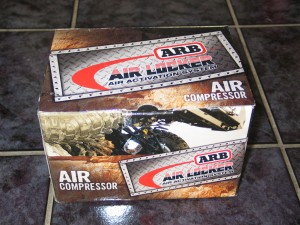 |
The kit comes in
the typical top-quality packaging one comes to expect from ARB. |
|
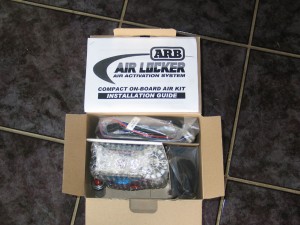 |
Inside are all the
pieces required, including an excellent set of instructions and clearly
labelled wiring harness. |
|
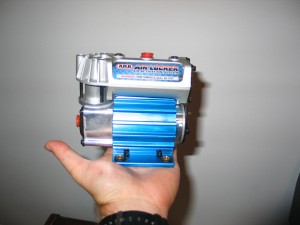 |
The compressor itself
is extremely compact - perfect for squeezing into the tight space available
in a buggy, and also easy to mount under the hood (or anywhere else) in
more conventional rigs. |
|
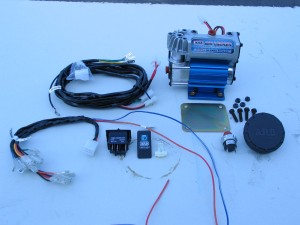 |
The kit contains
(clockwise from top right) the compressor, mounting plate and hardware,
air filter, pressure switch, dash-mount activation switch and wiring harness. |
The kit and instructions are supplied
for installation using the standard ARB electrical locker-activation switches
and solenoids.
In my opinion, this method is at
its best when installing ARB air lockers into rigs with interiors and dashes
that are clean and well laid out - such as in late-model rigs with near-stock
interiors. The ARB dash switches are nice clean pieces and by using electrical
solenoids for activation the switches can be neatly fitted into the dash or
console and everything else can be tucked away. |
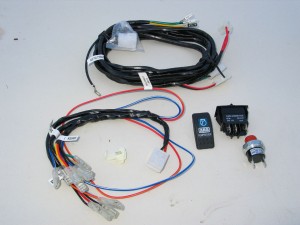 |
A close-up of
the wiring harness and switches.
For my installation I wanted
to do a "full pneumatic" system - that is, a system where there
are no solenoids used, everything downstream of the compressor is pneumatic
only, and the only electrical part of the system is the power to run the
compressor.
More on this later - for now,
the important thing to note is that the supplied wiring harness, as seen
at left, comes in 2 parts and will have to be modified if not following
the ARB electro-pneumatic route. To help keep things clear, I call the
larger portion of the harness (at the top of this pic) the "compressor
harness" and the smaller section the "switch harness" (where
'switch' refers to the compressor activation switch). |
|
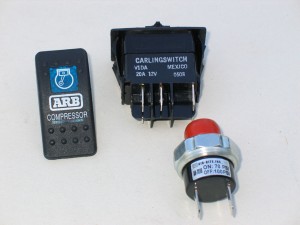 |
The dash-mounted,
compressor activation switch (left) and the compressor's pressure switch.
The compressor activation switch
is used to turn the compressor on or off and is used in both electro-pneumatic
installations as well as full pneumatic systems.
