|
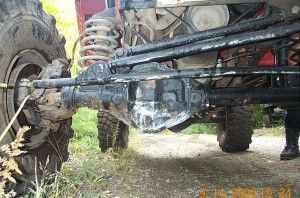 |
I was sick
of this... |
|
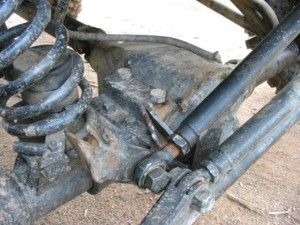 |
...and this... |
|
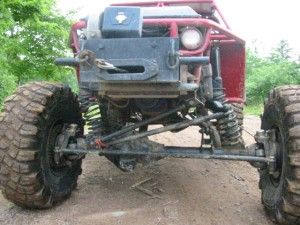 |
...and this! |
Not to mention, with a spooled front
differential (welded) and solid drive flanges in the hubs (in place of manual
locking hubs) the Wolf was an Olympic workout to steer, especially when bound
up in the rocks. The proverbial "final straw" was when poor old Scout
II steering box finally puked it's guts, leaving me stranded, on the third (and
best) day of our annual "rockathon" event, with no steering. My day
was done, I was a spectator, amongst some of the best rock terrain we have. |
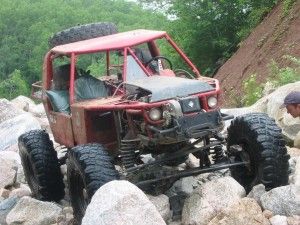 |
"Hey...what's
that peeing out from the sector shaft area...?" |
|
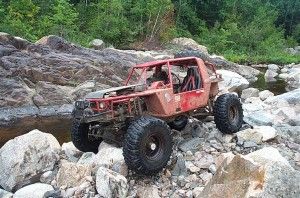 |
"Oh
good...I get to park while everyone else gets it awwwn in Rock City!" |
BOY was I ticked off. And so began
some loooong nights of research, which I attacked in my customary style. Eventually,
my search led me to Sean Stapely
of Performance Offroad Systems. He is a small one-man operation that specializes
in Hydraulic steering components and systems. He came highly recommended by
quite a long list of folks I highly respect, including "Diamond" Dan
Dibble and Frankie "Finland" Fountain. So I decided to give him a
call and see what he had to say, and to offer. Read along to see what I got,
what I dod right, what I did wrong, what I learned, and what I thought.
Be warned, this is not a simple or
cheap upgrade or modification. It can be complex, and very costly - especially
if you have additional system complexities such as hydroboost brakes or 4-wheel
steering requirements.
However, done right, it can and will
reward you with steering like no other you have EVER experienced. And I do mean
EVER. Not just in a 4x4 or Rock Buggy, I mean EVER. Read on and I shall explain...
The Parts |
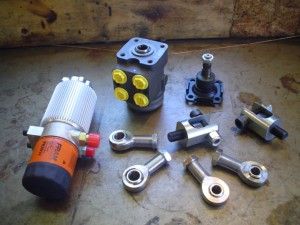 |
The system I ordered from Performance Off-Road Systems included
a Danfoss Steering Unit, Custom Steering shaft, Integrated fluid Cooler/Filter/Reservoir
(CFR), Custom Balanced (double-ended) cylinder with mounting clamps, Double-shear
Clevis ends for the cylinder and 4 QA1 Endura series spherical rod ends (Heim
joints) - 2 - 3/4"x5/8" and 2 - 3/4" x 3/4" . If you are
unfamiliar with any of these terms or components, I highly recommend you first
read Hydraulic Steering Systems. |
|
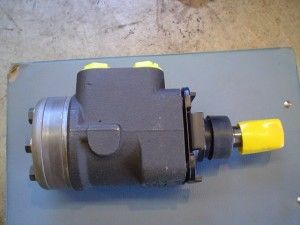 |
The heart of
the system is the Danfoss Steering Unit, seen here with the steering shaft
attached. |
|
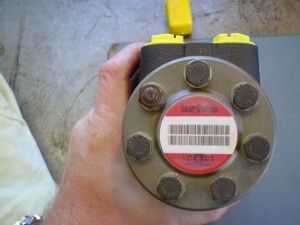 |
The steering unit is an open-center,
load-reactive unit. It weighs 12 lbs, displaces approximately 7 cu. in.
/ rev. and requires a pump capable of producing flow rates of 3.4-13.2 gpm.
It has a built-in manual check-valve that allows manual steering (pump inoperative). |
|
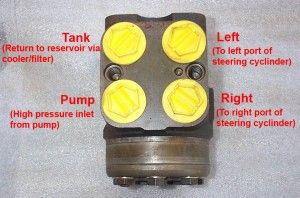 |
The ports are all 3/4-16 UNF
O-ring boss. |
|
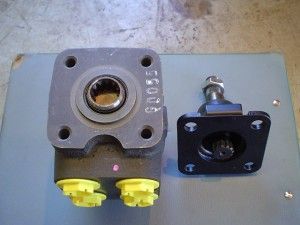 |
Shows the input end of the
steering unit, as well as the 4 threaded holes to which a) the steering
input shaft bolts; and b) the steering unit is mounted to the vehicle. |
|
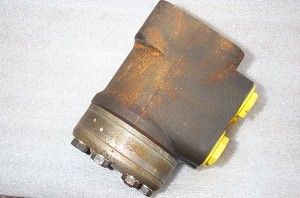 |
The steering unit does need
to be coated or painted before being exposed to the elements at all. I left
it in the garage for a week and surface rust began, so a quick coat of paint
would be a good idea. DO NOT get any paint anywhere near any of the hydraulic
ports or seals! |
|
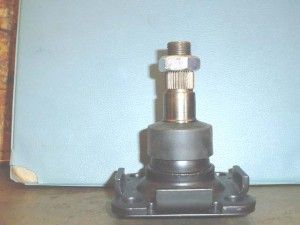 |
This is the Performance Off-Road Systems custom steering
shaft. The splined section is specifically manufactured in 36 spline .750"
,which is the common automotive steering shaft spline size, to fit standard
automotive parts, as opposed to most other shafts are a common agriculture
size that sends you searching for agricultural parts to match. |
|
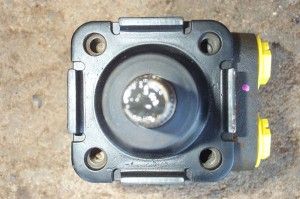 |
For some odd reason the holes
on my steering shaft did not line up exactly with the tapped holes in the
steering unit. I tried in in every possible orientation - but still things
would not line up exactly. It wasn't a huge deal, as the holes in the steering
shaft base plate were sufficiently large to allow all the bolts to go in.
