yield Torque (in/lb)= Tensile Strength (psi) x polar moment
of inertia/ radius of material and assumes same material and heat treat. |
|
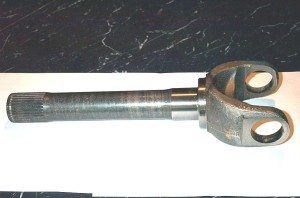 |
The Spicer shafts are made
from SAE1137 steel (not a true "alloy steel") and are induction
hardened. In this pic you can clearly see the blue circles along the shaft
that show the hardening.
From the "Machinery's
Handbook":
"Induction hardening is
done by placing the metal part inside or close to an "applicator"
coil of one or more turns, through which alternating current is passed.
The coil, formed to suit the general class of work to be heated, is usually
made of copper tubing through which water is passed to prevent overheating
of the coil itself. In most cases, the work piece is held either in a
fixed position or is rotated slowly within or close to the applicator
coil. Where the length of work is too great to permit heating in a fixed
position, progressive heating may be employed. Thus, a rod or tube of
steel may be fed through an applicator coil of one or more turns so that
the heating zone travels progressively along the entire length of the
work piece. " |
|
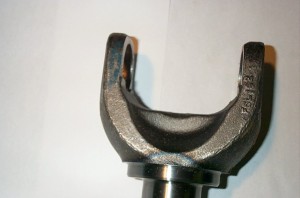 |
In this pic you can clearly
see the bluing that indicates the limit to the induction hardening of
the Spicer shafts. the shaft is passed through the coil, and the coil
has to be of a small enough diameter so that it is close enough to the
shaft to do the heating, but that diameter prevents the passage of the
yoke through the coil. |
Some more pics of the stub shafts:
|
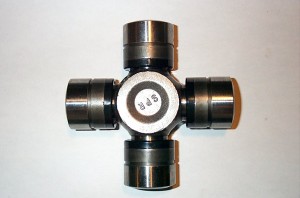 |
This is the Spicer Life Series
1480 series U-joint in greasable version. The older part number is Spicer
part #: 5-733X, which has been superceded by part # SPL55-4x. They are the
exact same part. Some shops are referring to these U-joints as "snap-tight"
because the new triple-locks seal is so good, the caps snap on really tightly.
Indeed, when I installed the U-joints, I had to use channel-lock pliers
to remove the bearing caps from the trunnions - I couldn't pull them off
by hand - that's how good the seals are. |
|
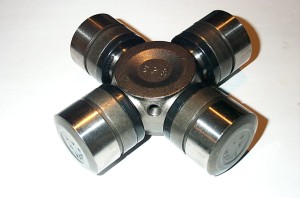 |
A great deal has been made
of these "new" style Spicer joints in the last year or so. You
will often see them referred to as the "new forged' or "cold
formed" U-joints. This is a bit of a misnomer, I think, because,
as far as I know, Spicer U-joints have always been forged.
Spicer refers to them as the
"Spicer Life" series. They do claim a 50% greater life due to
the improved seal. |
|
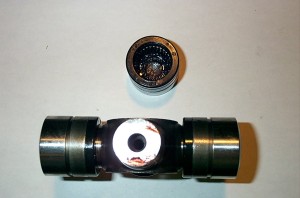 |
And they also mention "greater
torque carrying capacity", but give no figures on this. The greater
strength in part comes from the reduced diameter of the grease holes,
as seen in this pic. manufacturing process, metallurgy, heat treating,
and quality control procedures may all play a part as well.
Some conservative shade-tree
estimates have been made at 20-30% strength increase over the old style
U-joints. I personally have no idea if this is true or not, not having
the equipment to run proper testing myself. |
|
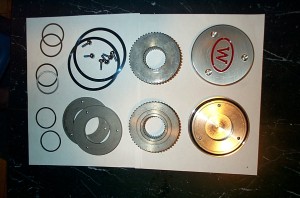 |
This is the contents of the
Warn 35 Spline drive flange kit. When I spoke to Greg, I hemmed and hawed
about whether to go with Warn 35 spline lockouts or drive flanges. On
the one hand - the lockouts are nice because of the flexibility they offer,
especially for a street driven or spooled front rig. On the other hand,
the drive flanges are undeniably simpler and MUCH stronger.