The pressure switch installs
in the compressor's small tank and, with the dash mount switch on, automatically
switches the compressor on when the tank pressure falls below 70psi and
switches it off when the pressure reaches 100psi. |
|
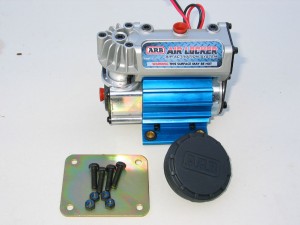 |
The compressor,
mounting plate, and air filter. The air filter is used to filter the incoming
air to the compressor. |
|
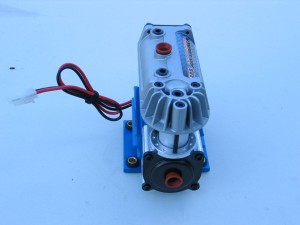 |
End view of the
compressor. Note the two red rubber plugs - one on top where the pressure
switch screws in, and one on the end where the air filter screws in. |
|
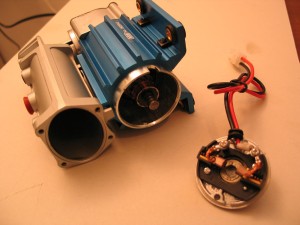 |
If we take the end
cap off the unit we can see inside the small storage tank (left) and the
electric motor. |
|
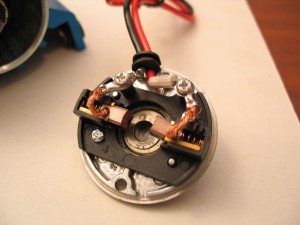 |
Close-up view of
the motor's brushes - which are available separately and are user-serviceable
That said - you need some skill and a big chunk of patience to finesse the
brush cover back on - be warned!! |
|
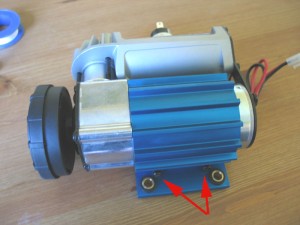 |
One of the coolest
features of the compressor is the fact that you have 270° of freedom
in choosing how to rotate the compressor in its mount.
By loosening the two small
hex-head motor mount screws (red arrows) you can loosen the mount and
rotate the compressor in the mount anywhere from 90° to the left,
through vertical, to 90° to the right. |
|
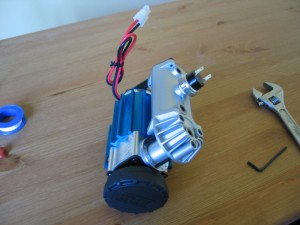 |
Here the compressor
is rotated about 45° to the right in its mount. |
Preparing
the Compressor for Installation |
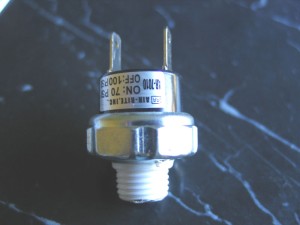 |
Unpack the kit
and lay it all out on a clean work surface.
Remove the caps from the pressure
switch and wrap the threads with Teflon tape. |
|
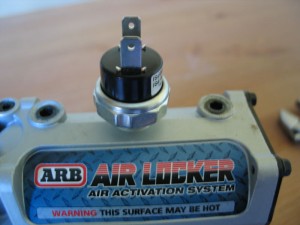 |
Remove the rubber
plug from the port on the top of the tank and install the pressure switch.
Snug it up but don't strip the threads! |
|
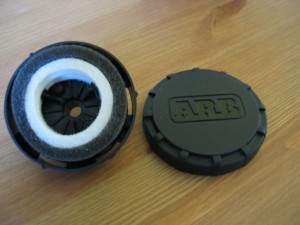 |
Snap the two halves
of the air filter together, being sure to line up the slots. |
|
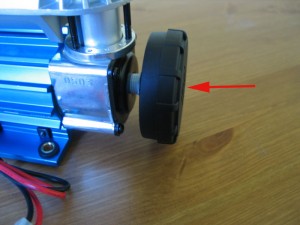 |
Apply Teflon
tape to the threads of the air filter, remove the red rubber plug in the
end of the compressor, and thread in the air filter.
Note that you can also thread
in a 1/4" NPT hose barb and use a length of tubing to relocate the
air filter to a more suitable location. This can be useful should, for
example, you choose to mount the compressor in a hot, dirty engine bay.
The ARB manual contains details on max allowable lengths for different
diameters of tube. |
|
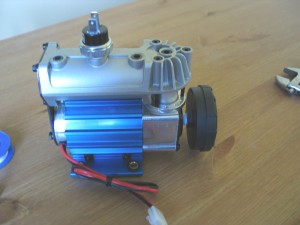 |
Ready to install,
the compressor looks like this. |
Modifying
the Harness for a Full Pneumatic Installation.
If you are using ARB's locker activation
switches and solenoids, you simply follow the supplied installation instructions
which are complete and very good. Obviously no modifications are necessary.