However, it did make things fiddley as heck trying to get the bolts all
in place when trying to mount the steering unit to the firewall, as the
bolts have to go through the firewall mounting plate, then steering shaft
base plate, then into the steering unit. To get this all lined up the holes
on the firewall mounting plate had to be drilled oversize by quite a bit
(29/64" for 3/8" bolts). |
|
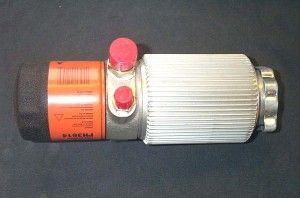 |
The Cooler/Filter/Reservoir
combo is from Appleton. It's aluminum and features integrated fins for cooling,
a standard automotive engine oil spin-on filter ( ) , and a reservoir capacity
of approximately 1.5 litres. It has a -10 JIC (AN) outlet fitting and a
-6 JIC (AN) inlet fitting. |
|
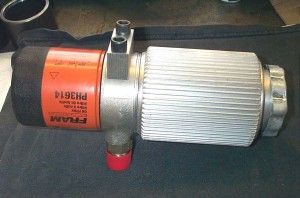 |
It also has an integrated mounting
block, shown at the top of this pic. |
|
 |
The fluid path through the unit
is as follows. Fluid enters through the "return" port (bottom
right in this pic). It flows through the small orifice shown, and then enters
the filter through the multiple smaller circular holes around the filter.
It passes through the filter media and exits the filter through the central
hole. From there it enters the reservoir again through the large central
port (the one onto which the filter screws) shown in the center in the pic
at left. |
|
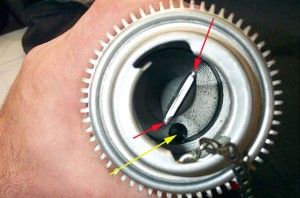 |
From the center hole of the
filter it flows up through this column that is in the middle of the reservoir,
and exits through 2 small ports in the column (red arrows indicate location),
that are about 1/2-1" below the top of the column.
This arrangement is designed
to reduce aeration of the fluid as it returns to the reservoir. It is
a form of baffling. Finally, the fluid exits through the large circular
port in the bottom of the reservoir (yellow arrow)... |
|
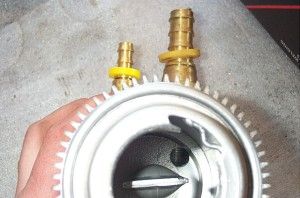 |
... and out the -10 fitting
to the pump (fitting on right in pic at left) |
|
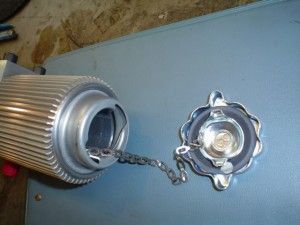 |
The CFR has a steel 1/4 turn
cap attached by a small chain.
This leads me to my first,
hopefully constructive, criticism. The cap supplied with the CFR is a
fully sealing kind. As discussed in Part 2, and indeed as Sean himself
recommends, the system should be run vented. However, a vented cap is
not supplied, nor available, from Performance Off-Road Systems or from any other source that I
could find (and I tried all kinds of gas, oil, and radiator caps - buying
several to try).This leaves you with only 3 choices:
- run the system sealed (I
wish I had actually just tried this first - as it would turn out that
I would have a bit of a nightmare time with plumbing the system),
- install the supplied CFR
as an auxiliary reservoir only, below the level of some other suitably
vented reservoir; normally a stock attached-to- pump reservoir. (This
solution is unsatisfactory for several reasons - chiefly the difficulty
in mounting this CFR below the level of a stock pump reservoir and also
the fact that many of us may be using Saginaw TC or aftermarket pumps
that don't have any integrated reservoir)
- modify the supplied cap
to vent. This is the option I chose, and it was a HUGE pain in the butt.
|
|
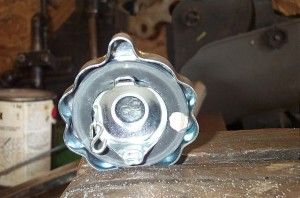 |
To start with, the only place
you can vent the cap is in the center, but as you can see from the pic,
the whole cap is held together by spot welds - so when you drill your vent
hole, it all falls apart. |
|
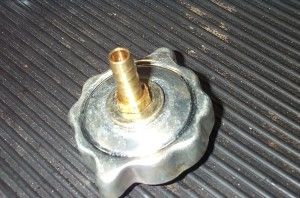 |
I solved this problem by drilling
a large hole, and fitting a pipe-thread hose barb... |
|
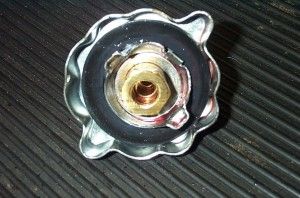 |
...held on the backside with
a pipe coupling I cut in half to produce a sort of NPT "nut"
to hold all the little bits back together with the nipple fitting.
This led to another little
SNAFU. As you can imagine, through this process, the exact orientation
of the little locking tabs of the cap changed somewhat. While getting
them re-aligned so the cap would go on and off easily enough but still
stay tight the steel galled the aluminum of the lip of the tank and left
me with a small pile of aluminum shavings in the bottom of the tank -
as you can imagine - not the best of things for a hydraulic reservoir!
All in all - nothing major,
possibly caused by my own ineptitude, but like I said, a royal pain that
could easily be avoided with a proper vented cap offering. |
|
 |
Moving on...the "other"
heart of the system, my personal favourite component, and the part that
makes the Performance Off-Road Systems system the best available on the market is the balanced ,
double-acting steering cylinder. |
|
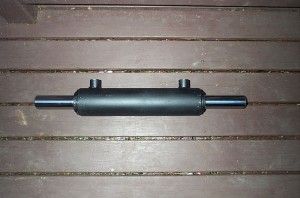 |
This beast is custom designed
and built to spec specifically for off-road hydro steering systems on
hardcore rock smacking machines. You won't find any other available quite
like it, and it is FAR superior to any other offered.
It has a 2.5" bore , 8"
stroke , 1.5" diameter IHCP( Induction hardened, Chrome plated) shaft
and .25" wall thickness on the body of the cylinder. The length is
21.5" + the length of the clevice ends.
Built to take a serious beating,
able to handle the unique stresses of rock crawling, and easily able to
handle the pressure of the most hi-po pumps and generate tremendous amounts
of steering power...this beauty may not be shiny but it definitely gets
the job done! |
|
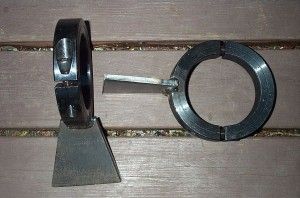 |
In the same vein, the supplied
mounting brackets are simple, no nonsense pieces that are easy to mount
and provide great ease and flexibility in mounting the cylinder... |
|
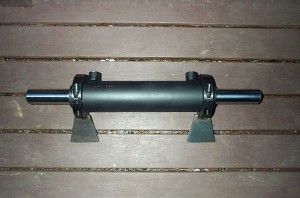 |
...and that's a very good thing
because the big, beefy cylinder is 3" OD alone, and 4.5" OD with
the brackets around it - so it takes up quite a bit of real estate and therefore
mounting can be challenging. |
|
 |
The system is rounded out nicely
with this very nice linkage hardware. There are 2 double shear style clevis
ends that thread into the ends of the cylinder, socket head cap screws with
nylock nuts to attach the rod ends to the clevis ends, and a total of 4
QA1 Endura series rod ends. |
|
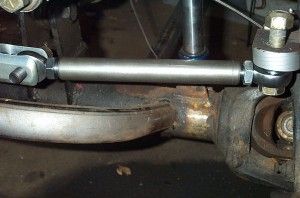 |
This gives you a basic idea
of the arrangement, with the cylinder on the left of the pic and the knuckles
steering arm on the right. Note, the mini tie rod shown is not included. |
|
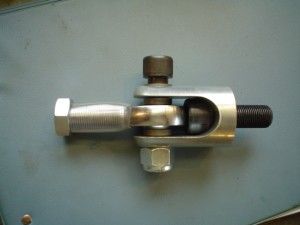 |
Two of the rod ends are 3/4"
shank and 5/8" ball bore and are used to connect the rod end of your
mini tie rods to the clevis end of the cylinder (pic at left). the other
2 rod ends are 3/4" shank and 3/4" bore for attaching the other
end of your mini tie-rod to the knuckles steering arm.