In the end I went with simplistic
and brute strength - was there ever really any question :-) |
|
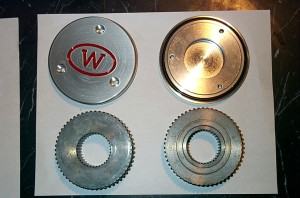 |
Whichever you decide, you
do have to purchase new 35 spline lockouts or drive flanges, as your old
30 spline units will not fit on the new stub shafts. |
|
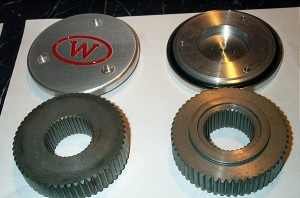 |
If you have 30 spline drive
flanges, you may be able to find a machine shop that can broach then to
35 spline for you.
The caps have a nice large
O-ring seal, and secure with 3 simple Torx screws. |
|
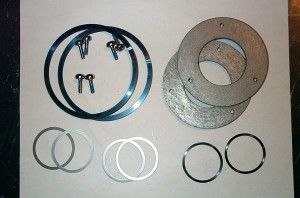 |
The kit also comes with (L top
R, top to bottom) large hub snap rings, cap screws with impregnated thread
locking compound, cap retention plates (to which the caps secure- see installation
later in article), 4 thrust/wear washers (2 for each side), and a pair of
small stub shaft snap rings. |
|
 |
Close-up of the drive flange
itself. |
|
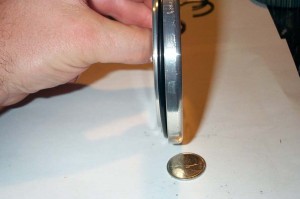 |
This shows one of my favourite
parts of the kit. The Warn drive flange caps are VERY thin (that's a quarter
in the picture), which means they stick out of the hub MUCH less than any
manual lockout would, which saves them from abuse amongst the rocks. |
|
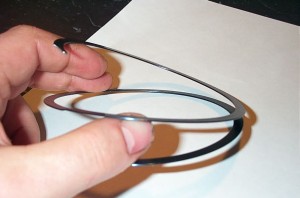 |
The snap rings included are
the "thin multi-wind" type. |
|
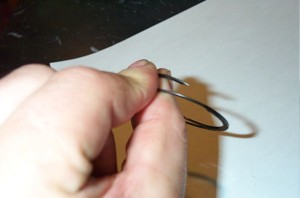 |
I much prefer these to the other type,
because you can install and remove them without requiring snap ring pliers
- just a small screwdriver will do. |
|
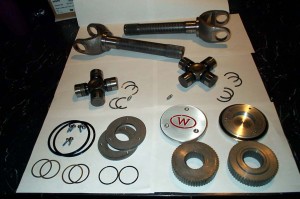 |
Complete 35 spline stub axle upgrade kit. |
|
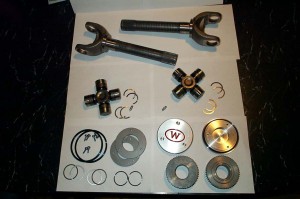 |
Complete 35 spline stub axle upgrade kit. |
Part
2 - Teardown |
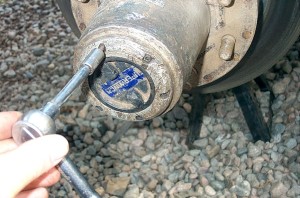 |
Start by removing
the 6 small bolts that hold the manual lockout cap on. They may be allen
head or Torx bits, depending on brand / age.
Just look at that tired, beat
up hub cap. I will not be sad to see the end of hassling with these things.
The Warn drive flange caps stick out far less from the end of the hub. |
|
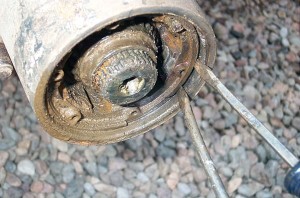 |
Once you have the cap off,
remove the 2 snap rings - one on the stub axle, and one just inside the
hub.
I find the "2 screwdriver"
method the best to lever out the big snap ring just inside the hub. Some
patience is required. The small snap ring in the end of the stub shaft
can be removed with a screwdriver, or with snap ring pliers if it is the
type with the holes for the pliers. |
|
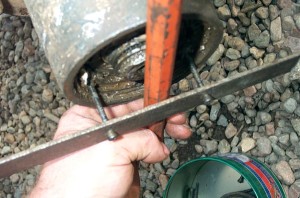 |
Once the snap rings are out,
you can remove the body of the manual lockout hub. If it is stubborn (as
most will be), you can easily fabricate a hub removal tool. I used a scrap
piece of 1" strap, drilled to take 2 of the hub cap screws, and a
big chisel behind it. To use it, just screw 2 screws back into the hub
through the tool, then put a bar or chisel behind it and yank out the
hub.