However, in a pneumatic installation,
much of the supplied wiring harness is unnecessary. Essentially, all you need
is the part that connects a fused 12V+ source to the compressor through the
dash-mounted activation switch and pressure switch, along with ground connections
and a dash-lighting 12V source to illuminate the switch. |
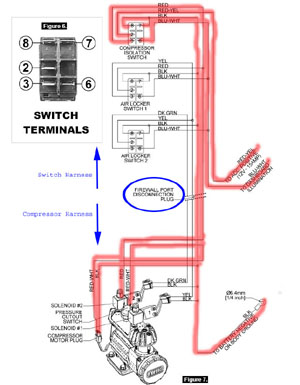 |
This diagram,
from the ARB manual, illustrates the wiring for the compressor. The portions
highlighted in red are those that you need to retain for a full pneumatic
installation. Note that the "Firewall Port Disconnection Plug"
is the place where the "switch harness" (upper part of the diagram)
connects to the "compressor harness" (lower part of the diagram).
To modify the harness as shown,
you essentially just cut off the unneeded parts - those that connect to
the solenoids and the ARB dash-mount locker-activation switches. |
|
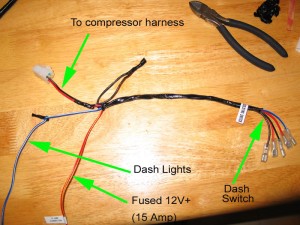 |
The modified
switch harness looks like this. |
|
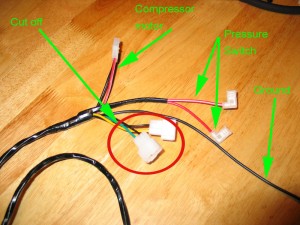 |
To modify the
compressor harness, cut off the 2 solenoid connectors (circled in red)
as they will not be needed. |
Pneumatic
Activation
So why go to all the trouble of modifying
parts and sourcing and plumbing special pneumatic switches? Simplicity and reliability
are my answer. As I mentioned, the ARB electro-pneumatic activation system is
very clean and professional looking and seems to have been designed with an
eye to integrating cleanly and neatly into existing interiors. As you shall
see, running full pneumatics from the compressor to the locker activation switches
to the lockers is not nearly as neat and clean. However, the electro-pneumatic
system does employ more parts, more wiring, and in particular solenoids that
could represent a possible failure point.
So, if you have a buggy you beat
the daylights out of, one with no real clean dash to mess up with bulky pneumatic
switches, a rig that could hardly be called "weather-proof" that you
run hard in all kinds of brutal conditions - from smashing rocks to mud and
deep water, you already know that eliminating any and all possible points of
failure is a good thing.
That's the case with my rig - so
I decided on a full pneumatic system. What this means is that air is supplied
by the compressor, and is controlled through a pneumatic switch (much like a
small hydraulic valve) on the way to the locker. It's a purely "manual"
system, with no additional electronics involved.
The key to such a system is, of course,
the pneumatic switch itself. There are many different kinds available on the
market that are suitable - and they can be purchased everywhere from tractor-trailer
suppliers to hydraulics/pneumatics shops to good on-line retailers such as McMaster-Carr.
Of course, the first thing we need
to do before ordering a suitable switch is to understand the terminology associated
with pneumatics, the type of switch we need, and how to read a pneumatic switch
diagram. Think of this as being similar to electronics - in that it would be
hard to order an electrical switch or solenoid if we couldn't read or understand
an electrical diagram.
The proper name for a "pneumatic
switch" is a "directional control valve" (I shall use the terms
"switch" and "valve" interchangeably when discussing pneumatic
control valves). A directional control valve has a valve body, internal passages,
and a sliding spool. The sliding spool will connect and disconnect internal
flow passages within the valve body resulting in the control of airflow direction.
Note that it doesn't throttle or meter the airflow or regulate the pressure
- it just changes the direction of the airflow. |
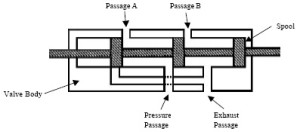 |
This diagram
shows a typical directional control valve.
Air pressure is supplied to
the Pressure Passage.
Depending on the position of
the sliding spool this airflow is either connected to Passage A while
Passage B is connected to the Exhaust Passage, or the airflow is connected
to Passage B while Passage A is connected to exhaust. |
|
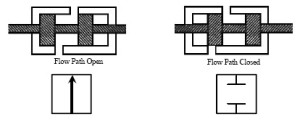 |
Directional control
valve's are normally classified according to the number of possible flow
paths or "ways" they have.
The simplest example is a 2-way
control valve.
