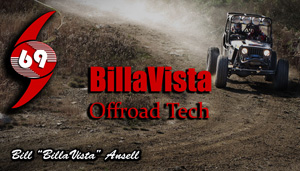 |
Teraflex T-Locker
By Bill "BillaVista" Ansell
Photography: Bill Ansell
Technical Drawings: Lonny Handwork
Copyright 2005 - Bill Ansell
(click any pic to enlarge)
|
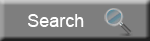 |
Introduction
I had long wanted a selectable locker for the front of my rig. While my
old welded-up spool provided all the traction I ever wanted, the handling
it induced was terrible. The overwhelming tendency for the front wheels
to plough straight ahead while turned, seriously compromised manoeuvrability.
It was especially annoying in tight, technical rock crawling where precision
is key and a few inches can mean making or losing the line. Adding full
hydraulic steering did nothing to help – sure, it reduced the steering
effort a lot, but it can’t make the wheels track a turn the way
an open differential can. I tried various other “solutions”
to the problem: I added cutting brakes and I tried using locking hubs
instead of drive flanges but nothing stopped the front end from ploughing.
And so I knew that if it was the ultimate in both traction and turning
I wanted, a selectable locker I must have. But which one? |
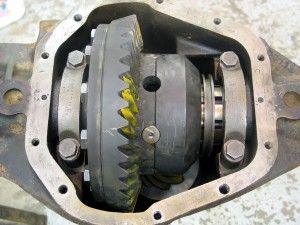 |
There are several choices
on the market, differentiated principally by the way in which the locker is
activated. I immediately dismissed cable and electrically-activated lockers,
as it is difficult for either of these methods to develop sufficient force for
the sure, reliable shifting I wanted. Additionally, the locker’s location
means constant submersion in water, mud, and goo – making it a not-so-great
location for electrical servos. Cable activation would require finicky setup,
a large lever for any real power, and likely constant adjustment and maintenance
of the cable. This leaves pneumatically or hydraulically activated lockers,
but which of these to choose? I’m a big fan of hydraulic power, but it
requires specialized pumps and plumbing, and operates at very high pressure.
Not only that, but Mercedes Benz make the only manually selectable hydraulic
lockers I’m aware of - and only for their own products like the Gelandewagen.
So that leaves pneumatic, or air-operated, activation. Fortunately, pneumatics
is an excellent solution. The beauty of pneumatics is that the plumbing is simple
and cheap, it operates at low pressures (under 100 psi as opposed to 1000+ in
hydraulics), and there are virtually limitless options for supplying the air
- from small electrical compressors to engine-driven on-board air systems to
portable CO2 tanks. Not only that, but most of us will already have some sort
of air supply system incorporated into our rigs. A short time ago, when I heard
that Tibus Offroad (of Unimog axle fame) were designing a new type of pneumatic
locker, I jumped at the chance to install one in my Dana 60, test and review
it. Here’s what I found:
The
T-locker
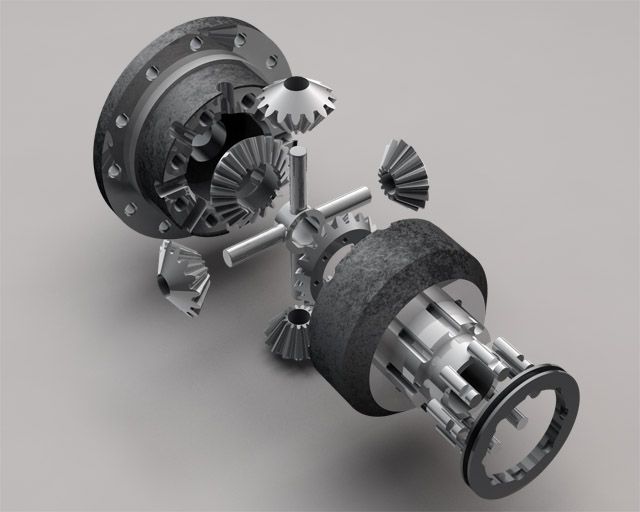
Figure 1 – T-locker
exploded view |
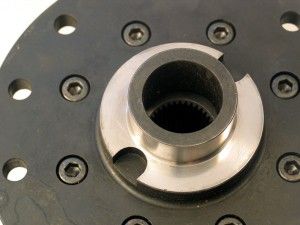 Figure 2 – Carrier bearing reliefs |
The new T-locker is a pneumatically shifted, manually controlled, selectable
locking differential that gives the operator a choice of fully-locked operation
(essentially operating as a spool) or fully-open operation (operating as
a standard open differential).
