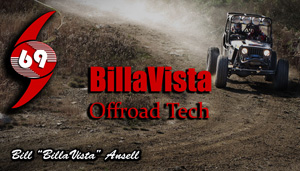 |
The Driveshaft Bible
By Bill "BillaVista" Ansell
Photography: Bill Ansell
Copyright 2008 - Bill Ansell
(click any pic to enlarge)
|
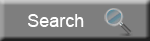 |
Introduction
In my quest to build my 1-ton rock buggy, The Wolf, as tough as possible, I upgraded my driveline from stock Dana 20 transfer case and hacked-together junkyard 1/2 ton pickup driveshaft to Advance Adapters D20 32 Spline Output and the famous 1 TON 1350 CV driveshaft from Jess at High Angle Driveline.
But before I explain why, how, what else Jess can do, and why High Angle Driveline build the best shafts in the business, I'm going to take you through a little (OK, a LOT!) of driveshaft tech. Why? For 3 reasons:
First, it's important we have a common understanding and language to use, so there is no confusion or misunderstanding (especially in this sport/hobby, where confusion, rumour, legend, and misunderstanding often run rampant - driveshafts being no exception); |
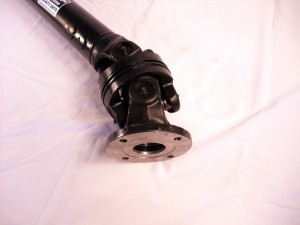 |
Second, because I'm just a super-geek when it comes to accuracy and terminology - you already know this if you've been reading my articles for a while now. Sure, it often get's me beaten up at club event's and four wheeling trips......but the guys really love me, I know they do ;-)
Third, and most importantly, it is because I am committed to bringing my readers only the very best in tech articles and product reviews. I don't do cheesy 2 pic, unwrap, install, "call it good" articles, where I claim the product is superb, even though I clearly know nothing about it. I am committed to providing you with the technical information and facts to make informed decisions, and in so doing, I hope to prove to you that I know a bit about what I'm talking about, and that my opinions, especially on products I recommend, are based on solid knowledge, fact, and experience.
There's a lot to cover, so this article is arranged in 5 broad sections, further subdivided as follows:
Part 1 - Definitions and Operating Descriptions
- Universal joints
- Driveshafts
- Methods of accommodating length change
- U joint Series
- Glossary
Part 2 - Driveshaft Geometry
- Driveshaft Geometry
- How to choose a driveshaft for your rig
Part 3 - Driveshaft maintenance
- Safety
- Driveshaft Maintenance
|
Part 4 - U-joint tech, failure analysis
- U-joint Tech
- Driveshaft failure analysis
- Spicer stock driveshaft application information
- Spicer driveshaft component catalogues
- Spicer part number decode information
- Driveshaft / U-joint technical bulletins
- Spicer driveshaft brochures
- Spicer driveshaft division training videos
|
Part
1 - Definitions and Operating Descriptions:
There are some very common misconceptions
out there about driveshafts, many of which revolve around terminology. To help
alleviate this, I offer the following information:
Universal
Joints: A universal joint is defined as a "shaft coupling
capable of transmitting rotation from one shaft to another not collinear
with it." In other words, it is a mechanical device that transmits
torque / rotary motion between two shafts that are not in a straight
line.
There are 2 types, the:
1) Cardan style universal
joint; and the
2) Constant velocity
universal joint
We shall explore them
both separately:
Cardan
Style Universal Joint |
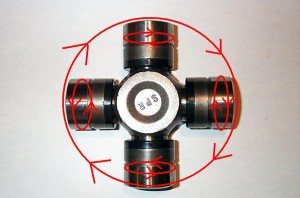 |
The most
common type we encounter is the cardan style universal joint, developed
by Spicer, and pictured
to the left. This is the familiar "cross and caps" style
universal joint, often just referred to as a "U-joint".
Remember though, that technically it is a cardan style universal
joint. |
The way the cardan style
universal joint works is as follows (and this is very important
to understand):
First - why do we need
to use a universal joint in the first place? The answer is easy,
and can be surmised from the above definition. |
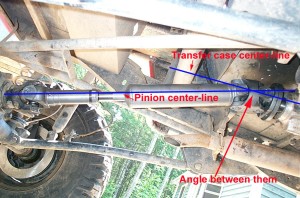 |
It is because we need
to transmit torque from the transfer case to the axle pinion, and
of course, the transfer case and pinion are not collinear - they
are not in a straight line. The t-case is above the pinion (obviously)!
Therefore there is an angle between them. In order to transmit torque
or rotation between 2 shafts that are at an angle, we must use a
universal joint. In the automotive driveshaft world, 99% of the
time that means we use a cardan (cross) style universal joint. |
|
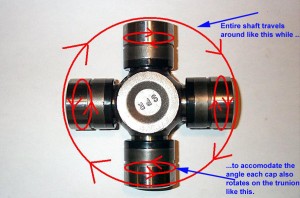 |
Because of the way the
cardan style universal joint operates when the 2 shafts it joins lie
at an angle (see pic to left - the joint cross or body rotates about
it's center, while at the same time the caps rotate around their trunnions),
the result is that the joint follows an elliptical, rather than a
circular path. |
To visualize how this
occurs, look down the length of a rear driveshaft at the U-joint
in the transfer case yoke. If the pinion end of the driveshaft were
unbolted from the differential and lowered to the floor, it would
create a severe angle in the forward U-joint. If the shaft were
then turned by hand, you’d then be able to see that the two
bearing caps on the U-joint center cross attached to the driveshaft
rotate in one plane while the two attached to the transfer case
yoke rotate in a different plane. All the while the center cross
is swiveling back and forth with each revolution. |
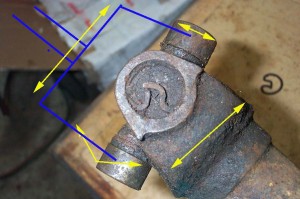 |
The best way to illustrate
this is to hold 2 shafts coupled by a U-joint in your hand and rotate
them- you will quickly see exactly what I mean. The crude drawing
to the left may also serve to illustrate what is happening. I have
drawn in blue a representation of a second yoke on the other side
of the joint from the actual yoke pictured. Now, what happens is,
the real yoke and the blue yoke, connected by the U-joint, both
rotate around in the direction indicated by the long double-headed
arrows. To accommodate the angle between the 2 yokes, the bearing
caps each rotate around on their respective trunnions, as indicated
by the short double-headed arrow. The result of the combination
of these two motions is the U-joint swiveling back and forth each
revolution, in a sort of see-saw back-and-forth motion, as indicated
by the "V" shaped double-headed arrow. Ultimately, this
leads to the elliptical path of the bearing caps, when viewed longitudinally
down the shafts. |
|
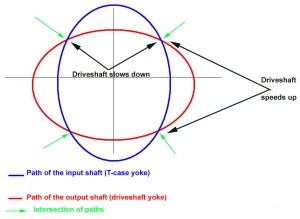 |
If you drew what’s
happening on paper (and of course I have done that for you :-), the
two bearing caps in the transfer case yoke would appear to be traveling
in an elliptical (oval) shaped path as viewed down the length of the
driveshaft (blue ellipse). Or, from the other point of view, the two
bearing caps on the driveshaft would appear to be traveling an elliptical
path if viewed from the transfer case (red ellipse). It is this difference
in geometry that causes the driven shaft to change speed with respect
to the driving shaft. |
So, we have two different
shafts, connected by a universal joint operating at an angle. Because
of this, the ends of the U-joint in each of the yokes in the 2 different
shafts (the t-case output yoke, and the yoke at the transfer case
end of the driveshaft) both travel in elliptical paths, but the
paths are 90° offset (out of phase) from one-another. In the
pic to the left, the blue ellipse represents the path of the input
shaft (t-case yoke) and the red ellipse represents the path of the
output shaft (driveshaft yoke). Because the 2 shafts are connected
to opposite bearing caps, their elliptical paths are offset 90°,
as can be seen in the pic.
Now, the problem is,
the t-case output is driven from the crankshaft by gears and/or
chain drive at a fixed rate (angular velocity) - let's say 1000
rpm for example. Of course, because the driveshaft is mechanically
connected to the t-case output, it also must be rotating at 1000
rpm. In the pic, the green arrows show where the two elliptical
paths cross, the points of intersection. At these points, the 2
shafts must be in the same place at the same time (otherwise the
assembly would come apart.) In order for this to happen, you can
see that at times the driveshaft's elliptical path (red ellipse)
is longer than the t-case yokes (blue ellipse) and vice versa. So,
in order for the assembly to remain together and driven at a fixed
rpm, the driveshaft must have to speed up and slow down at different
points along it's path in order to match the t-case yoke that is
being driven at 1000 rpm. The black arrows show where this happens.
In this case, the driveshaft will speed up and slow down a total
of 4 times per revolution. That is, it speeds up, slows down, speed
up, slows down, then repeats. This is the reason why we say a cardan
style universal joint transmits rotation/torque with a "variation
in angular velocity between the input and output shafts".
This speeding up and
slowing down can cause vibration of the driveshaft and significant
wear on the universal joints if not properly accounted for in the
driveshafts design. This "accounting for" is what we call
driveline geometry and will be discussed in great detail in part
2.