Obviously, this type of valve
has only 2 possible paths - flow path open or flow path closed. In other
words - "on" or "off". |
This diagram illustrates a
2-way valve and shows the ANSI symbols for each of the valve's positions.
Often, in describing a directional
control valve, we also include the number of positions the actuator has.
This simple valve illustrated at left would be described as a "2-way,
2 position" valve. |
In order to actuate our ARB air lockers,
we need a slightly more complicated switch.
As we know from reading the ARB
Install Part 1 - ARB 14-Bolt Air Locker Install article, in order to operate
an ARB we supply it with air pressure to lock it, and exhaust this pressure
so that it unlocks via the internal return springs. Knowing this, we can see
why a 2-way switch won't work - because in either position there is no path
for the air to exhaust, so, regardless of the switch position, the locker would
remain pressurized and locked. |
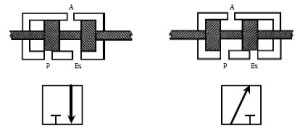 |
What we need
is a 3-way, 2-position valve. A 3-way, 2-position valve will alternately
pressurize or exhaust a single port. In the case of our ARB - when the
actuator is in one position, pressure is supplied to the port and the
locker locks and remains locked. When the actuator is moved to the other
position, the air pressure supply is blocked, and the port is vented to
exhaust, allowing the locker to unlock. |
The figure above illustrates
a 3-way, 2-position valve, with the accompanying symbols. In our installation,
the port labelled"P" would be where we connect the air supply
line from the compressor/air source, the port "A" would be where
we connect the air line running to the locker, and the port "Ex"
would be the exhaust port.
As for the symbols, note that
a blocked port is represented by a "T" symbol, and that airflow
between ports is represented by an arrow showing the direction of flow.
Knowing this, we can see that
the position on the left of this diagram would be "locker unlocked"
(pressure port blocked, line from locker exhausted) and the position on
the right would be "locked" (pressure supplied to the locker
line and the exhaust port blocked). |
Reading the
ANSI symbols. |
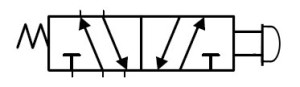 |
When browsing
a catalogue of pneumatic valves or switches we see that the type of switch
is illustrated using the ANSI symbols we have seen.
A typical switch may look something
like this. |
Positions
The number of positions the switch
has is illustrated by the number of boxes drawn. Each box represents the flow
path that is active when the switch is in that position. For example: |
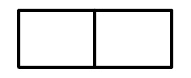 |
A 2-position
switch would have 2 boxes. |
|
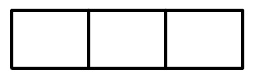 |
A 3-position
switch would have 3 boxes. |
Flow Paths
Each box of the switch diagram will
contain lines and symbols that depict the flow paths in the valve when the switch
is in that position. |
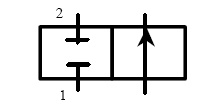
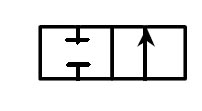
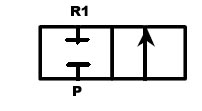
|
Recall our original
example of the simplest on/off valve. Its diagram would look like this.
Note that in the diagram the
ports may or may not be indicated by tick-marks outside the box and the
ports may or may not be labelled or numbered.
All three of these diagrams
illustrate the same thing - a simple 2-way, 2-position switch. |
|
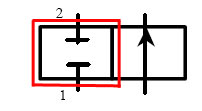 |
In this position,
both ports are blocked, no air flows, and the switch is "Off". |
|
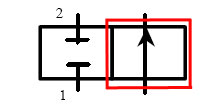 |
In this position,
the two ports are connected, the air flows in the direction indicated
- from port 1 to port 2 - and the switch is "On". |
Actuators
The symbols for the valve actuators
are drawn on the end of the position boxes. They are drawn next to the box that
illustrates the flow path that exists when that actuator has control.
An example should clarify. |
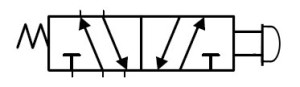 |
In this example,
the symbol on the far left represents a spring, and the symbol on the
right represents a push button.
It's a spring-loaded push-button
switch.
It has two boxes - so we know
it's a 2-position switch.