An interesting note, if you
drill the holes in the scrap for 2 adjacent holes in a D60 hub, it will
also work for D44 hubs, 3 holes apart. |
[NOTE: My photos
didn't turn out for the next 4 pics, so the photos shown are actually a
full-float rear axle, but the parts are exactly the same for this step,
so bear with me] |
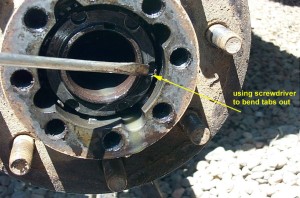 |
Once you have the locking
hub removed, the hub will look like this. Bend the little tabs on the
spindle lock-washer outwards so the outer spindle lock nut can be removed. |
|
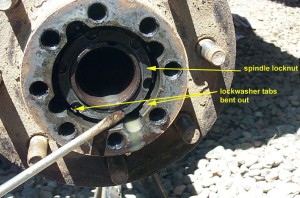 |
The proper way to remove
and install the spindle nuts is to use the proper 6-slot socket. of course,
if you're a high-tech redneck like me, you can bang them out with a hammer
and screwdriver!
Note - there are a huge number
of different lock washer and spindle nut arrangements out there. Some
are 6 slot as shown some are 4 slot, some are a large hex head and some
are a special rounded hex head. Also, some lock washers use tabs as shown,
and some have holes that index onto little "tits" on the spindle
nuts. You will have to adapt, improvise, overcome. |
|
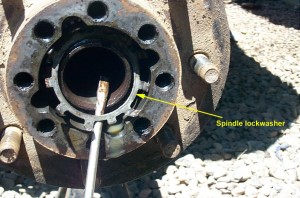 |
Once the outer lock nut is removed,
fish out the lock washer with a screwdriver / pick. |
|
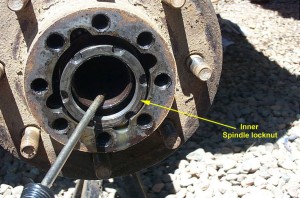 |
And then the inner nut can be
removed. Behind the inner nut will be a flat, indexing washer. Once you
have fished all that out and set it aside carefully, you are almost ready
to pull the whole hub/rotor assembly off the spindle. |
|
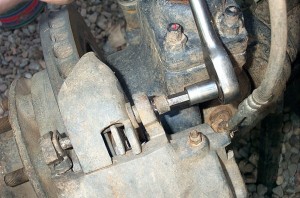 |
But first you have to remove
the brake calipers. There are several different styles. You may have to
remove caliper slide bolts as I did, or you may have to remove a grub screw
and knock out some locating wedges. |
|
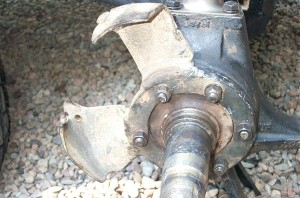 |
Once you have the caliper removed,
and the hub/rotor assembly pulled off (careful not to drop the outer wheel
bearing in the dirt as you slide the hub/rotor off), this is what you are
left with. |
|
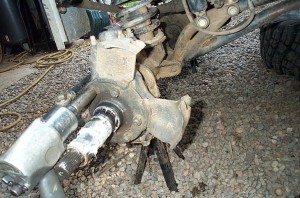 |
Remove the nuts that secure
the brake caliper mounting bracket and spindle to the knuckle. |
|
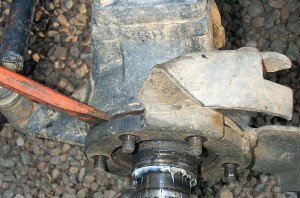 |
On a Chevy Dana 60, the brake
caliper bracket comes off first. I persuaded it with a large chisel. But
be careful not to beat things to death. |
|
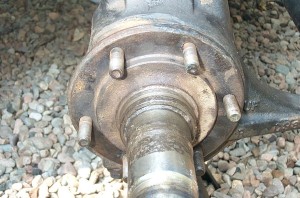 |
Finally, you can tap off the
spindle. You can use a soft-faced hammer to tap on the spindle itself, but
do not strike a bearing surface. On the GM Dana60, there is a notch in the
knuckle to allow for the large single-caliper 1 ton brake calipers, and
it provides a place to carefully strike the back side of the spindle to
help loosen / remove it. |
|
 |
The final step is simply
to grab the shafts, and gently slide them from the housing.
Be careful as you remove them
from the housing, so as to avoid damaging the inner axle seals. |
|
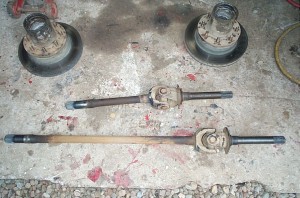 |
When you are all done, you'll
have the old axles removed, and ready to be replaced.