As can be seen at left, 6 small
machine washers are included for use with each clevis, to center the rod
end between the jaws of the clevis.
I found, however, that the
supplied socket head cap screws left the threads between the jaws of the
clevis, so the washers and rod end would be bearing against the threads
instead of the full 3/4" shank diameter. |
|
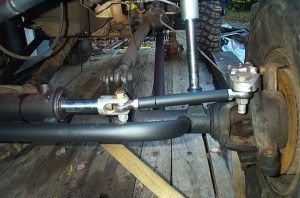 |
I wasn't happy with this arrangement
so replaced the supplied socket head cap screws with some Bowman Grade 8
hex head cap screws (bolts) that left a full shank diameter between the
jaws. |
Installation
Steering Unit
One of the great benefits to hydro
steering is the enormous flexibility one has in mounting the steering unit,
which then only connects to the steering cylinder (mounted to the axle) via
flexible hydraulic lines. This opposed to conventional power steering where
the steering gearbox must fit in a very specific location such that it can be
joined via mechanical linkage to both the steering wheel and the steering knuckles
(via the pitman arm and drag link / tie rod).
The steering unit can be mounted
virtually anywhere, within reason. However, there is a very important safety
consideration to take into account. I have seen many hydro steering systems
setup with the steering unit mounted inside the cockpit, connected to the steering
wheel by only a very short steering column. While this may make for a convenient
and "clean" install it is, in my opinion, EXTREMELY DANGEROUS and
therefore very very ill advised. This is because of a concept known as fluid
injection.
A fluid injections is a fine stream
of escaping pressurized fluid that can penetrate skin and enter a human body.
These fluid injections may cause severe tissue damage and loss of limb. Not
only will a fine stream of hydraulic fluid at 1500 psi slice through body tissue
like a hot knife, the resulting injection of pressurized toxic fluid deep into
the body can cause all manner of very serious medical complications. From SAE
j1273 "RECOMMENDED PRACTICES FOR HYDRAULIC HOSE ASSEMBLIES":
"Consider various means to reduce
the risk of fluid injections, particularly in areas normally occupied by operators.
Consider careful routing, adjacent components, warnings, guards, shields, and
training programs. Relieve pressure before disconnecting hydraulic or other
lines. Tighten all connections before applying pressure. Avoid contact with
escaping fluids. Treat all leaks as though pressurized and hot enough to burn
skin. Never use any part of your body to check a hose for leaks. If a fluid-injection
accident occurs, see a doctor immediately. DO NOT DELAY OR TREAT AS A SIMPLE
CUT! Any fluid injected into the skin must be surgically removed within a few
hours or gangrene may result. Doctors unfamiliar with this type of injury should
consult a knowledgeable medical source. Whipping Hose—If a pressurized
hose assembly blows apart, the fittings can be thrown off at high speed, and
the loose hose can flail or whip with great force. This is particularly true
in compressible-fluid systems. When this risk exists, consider guards and restraints
to protect against injury."
Pretty scary stuff - so the steering
unit should definitely be mounted outside the cockpit / driver compartment. |
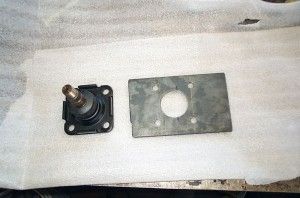 |
I made a small 1/4"
mounting plate... |
|
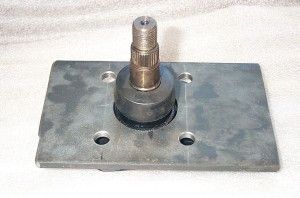 |
...that fit over the steering
column... |
|
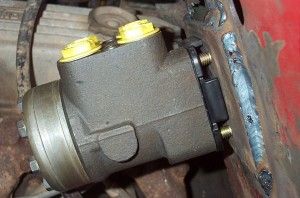 |
...and welded it to the firewall... |
|
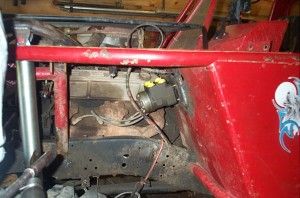 |
...so that the steering unit
was up high out of harms way, close enough to the driver to allow for a
simple, short steering column, but still safely on the other side of the
firewall. |
|
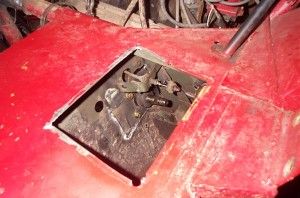 |
The stub steering shaft is all
that pokes through the firewall... |
|
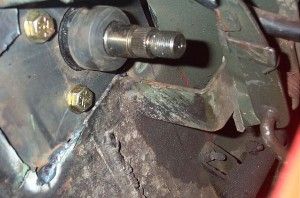 |
...leaving the 36 spline shaft
for you to connect your steering column/shaft too. |
|
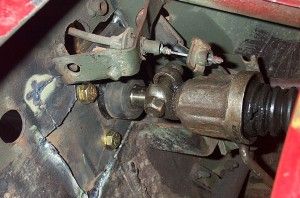 |
I used an old shaft from
an F250 that had this neat flexible coupling that, of course, fit perfectly
onto the steering shaft from Performance Off-Road Systems.
The other end of the column
(really just a solid 3/4" steel shaft) runs through a bearing for
support under the "dash" and then has the quick-disconnect coupling
for my steering wheel welded to it. |
Cylinder
One of the most tricky parts of the
installation is mounting the steering cylinder and getting the geometry right.
of course, every installation will be custom and so no set of instructions can
completely describe the process for everyone, but some general guidelines may
help: |
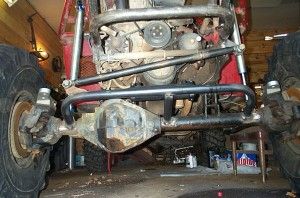 |
No matter how robust the
cylinder, you don't want it left vulnerable, hanging out front to get
damaged.
I built a large truss from
1.75" tubing angled forward and up in front of the axle to serve
as both a skid plate / guard for the cylinder as well as a place to mount
the cylinder.