Obviously, in one position
the button has control (when it has been pushed), and in the other position
the spring would have control (when it's extended). |
|
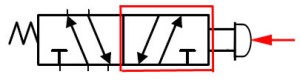 |
With the button
pushed, the spring compresses, and the flow paths will be those illustrated
in the box next to the button symbol. |
|
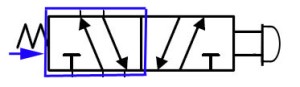 |
With the button
released, the spring extends, and the flow paths will be those illustrated
in the box next to the spring symbol. |
|
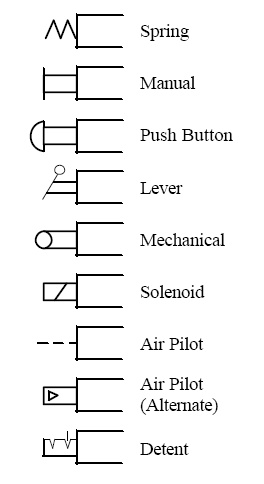 |
This chart shows
common types of actuators you might see. |
|
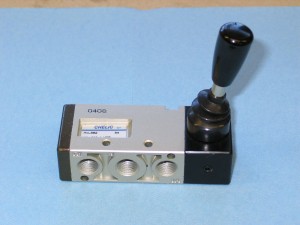
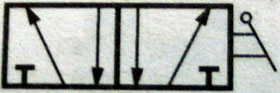
|
Note that, even
for a multi-position switch there may be only one actuator drawn if that
type of actuator is capable of controlling a number of different positions.
The most common type of actuator of this sort would be the lever (or joystick)
actuated valve - much like a multi-position hydraulic valve (as seen on
tow trucks, etc.). In this case, only the single symbol for the lever
is shown.
At left are a picture of just
such a valve and its ANSI diagram.
Q: For bonus marks, what type
of switch is this? You should be able to tell by now from reading the
diagram.
A: It's a 5-way, 2-position
lever control valve! |
A Pneumatic
Switch to Control an ARB
So, given all that we now know, what
would the diagram for a switch that can control our ARB air locker look like?
We should be able to draw it ourselves
at this point. |
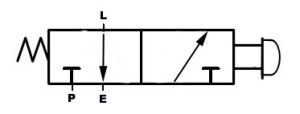 |
Here's the diagram
for a spring-loaded, push-button, 3-way, 2-position directional control
valve.
Quiz:
Assuming the ports are labelled
P for air pressure supply, L for line to locker, and E for exhaust, would
you push the button in to lock the locker or release it to lock the locker?
Answer: Push it in. Because
to lock, we want to connect P to L and block E. We can see this is the
case in the box next to the button - therefore we push the button to lock. |
Note: Many small pneumatic switches
may not have an obvious exhaust port. Instead they vent through the body of
the switch. Regardless, the ANSI diagram should still show it as a 3-way, 2-position
switch.
Another advantage to using a pneumatic
switch to control your air locker is that they are available with a seemingly
endless number of different methods of activation - you aren't limited to a
dash-mount switch - there are levers, push-buttons, twist-knobs, cable-pull,
and even pedal-actuated models available.
Putting it
all Together - the CKSA12 Compressor and Pneumatic Switches to Control an ARB. |
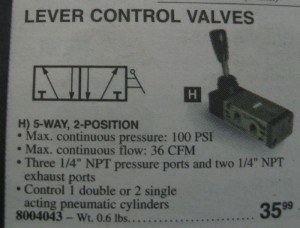 |
This is the page
from the catalogue of my local supplier (Princess Auto) illustrating the
valve I chose to control my rear ARB.
The reason it is a 5-way is
because I have a different brand of air locker in my front axle (that
requires a 5-way switch due to different operation) and I wanted the two
switches to match.
It's not a problem as I can
simply block the unneeded ports in the switch that controls the ARB. |
|
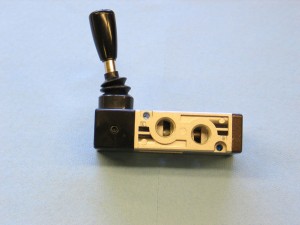 |
This side of
the valve has the two ports illustrated on the top of the ANSI box diagrams.
They are labelled A and B.