The T-locker was designed from the ground up by German
engineer Wolfgang Tibus to be the strongest, most reliable selectable
locker available. The engineering, machining, and fit & finish of
the T-locker are absolutely first rate – and this is immediately
apparent the second you hold one in your hands. Weighing in at over 35
pounds it’s a serious brute of a machine. Not only that, but there
are also several small touches that demonstrate the level of thought and
attention to detail that went into its construction. For example, there
are very generous reliefs machined into the carrier bearing seats –
sure to be appreciated by anyone who’s had to use a twin-leg puller
to remove carrier bearings (Figure 2). |
|
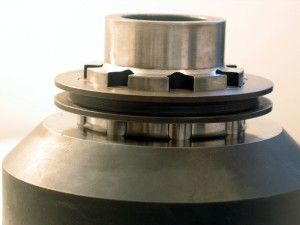 Figure 3 – Shift collar |
The
way that it works is deceptively simple. Figure 1 illustrates an exploded
view of the locker. Inside the case there are four spider gears, two side
gears, and two cross-pins. The locking ability comes from the fact that
one of the side gears is machined to accept eight hardened-steel locking
pins.
These pins slide in
grooves in the case to engage or disengage the side gear. The position
of the pins is controlled by a sliding shift collar that sits just below
the carrier bearing journal on the non ring-gear side of the case (Figure
3). |
|
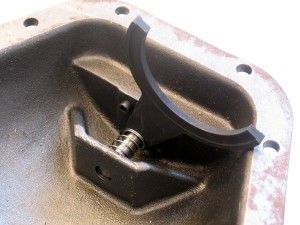 Figure 4 – Shift fork |
The position
of the shift collar is in turn controlled by a shift fork that is built
into the diff cover (Figure 4). When the shift fork is shifted to the “lock”
position, the shift collar slides towards the centre of the case, the pins
engage the side gear, the locker is “locked”, and the axle shafts
are 100% mechanically locked together giving maximum traction. When the
shift fork is shifted to “unlock”, the collar slides away from
the centre of the diff , the pins retract from the side gear, the side gear
is allowed to turn freely, and the T-locker now behaves as an open differential.
The shift fork itself is shifted by a small pneumatic cylinder (very much
like a small hydraulic cylinder) that is mounted on the diff cover (Figure
6). |
|
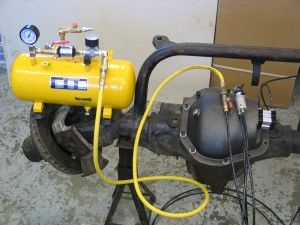 Figure 5 – Complete pneumatic system |
There are
two ports on the pneumatic cylinder, one for lock and one for unlock. Applying
air pressure to one or the other shifts the fork in the desired direction,
meaning the locker is powered in both directions. As such it doesn’t
rely solely on a return spring to unlock, resulting in much more positive
shifting than would otherwise be the case.
There is also a return spring, as can be seen in Figure
4. The purpose of the return spring is to return the shift fork, and therefore
the locker, to the desired state, should there be a complete loss of system
pressure. I say “desired state” because of one of the great
advantages of the T-locker’s design – the user can choose
whether the default, pressure-loss position is “locked” or
“unlocked”. The factory setting is “unlocked”,
and this should never be altered for a street driven rig (imagine tooling
along at 50mph with the locker open and experiencing a pressure loss –
the return spring would take over and shift the locker to lock with disastrous
consequences!) However, in a dedicated trail rig, one can simply install
the spring on the other side of the shift fork, causing the pressure-loss
position to be “locked” – which may be an advantage
where maximum traction is a must. As far as I know – no other locker
offers this choice. |
The
Pneumatic System |
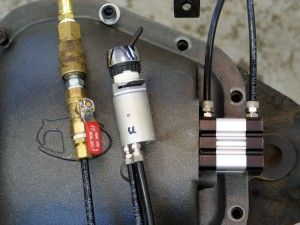 Figure 6 – T-locker switch and cylinder |
That said,
a loss of air pressure is unlikely, and even if it happens, it will be quick
and simple to repair – even on the trail. That’s because the
real beauty of the T-locker lies in the simple, rugged design of the pneumatics.