But first, let's compare the
old with the new, to make sure we're not just replacing these parts because
it's the latest cool thing to do, but because there's a good reason. |
Part
3 - Old vs New shafts
Please note that all dimensions and
measurements quoted here were measured by me with a pair if inexpensive digital
calipers. They are likely only accurate to within +/- .020 inches, and should
not be used for precise machining purposes or exact layout. They do however
clearly illustrate comparative differences. |
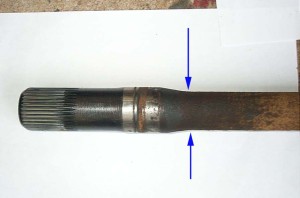 |
Here's the spline
end of the original, pre 1981 stock long-side inner front GM Dana60 shaft.
Prior to 1981 was when the shafts "necked down", which you can
clearly see in the picture.
One other thing is well illustrated
here. On an older axle shaft, even a 1981 and later "big" shaft,
there will likely be a lot of wear and corrosion. this can be a significant
weakness, as very often, when a shaft breaks, it does so at a place where
there is a stress riser - frequently caused by surface corrosion, nicks,
or flaws. That's why Drag racers polish their shafts to a mirror finish
- to remove surface stress risers. |
|
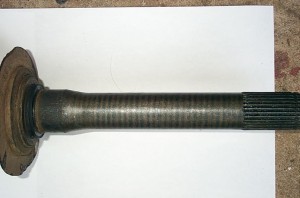 |
This pic of the stock Dana60
front 30 spline stub shaft also clearly shows where it reduces in diameter
to about 1.258"
It also shows quite well the
"bluing" marks on the body of the shaft created as the shaft
passes through the coil in the induction hardening process. |
|
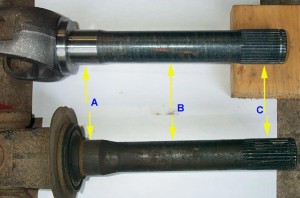 |
Here's a comparison shot
of the Dana60 30 spline stub shaft versus the 35 Spline Dana70 stub shaft.
Note that both are exactly 12.0 inches long.
The other dimensions in the
pic are:
|
Old 30
spline |
New 35
Spline |
A |
1.500" |
1.500" |
B |
1.258" |
1.377" |
C |
1.281" |
1.472" |
|
|
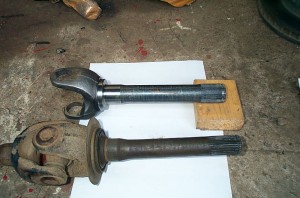 |
Another shot of the 2 stub shafts,
clearly showing how much bigger the 35 spline stub shaft is. |
|
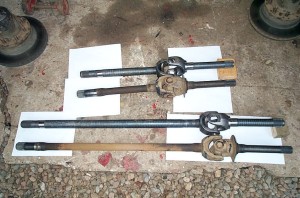 |
All the old next to all the
new. |
|
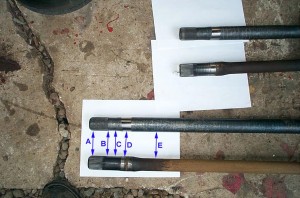 |
Comparison of old and new
long-side inner shafts:
|
Old 35
spline |
New 35
Spline |
A |
1.492" |
1.473" |
B |
1.494" |
1.441" |
C |
1.494" |
1.441" |
D |
1.568" |
1.566" |
E |
1.318" |
1.584" |
|
|
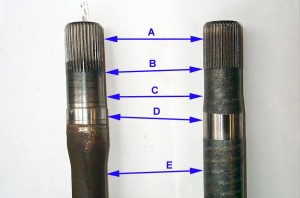 |
Comparison of old and new
short-side inner shafts:
|
Old 35
spline |
New 35
Spline |
A |
1.495" |
1.475" |
B |
1.495" |
1.445" |
C |
1.495" |
1.445" |
D |
1.567" |
1.565" |
E |
1.318" |
1.590" |
|
It seems odd, and I have no
hard factual or tech data to back this up, but the splines on the old
shaft actually "look better" to me. I don't know if they actually
are or not. But the real story is the dimension "E" - much larger
on the newer shafts! |
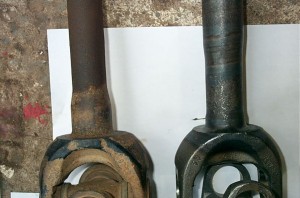 |
This comparison is actually
an interesting optical illusion. Because the main operating diameter of
the newer shafts is so much bigger than in the older shafts, it actually
appears as if the newer shafts are smaller at the yoke. this is not actually
true, and they are bigger, or at least the same size as the old shafts... |
|
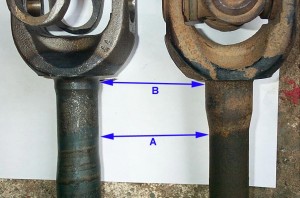 |
...as this picture and table
illustrates. These are the long-side inner axles.