If you look carefully you can
see the sliding spool through the ports. |
|
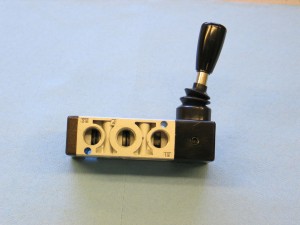 |
This side has
the three ports illustrated on the bottom of the box diagrams.
They are labelled R1, P, and
R2. |
|
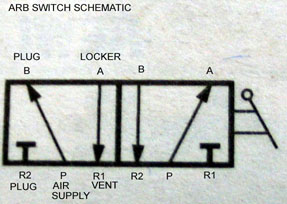 |
Here's the switch
diagram labelled for ARB control. |
|
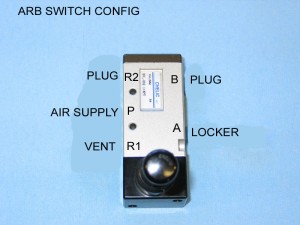 |
Here's how the ports
are configured / plumbed to control the ARB. |
|
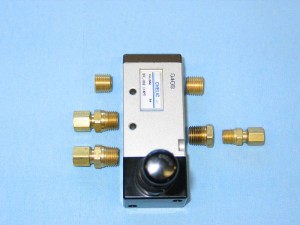 |
Showing the fittings
used.
Top two are simply brass 1/4"
NPT plugs to block off unneeded ports.
Two on left are 1/4" NPT
to 1/4" compression fitting. 1/4" compression fittings connect
to 1/4" SAE air-brake plastic hose that connects to the compressor
(middle fitting) and runs to an exhaust (bottom fitting). You want to
run an exhaust line because just leaving the port open would allow dirt
into the valve which would damage the sliding spool and internal seal
surfaces.
Right middle fitting is a 1/4"
NPT to 3/16" compression for connecting to the rear ARB locker. With
a bit of effort you can get a 3/16" compression fitting over the
5mm ARB supplied blue air line. |
|
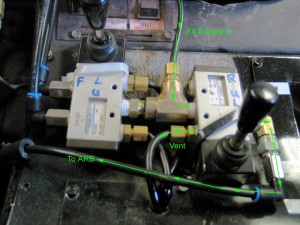 |
As I mentioned,
I wanted 2 matching pneumatic switches to control two different air lockers.
Here they are laid out on the
"centre console" (such as it is) of the buggy.
The one on the left, with the
stick to the front, controls the front (non-ARB) air locker.
The one on the right controls
the rear ARB.
The air flow through the ARB
switch is indicated in the picture.
Note that the 2 switches share
the incoming air supply from the CKSA12 via a T fitting. There's a reason
for this...see below. |
|
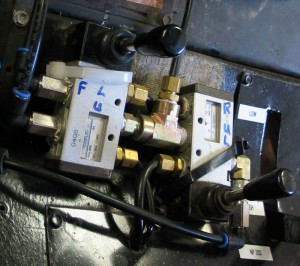 |
Another view
of the valves.
Notice that they are bulky
and with all the air line connections not a very tidy install (well, that
and because of my chronic lack of time/patience/skill and total apathy
towards how the rig looks!)
You can get much more compact
3-way pneumatic switches, but I do really like the little joysticks -
super easy to reach and use - even without looking. |
|
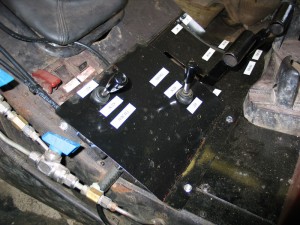 |
OK, maybe I'm
not TOTALLY apathetic about how booty-fab my rig looks - I made this rudimentary
cover to cover the valves and just let the joysticks protrude.
If you had any amount of skill
you could probably make a tidy little installation of these valves! |
|
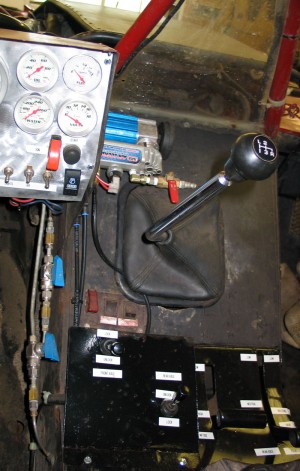 |
I mounted my
new CKSA12 compressor inside the rig, up beside the "dash".
This way it's kept reasonably clean and dry and has decent, clean air
supply.