There are only three components involved: the pneumatic cylinder (built
into the diff cover), the switch (mounted wherever the operator desires),
and a supply of air. Figure 5 shows the complete pneumatic system, from
supply tank to cylinder.
The entire air system lies outside the diff cover. This
means that there are no seals on rotating parts to wear or leak, no drilling
into housings or bearing caps required, no gear oil will ever blow back
up the lines, and the system can be installed, troubleshot, and repaired,
even in the field, without ever having to remove the diff cover.
Figure 6 illustrates, from left to right: quick-release
air supply with shut-off valve, locker activation switch, and pneumatic
cylinder with air-lines attached. |
The key to the system is
the very clever switch (centre, Figure 6). The switch is actually a mechanically
operated, two-position, monostable, pneumatic solenoid valve designed and built
by the German company, Joyner Pneumatic (as is the cylinder). What this really
means is that it is ingenious! First, there is no electrical wiring involved
– the switch is mechanically operated (the user flips a toggle) and pneumatically
actuated (only a supply of air is required for operation). Second, there are
only three simple air lines – one from the air source to the switch, one
from the switch to the “lock“ port on the cylinder, and one from
the switch to the “unlock” port on the cylinder.
There are five ports on
the switch, as follows:
1 – Air supply
2 – Lock
3 – Lock-line vent
4 – Unlock
5 – Unlock-line vent
To port 1 you connect an
air supply capable of delivering anywhere from 20-150 psi. Port 2 is connected
to the lock port on the cylinder (the outer port), and port 4 is connected to
the unlock port on the cylinder (the inner port, closest to the diff). Ports
3 and 5 are vents and are left unconnected. |
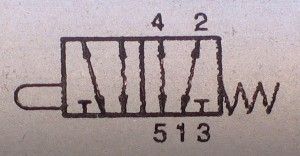 Figure 7 – Pneumatic switch solenoid diagram |
Figure
7 illustrates the solenoid schematic diagram. The diagram shows us that
the solenoid is a two-position, push-button activated, spring-loaded switch
(similar to a spring-loaded on/off switch). There are two positions for
the switch, each represented by a rectangular box in the schematic. The
arrows in the boxes show the connections between the numbered ports, depending
on which position the switch is in. The box on the right, closest to the
spring, shows the connections in the normal (spring relaxed) position,
the box on the left shows the connections with the spring compressed.
With the switch in “normal” port 1 is connected to port 2,
supplying air pressure to the lock side of the cylinder; port 4 is connected
to port 5, venting the unlock side and port 3 is internally blocked off
(represented by the T). When the operator flips the toggle switch a plunger
presses on the activation button, the spring is compressed and the connections
become those shown in the box on the left: port 2 is vented to port 3
(releasing the lock side), port 1 is connected to port 4 (pressurizing
the unlock side of the cylinder), and port 5 is blocked off. In simple
terms, flipping the toggle switch one way pressurizes the lock line and
vents the unlock line, flipping it the other way does the reverse. |
It takes very little volume
to power the cylinder and activate the locker, and it works with pressure ranging
from 20 to 150 psi. Below 20 psi the shifts become a little weak and slow, and
greater than 150 psi puts unnecessary stress on the air-lines and cylinder/switch
seals. Note that the lock and unlock circuits are completely isolated by having
their own vents. This means that a loss of pressure on one side will not affect
the other – in other words, if you rip the unlock air-line, the locker
will remain locked, and vice versa.