You can see from this pic that
the cylinder is extremely well protected. |
|
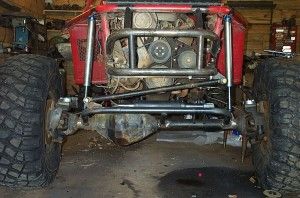 |
I tried various positions, eventually
settling on as high and far back as possible without interfering with the
crank pulley on full suspension compression. |
|
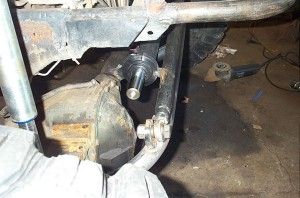 |
Clearance from the diff cover
is an issue. Not only must the cylinder shaft obviously not hit the cover,
but it would also be a large PITA to have to remove the cylinder every
time you wanted to remove the cover.
We managed to get my cylinder
positioned so that it clears the cover, the cover can come off without
moving the cylinder, and yet the cylinder is not too far offset to one
side of the axle. |
|
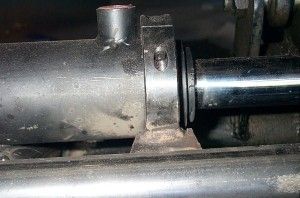 |
Here are the clamps
in place around the cylinder and welded to the truss. |
|
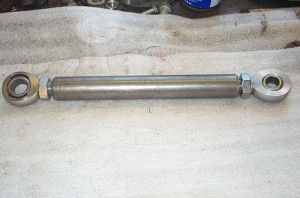 |
Mini tie rods have to be
constructed to connect the ends of the cylinders shafts to the steering
arms on the knuckles. |
|
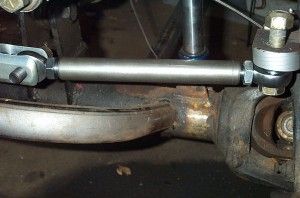 |
This is an early mock-up showing
how the tie rods are positioned. There is one each side. |
|
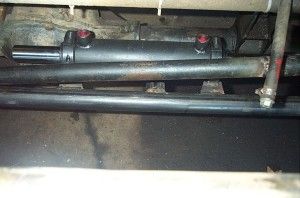 |
Cylinder clamped in place with
ports facing up. The port on the left side of the cylinder (as viewed from
the drivers seat) is the one to which you direct fluid to extend the shaft
to the right, thereby steering the vehicle right. In other words, the left-end
port is Right, and the right-end port is Left. |
|
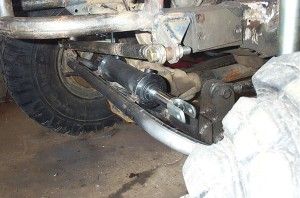 |
A side shot showing the positioning.
The cylinder does not have
to be mounted dead center in the middle of the axle (which is a good thing,
because if it did, either the diff would be in the way, or you would have
to have it stuck way too far out in front).
However, you should not mount
it such that it is more than 30% off center. this is because, the more
off center it is, the greater the difference in length between the 2 mini
tie rods. If the shorter of the tie rods gets too short, it will have
to move in too much of an arc as it's knuckle steers from full left to
full right. As it moves through this arc, if there is too much of an angle
created between the knuckle and the cylinder shaft, undesirable side loads
can be imposed on the cylinder shaft that can wear or damage seals or
the shaft itself.
having said that, the Performance Off-Road Systems cylinder
is the biggest and strongest available, specifically designed to be able
to handle some degree of side-loading. |
|
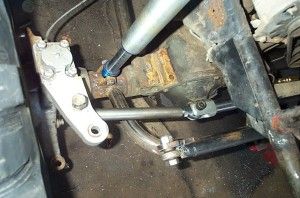 |
Here you can see what I mean
about the angle of the tie rod.
In these initial installation
pics, you will notice that I am using my OTT steering arms.
However, a problem readily
became apparent with the use of these arms with my new setup / geometry. |
|
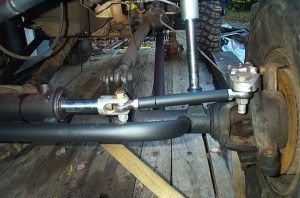 |
Because the OTT arms are
designed to be able to accommodate virtually all combinations of rims
and backspacing, the distance from the center of the kingpin to the tie
rod holes is quite short, in the order of 4.5" I believe.
This means that, in order for
the cylinder and tie rods to all lie in a nice straight line, the cylinder
itself would have to be mounted virtually directly on top of the axle
tube.
And the problem with that approach
is that you would need a lot of "lift" in order to create the
space necessary and not have the cylinder smacking the crank snout or
radiator or chasis. |
|
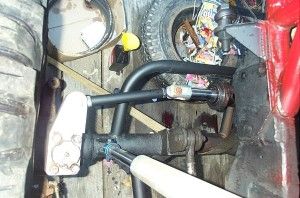 |
I was unwilling to add any chasis
height for this purpose, so I mounted the cylinder where I wanted it and
made do with the mini tie rods angling back to the short steering arms. |
|
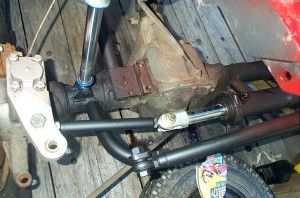 |
However, this created tie
rod angles I am not happy with and also resulted in me being unable to
use the cylinders full 8" stroke.
As I write this I am currently
working on a new steering arm setup that will have the kingpin-to-tie-rod-hole
distance closer to 6.5 or 7". This will allow full use of the entire
cylinder stroke and allow me to keep the mini tie rod in a straight line
with the cylinder shaft when the shaft is fully extended and at it's most
vulnerable.
Stay tuned for an update later
on.... |
|
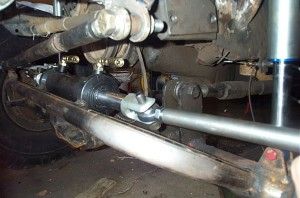 |
Pic showing tight spacing between
panhard bar in front and crank pulley behind the cylinder. |
|
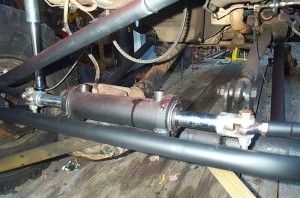 |
When setting up the cylinder,
you also need to account for any cylinder stroke not used because of your
geometry. In other words, you MUST have the cylinder run out of stroke
before, or right as, the steering stops are reached.