It isn't exactly "whisper
quiet" but if you have no leaks its cycle time is infrequent and
it only runs very briefly to charge the small tank.
In fact, with the sound of
a V8 in an open buggy as well as my daughter's constant cries of "Faster,
Daddy, faster!" and my son yelling "Use the Cherry Bombs Dad
- use the Cherry Bombs!" (I think he thinks they're some kind of "switched"
thing like Nitrous instead of me just planting my foot on the idiot pedal)
- I hardly hear it at all!
Of course, if you have such
extravagant luxuries as, oh say, doors and a roof and a hood, you could
easily tuck it away in the engine bay and never hear it at all.
I particularly like that it's
well protected where it is.
And this is the great thing
about the CKSA12 - it's so small you can mount it anywhere and be worry
free because you have a completely independent system to run your lockers.
Nothing's worse than having
lockers that don't work - and now I don't have to worry about broken fan
belts on an OBA compressor or running out of CO2 in a tank. |
|
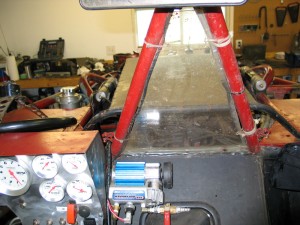 |
Note that I made
good use of the rotating mount capability so that the air supply line would
lay as flat as possible. |
|
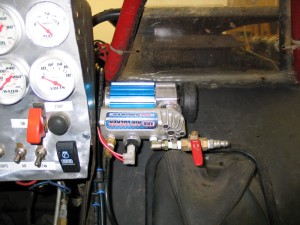 |
The CKSA12 has
2 supply ports - one is used for each solenoid in a "normal"
installation.
I supplied both my pneumatic
switches from a single port (on the left in this pic) using a T-fitting
at the switches so that I had the other port free.
As you can see, to this free
port I added a manual valve and quick-connect fitting. This way, if I
ever do have a problem with the compressor, I can hook up virtually any
other source of air to charge the small tank and retain full locker capability
without having to mess around with the air lines. |
|
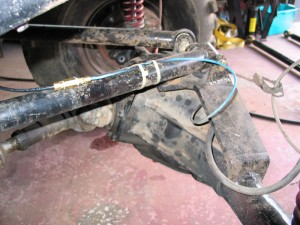 |
Speaking of air
lines - you may have noticed that in an earlier picture I talked about
connecting the 5mm ARB blue air line to my pneumatic switch using a 3/16"
compression fitting - but in these more recent pics I'm running 1/4"
SAE air brake hose from the switch.
Since here in Canada the ARB
line is harder to come by than 1/4" air brake hose (which can be
bought almost anywhere for pennies a foot) I decided to minimize the use
of the 5mm line. That way I have a coil of the 5mm line (that came with
my ARB locker) for spare/repairs that, because I use only a small length,
will last a very long time.
Everywhere else I use the cheap,
readily available 1/4" line.
The only place I use the 5mm
is to connect to the axle housing bulkhead fitting, as shown in this pic. |
|
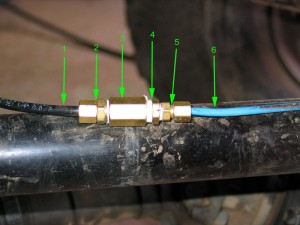 |
To join the 1/4"
air brake hose to the 5mm blue line I used:
1) 1/4" SAE air brake
hose
2) 1/4" compression to 1/4" male NPT fitting
3) 1/4" female NPT coupler
4) 1/4" male NPT to 1/8" female NPT adapter
5) 3/16" compression to 1/8" male NPT fitting
6) a short length of 5mm blue air line |
SERIOUSLY
abusive testing
The following series of pictures
and video were recently sent to me by ARB's Engineering Supervisor in Melbourne,
Australia. They demonstrate clearly just how seriously ARB take their products
and their durability. Subjecting a product like this to this kind of abuse shows
the confidence they have in it - and the impressive results should fill you
with confidence too. |
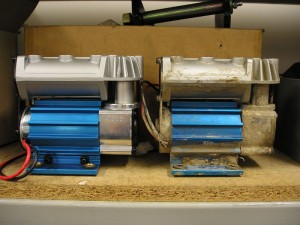
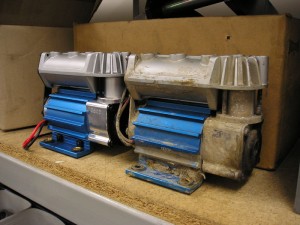
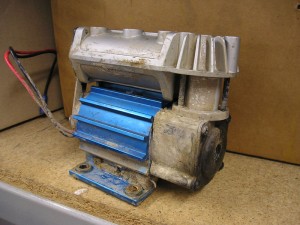