In fact, because of this
design, if you install a shut-off valve in the air-supply-to-switch line, it
is possible to pressurize the desired line (lock or unlock), close the valve
in the supply line, and then actually disconnect and remove the air supply completely
and the locker will remain in the desired position. Taking this to the extreme,
you could actually fit your supply line with a Schrader valve and operate the
locker with a small hand-operated bicycle pump! It’s certainly not the
recommended method – but it’s nice to know it could be done if required. |
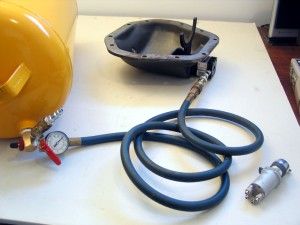 Figure 8 – Pressure and leak testing |
During testing I was
able to get the locker to shift all the way down to 10 psi. I also disconnected
the air supply and found that the locker requires such a small volume
of air for activation that I could lock and unlock it three times with
just the volume of air in the lines. To test the air fittings I pressurized
the lock line, disconnected the air supply and monitored for leaks (Figure
8). Eleven hours later the line still held pressure, the fork remained
firmly locked, and I got tired of watching it! |
Plumbing |
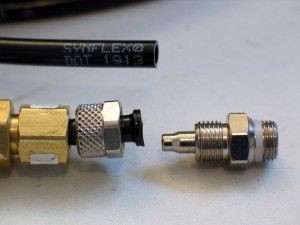
Figure 9 – T-locker air-line fitting |
Possibly
the trickest parts of the kit are the air-line fittings (Figure 9). There
are two different size fittings, a large one for the cylinder ports and
a smaller one for the switch ports. The larger has British Standard Pipe
Parallel (BSPP) 1/8” x 28 TPI threads (also called ‘G-1/8”
Pipe’, and very common in pneumatics.) The smaller fitting has M5x0.8
mm threads. Both are designed to use either 6x4mm metric or ¼”
SAE air line, and both consist of only two parts. The main body threads
into the port, the small cap slips over the air line, the air line is pushed
onto the nipple on the main body, and the cap is then tightened onto the
main body. There is no separate ferrule to lose or risk deforming when the
fitting is tightened. When the cap is tightened onto the main body, it creates
a sort of “self-flaring” effect on the air-line, resulting in
a leak-free connection. After initial installation the line can even be
removed and then re-attached, unlike a normal compression fitting that requires
replacement of the ferrule.
The only thing not included in the kit is the air-line
itself. You will need to acquire about 20-30 feet of ¼” SAE
J844 Type A or B nylon tubing designed for use in tractor-trailer and
other mobile air brake, instrumentation, and air accessory systems. |
It
should have a temperature range of about -40°F to +200°F and a
working pressure of at least 150 PSI. It is commonly just called “quarter-inch
air brake line”. The beauty is, though it is fairly rugged, if it
should break it is dirt cheap (probably less than 25 cents a foot), available
almost anywhere (you can get it at any tractor-trailer parts house and
many other farm or equipment dealers), and it requires only a sharp knife
to cut to length and a small wrench or strong fingers to install. |
Air
Source |
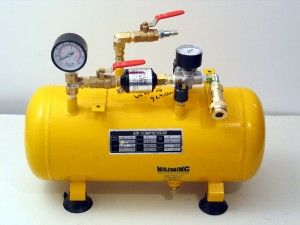 Figure 10 – Air supply tank |
As mentioned,
virtually any air source will power the T-locker, from bicycle pump to CO2
tank. The best setup is to have some sort of small storage tank, which can
be filled as required from whatever air source you have. I scrounged around
the local surplus store and found a small 2-gallon tank that was originally
connected to a small portable compressor (Figure 10). For some reason I
decided to make it resemble a small nuclear reactor! In fact, each component
has a function. In the background you can see the fill port with quick-disconnect
and manual valve. This allows me to fill my tank from virtually any source
– my engine-mounted OBA compressor, my CO2 tank, or a cheap plug-in
electric compressor. I can even fill the tank directly from my shop compressor
and it will hold enough air for a full days locking and unlocking. On the
outlet side, from left to right, I have the tank pressure gauge, shutoff
valve, filter, regulator with gauge, and a universal air-tool quick-connect
fitting that connects to the supply line running to the T-locker switch.
It’s important to supply the cylinder with clean, dry air and I have
found that 80 psi is about optimum. |
Protecting
the Cylinder |
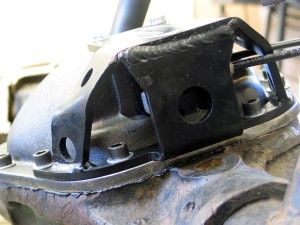 Figure 11 – Quarter-inch steel cylinder guard |
The only
possible drawback to the externally-shifted design of the T-locker is that
the pneumatic cylinder must be protected – but this is easily done.
To begin with, the cylinder is very compact and securely mounted to the
diff cover (Figure 6). The T-locker also comes with a stout, compact, quarter-inch
steel guard that fits closely over the cylinder, keeping it well protected
without resulting in any overhang or loss of clearance (Figures 11 and 12).