For now, remember that
a U-joint must be used because there's an angle between the t-case
and pinion (and often a very big angle in the case of lifted 4x4s
- which is why this whole driveshaft business is so important to
us in the first place). When a U-joint is used, and operates at
an angle, the bearing caps on the input and output shafts will describe
elliptical paths offset by 90° from one-another because of the
difference in geometry between the two opposing bearing caps in
the U-joint. Since they travel in elliptical paths, and yet must
remain fixed together driven at a constant rpm the driveshaft must
therefore speed up and slow down twice each per revolution. This
difference in angular velocity between the 2 shafts causes noise,
vibration, and U-joint wear, and must be accounted for in proper
driveshaft design.
The speed changes are
not great when the angle is less than a few degrees, but as the
operating angle of the joint increases so do the cyclic vibrations
of the driven shaft as well as the back and forth motion in the
joint itself.
Constant-Velocity
(CV) Universal Joint: |
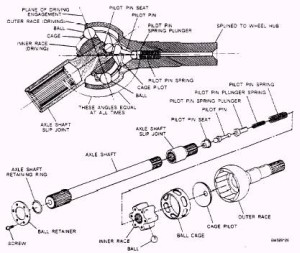 |
In marked contrast
to the cardan style universal joint, a true constant-velocity (CV)
universal joint is one that transmits torque/rotation with an angular
velocity ratio of unity between input and output shafts. In other
words, even at an angle, the input and output shafts travel at the
same (Constant) speed (Velocity) hence the name - Constant Velocity.
CV universal joints are not common in 4x4 driveshafts, but are very
common in front wheel drive car half-shafts (axles). The pic to
the left shows a very common style of CV joint, the Rzeppa joint,
invented in 1920 by a Dana engineer named Alfred H. Rzeppa |
Their common use in fwd
cars is because the joints in the half shafts must accommodate being
driven at high speeds for long times as well as changing compound
angles due to the front wheels being steered and the front wheels
cycling up and down with the suspension. As such, the inner and
outer joints in a fwd car half shaft often operate at different
angles. Whenever the wheels are turned the outer joint runs at a
much higher angle than the inner joint. This upsets the offsetting
relationship between inner and outer joint angles that’s a
necessary requirement for ordinary U-joints. What’s more,
the front wheels are required to steer at angles of up to 45 degrees—which
puts too much strain on a U-joint.
A CV joint, by comparison,
always splits the operating angle in half so the driven shaft turns
at the exact same speed as the input shaft. So no matter what the
joint angle, there are no changes in speed -- thus the name "constant
velocity."
Driveshafts:
A driveshaft is a device
that connects the transfer case to the axles, transmitting torque
from the engine to the driving wheels. It is also called a propeller
shaft or prop-shaft for short (mostly by Brits and Aussies). Virtually
all driveshafts (certainly all that I know of) fit into one of two
often misunderstood broad categories. They are:
EITHER
Cardan-style
universal joint driveshafts, subdivided into:
- Single-Cardan-style
universal joint shaft; or
- Double-Cardan-style
universal joint shaft
|
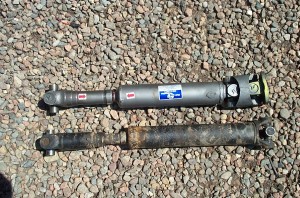 |
Pictured at left - double-cardan-style
universal joint shaft on top (my new High
Angle Driveline shaft) and a single-cardan-style universal joint
shaft (the junk I took out!)
Note
that, as you would expect, the double-cardan shaft has one end (the
transfer case end) that has a joint that contains, two cardan-style
U-joints - forming the "double-cardan" portion. More on
this later. |
OR
Constant
Velocity (CV) joint style driveshafts.
This is an important
distinction, if only academically. You see, true CV joint driveshaft
are rare in 4x4 driveshafts (some earlier Jeeps came with GKN
CV style front driveshafts that were tiny and weak) |
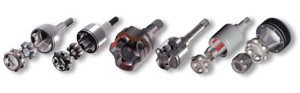 |
CV joints are, however,
extremely common in FWD car half shafts (half axle shafts). Pictured
at left are some GKN half-shaft CV joints. Virtually all modern
cars have them. Virtually all are made by GKN's automotive driveshaft
group. |
There are many different
types of CV joint, including Fixed Ball, Single Roller Tripod Plunging
Joint, Ball Plunging Joint, etc. You can read about them at http://www.gkndriveline.com/ None have anything to do with our needs and heavy-duty 4x4 driveshafts.
WHAT???? You cry. But
everyone's always talking about CV driveshafts - heck the title
of your own article is "1 Ton CV driveshaft" you hypocrite!
You're right - you see,
the very common double-cardan-style universal joint shaft (pictured
above, upper shaft in pic), is properly called a "near constant
velocity, double-cardan-style universal joint shaft." (incidentally,
this "velocity" we keep referring to is the angular velocity
of the joint in the shaft). Now, what has happened is that because
"near constant velocity, double-cardan-style universal joint
shaft" is such a huge mouthful, it has become common practice
to drop the "near" , "double-cardan-style",
and "universal joint" and what we are left with is common
convention leading to a double-cardan-style universal joint shaft
simply being referred to as a CV shaft.
There - now you know
the truth, and you can amaze your friends (or getting soundly beaten
by them for being a nerdy smart-ass) at the next trail-side campfire!
So, we know that true
CV joint driveshafts are of no interest to us, so forget them now.
That leaves us with either single or double cardan style driveshafts.
The latter, I shall bow to convention, an henceforth refer to them
as CV driveshafts, simply because everyone does.
Now, whether a 4x4s driveshaft
is single cardan (also called "regular' or "single-joint"
or simply "U-joint) or CV, there is one more distinction to
make.
All driveshaft's must
have some way of changing length, allowing the driveshaft to shorten
or lengthen as required, to accommodate suspension movement. This
is because suspension movement will cause the distance between the
output of the transfer case and the yoke on the axles pinion to
change somewhat. How much the distance changes, and therefore how
much "accommodation" you need in your driveshaft will
depend on a lot of different factors, including suspension geometry,
amount of wheel travel, whether the diff on the axle is centered
or offset, etc. For example, a 4 link coil sprung rear axle with
center limiting strap will require significantly less length change
accommodation than a soft leaf-spring-over-axle front axle with
shackle reversal, offset diff, and no limit straps. The former may
require only an inch or 2, the latter many inches. The only way
to know for sure is to flex the suspension and measure.
The 2 common methods
of accommodating this length change, or slip, are:
Type
1 - Slip-yoke shaft.
This style is a very common late model rear driveshaft factory style.
It comes stock in a great number of 4x4s, including Jeeps, Chevy's,
and many others. The slip-yoke is an internally splined tube that
slips into the rear output of the transfer case. As the name implies,
the slip yoke slips in and out of the transfer case output housing,
to accommodate driveshaft length change. generally, this type is
not favoured by the hardcore crowd as it's drawbacks generally include:
- Small U-joint size
(stock)
- Small tubing (stock)
- Limited travel in
the slip yoke
- The fact that the
transfer case output is sealed by the slip yoke, meaning that
if you break a U-joint or the shaft, and have to remove the slip
yoke, you have to have some sort of method for plugging the transfer
case output hole, otherwise the t-case will lose all its fluid.
|
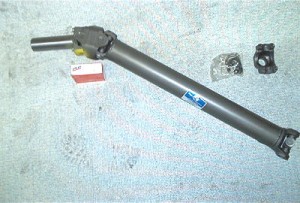 |
That said, High
Angle Driveline can build you a 1350 1 Ton CV slip-yoke driveshaft.
The pic to the left is just such a shaft. |
Type
2 - Slip-member shaft. This style is common on trucks and
4x4s, especially older trucks, and is the most desirable type.
They use a splined section incorporated in the shaft itself, called
the slip-member, which allows the shaft to change length. |
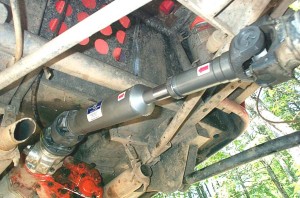 |
The pic to the
left is my new shaft installed, which is a slip-member style shaft.
The slip-member is easily visible between the red arrows. |
|
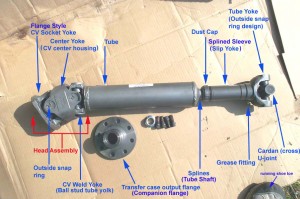 |
Now that we know all about
the different types of shafts, this picture illustrates the names
of the various parts of the drive shaft. Where there is more than
one common name, the alternate names are shown in brackets. |
Driveshaft
U-joint Series / Sizes
So we know all about
the different types, and all the parts, the last thing we need to
know before we can fully and accurately describe and talk about
driveshafts is the relative size (and therefore strength), normally
determined by and referenced to, the size (series) of the U-joints
used in the driveshaft.
A U-joint "series"
is a number that describes a group of cardan style universal joints
by common dimensional grouping. A series number is not an actual
specific part number.