This is because of the enormous
force possible from the system. If the steering stops hit before the cylinder
is out of stroke, and the pump is producing healthy flow and pressure,
it is quite conceivable that continuing to turn the steering wheel after
the knuckles reach their stops would simply shear the knuckles right off
the housing. |
|
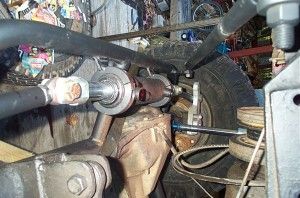 |
Even though my initial geometry
was not great, and the angled tie rods and short steering arms meant the
cylinder had an inch of stroke left after the steering stops hit, I was
unable to test the knuckle shearing theory (though I did try) as my pump
at the time was anaemic and weak. |
|
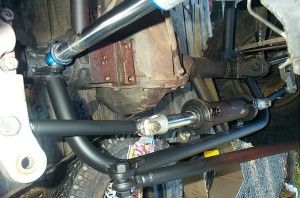 |
Shot showing knuckle to knuckle
geometry of original design. |
|
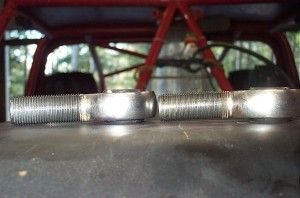 |
Even though my initial testing
was done with a weak pump, and didn't include any real hardcore wheeling,
somehow I managed to bend one of the outer-most rod ends. In this pic, the
one on the left seemed fine after the first 2 runs, but the one on the right
in the pic (which came off the right side of the buggy) was bent slightly
when I removed it. |
|
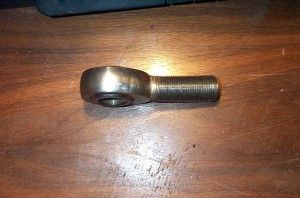 |
The rod ends are quite beefy,
and a good quality joint, so I suspect something was initially amiss with
the geometry. As I said before, mounting the cylinder and getting the linkages
and geometry all correct is likely the most challenging part of the upgrade. |
|
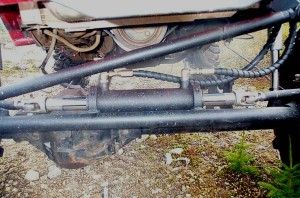
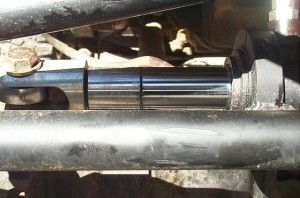
|
If you look closely at these
early testing pics, you can see that the geometry (short steering arms
to be precise) only allowed for 3/4 of the cylinder's stroke to be used
(you can tell by the wear markings on the cylinder shaft). This is probably
what allowed the rod end to get bent as the cylinder continued to push
to that side after the steering had run out of travel, and the weakest
link, in this case the rod end, deformed under the load. |
Reservoir |
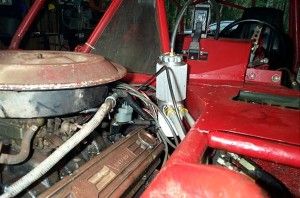 |
Mounting the reservoir
is fairly straightforward. If you decide to run it vented, as I did, it
must be both the highest point in the entire system; and also the only vent.
To that end - if you are using it in conjunction with a stock reservoir
of some kind (particularly an attached-to-pump stock reservoir) that is
vented (be warned - the vent may not be obvious - many stock setups were
designed to vent via the threads in the reservoir cap), you will have to
seal up the original vent. |
|
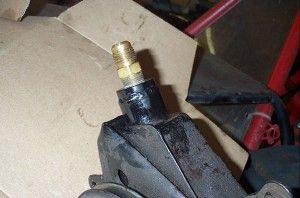 |
In my original system setup
I used a stock Saginaw P-style PS pump with the attached tear-drop (or "can-o-ham")
reservoir that was originally vented through the cap threads. In order to
seal the vent, and run the stock reservoir in series with the new CFR, I
asked my good buddy Rue to TIG weld a piece on the reservoir neck in place
of the cap; which we subsequently drilled and tapped for a pipe fitting.
I then used a 1/2" NPT to -10 JIC fitting to which i attached my suction
line which I then ran back to the -10 JIC outlet fitting of the CFR. The
ends of the suction line are terminated with hose-barb to -10 JIC adapter
fittings. |
|
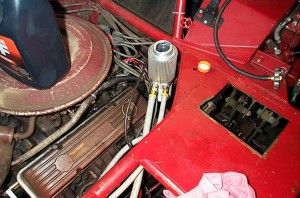 |
I mounted the reservoir back
near the firewall where it could get some airflow for cooling. |
|
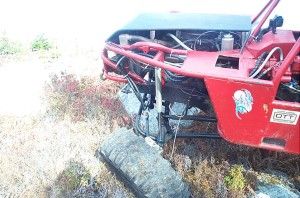 |
I am going to investigate adding
a larger reservoir soon, as I believe this small reservoir is barely adequate
in terms of size. Recall from Part 2 that standard industrial system design
practice is to specify a reservoir size of 2-3 times the gpm of the pump.
In my case, the pump flows 3.7 gpm, making a min reservoir of over 6 gallons.
Obviously that size is neither practical, nor required, as I am running
only a single cylinder, rather than many cylinders or actuators for lifts,
buckets, forks, rams etc. However, if you also recall from part 1, all of
the many important functions of the reservoir, I feel that this reservoir
alone, at only approximately 1/3 of a gallon to be inadequate in capacity.
I say this because I have found that fluid level is extremely critical and
that there is little (if any) reserve fluid capacity that the fluid is at
risk of excessive turbulence, aeration, and foaming - all conditions a properly
sized reservoir is designed to reduce. |
Pump |
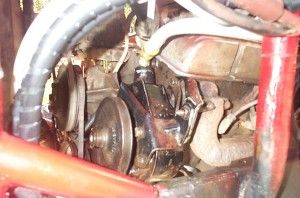 |
Here's the modified P-style
Saginaw pump used in my initial system. Note the 5/8" suction line
supplying fluid to the reservoir from the remote auxiliary cooler/filter/reservoir
assembly.
After struggling with some
strange plumbing problems, the worst of which was the vented reservoir
from Performance Off-Road Systems puking hydraulic fluid out the top of a 2' vent hose, that we
couldn't fully troubleshoot before I lost my mind in frustration, I ended
up replacing the pump and suction line, as well as deleting my Hydroboost
brakes all in one go. |
|
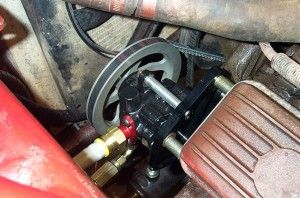 |
This is the KRC cast Iron pump
with 6" Aluminum V-belt pulley I settled on. I mounted to to the left
head of the 350 with the KRC bracket kit. |
|
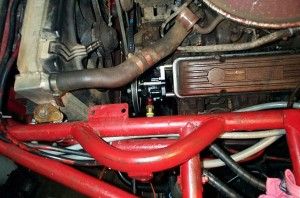 |
It is a very compact unit, that
installed easily and very cleanly. I had to get a longer V-belt to run it,
and makes some small custom spacers to mount the bracket to the head so
that everything lined up perfectly (because of my non-stock water pump housing). |
|
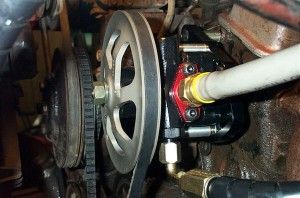 |
These pumps are high volume
pumps with standard flow of 2.5 GPM. With the interchangeable flow valves
the flow can be set anywhere in the range 1.5 GPM to 3.7 GPM. These units
have the same pulley offset and mounting pattern as the GM Saginaw style
pumps.