The cylinder-guard bolts to the housing with four 3/8” socket-head
cap screws and to the massive 5/16” cast steel diff cover with two
additional hex-head bolts. |
|
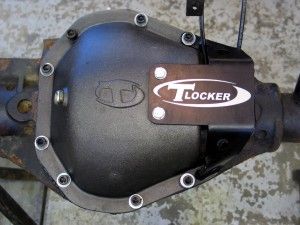 Figure 12 – Installed T-locker with cylinder guard and air-lines in place |
Even for
those of us, like me, who prefer to “drive by brail” in the
rocks, there should be no concerns with damaging the cylinder. If, however,
the worst should happen, replacement parts are available from Teraflex. |
Installation Essentially,
installation involves assembling the air cylinder to the diff cover, installing
the locker and setting-up the gears, adjusting the shift fork position, bolting
on the diff cover, installing the air lines, and installing the cylinder guard.
The installation instructions provided with the T-locker are actually pretty
good so I’ll just mention the following tips and info I learned along
the way.
Installing the locker in
the housing is the same as installing any carrier, the only exception being
that prior to installing the carrier bearings you must first remove the zip-tie
that holds the shift collar and locking-pins in place during shipment. Once
you have removed it, be careful not to hold the locker in such a way that the
set-up bearing can slide off, allowing the shift collar and locking-pins to
fall out and scatter all over the floor. (Ask me how I figured this out!) Once
the locker is installed and the gears set-up, the only tricky part of the installation
is adjusting the shift fork position so that its throw is both sufficient and
in the right location to completely lock and unlock the locker when the cylinder
is actuated.
I used the following method
to accomplish this: |
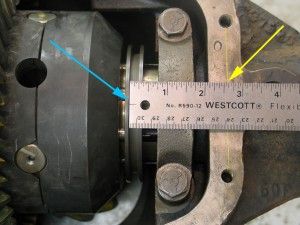 Figure 13 – measuring “lock position” of shift collar |
1. Referring
to Figure 13: Slide the locking collar all the way towards the centre of
the diff, and ensure the locker is fully locked. Scribe a line between the
centres of the two cover-bolt holes on the housing (yellow arrow). Measure
the distance from the inside of the inner lip on the shift collar (blue
arrow) to the line you just scribed – this is the “lock position”
of the shift fork. |
|
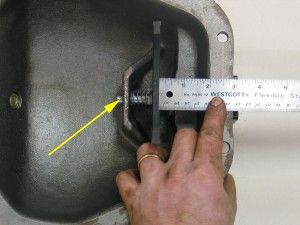 Figure 14 – measuring “lock position” of shift fork |
2. Referring to Figure
14: Scribe a vertical line between the centres of the corresponding bolt
holes on the diff cover. Move the shift fork to the centre, locked position
and holding it in place, measure the distance from the outside edge of the
shift fork to the scribed line. This measurement should be the same as that
obtained in step 1. If it is not, adjust the position of the shift fork
on the cylinder rod by screwing the shift shaft (yellow arrow) and jam nut
in or out, until the measurements are equal.
3. Move the shift fork from locked to unlocked and using the scribe line
on the diff cover as a reference, measure the total throw of the shift fork
from the locked to unlocked positions; the “fork throw”.
4. Returning to the axle housing, and measuring from the scribed line, slide
the shift collar away from the centre a distance equal to the “fork
throw” measured in step 3, making sure that the locker completely
unlocks.
5. With the locker unlocked and measuring from the scribe line again, make
a note of the shift collar’s “unlocked position”. |
6. Double-check the shift fork position as follows: On the diff cover, allow
the spring to return the shift fork to the unlocked position, then measure
from the shift fork to the scribed line as in step 2, confirming the shift
fork’s unlocked position is the same as that for the shift collar.
7. Repeat steps 1-6 until the measurements for the lock and unlock position
of the shift collar are equal to the measurements for the lock and unlock
position of the shift fork. |
When plumbing the system,
the following tips will help:
• Tighten the air-line
fittings into the switch or the cylinder before attaching the air line to the
fitting.
• The switch fittings take an 8mm wrench and the cylinder fittings a 12mm
wrench.
• Cut your air-lines to length using a sharp utility knife, and make sure
the ends are square and burr-free.
• Do not over-tighten the fittings or the air-line nuts onto the fittings
or you risk damaging them. You should be able to attach the air-lines to the
fittings by screwing the nuts down finger-tight. Since I was working in an unheated
shop at about –20°C I found that I needed to use a wrench. Tightening
both the fittings and air-line nuts using one finger on the wrench positioned
about one inch from the nut worked well.