The common U-joint series
used in light truck and 4x4 driveshaft construction, with dimensions
listed corresponding to the diagram are: |
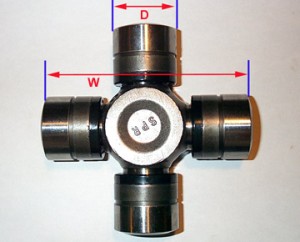 |
U-joint
series |
Joint
width (W) (inches) |
Cap
diameter (D) (inches) |
Maximum
Angle |
Continuous
rating (lb-ft) |
Short
Duration rating (lb-ft) |
1310 |
3.219 |
1.062 |
30 |
130 |
800 |
1330 |
3.625 |
1.062 |
20 |
150 |
890 |
1350 |
3.625 |
1.188 |
20 |
210 |
1240 |
1410 |
4.188 |
1.188 |
37 |
250 |
1500 |
|
Glossary
- Bearing Cup Assembly
— Consists of a bearing cup with needle rollers generally
held in place by a seal guard and bearing seal. Sometimes the
assembly includes a thrust washer.
- Bearing Cup —
A cup-shaped member used as the bearing bore of a bearing cup
assembly and for positioning a thrust end of a cross trunnion.
- Bearing Seal —
A flexible member of a bearing cup assembly which prevents the
escape of lubricant from or entry of foreign matter into a bearing.
- Boot — A flexible
member which prevents the escape of lubricant from or entry of
foreign matter into the slip member assembly.
- Boot Clamp —
A thin adjustable band used to hold the boot in position on the
slip member assembly.
- Boot Seal —
See Boot.
- Companion Flange
— A fixed flange member that attaches a steering shaft (intermediate
shaft) to a steering gear box or steering column shaft.
- Cross — See
Journal Cross.
- Cross Hole —
A through hole in each lug ear of a yoke used to locate a bearing
cup assembly.
- Ear— One of
two projecting parts of a yoke symmetrically located with respect
to the yoke’s rotational axis.
- End Fitting —
An end yoke or companion flange that attaches a driveshaft to
a transfer case or axle (pinion).
- End Yoke — A
yoke that attaches a driveshaft to a transfer case or axle (pinion).
- Flange Yoke —
A full-round style yoke which attaches a driveshaft to a transfer
case or axle (pinion).
- Glidecote® —
The blue, nylon, wear-resistant coating on Spicer yoke shafts.
- Grease Zerk (Nipple)
Fitting— The fitting on the shoulder or center of a journal
cross that allows for lubrication.
- Inboard Yokes —
Yokes that make up the ends of a driveshaft.
- Intermediate Shaft
— See Steering Shaft.
- Journal Cross —
The core component of a universal joint which is an intermediate
drive member with four equally spaced trunnions in the same plane.
- Lug Ear — See
Ear.
- Needle Roller Bearings
— See Needle Rollers.
- Needle Rollers —
One of the rolling elements of a bearing cup assembly.
- Outboard Yokes —
Yokes that are not a part of a driveshaft (i.e. yokes that are
part of a transfer case output or axle (pinion) input.
- Phasing — The
relative rotational position of each yoke on a driveshaft.
- Pinch Bolt —
Bolt used to compress slotted end fittings for retention.
- Purge— The
act of flushing old grease and contaminants from universal joint
kits with fresh grease.
- Slip Member Assembly
— Combination of slip spline, slip yoke and boot assembly.
- Slip Spline—
A patented tubular-type, machined element consisting of internal
splines in a driveshaft assembly.
- Slip Yoke —
A slip member yoke with a female machined spline used for axial
movement.
- Slip Yoke Plug —
See Welch Plug.
- Snap Ring —
A removable member used as a shoulder to retain and position a
bearing cup assembly in a yoke cross hole.
- Snap Ring Groove—
A groove used to locate a snap ring.
- Spline — A
machined element consisting of integral keys (splined teeth) or
keyways (spaces) equally spaced around a circle or portion thereof.
- Trunnion(s)—
Any of the four projecting journals of a cross.
- Universal Joint —
A mechanical device which can transmit torque and/or rotary motion
from one shaft to another at fixed or varying angles of intersection
of the shaft axes. Consisting usually of a journal cross, grease
zerk (nipple) fitting and four bearing cup assemblies.
- Universal Joint Kit
— See Universal Joint.
- U-Joint — See
Universal Joint.
- Welch Plug—
A plug in the slip yoke face that seals off one end of the spline
opening. Also known as a slip yoke plug.
- Yoke Lug Ear Cross
Hole — See Cross Hole.
- Yoke Shaft —
A slip member yoke with a male machined spline used for axial
movement.
So now that we know all
the terms and definitions regarding Driveshafts, what else do we
need to know to get the best, world class, bulletproof driveshaft
under our truck?
Well - the answer is
....depends. It depends on what kind of person you are. If you just
want the job done, so you can get behind the wheel, the answer is
NOTHING. You simply call up Jess at High Angle Driveline @ (530) 877-2875 and have a nice chat with him about your needs.
He will help you with whatever you need, discuss your options with
you, and be pleased to talk to you about driveshaft tech, and his
customer service is second to none.
However - if you're a
tech-geek like me - you want to know more.
Part
2 - Driveshaft Geometry
Proper driveshaft geometry
is critical to getting the most from your driveshafts. Improper
geometry will cause vibration, excessive wear, and premature failure.
Even the best driveshaft in the world will suck if it is not installed
with proper geometry. We also need to know about proper geometry
in order to select the best type of shaft for our application.
Before we discuss geometry,
a couple more definitions of some terms are in order. For the purposes
of this article:
Terms |
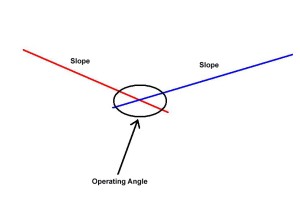 |
Angle:
An angle is the measurement
of angularity, in degrees, between any two planes. Where those 2
planes meet, they form an angle. In other words, where two lines
intersect, providing they are not parallel, there is an angle. In
the case of driveshaft tech, where something rotates through that
angle, we call it an "operating angle"
Slope:
Slope. A slope is a special
kind of angle. It is the angle formed between the horizontal surface
of the earth (one plane), and the object in question (e.g. driveshaft)
(second plane). |
When talking
about driveshafts, we say that a slope is down if, when viewed from
the side of the vehicle, it is higher at the transfer case and lower
at the axle (i.e. it descends from the center to the rear of the
vehicle for a rear driveshaft or descends from the center to the
front of the vehicle for a front driveshaft). The slope is up if,
when viewed from the side of the vehicle, it is lower at the transfer
case and higher at the axle (i.e. it rises from the center to the
rear of the vehicle for a rear driveshaft or rises from the center
to the front of the vehicle for a front driveshaft).
Phase:
We say that 2 U-joints
are in-phase if they are fitted to yokes that are fixed on the same
shaft, such that the 2 opposing bearing caps in the U-joint that
are held captive by the yoke on the shaft (the inboard yoke's U-joint
caps) are both in the same orientation. |
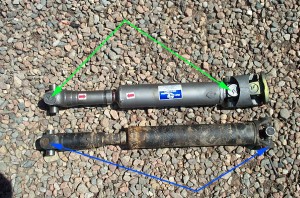 |
A pic is worth a thousand
words. Look at the pic to the left. In the top shaft, the 2 joints
indicated by the green arrows (ignore the fact that the right-most
is part of a double cardan CV assembly) are in-phase because in
both joints, the bearing caps held captive in the shaft are both
vertical, while the bearing caps that are free (not held captive
in the shaft) are both horizontal. If you then look at the bottom
shaft, you will notice that this is not the case with the joints
indicated by the blue arrows. The left has captive bearing caps
vertically oriented, while the right most joint has it's captive
bearing caps oriented horizontally. The joints are therefore 90°
out of phase. |
Note that this means
that they would be in phase if you rotated one or the other 90°
(by cutting and re-welding the shaft). Note also that 90° is
the most they can ever be out of phase, for as you pass through
90° difference between the two joints orientation, you begin
to come back into phase.
U-joint
life span. |
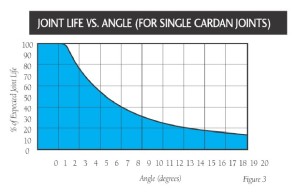 |
One geometry factor
that is common to all shafts, regardless of type, is the decrease
in U-joint life span that is experienced with an increase in the
operating angle of that U-joint.
No matter what the shaft
style, the greater the angle a U-joint operates at, the shorter
it's life span will be. The graph at the left comes directly from
Spicer, and shows the range from 100% expected life span at 0°
up to just over 15% expected life span at 20°. |
As we learned in part
1, there are 2 types of driveshaft that interest us, each with their
own separate geometry requirements.