|
Old 35
spline |
New 35
Spline |
A |
1.338" |
1.467" |
B |
1.568" |
1.601" |
|
|
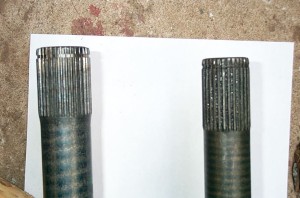 |
35 spline stub on the left,
stock 30 spline on the right.
Reason enough to buy the kit
right there! |
Here are a bunch
more comparison pics:
So it seems pretty clear, based on size, condition, lack of corrosion, and very likely improved manufacturing techniques and metallurgy over 25 years or more, that the new "big" inner axles and 35 spline stub shafts are a real and significant upgrade.
Part
4 - Assembling New Shafts and U-joints |
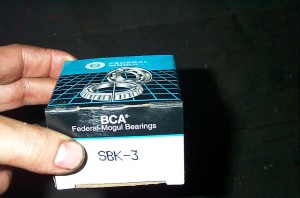 |
No sense in installing those
shiny new shafts with a bunch of old, rotted out seals and rusty bearings.
I purchased 2 spindle seal
and bearing kits locally. They can be a bit of a bear to find, so if you're
reading this Greg, it might be an idea to offer them as an add-on to the
35 spline kits.
I for one highly recommend
using all new bearings and seals, especially while you have everything
apart. |
|
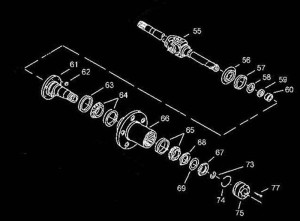 |
Here is an exploded diagram
and part numbers for the seals and bearings:
Diagram
# |
Description |
Dana
Spicer # |
Timken
# |
GM
# |
Ford
# |
56 |
Stone Guard |
37308 |
|
|
|
57 |
Inner
Spindle seal |
37311 |
710045 |
462811 |
D8TZ1175A |
58 |
Thrust washer |
|
|
|
|
59 |
Outer
spindle seal |
620062 |
710044 |
14012967 |
D8TZ1175C |
60 |
Spindle
needle bearing |
620063 |
B2414 |
1400967 |
D8TZ3123A |
57,
58, 59, and 60 |
Spindle
seal and bearing kit |
700014 |
SBK3 |
14009626 |
|
|
|
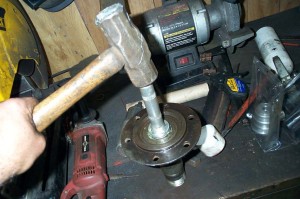 |
I use a small aluminum bearing/seal
driver and a BFH to install the new "Torrington" needle bearing
into the back side of the spindle.
Don't ask how I got the old
ones out - it was an embarrassing, frustrating, and altogether not very
technical mixture of heat, blunt objects, brute force and cussing. - in
other words - nothing at all you could learn from! |
|
 |
The metal "dust shields"
or "stone guards" or "slingers" are not included in
the spindle kit (but everything else is), so they have to be removed from
the old stub shafts and reused.