|
This series shows
a brand new CKS compressor next to one that was installed in the rear
wheel-well of a Land Rover 110 that then spent two solid weeks off road
on the beaches of South Australia. The unit was mounted in the gravel
blast-zone directly behind the tire - possibly the worst possible location
to mount one. After this abuse the unit still runs 100% and dyno'd up
to full performance. |
|
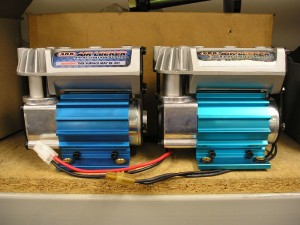 |
This is a pic of
a unit that ARB high-temperature tested shown beside a new unit (left) for
contrast. First It was baked it for a couple of days at 120°C after
which there was no identifiable damage of any kind. Next they stepped the
temperature up to 150°C. Finally they stepped the temperature up to
180°C for a whole day which is the point at which the wiring insulation
actually baked itself brittle, the plug changed to that brown colour, and
the sticker shrivelled up. Also notice that they actually cooked it so much
that the blue anodizing of the motor mount became discoloured.
This unit still runs to this day, and has suffered only minor performance
degradation which ARB were able to detect on their computerized flow dyno. |
|
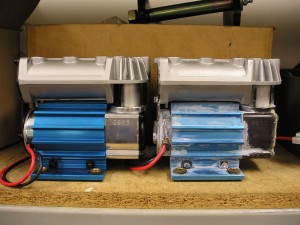
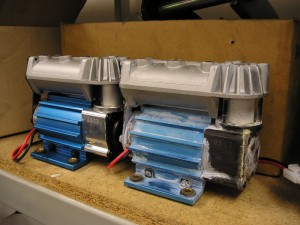
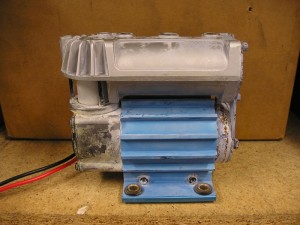
|
These pics are of
a unit that spent over a full month completely submerged in a super-saturated
solution of sea salt and water. Notice that the corrosive solution did get
through the zinc plating in a few spots on the motor tube, turned the aluminium
crank-case die-casting a very strange black colour, and left a hard-nasty
salt build-up on the rest of the whole unit.
This unit is kept at ARB's head office in Melbourne, Australia in case anybody
would like to stop by and see it fired up and dyno'd at full performance
levels. |
|
ARB
CKS Compressor - Runs completely submerged !!! |
Finally - click
the title to the left to see a 2MB .avi video clip of the CKS compressor
running completely submerged!! |
It's a rare thing that a company
spends such time and effort abusively testing their products, and rarer still
that they release the results to the public. My thanks to ARB for the pictures
and video and congratulations to them for building such a seriously tough little
unit!
Conclusion
The new CKSA12 compact on-board air
kit is a dandy little product. You won't be filling any tires with it or powering
air tools - but at the job it is designed for - running air lockers - it is
excellent. It's compact, easy to mount, reasonably quiet, simple to hookup and
best of all - rugged, independent and reliable. I've been running mine for many
months now and it easily and reliably runs both my air lockers. It occurs to
me that it would also be an excellent choice for anyone with limited space or
particularly for competitors looking to save weight anywhere they can.
The only thing I could suggest for
improvement would be if ARB themselves could design and produce a "full
pneumatic" kit. With their usual attention to detail and if it were anything
like their normal kit in terms of fit and finish, heck even I could end up with
a clean, show-quality install. So how about it ARB?
This
little compressor works great, is amazingly rugged, and would be an excellent
choice for anyone - whether running "full pneumatic" or the conventional
electro-pneumatic.
References:
Go to >>> ARB
Install Part 1 - ARB 14-Bolt Air Locker Install |