Single-Cardan-style
universal joint driveshaft geometry |
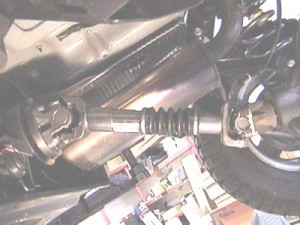 |
The single-cardan style
driveshaft, also called a "standard" driveshaft, consists
of a tubular shaft with 2 tube yokes, one at each end, that each
utilize a single cardan U-joint. Recall how, when we have a single
U-joint operating at an angle (as will certainly be the case in
any 4x4 because the transfer case output will be above the pinion)
it causes the driveshaft to speed up twice and slow down twice each
revolution. Uncorrected, this change in angular velocity will cause
annoying vibration, wear out U-joints, and cause undue stress and
strain on the driveshaft itself, transfer case output, and axle
pinion. |
|
 |
The solution is simple
and elegant. If we ensure that the U-joints at each end of the shaft
are both "in phase" and operating through exactly the
same angle, the pinion end of the driveshaft will speed-up and slow
down opposite to the transfer case end, and therefore the different
angular velocities cancel one another out, the pinion is driven
at a steady rate, and vibration is minimal (if I did a decent job
of describing why the elliptical paths happen in the first place
- you should be able to prove this to yourself). This works fairly
well up to angles approaching the maximum operating angles of the
U-joints in question. As the angles grow, so do the magnitude of
the accelerations and decelerations, and the less effective the
matched angle are at eliminating vibration. |
In other words, eventually,
you may have a driveshaft operating at such an angle that, even
though the input (transfer case) and output (pinion) operating angles
match exactly, the shaft will still vibrate. At this point, it's
time for a double cardan CV driveshaft! |
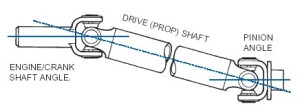 |
Note that in the standard
single-cardan shaft "match the angles" geometry the angles
do not have to be the same "sign". THIS IS A COMMON MISCONCEPTION.
Certainly, the most common method of achieving proper single-cardan
shaft geometry is to set the transfer case output and pinion shaft
centerlines parallel, thus achieving equal angles between each end
of the driveshaft (pic at left). |
Normally, this is done
by rotating the axle housing (with shims in a leaf-spring suspension,
or with relative lengths of upper and lower control arms with a
link suspension). This is because the transfer case output is usually
considered pretty fixed - the only way to adjust it is to either
lower the transfer case (an all around bad idea and bad deal - I
speak from experience) or to tilt the engine up (raise the engine
mounts) again - not a good idea). |
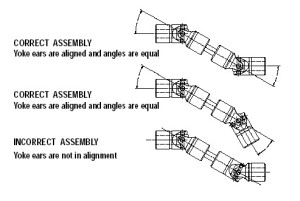 |
However - this is not
the only acceptable method of achieving the proper matched-angle
geometry. The angle between the driveshaft and pinion can be opposite
to the angle between the transfer case and driveshaft - as long
as they are equal. Note that they must still be in phase. This unusual
configuration is called "Broken back" or "W"
geometry (see pic at left ), and is common on agricultural equipment,
marine drives, some tractor-trailers that use stub-shafts between
front and rear of a tandem assembly, and most often on power-takeoffs
like hydraulic pumps and PTO shafts. |
Most of the equipment
that uses driven shafts in a broken-back configuration though, are
fairly low RPM (but not all). The reason is, due to the nature (geometry)
of the configuration (again, have a look at the picture above) with
this setup, there's a lot more inherent strain on the slip member
as it rotates. because of the opposite angles, the shaft "wobbles"
the slip member back and forth as it rotates - like a skipping rope
being swung. At high rpm, with anything but the tightest slip-joint
assembly, this would cause a horrible vibration - that's why Spicer
light duty driveshafts do not normally come factory in this arrangement.
Note however, that some Land Rovers do have stock driveshafts in
the broken back configuration, so it can work! I don't have any
experience with these Rover's, but I imagine that the angles in
the stock configuration are pretty darned small. As with the more
standard single-cardan setup - start increasing the operating angles
of the U-joints and the elliptical paths get more and more elliptical,
the angular velocities (amount the shaft speeds up and slows down
each revolution) get greater, and when you spin that shaft at 1000rpm,
the more likely it is that the shaft will be noisy, harsh, and vibrate
- EVEN IF the angles are matched. Again...time for the double cardan
CV shaft!
Double
cardan (near) constant velocity driveshaft (commonly known as a
CV driveshaft) geometry. |
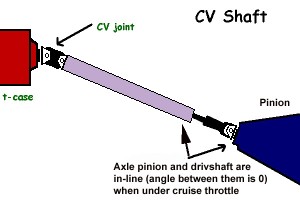 |
Proper CV driveshaft geometry
is actually a lot more simple to understand than single-cardan driveshaft
geometry. Pictured at left, proper CV shaft geometry is achieved when
the operating angle of the CV joint (head assembly) is less than the
maximum (and there is some room for increase in operating angle under
suspension droop), and the operating angle between driveshaft and
pinion is 0 under cruise throttle. |
|
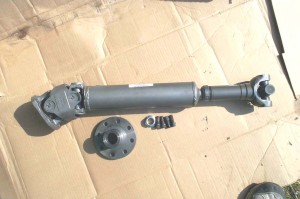 |
This is because of
the clever design of the CV joint, or head assembly. If you refer
back to the picture of the CV shaft components in pat one, you will
see that the CV head assembly (double cardan joint) contains two
cardan style universal joints and a centering yoke assembly. This
clever arrangement serves to neutralize the effects of the increasing
and decreasing angular velocities, right at the head assembly. This
relieves us of having to arrange the pinion yoke operating angle
to be equal to the transfer case operating angle. Instead, the pinion
is arranged so that the operating angle between it and the driveshaft
is zero degrees (0°). |
Measuring
and calculating universal joint and driveshaft operating angles
So, we know what the
geometry is supposed to be - how do we find out what ours actually
is, and what do we do about it? This section discusses measuring
your geometry, calculating the results, interpreting the results,
and making necessary adjustments.
The first 2 steps, measuring
slopes of components, and calculating operating angles are the same,
regardless of whether you have a standard single-cardan shaft or
a double-cardan CV shaft. The third step, interpreting the results,
will differ, depending on the style of driveshaft.
Before attempting to
measure angles ensure that tire air pressure is correct, that the
vehicle is at the correct trim (chassis) height (i.e. suspension
loaded, operating weight in/on the vehicle, etc.) and the ground
surface is perfectly level. The driveshaft also needs to be installed
and torqued to spec.
Step
1 - Find the slopes of the components involved.
Recall that the slope
is the angle formed between the component in question, and the horizontal.
To find these slopes, we measure them with a protractor as follows: |
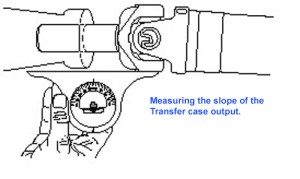 |
Transfer case
Measure the slope of
the transfer case output yoke by placing the protractor or angle
finder (inclinometer) on the bottom of the bearing cup, (see pic
at left). Position the angle finder on the clean flat surface of
the bearing cup, level the bubble (if equipped) and note the reading. |
If your transfer case
has an output flange, the best way to measure the slope is to temporarily
remove the shaft from the flange,place the angle finder against
the flat machined surface of the flange, then add or subtract 90°
from the reading taken. Remember to re-attach the driveshaft so
that you can correctly measure its slope.
Remember that the slope
is "down" if it is higher at the t case than at the axle. |
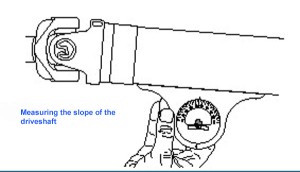 |
Driveshaft
Measure the drive shaft
slope, as shown, by placing the angle finder directly against the
tube. level the bubble (if equipped) and note the reading.
Remember that the slope
is "down" if it is higher at the t case end than at the
axle end. |
|
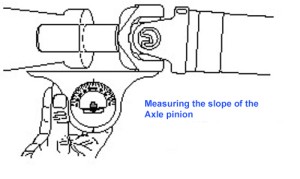 |
Axle Pinion
Measure the slope of
the pinion yoke by placing the protractor or angle finder (inclinometer)
on the bottom of the bearing cup, (see pic at left). Position the
angle finder on the clean flat surface of the bearing cup, level
the bubble (if equipped) and note the reading. Alternatively, the
angle finder can be placed against a flat machined surface that
lies 90° to the pinion shaft centerline, the reading taken,
and then 90° added to or subtracted from the result. |
Remember
that the slope is "down" if it is higher towards the center
of the vehicle, and lower at the end of the vehicle.
Step
2 - Find each operating angle between each pair of slopes as follows: |
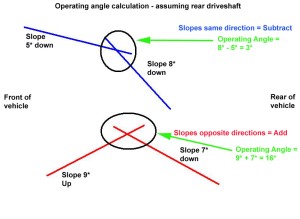 |
If both slopes are
in the same direction (up or down), subtract the lesser number from
the greater to obtain the operating angle.
If both slopes are in
different directions (one up and one down), add the lesser number
to the greater to obtain the operating angle. |
In the special case of
calculating the operating angle at the pinion in a CV shaft application,
assign the pinion slope a (+) sign if it is DOWN and a (-) sign
if it is UP, then always subtract the pinion slope from the driveshaft
slope, regardless of their relative sizes, and make note of the
resulting sign (+ or -), as this will help in deciding any possible
corrective action.
Step
3 - Interpret the results
Assuming a fairly standard
4x4 setup with no pillow blocks or intermediate shafts, once you
have measured all the slopes of the components, and calculated all
the operating angles, you should have a piece of paper that has
3 slopes and 2 operating angles written on it. It helps to have
a sketch too, like those shown below on the left.
Standard (single
cardan) Shaft:
The first operating angle
must be less than the maximum operating angle of the series of U-joint
used, and preferably less than half the maximum (remember - you
need to allow for increase in operating angles while off road due
to suspension movement, and also how the higher the operating angles,
the more likely vibration, even if geometry is correct). If it is
not, you have only 2 choices: lower the suspension or drop the drivetrain
(lower t-case); or switch to a CV style shaft.