They run at 1350-1450 psi,
and I chose the highest flow of 3.7 gpm to feed my steering unit. |
Plumbing
This was a PITA, plain and simple.
I was pretty much on my own, and ended up trial and error'ing my way through
a bunch of stuff, buying way more than I needed, having to redo stuff more than
once, ending up with a drawer full of used, useless fittings etc etc.
Oh well - at last you can learn from
my mistakes!
Note: Originally I incorporated hydroboost
brakes into my system. I had some big problems with my plumbing, extremely frustrating
problems that I was unable to isolate or solve before cutting the entire hydroboost
brake system out (in part because I suspected a faulty hydroboost booster) of
the hydraulic circuit. The problem is, I may never know exactly what the problem
was as I replaced some hoses and the pump itself all in one go - I was that
frustrated. As such, this article will concentrate on a hydro steering system
without any other hydraulic components (such as hydroboost brakes). If I ever
return to hydroboost and sort out the plumbing I will update the article.
The usual flow of fluid through the
circuit will be: Reservoir --> Pump --> Steering Unit --> Cylinder
-->Steering Unit --> Cooler and/or filter --> Reservoir.
There are 3 types of hose you will
be running in a hydro steering system: pressure hose, return hose, and suction
hose. Each has a different requirement.
The following table summarizes all
the hoses and fittings I ended up using in my system. I used Parker hose and
fittings, and also made a small pdf file of the appropriate Parker catalogue
pages that show the hose and fittings I used. I even highlighted in yellow the
parts that I used. You can view it by clicking below: (NOTE: In the catalogue,
I highlighted the 801 Push-lok hose in 1/2" and the -10 JIC to 1/2"
hose barb fittings, because that's what I actually used. However, I also highlighted
the 821 Push-lok hose in 5/8" and the -10 JIC to 5/8" hose barb fittings.
because in retrospect these would have been a better choice, being larger ID
and still rated for a full 28" Hg Vacuum as a suction line. The reason
I didn't use the 5/8" 821 was, my supplier doesn't stock it. This meant
had to drop down to the 1/2" size in the 801 hose as this was the only
way to retain the full vacuum rating of 28". This is important to your
suction hose (pump supply) doesn't suck closed at higher RPM's. Bottom line
- use the largest diameter suction line from reservoir to pump that you can,
but MAKE SURE it is rated for a full 28" Hg (Ask me how I know !!) |
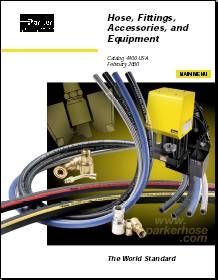 |
Parker Hose and Fittings used on the Wolf |
Use
/ Location |
Product |
Part
# |
Ref
# in pic at right -> |
Pic |
Hose
Assembly - Pump to Steering Unit |
PS Pump Outlet |
Aluminum -6 JIC supplied with
pump |
n/a |
V |
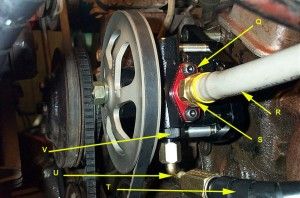 |
PS Pump Outlet Fitting |
Parker 42 Series Field Attachable
3/8" hose -6 Female JIC 37° - Swivel 90° Elbow - Short Drop |
23942-6-6 |
U |
HP Hose to Steering Unit |
3/8" Parker 421 Hydraulic
Hose - No Skive SAE 100R1 Type AT |
421-6 |
T |
Steering Unit HP inlet fitting |
Parker 42 Series Field Attachable
3/8" hose -6 Female JIC 37° - Straight |
20642-6-6 |
W |
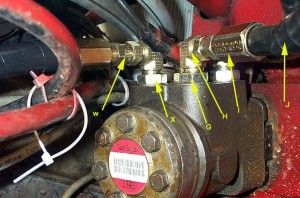 |
Steering Unit HP inlet fitting
adapter |
Parker -6 JIC 37° to -8
(3/4-16 UNF) ORB - 90° Elbow |
|
X |
Hose
assemblies - Steering unit to Cylinder |
Steering Unit L and R outlet
port adapters |
Parker -6 JIC 37° to -8
(3/4-16 UNF) ORB - 90° Elbow |
|
G/H |
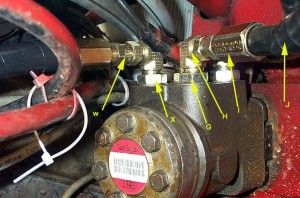 |
Steering unit end of hose fitting |
Parker 42 Series Field Attachable
3/8" hose -6 Female JIC 37° - Straight |
20642-6-6 |
I |
HP Hose to cylinder |
3/8" Parker 421 Hydraulic
Hose - No Skive SAE 100R1 Type AT |
421-6 |
J |
Cylinder end of hose fitting |
Parker 42 Series Field Attachable
3/8" hose -6 Female JIC 37° - Straight |
20642-6-6 |
O/L |
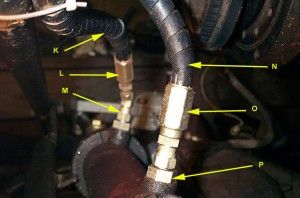 |
Cylinder L port adapter |
Parker -6 JIC 37° to -8
(3/4-16 UNF) ORB - 45° Elbow |
|
M |
Cylinder L port adapter |
Parker -6 JIC 37° to -8
(3/4-16 UNF) ORB - Straight |
|
P |
Hose
Assembly - Steering unit to Reservoir (return) |
Steering Unit T outlet port
adapter |
Parker -6 JIC 37° to -8
(3/4-16 UNF) ORB - 90° Elbow |
|
3 |
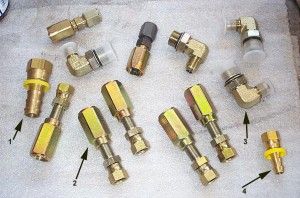 |
Steering unit end of hose fitting |
Parker 82 Series "Push-lok"
3/8" hose barb to -6 JIC 37° Swivel - straight |
30682-6-6 |
4 |
LP Return hose (routes through
aux tranny cooler that has built-in hose barb fittings) |
3/8" Parker 801 General
Purpose Hose For use with “Push-Lok” Fittings |
801-6 |
F |
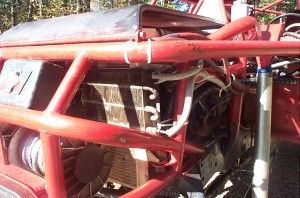 |