Alternatively you can order
new ones - the Spicer part number is 37308 (for GM and Dodge), and I expect
the Ford are exactly the same. |
|
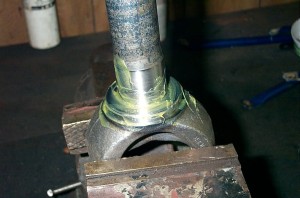 |
Grease the new stub shaft liberally. |
|
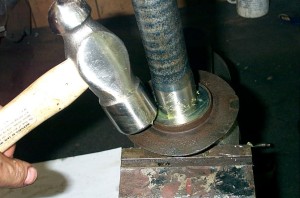 |
Tap the stone guard into place. |
|
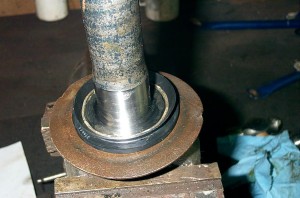 |
Then place the inner spindle
seal on with the lip facing out. |
|
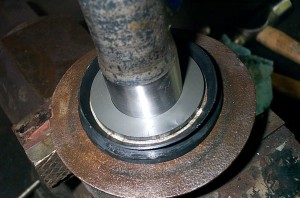 |
Next place the thrust washer
on with the "chamfer" facing in (or the perfectly flat side facing
out). |
|
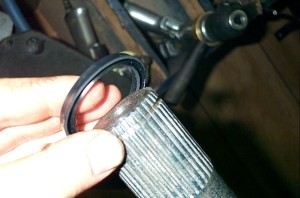 |
And finally, place the outer
spindle seal on with the lip facing in. |
|
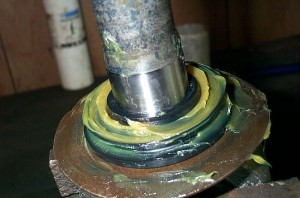 |
Then grease everything liberally,
ready to go into the back of the spindle. |
|
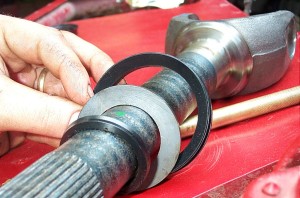 |
This picture clearly shows the order and orientation of the seals and washer. |
|
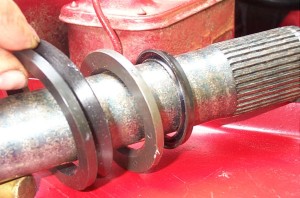 |
Another view of the order and orientation of the seals and washer. |
Once you have the stub shafts
all geared up, it's time to assemble the inner and stub shafts with the
new U-joints. |
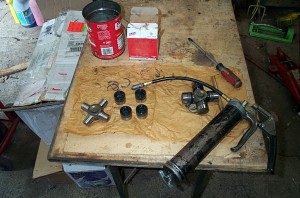 |
You will need a reasonably clean workspace, a grease gun, a large hammer, a large socket, and a small standard screwdriver. |
|
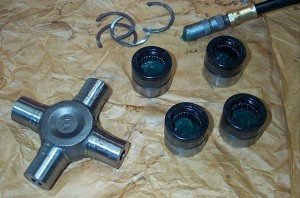 |
First, remove all the bearing
caps from the trunnions of the cross. With the new Spicer Life Series
U-joints, the seals are so good you may have to use pliers to remove the
caps - they are extremely hard to remove by hand.
Place a moderate amount of
grease in each cap. Do not go overboard, as excess grease in the cap during
assembly will cause excessive hydraulic force and make assembling the
U-joint very difficult. I just put a good dab in the cap then wipe it
around the needle bearings with a finger. the joint will be fully greased
after assembly. |
|
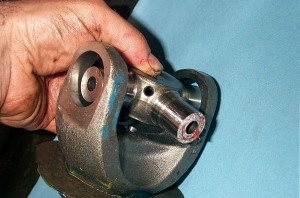 |
Place the cross in the bores
of the yoke of the stub shaft, with the grease nipple hole facing in (towards
the inner shaft). |
|
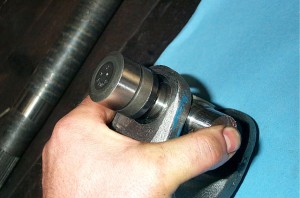 |
Raise the trunnion up in the
bore and place a bearing cap on it. |
|
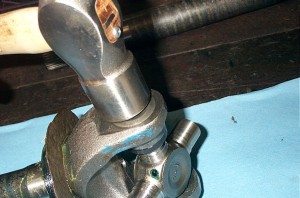 |
Drive the cap into the bore
with a hammer... |
|
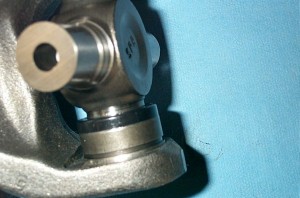 |
...until the groove in the cap
for the snap ring is visible inside the yoke. |
|
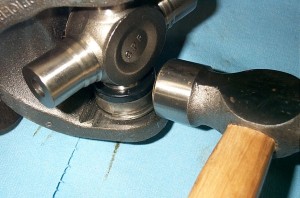 |
Tap the snap ring into place. |
|
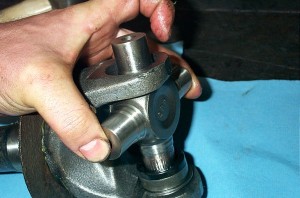 |