The second operating
angle should be within 0.5° (1/2)° of the first AT CRUISE
THROTTLE. This is a critical point. virtually every axle (to a greater
or lesser degree, depending on power and suspension) will experience
some "axle wrap" or pinion rotation ( pinion rotates up
in rear axle, and down in front axle) depending on acceleration
and to some extent braking torque. This will of course alter the
geometry of the pinion, and therefore the whole driveshaft! Since
the driveshaft will presumably spend most of it's time (and therefore
the effects of it's vibrations will be most annoying and damaging)
in a cruise throttle condition, it is standard practice to set driveshaft
geometry for this state (If you have a highly specialized vehicle,
like a drag car, this may not apply - and you will want to discuss
your needs with an expert like Jess at High Angle Driveline). Generally, for most truck rear axles,
at cruise, the pinion will rotate up 1-2° from its static position.
As such, it is common practice to shim the axle or adjust the links,
rotating the pinion and changing the pinion slope at rests, such
that the pinion slope is 2° lower than that required to achieve
equal operating angles at rest. Read that bit again, carefully!
It's a bit of a juggle, because as you adjust the pinion slope itself,
so you also actually alter the driveshafts slope, and therefore
the transfer case operating angle as well. Once you get close though,
you will easily end up at the correct balance point. the point I'm
making is, don't just make a whopping 20° change to the pinion
angle, then weld those spring perches on and call it done. That
big of a change will have effected things, so you'd have to measure
and re-calc all the slopes and operating angles again, as you hone
in on the final setting. |
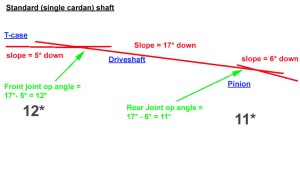 |
Example:
Looking at the sample
worksheet to the left, and assuming it is for a rear driveshaft |
We can see that the front
operating angle is 12°. Assuming we are using a 1350 series
U-joint, and the vehicle is not a frequent, long-range freeway cruiser,
nor does it have a super-flexy suspension with monstrous travel,
we decide that this is satisfactory. The axle joint operating angle
is 11°. Because it is a rear driveshaft, the rear pinion will
rotate up, let's say 2° under cruise throttle. Since our measurements
and calculations were done at static, this means that in reality,
under cruise throttle, the pinion slope would change from 6°
down to 8° down (even though the pinion wraps "up"
- remember we describe slopes as up or down depending on orientation
between t-case and axle). This would make the axle joint operating
angle actually 17° - 8° = 9° at cruise. Since we need
it to equal 12° at cruise, we need to rotate/shim the pinion
at rest down 3°. This will result in a static pinion slope of
3°. the would net a cruise throttle pinion slope of 3° +
2° = 5°. That would make our axle joint operating angle
now 17° - 5° = 12° - A perfect match for the front!
Of course
- we would need to make this adjustment (rotate pinion down 3°
at rest) and then re-measure and re-calc everything to get it perfect,
as the change may effect driveshaft slope and therefore t-case joint
angle too. However, this is unlikely with the magnitude of the changes
in this example.
Double cardan
CV shaft
The first operating angle,
the CV joint op angle, must be less than the maximum operating angle
of CV joint used. Remember - you need to allow for increase in operating
angles while off road due to suspension movement. How much you must
allow will depend entirely on your suspension design and the terrain
driven. If it is not, you have only 2 choices: lower the suspension
or drop the drivetrain (lower t-case); or switch to a higher angle
capable CV joint shaft.
The second operating
angle, the pinion op angle, should be within 0.5° (1/2)°
of zero (0°) AT CRUISE THROTTLE. This is a critical point. virtually
every axle (to a greater or lesser degree, depending on power and
suspension) will experience some "axle wrap" or pinion
rotation ( pinion rotates up in rear axle, and down in front axle)
depending on acceleration and to some extent braking torque. This
will of course alter the geometry of the pinion, and therefore the
whole driveshaft! Since the driveshaft will presumably spend most
of it's time (and therefore the effects of it's vibrations will
be most annoying and damaging) in a cruise throttle condition, it
is standard practice to set driveshaft geometry for this state Generally,
for most cars and trucks rear axles, at cruise, the pinion will
rotate up 1-2° from its static position. As such, it is common
practice to shim the axle or adjust the links, rotating the pinion
and changing the pinion slope at rests, such that the pinion slope
is 2° lower than that required to achieve an operating angles
of zero at rest. Read that bit again, carefully! It's a bit of a
juggle, because as you adjust the pinion slope itself, so you also
actually alter the driveshafts slope, which directly affects what
your pinion angle must be, in a feedback type loop. Once you get
close though, you will easily end up at the correct balance point.
The point I'm making is, don't just make a whopping 20° change
to the pinion angle, then weld those spring perches on and call
it done. That big of a change will have effected things, so you'd
have to measure and re-calc all the slopes and op angles again,
as you hone in on the final setting. |
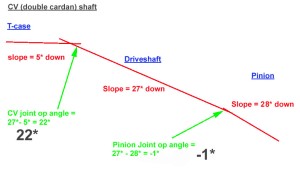 |
Example:
Looking at the sample
worksheet to the left, and assuming it is for a rear driveshaft |
We can see that the front
CV operating angle is 22°. Assuming we are using a High Angle
1350 series CV shaft, we are comfortably within the proper operating
spectrum here. The axle pinion joint operating angle is -1°.
Because it is a rear driveshaft, the rear pinion will rotate up,
let's say 2° under cruise throttle. Since our measurements and
calculations were done at static, this means that in reality, under
cruise throttle, the pinion slope would change from 28° down
to 30° down (even though the pinion wraps "up" - remember
we describe slopes as up or down depending on orientation between
t-case and axle). This would make the axle joint operating angle
actually 27° - 30° = -3° at cruise. Since we need it
to equal 0° at cruise, we need to rotate/shim the pinion at
rest down 3°. This will result in a static pinion slope of 25°.
This would net a cruise throttle pinion slope of 25° + 2°
= 27°. That would make our cruise throttle axle joint operating
angle now 27° - 27° = 0° - A perfect setup for a CV
shaft!
Note that, in the case
of a CV shaft, since we always calculate the angle the same way
driveshaft slope minus pinion slope, the sign of the result tells
allows us to write an equation, the result of which tells us whether
we need to rotate the pinion at rest down or up.
The equation is RR=DS-PS-WA.
Where RR = rotation required (of the pinion at rest), DS - driveshaft
slope, PS = pinion slope, and WA is the estimated pinion wrap angle.
If the result is (-), we must rotate the pinion down at rest that
many degrees, if the result is (+) we must rotate the pinion up
that many degrees.
Of course
- we would need to make this adjustment (rotate pinion down 3°
at rest) and then re-measure and re-calc everything to get to perfect,
as the change may effect driveshaft slope. However, this is unlikely
with the magnitude of the changes in this example.
How
to chose a Driveshaft for your Rig.
This is actually a fairly
easy one to answer.
First - buy the absolute
best you can possibly afford. Why? It is almost impossible to overstate
the massive annoyance of a bad driveshaft. Driveshaft vibration
is horrendously annoying - street queen or trail-only rig. Believe
me, I know. My current buggy, the Wolf, is always trailered, and
spends 90% of it's time below 10mph - occasionally it may get to
40mph. I had NO IDEA how bad my cobbled-together shaft was until
I replaced it with a High Angle driveshaft. Even at slow speeds,
a crappy driveshaft will EASILY suck the fun out of driving your
rig. I figured - it's trail buggy - it's loose and noisy anyway
- who cares. Well, I learned....it is Sooooooooo much nicer with
a decent balanced shaft, operating within it's angle capabilities
- and of course - the peace of mind for the components that actually
put the power to the axles is priceless.
Do you need a a CV shaft,
or will a standard single-cardan style do? Well, in my opinion,
unless your rig is only an inch or 2 over stock suspension height,
with minimal wheel travel / flex, the answer is definitely YES!
The CV driveshaft offers
several HUGE advantages to the off-road vehicle.
First, the pinion and
pinion yoke can be rotated up out of harms way, where it will be
less susceptible to damage from rocks and other obstacles.
Secondly, the only limit
to our operating angle at the CV joint (and thus how much suspension
height we can run) is the limit of the double-cardan joint itself.
A stock Spicer double cardan CV joint can run successfully at about
22°, and a High
Angle Driveline double-cardan CV joint can be run successfully
at as much as 32° !!! This allows for successful driveshaft
installations in vehicles with much more suspension height than
a simple single-cardan shaft can accommodate. Even if you matched
the angles on a single cardan shaft exactly, you could never run
it safely and vibration free at 30°!
Thirdly, the double-cardan
CV joint assembly is simply better and more efficient at reducing
or eliminating driveshaft vibration. Even at smaller angles, and
even with correct matched-angle geometry, the single-cardan shaft
is still susceptible to vibration. The CV shaft will always run
smoother, quieter, and with less stress on the U-joints, and transfer
case and pinion shafts, bearings, and seals.
The only advantage the
single-cardan shaft has is that it is cheaper to manufacture / buy,
and you don't have to buy a centering yoke or a third U-joint when
rebuilding it. As always - the best costs a little more!