Reservoir end of hose fitting |
Parker 82 Series "Push-lok"
3/8" hose barb to -6 JIC 37° Swivel - straight |
30682-6-6 |
E |
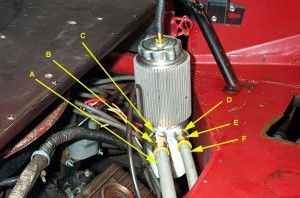 |
Reservoir inlet fitting |
built-in -6 JIC 37° |
n/a |
D |
Hose
Assembly - Reservoir to Pump (supply (suction) line) |
Reservoir outlet port fitting |
built-in -10 JIC 37° |
n/a |
C |
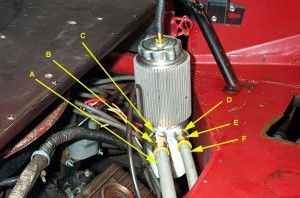 |
Reservoir end of hose fitting |
Parker 82 Series "Push-lok"
1/2" hose barb to -10 JIC 37° Swivel - straight |
30682-10-8 |
B |
LP Vacuum rated suction hose |
1/2" Parker 801 General
Purpose Hose For use with “Push-Lok” Fittings |
801-8 |
A |
Pump end of hose fitting |
Parker 82 Series "Push-lok"
1/2" hose barb to -10 JIC 37° Swivel - straight |
30682-10-8 |
S |
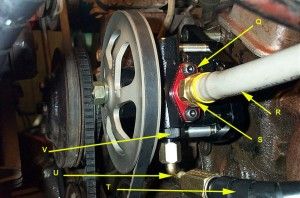 |
Pump inlet fitting |
built-in aluminum -10 JIC 37° |
n/a |
Q |
Browse the complete Parker hose and
fitting catalogue at:
Parker Hose & Fittings Catalog
Custom making hydraulic
hoses at home with field attachable fittings |
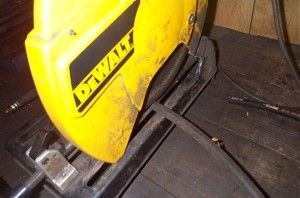 |
Cut the hose to
length with a quality hacksaw or abrasive chop saw. |
|
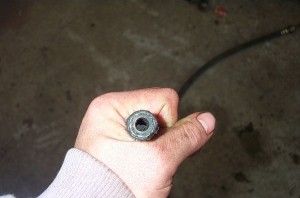 |
Be sure you clean out the debris
from inside the hose after the cut, and then lubricate the inside of the
hose with hydraulic fluid. |
|
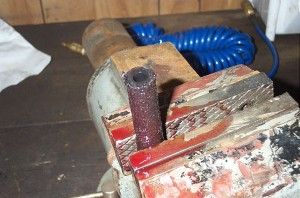 |
Clamp hose in vice. |
|
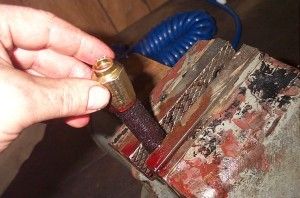 |
Place socket over hose and screw
on counterclockwise until it bottoms. |
|
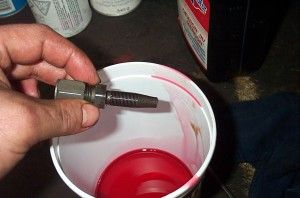 |
Lubricate insert with fluid. |
|
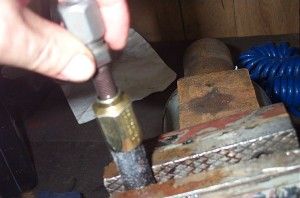 |
Thread insert into socket. |
|
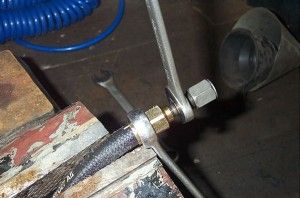 |
Tighten insert until it almost
bottoms (leave about thickness of a dime between insert head and socket. |
Bleeding the system |
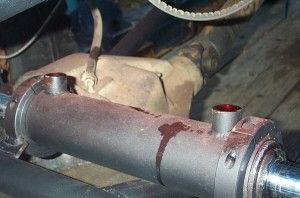 |
In preparation for
the step of bleeding all the air from the system it is a good idea to pre-charge
all of the components with fluid, as much as possible. I used a small funnel
to fill the cylinder - it took almost half a quart! You can't get any fluid
in the steering unit really, so that just leaves filling up the cooler if
you can and of course the reservoir. |
|
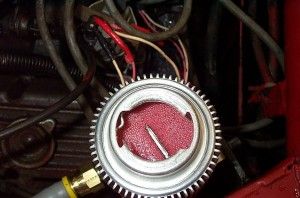 |
Once you have everything
installed and plumbed, it's time to fill and bleed. The procedure I discovered
works well is:
- Fill reservoir to just
over tip of column
- Raise front tires off ground
to remove resistance
- Turn steering wheel lock-to-lock
while constantly checking the reservoir for air bubbles and level drop.
Top us as necessary - be careful not to over-fill. When no more air
appears to bubble out and the level remains constant, go to step 4
- Check fluid level in reservoir,
disconnect coil wire, and crank engine over to operate pump and flow
fluid through entire circuit. Crank in short bursts. When no more air
appears to bubble out and the level remains constant, go to step 5
- Re-connect coil wire.
- Check fluid level in reservoir
and start engine. Operate at low rpm's at first, do not turn steering
wheel. After a few seconds shut down engine and check reservoir. It
will likely look like the pic at left, frothy and full of air bubbles.
Allow bubbles to dissipate (can take upwards of an hour) and repeat
this step until frothing does not occur.
- Check fluid level in reservoir
and start engine. Operate steering lock-to-lock while constantly checking
the reservoir for air bubbles and level drop. Top us as necessary -
be careful not to over-fill. When no more air appears to bubble out
and the level remains constant, go to step 8
- Top up reservoir, install
reservoir cap, lower front tires to ground.
|
Complete System
In case you haven't seen enough,
here are a few more pics of my system, as it stands right now. |
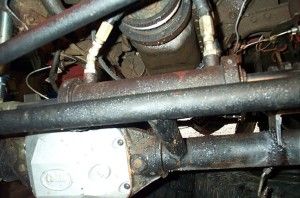 |
Cylinder and hoses. |
|
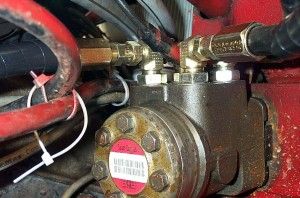 |
Mounted and plumbed Steering
Unit. |
|
 |
Low Pressure "Push-Lok"
connections at the Cooler/Filter/Reservoir. |
|
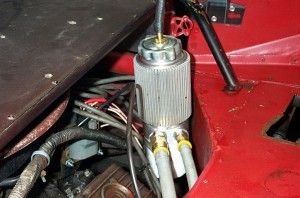 |
CFR mounted with vent hose on
cap. |
|
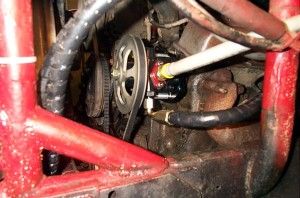 |
PS Pump mounted and plumbed. |
|
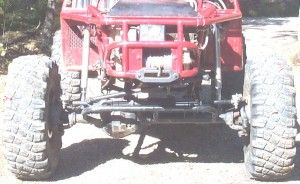 |
Cylinder location. |
|
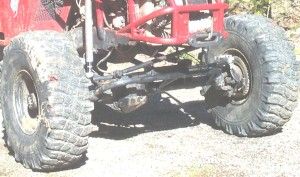 |
Steering is high and well protected. |
|
 |
- Cylinder ports
- Cylinder
- Tie rod
- Cooler
- Pump
- Steering Unit
- Hoses to Hydroboost brake
booster (deleted in final system config)
- Hydroboost booster (deleted
in final system config)
- Cooler/Filter/Reservoir
|
Performance
AT LAST - This is the
most important bit, right?