Raise the opposite trunnion
up in it's yoke bore. |
|
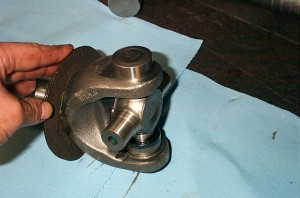 |
Place its bearing cap on. |
|
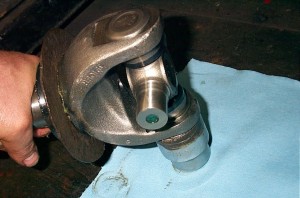 |
Then place the yoke, with the
bearing cap that already has its snap ring installed, on a large socket
whose ID is larger than the OD of the bearing cap... |
|
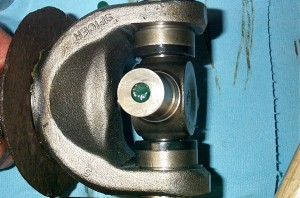 |
...and tap the other bearing
cap into its bore until the snap ring can be inserted
With both snap rings installed,
rotate the cross and check for binding. |
|
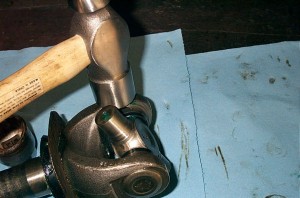 |
If the joint is tight, you can
attempt to relieve pressure by striking the ear of the yoke sharply. If
this fails to allow the joint to rotate firmly (not sloppily) but without
binding or over-tightness, you will have to disassemble and inspect. It
is likely that one of the caps may have a toppled needle bearing. |
|
 |
Place the stub shaft with
U-joint installed into the inner shaft yoke so that one of the trunnions
protrudes through the top of the bore.
Then essentially repeat the
entire procedure as above to install the other 2 bearing caps. |
|
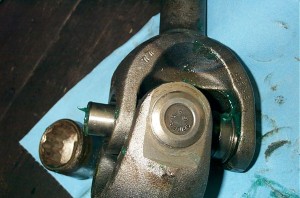 |
Here the last bearing cap is
about to be installed. |
|
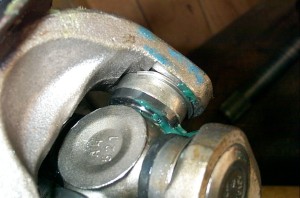 |
Be careful when installing
the snap rings that they are straight and properly seated in the groove,
otherwise you will bend one, like I did here, as you drive on the opposite
bearing cap. Doh!
When all the caps are on and
clips installed, install the grease nipple, the grease the joint until
fresh grease purges from all 4 seals. Then do a final check for any binding
in the U-joint. |
Part
5 - Installation |
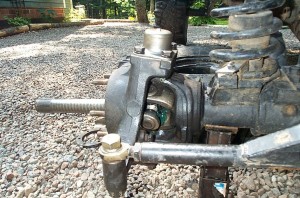 |
Installing the shafts
simply requires sliding them carefully back into the housing, again being
careful not to nick or damage the inner axle seals. |
|
 |
Once installed, they look like
this. |
|
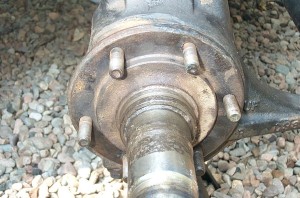 |
Re assembling the rest of the
components is simply the old "installation is the reverse of removal". |
|
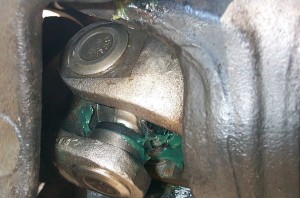 |
When everything is back together
(except the drive flanges), rotate the shaft in place and check to make
sure the U-joint turns freely between the knuckle and end forging, that
there is no binding or interference. Do this throughout the steering range
of the knuckles.
Ensure the grease fitting is
accessable and not interfering. |
|
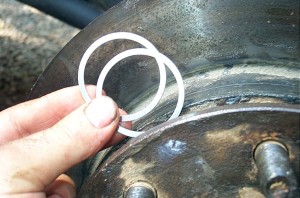 |
The last part of the assembly
is to install the new warn 35 Spline Drive Flanges.