Part
3 - Driveshaft maintenance.
Driveshafts should be
carefully inspected and lubricated (as applicable - some components,
and even some entire driveshafts are non-serviceable and cannot
be re-greased) at recommended original equipment vehicle manufacturers’
service intervals and/or at Spicer recommended lubrication intervals
OR you can use my recommendations, which are:
Severe use (wet, muddy,
or high-torque carrying use, extreme low gears (80:1 and lower),
large tires(35" and over)) 3000 miles, 2 months, or 250 Hrs,
whichever comes first
Moderate use (dry conditions,
on and off road use) 5000 miles, 3 months, 500 Hrs, whichever comes
first
Mild use (mostly street
duty - some off-road) 8000 miles, 6 months, whichever comes first
Before undertaking any
of these procedure, be sure to read and heed the section on Safety.
Driveshaft
Safety
CAUTION
Caution – Under
no circumstances should individuals attempt to perform driveline
service and/or maintenance procedures for which they have not been
trained or do not have the proper tools and equipment. See warning
below.
WARNING
WARNING
Failure to release all parking brakes and failure to place transmission
in neutral can result in torque being applied to the driveshaft.
Disconnecting a driveshaft with applied torque can result in property
damage, serious personal injury or death.
WARNING
Failure to take commonsense, precautionary measures when working
on a vehicle or other machinery could result in property damage,
serious personal injury or death. In order to avoid property damage,
serious personal injury or death, you must:
1. ALWAYS wear safety
glasses when performing maintenance or service. Failure to wear
safety glasses can result in personal injury and/or partial or complete
vision loss.
2. NEVER go under a vehicle while the engine is running. Be sure
the vehicle’s engine is off, and keys are removed from ignition.
3. NEVER go under or work on a vehicle that is not on a level or
flat surface.
4. NEVER work on a driveshaft without blocking the vehicle’s
wheels and releasing all parking brakes.
5. NEVER lift a vehicle without the appropriate weight-rated, vehicle-support
equipment.
6. NEVER REMOVE a driveshaft from the vehicle without keeping the
vehicle’s transmission in neutral.
7. CAUTION – Driveshaft assemblies can be very heavy. Be sure
to use proper lifting techniques when handling driveshafts. More
than one person may be needed when handling driveshaft assemblies.
8. ALWAYS use support straps to prevent the driveshaft from falling
out of vehicle during the removal and installation process.
9. NEVER heat components or use sledgehammers or floor jacks to
remove the driveshaft from vehicle.
Note – For driveshaft
applications that have pillow blocks, dampers, parking brakes or
retarders, refer to these component manufacturers’ or the
original equipment vehicle manufacturers’ service manuals
for proper procedures.
Inspection
Note – The following
procedures are to be performed prior to any lubrication of universal
joints or slip members.
The addition of lubricant can mask the looseness in a component
that is beginning to show wear and may be in need of replacement.
Note - The following
pics are taken from Spicer's Heavy Duty Driveshaft manual (trucks
over 30,000lbs) so the driveshafts themselves will appear huge,
compared to what we 4x4 users are used to.
To properly inspect the
driveshaft, you need to block the vehicles wheels, set the parking
brake, put the transmission in Neutral (N), and the transfer case
in 2wd. If you have a selectable locker or lockout manual hubs,
unlock them. This is all important because you want to make sure
that there is no drag or pressure or bind on the driveshaft that
can mask wear and sloppiness during your inspection.
INSPECTING
END FITTINGS
Visually inspect all
input and output end-fitting (yoke) retaining nuts, clips, or bolts
for any gaps between mating surfaces. If gaps are present, consult
transmission, axle or transfer case original equipment manufacturers’
service and maintenance manuals for proper fastener specifications. |
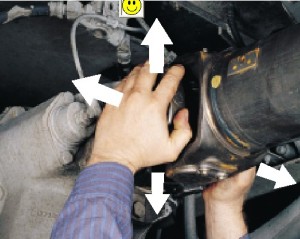 |
Check all
input and output end fittings (yokes at each end of driveshaft) for
looseness or play. Take hold of the end fitting with both hands. Try
to move it vertically and horizontally to feel any looseness. (See
photo left.) Listen for any clicking, or grinding noise from the joint.
There should NOT be any movement in the end fittings. If looseness
is evident, U-joints or yokes will have to be replaced. |
|
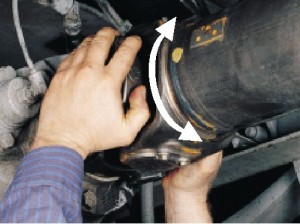 |
If the end fittings are
tight, check for excessive radial looseness of the transfer case output
shaft and axle input shaft (pinion) splines relative to the end fitting.
Take hold of the end fitting with both hands, rotate left to right,
feeling for play or backlash (see photo left.) Listen for any clicking,
or grinding noise from the joint. If radial looseness is evident,
U-joints or yokes will have to be replaced. |
Visually inspect for
damaged bearing retainers or stamped straps, loose bearing retainer
bolts or strap bolts, loose companion flange bolts and nuts, loose
or missing spring tabs or spring tab bolts, damaged tangs on end
fittings, damaged or missing snap rings, and rotating bearing cups.
If any of these situations are evident, replacement of the components
is necessary. |
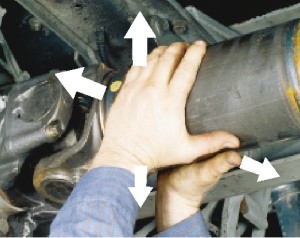 |
Check for excessive
looseness across the ends of the universal joint bearing cup assemblies
and trunnions. Take hold of the inboard yoke on the driveshaft with
both hands. Try to move yoke vertically and horizontally. (See photo
left above.) There should be less than .006 in. (.15mm) movement
in the universal joint kit relative to the inboard or outboard yokes.
If looseness is greater than .006 in. (.15mm), the universal joint
kit must be replaced. |
INSPECTING
UNIVERSAL JOINTS
Visually inspect all
universal joint kits in the driveshaft assembly. Make a careful
inspection of the caps of the U-joints where they are held captive
in the end fittings (yokes). Look to see if the caps are polished
or shiny. If they are, it indicates that the cap is spinning in
the bore, and the U-joint and attachment hardware will have to be
replaced.
There are 3 types of
U-joints used in driveshafts:
- Relubable style
- Permanently Lubricated
Plug Style
- Permanently Lubricated
Net-Formed Style
Each requires slightly
different inspection procedures |
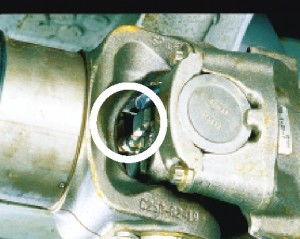 |
Relubable style
Check for the presence
of all grease zerk (nipple) fittings. (See photo left). Grease zerk
(nipple) fittings should not be missing, loose or fractured. If
grease zerk fitting is loose, tighten to required specifications.
If grease zerk fitting is fractured, replace grease zerk fitting
and tighten to required specifications. If grease zerk fitting is
missing, the entire universal joint kit needs to be replaced. |
|
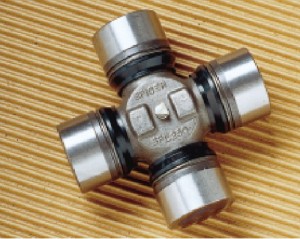 |
Permanently Lubricated
Plug Style
Permanently lubricated
plug style universal joint kits do not contain grease zerk fittings,
only a plug. (See photo left) Make sure plug is not missing, loose
or fractured. If the plug is loose, tighten to required specifications.
If a plug is missing or fractured, the entire universal joint kit
needs to be replaced. |
|
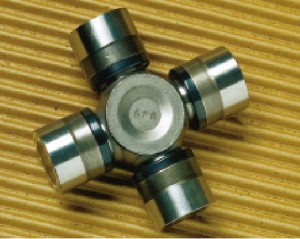 |
Permanently Lubricated
Net-Formed Style
Net-formed universal joints do not contain grease zerk (nipple)
fittings or plugs and are not relubable (See photo left) |
INSPECTING
SLIP MEMBERS |
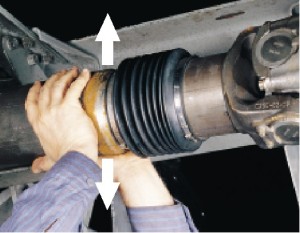 |
Check the slip member
assembly for excessive radial looseness. Using a dial indicator
(or a very carefully calibrated eyeball :-), take hold of the tubing
near the slip member with both hands and try to move vertically,
up and down relative to the ground. There should be limited looseness
in the slip member assembly. (See photo left) If looseness is greater
than .012 in. (.30mm) as read on dial indicator, replacement of
the slip member assembly is necessary. |
|
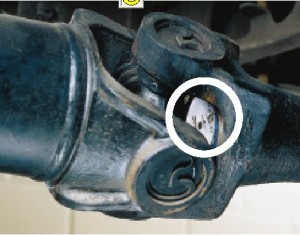 |
For an inboard and outboard
slip yoke assembly design, check to be sure the slip yoke welch plug
is not loose, missing or damaged. (See photo left) If any of these
situations are evident, replacement of the slip yoke and professional
re balancing of the driveshaft is necessary. |
|
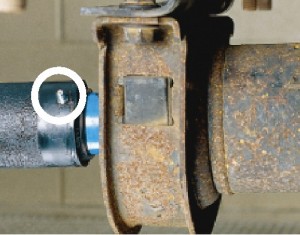 |
Visually inspect for
the presence of the grease zerk fitting, if applicable, on the slip
yoke. (See photo left) Grease zerk fittings should not be missing,
loose or fractured. If grease zerk fitting is loose, tighten to
required specifications. If grease zerk fitting is missing or fractured,
the slip members may need to be replaced. Be sure to follow above
procedure for inspection of radial looseness in slip member assembly.