I am THRILLED to report
it is everything I had hoped it would be and more. Not only that, but none of
the negative things I had read were even remotely true either!
First - what it isn't.
All the tings you may have read,
certainly that I had read, about hydro steering, all the negatives and drawbacks
- none were true of my system. The steering wheel returns to center fine after
a turn. There is plenty of "road feel' both at speed and in the rocks.
It is not "squirrely at speed", at least not up to 45-50mph, despite
being approximately 2.5 turns lock-to-lock. It doesn't wander, there is no fade,
and, when plumbed properly and with all the components in top shape (no crapped
out old pump or malfunctioning hydroboost booster or improperly rated suction
hose sucking closed at high rpm - all mistakes I made of course!) it is cool
and quiet.
I attribute this to the fact that
the components themselves and in particular the system is designed for my specific
application. The steering unit has the proper displacement for my pump and turns
lock-lock desired. My new pump produces the appropriate flow and pressure, hoses
are properly specified and sized, cylinder is custom built for purpose, etc
etc. I believe a lot of the "negative" feeling and opinion / experience
you may read about "out there" on the net comes from the early days
of guys pioneering the idea of 4x4 hydro steering (no offence to them - they
did us all a service) with used, mismatched, parts scavenged from broken combine
harvesters and wrecked forklifts and such. As you are now fully aware - this
can lead to all manner of wacky results - you need only review the section in
Part 2 about system design to understand this. I am pleased to report that none
of these faults are present in my system.
Second - what it is.
Quite simply - the best steering
I have ever experienced, on ANY vehicle I have ever owned or driven, with the
exception of an extremely expensive sports car I rented once at one of those
fantasy places. Not only can I now steer my welded and slugged, 38" @ 5
psi shod Dana 60 sitting still on the rocks LOCK to LOCK with just one finger...but
the feel and response at (moderate) speed is unbelievable! There is no slop
at all At speed, (granted, we're only talking up to 40-50 mph here, as that
is as fast as I have driven the Wolf) it is tight and precise. I'd never driven
a 4x4 with a slop-less steering system before - usually a huge amount of the
slop is the hallmark of a 4x4. Not so anymore. Being a fluid power system, there
are no gears requiring backlash, and with the only joints being the rod ends
between cylinder and steering arms, and those being brand new ptfe lined units,
there is simply no slop in the system. This alone makes it a joy to drive again.
But the real thrill is in the rocks
and over the tough stuff |
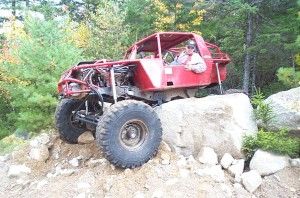 |
This was the
first obstacle on the first trail on my first ever day of testing. At
this time I didn't have the tie-rod / steering arm geometry right, the
presumed dysfunctional hydroboost booster was still plumbed in the system,
and the old worn out pump was running the show. As a result the reservoir
was puking fluid out the vent hose and into a catch can bungee tied to
the hood.
Even with those limitations,
the steering was superb.
In this pic, with the old steering
gearbox setup, and with me being in welded front low-low with drive slugs
in the hubs, steering in a situation like this would have been impossible.
I'm just about high-centered, and the front tires are over but still up
against the rock while the rear tires are just meeting the back side of
the rock. With forward progress stopped, steering the old fashioned way
would be impossible. Not only that, but I would have been forced to dismount
and press the winch into service. |
Not so with my new hydro steering.
Even in a situation like this, with no forward progress, essentialy stuck,
with welded fromt diff, I could easily steer back and forth with only
2 fingers and the engine just idling.
In the end I was able to just
wiggle the steering back and forth from this position, grab some traction,
and pull my self over the boulder.
Actually, that was an unexpected
by very cool advantage to the mod - I never thought of hydro steering
as a traction aid, but throught my expereince and testing so far i have
found many times that the ease of steering allowed me to wiggle around
and find traction in situations that before would have left me hung up
and looking for a yank or winch. VERY COOL! |
|
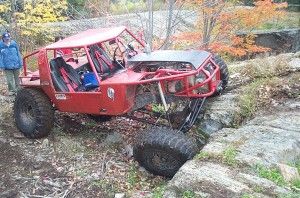 |
Even while scraping the diff
and axle tube over rocks the steering remains well protected. And again,
in this spot, with the passenger front in a hole and up against the rock,
I was easily able to steer back and forth to find traction. |
|
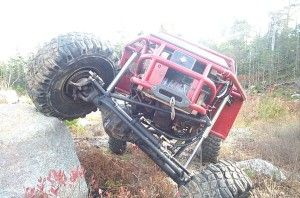 |
In this spot I drove up with
the steering cranked hard to the right, and let the suspension fully twist
up. Leaving the engine idling in neutral with the rear line lock on I was
able to hop out and crank the wheels from lock to lock with 2 fingers standing
beside the rig. |
|
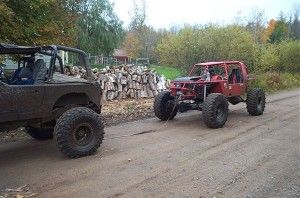 |
And I can fully attest to the
manual steering capability of my Danfoss steering unit. I killed an alternator,
a battery, and a coil in one trip (bad day electrically!) which lef me on
the strap behind Chad's YJ the whole way out. It wasn;t easy or comfortable,
but it works. |
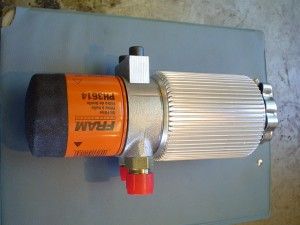 |
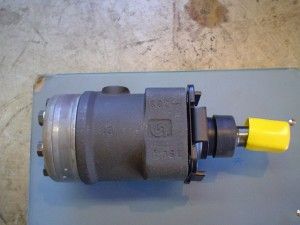 |
Conclusion
Good
High quality components, excellent
steering unit, awesome custom cylinder, totally kickass performance, great price,
terrific no-BS friendly, knowledgable guy to do business with.
For Improvement
I'm not much of a fan of the supplied
reservoir unit - I feel it is too small and needs a quality vented cap option.
The "through clevis" bolts supplied need a longer shoulder to bear
the rod end, however I know Sean is already in the process of researching better
fitting higher quality fasteners, and may already have something available by
the time you read this. I had my share of challenges getting my system plumbed
and running properly and ended up having to trial and error my installation
- a standard kit of hose and fittings may have been helpful.
Verdict
Buy it! Buy it now, do not suffer
any longer. Buy it, install it carefully, bleed it diligently and enjoy the
finest 4x4 steering you have EVER experienced. Live the dream of effortless
powerful steering and you will never want to drive a rig without a Performance
Off-Road Systems Hydro Steering System again!! |
|