• It’s a good idea to protect the air-lines, at least in vulnerable
spots, with some sort of protective loom. Quarter-inch ID rubber hose makes
a great protective sleeve for where the lines might rub or where they pass through
a bulkhead.
• It’s possible to upgrade the air-lines to a braided stainless-steel
or the like, but I wouldn’t recommend it. Well routed and secured, the
nylon lines should be more than adequate. Also, if one does snag, being the
weakest link, it will be the part to fail – which is OK since it’s
so cheap and easy to fix (it’s very easy to carry a coil of spare line
and a couple of push-to-connect fittings to make a repair). On the other hand,
it would truly suck to have a strong steel line snag and break a fitting, or
worse, strip the internal threads out of the cylinder or switch.
For
Improvement
Nothing’s ever really
perfect, there are always things that can be better, and I’m committed
to always pointing out what I think needs improvement – both as information
for you, the reader and potential customer, and also for the company concerned,
should they wish to act on any of my suggestions. With that said, the T-locker
made this part of my job pretty difficult – there really isn’t a
whole lot that can be improved as far as I can tell, so I’m really digging
here:
• The mounting holes
on the diff cover are drilled slightly oversize, presumably to facilitate installing
the diff cover, getting the bolts all lined up, and getting the shift fork engaged
in the locking collar all at one time. Fair enough - but this necessitates the
use of washers under the heads of the supplied cover bolts. Sadly, the supplied
washers are cheap junk, far too soft for the job. When you tighten the bolts
anywhere near the Dana recommended 40 ft lbs the washers squish and splay out,
becoming useless and endangering proper cover-to-housing clamping load. Throw
them out and use some decent hardened washers, such as SAE Grade 8.
• Quarter-inch air-brake line may be cheap and easy to source, but it
would have been nice to find a 30 foot coil included in the box – purple
would be cool!
• Similarly, it would have been a very nice touch to throw in at least
one spare fitting of each size – just for those of us who like to lose
important little pieces (don’t ask!)
• The supplied instructions were a little “thin” in the plumbing
section, stating merely: “Run 2 hoses to the axle.” That said –
since you’re reading this article I imagine you won’t have any problems. |
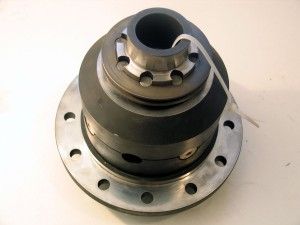 |
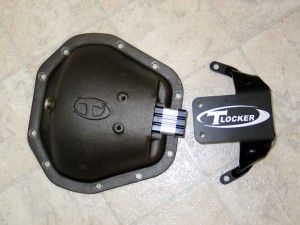 |
Conclusion
The T-locker is a full-case,
manually operated, pneumatically powered selectable locker with power-lock and
power-unlock ability. It requires only a simple air-system to operate, has isolated
lock and unlock circuits, and needs little pressure and only a tiny volume of
air to work. The entire pneumatic system is contained outside the differential
for strength and reliability and the required air-lines are cheap, readily available
and easy to repair. For trail-only rigs, the locker has the ability to be switched
between “default-locked” and “default-unlocked”. It
comes complete with a rugged cylinder guard and it is very impressive in its
design and quality. Air-line is not included and you have to buy your own decent
quality cover-bolt washers.
So far I have dismantled,
inspected, measured, photographed, rebuilt, tested, installed, plumbed, and
operated my Dana 60 T-locker and I am very, very impressed with it. At first
I was sceptical about the cylinder outside the diff and hesitant about the pneumatic
shifting. However, now that I have first-hand experience with the locker my
concerns are completely put to rest. What remains is for me to take the locker
out for some brutal real-word trail testing, and that’s exactly what I
plan. Stay tuned for a full future update on this highly impressive product’s
trail performance. |
|
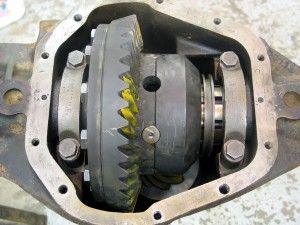
|
Sources: TERAFLEX
Tera Manufacturing, Inc.
5251 South Commerce Drive
Murray, Utah 84107
Ph: 801 288 2585
www.teraflex.biz
Tibus
Offroad
Roffhausener Landstr.25
26419 Schortens
Germany
Ph: +49 (0)4421 70691
http://www.killeraxles.com |
|