First, take the 2 "wear
washers" (the small flat washers, not to be confused with the stub
shaft snap rings)... |
|
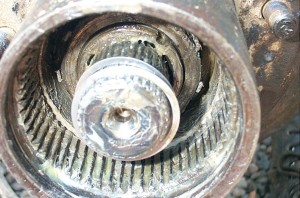 |
...and place them over the stub
shaft. |
|
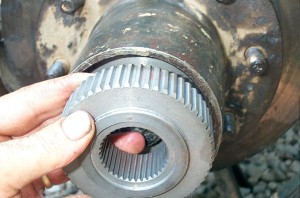 |
Then slide the drive gear in
place over the stub axle. You may need to rotate the axles slightly to get
the stub shaft splines, drive flange, and hub splines all lined up. |
|
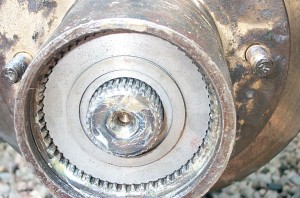 |
Fully installed it looks like
this. |
|
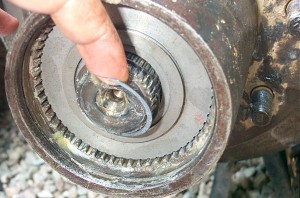 |
Next place the stub shaft snap
ring over the end of the stub shaft and into the groove. |
|
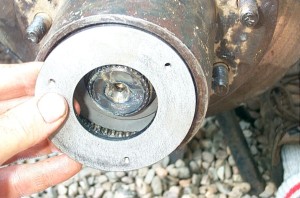 |
Then place the drive flange
cap retention plate in the hub... |
|
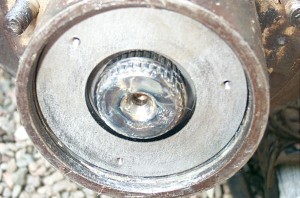 |
... and install the big outer
snap ring. |
|
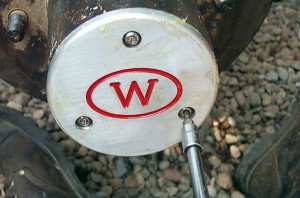 |
The last thing to do is tighten
down the #8 Torx screws that are pre-impregnated with thread locker. |
|
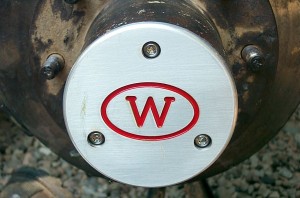 |
And you're done!!! |
|
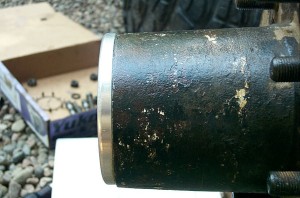 |
It's AWESOME how much less
protrudes from the hub with the 35 spline drive flanges compared to lockout
hubs.
And of course, having the biggest
35 spline axles throughout brings a lot of peace of mind... |
Part 6 - Testing
...And that peace
of mind is great to have when you like to go out and Fully Get It like I do.
Here are some shots and a short video clip of my first 2 runs since the install.
From high torque, 110:1, crossed up, full-lock, bound-up rock crawling, to 6000
rpm full-throttle assaults on slick, muddy, rocky hill climbs - I did my best
to break something...but everything has held up extremely well so far, and I
really enjoy the extra clearance with the drive flanges tight to the hub body.
Check out the pics. |
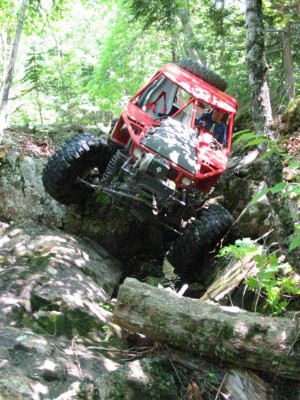 |
Full lock, and
throttling through a tight spot. Murder on joints and shafts...but not a
problem for me now! |
|
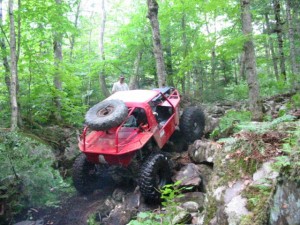 |
A tough rocky climb - tried
several ways - from crawling to throttling. |
|
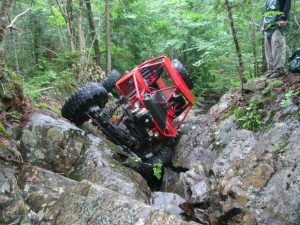 |
Another brutal, low-low gear,
caught-in-a-crack, rock crawling spot. I *may* have needed a spot of help
to get out...but I didn't break, and I gave it hell trying! :-) |
|
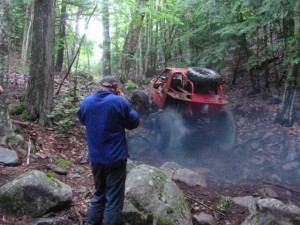 |
Check out the smoking tires.....I
love being able to attack things with confidence when required. that's why,
as I mentioned way back in the beginning, I don't believe in designing in
a weak link...let my courage be the weak link! |
|