If slip member assembly is within acceptable limits as stated above
install new grease zerk fitting and tighten to required specifications.
Be sure to completely re lubricate slip member assembly with recommended
lubricant. |
|
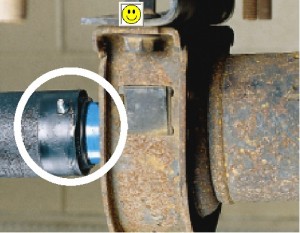 |
Check the slip yoke seal.
(See photo left) Make sure the seal is properly attached to the slip
yoke and is not loose or damaged. If any of these situations are evident,
replacement of slip member assembly is necessary. |
|
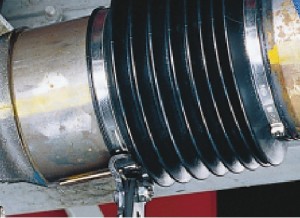 |
For permanently lubricated
slip members, check yoke shaft boot (see photo left) or seal can.
Make sure the boot or seal can is properly attached to the yoke shaft
and tube sleeve and no damage or looseness is apparent. Visually inspect
boot for tears. Inspect boot or seal can for punctures. Inspect boot
clamps for damage. If any of these situations are evident, replacement
of slip member assembly is necessary. |
INSPECTING
TUBING
Check the driveshaft
for bent or dented tubing, cracks, or failed welds. If any of these
situations is evident, replacement of the complete driveshaft assembly
or tube is necessary.
INSPECTING
CENTER BEARINGS |
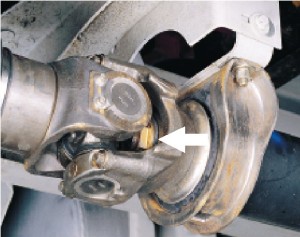 |
Visually inspect all
center bearings, end-fitting midship nuts for any gaps between the
mating surfaces. (See photo left) Be sure to repeat check for broken
back and backlash.for all center bearing end fittings. |
|
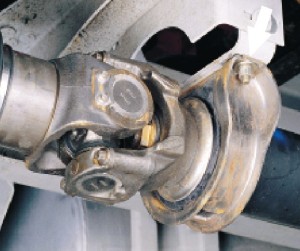 |
Inspect the center bearing
bracket bolts for looseness. (See photo left) If looseness is evident,
re tighten center bearing bracket bolts. Consult the vehicle manufacturers’
specifications for proper bolt torque. Check the alignment of the
bracket before tightening the bolts. Bracket should not be skewed.
Visually inspect the center bearing rubber cushion for
damage. Make sure the slingers are not rubbing against the rubber
cushion. Verify that the rubber cushion is properly seated in the
metal bracket. If any of these situations are evident, replacement
of the center bearing assembly is necessary. |
Lubrication
Why?
Lack of proper lubrication
is one of the most common causes of universal joint and slip member
problems. In all of my experience, (and Jess will back me up on this too) the U-joints most likely to fail are
the re greasable kind that haven't been properly lubricated frequently
enough.
Proper re lubrication
flushes the universal joints, thus removing abrasive contaminants
from the bearings. Relubable slip members must also be adequately
re lubricated to prevent slip member failure.
When?
First, on installation,
regardless of if the joint is re lubable or not. Replacement universal
joint kits contain only enough grease to provide needle roller bearing
protection during storage. It is therefore necessary to completely
lubricate each replacement kit prior to assembly into the yokes.
After initial installation,
you can follow either your vehicle manufacturer's recommended intervals,
Jess's recommendations, or follow my recommendations, which are:
Severe use (wet, muddy,
or high-torque carrying use, extreme low gears (80:1 and lower),
large tires(35" and over)) After every off-road trip, 3000
miles, 2 months, or 250 Hrs, whichever comes first
Moderate use (dry conditions,
on and off road use) 5000 miles, 3 months, 500 Hrs, whichever comes
first
Mild use (mostly street
duty - some off-road) 8000 miles, 6 months, whichever comes first
How?
For
the Universal Joints:
|
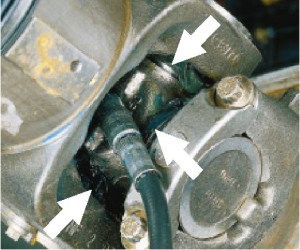 |
Using the recommended
lubricant (see below) use a hand operated grease gun (air powered
guns use to much pressure and can blow out seals and force contaminant
in) and pump grease into the grease nipple until it flows out from
all 4 bearing cap seals. You cannot over-grease a U-joint. |
Note: If your shaft uses
permanently sealed (non re lubable U-joints - don't attempt to disassemble
them to re-lube them, and DO NOT attempt to use any of those sharp
needle attachments designed for piercing seals to inject grease.
You will only make things worse, and hasten their demise, as you
will ruin the seals. Just leave them in there, and replace the whole
thing when it wears out. If you find yourself dissatisfied with
their life-span, consider trying the re lubable kind in future.
For
the Slip Member:
|
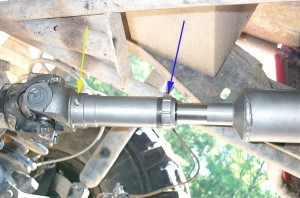 |
Remove one end of the
driveshafts connection so that you can fully compress the slip member
(splines all the way in). If your driveshaft has the grease nipple
in the dust cap (blue arrow) - pump grease till it flows out relief
hole. |
|
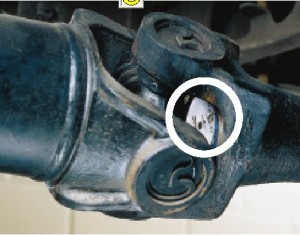 |
If your driveshaft
slip member has the grease nipple at the yoke end (like mine - yellow
arrow in pic above) - cover relief hole (pic at left) and pump grease
till it flows from under the dust cap (blue arrow in pic above). |
For
the CV assembly (if applicable).
|
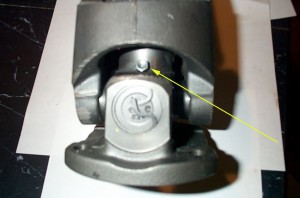 |
Disconnect the CV head
assembly from the vehicle so that you can access the recessed grease
fitting in the CV assembly (yellow arrow). Using a needle attachment
on your grease gun, pump grease into the fitting until it flows
out freely. |
THIS is critical. This
is probably the single most neglected grease fitting on a 4x4. Long,
smooth driveshaft operation demands proper and frequent lubrication.
You wouldn't be too lazy to change the oil in your engine for 50
000 miles, so don't abuse your driveshaft that way either.
Important Note: High
Angle Driveline is the ONLY company to offer a true HIGH ANGLE
1350 CV assembly that is re lubable for smooth operation and long-life.
the others say it couldn't be done.......but they were WRONG! Jess has worked his magic - and it works, and it still brutally strong
- anyone claiming otherwise is fooling themselves. This is reason
enough to go to Jess for
your driveshafts. Having that CV head assembly wear out prematurely
because of improper service and ingress of contaminants (and if
you use your 4x4 like I do, you WILL get water and mud and grit
and dust in EVERYTHING!) would be a huge pain, and expensive to
repair/replace!
With
What?
Spicer recommends that
the following requirements be met for any lubricant that will be
used to service most vehicular, industrial and all auxiliary driveshaft
applications.
• Use a good quality E. P. (extreme pressure) grease
• Timkin Test Load - 50 Lbs./23 Kg. minimum
• Meeting N.L.G.I.,* E. P., Grade 2 specifications
• Grease must have an operating range of
+325°F to -10°F (+163°C to -23°C)
*National Lubricating
Grease Institute
GREASE COMPATIBILITY*
When greases made from different thickeners are mixed, the mixture
may result in lower service performance or physical properties than
either of the original component products.
This reduction in lubricant performance is called incompatibility.
It may show up in any of several areas, such as:
1. Lower heat resistance;
2. Change in consistency, usually softening; or
3. Decrease in shear stability.
Mixtures which show none of these changes are considered compatible.
Incompatibility is not always caused by the thickener, since each
of the greases in the mixture is a complete package – thickener,
fluid, and additives. Sometimes the thickener of one grease is incompatible
with the fluid or the additives present in the second grease. If
the mixture proves to be significantly softer, less shear stable,
or less heat resistant than the original grease, the mixture shall
be deemed incompatible. Incompatibility is best determined in service
or in service related tests; it is not predictable. Certain thickener
combinations often have been found unsatisfactory and are generally
so recognized. These would include lithium and sodium greases and
organo-clay and most soap greases. Contact your local lubricant
supplier for grease compatibility information. To help reduce the
effects of incompatible greases, make sure to thoroughly purge all
four bearing seals on each universal joint with the new grease.
Purge seals until the fresh grease is visible on the outside of
all four bearing seals. It is recommended that all purged grease
be wiped clean to prevent discharge into the general environment.
Did I
do it right?
Ever wonder if you HAVE
to get grease purging from all 4 bearing caps in a U-joint when
lubricating it? Ever wonder why? The answer is "yes, you do,
because otherwise you cannot be sure all bearings are fully lubricated
and all foreign material and water is evacuated due to unequal seal
pressures due to tolerance stack up in components." What the
heck does that mean? It means, grease the joint until all 4 sealed
purge! And if all 4 will not purge - relieve the pressure on the
bearing caps that will not, and try again. The procedure is outlined
below. If the joint still will not purge from all 4 seals - it must
be replaced. See the Spicer Video on Proper
U-joint Lubrication for the complete story.
Procedure
for releasing universal joint bearing seal tension
Bearing strap
/ U-bolt style. |
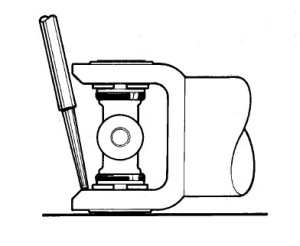 |
Utilizing a brass hammer
or punch and wearing safety glasses, sharply strike inboard yoke
on lug ear once to try to firmly seat bearing cap and relieve tension
across span. Rotate shaft 180 degrees and repeat procedure on opposite
lug ear. Apply grease gun pressure and purge all four bearings until
fresh grease is seen at all four bearing seals. |
If striking lug ears
does not cause purging, remove the retaining hardware from the affected
bearing caps (follow removal procedure outlined below if required,
making sure to mark driveshaft for phasing before removing any hardware)
and unseat bearing cup assemblies from yokes (by tapping on yoke
or bearing cup with a soft-faced hammer if required). Once the bearing
cup assemblies are free, allow the driveshaft to rest on a. support
strap. Remove snap rings in lug ears of the inboard bearing caps
that are not purging Note – Spicer snap rings can be reused
if they ARE NOT severely corroded or distorted. If corroded or distorted,
replace used snap rings with new |
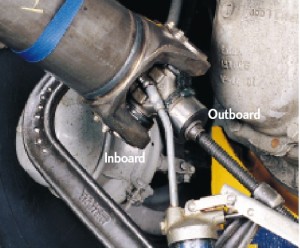 |
Purging
Inboard (captive in driveshaft yoke) Bearings
Apply a c-clamp around
the outboard (those that seat in the pinion or T-case yoke) bearings.
Apply grease gun pressure. Completely purge both inboard (those
captive in the driveshaft yoke) bearings. See pic (purge inboard)
Purging
Outboard (that connect to yokes) Bearings
If outboard bearings
fail to purge, slightly loosen c-clamp and reapply grease gun pressure
until both outboard bearings purge. |
After all four bearings
purge fresh grease, re-tighten c-clamp to squeeze out excess grease
and wipe clean. This will ease installation of universal joint kit
back into yoke. Install universal joint in the yoke using new hardware
and torque bolts or nuts to the required specifications.
If the bearings still
will not purge, complete removal and replacement of the universal
joint is required.
Driveshaft
Removal |
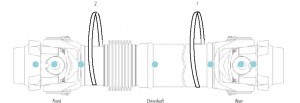 |
Mark Driveshaft (“Phasing
Marks”)
It is imperative to mark all the mating components of a driveshaft.
Mark the driveshaft with a marking stick, paint marker or other legible
marking device. In addition, be sure to mark all bearing positions,
spline positions, shaft locations and all bearing retainers. This
assures proper reassembly of the driveshaft into the vehicle, in its
original position. |
|
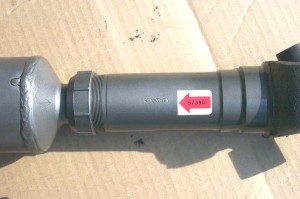 |
This pic shows the phasing
marks on my new shaft. |
Support the driveshaft
with a support strap, if required, at the appropriate location,
Attach support straps to frame rails or some structural part of
the vehicle.
Remove the bearing retainer
bolts and bearing retainers or stamped straps or remove nuts and
U-bolts. Stamped straps and stamped strap bolts or bearing retainer
bolts CANNOT be reused. Loosening or removing bearing retainer bolts
or U-bolts requires replacement of used bolts with new. Do not substitute
other hardware – Spicer driveshaft hardware is made from correct
alloys and is specially heat treated. |
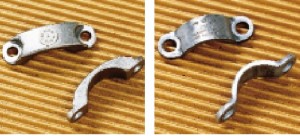 |
Note – New cold
formed bearing retainers DO NOT need to be replaced. Replace only
if damaged. Pic at left shows cold-formed bearing retainers (that
can be re-used) on the left, and stamped straps (that cannot be
re-used) on the right. |
|
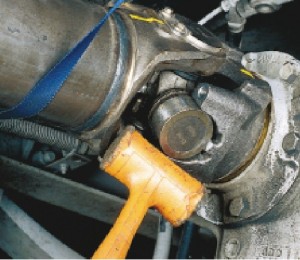 |
It may be necessary
to unseat bearing cup assemblies by tapping on yoke or bearing cup
with a soft-faced hammer. (See pic at left.) Once the bearing cup
assemblies are free, collapse the driveshaft until both bearing
assemblies clear the open end yoke cross holes. Allow the driveshaft
to rest on support strap.
Once the driveshaft is
free, remove the driveshaft from the support straps and take it
to a work bench area.
Check all end yokes for
looseness. Take hold of end yoke with both hands. Try to move it
vertically and horizontally to feel any looseness. There should
NOT be any looseness in the end yokes relative to the input or output
shafts to which they are connected. If looseness is evident, the
end yoke needs to be replaced. |
|
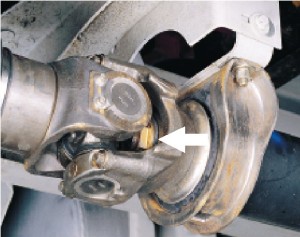 |
Visually inspect all
end yoke retaining nuts or bolts for any gaps between mating surfaces.
Pic at left shows gap under yoke mounting nut.
Inspect all end yoke
cross hole surfaces and bolt hole threads for damage. If the bolt
hole threads are damaged, the yoke must be replaced. |
Replacing
universal joints in the driveshaft.
Remove driveshaft from
vehicle as described above, and set on work bench
Remove
joints from shaft |
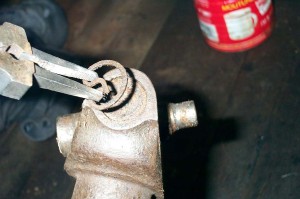 |
Remove all internal and
external snap rings. |
|
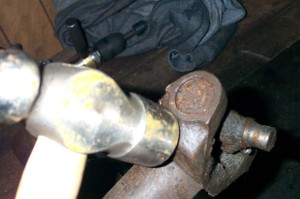 |
Support driveshaft, and
with a hammer, strike the shoulder of the yoke. Inertia will cause
the bearing cap to walk out of the bore. Grasp the bearing cap with
a pair of channel-lok or vice grip pliers, and twist it free from
the trunnion Rotate the driveshaft yoke 180° and repeat. Alternatively,
you can use a press or hammer and socket to drive the bearing cups
from the yoke bores. Whichever method you choose, be sure not to damage
the yoke in the process. |
|
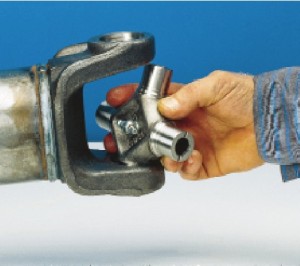 |
Remove U-joint cross
from yoke.
Thoroughly clean and
inspect the bores of the yoke, follow inspection procedures above
if required. |
Install
new joints in shaft
Note – Spicer Life
replacement universal joint kit bearing assemblies contain only
enough grease to provide needle roller bearing protection during
storage. It is therefore necessary to completely lubricate each
bearing assembly. It is also necessary to fully lubricate the universal
joint kit after it is installed in the vehicle. |
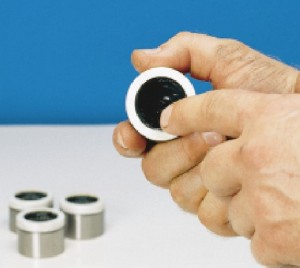 |
Using a high-quality,
N.L.G.I., E. P. Grade 2 lubricating grease, wipe each bearing cup
assembly with grease. Fill all cavities between the needle rollers.
Also apply a liberal coating of grease on the bottom of each bearing
cup assembly and on the lip of the seal.
DO NOT overfill the bearing cups though, as this will create excessive
hydraulic pressure in the bearing caps when the joint is installed,
making proper installation extremely difficult.
Caution – Spicer
DOES NOT recommend wiping the outside of bearing cup assemblies
or yoke cross holes with grease, oil or silicone-based sprays. This
could result in bearing cup assembly rotation in yokes. |
|
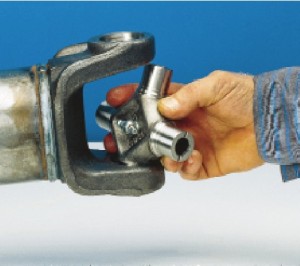 |
Position the journal
cross into the yoke cross holes with the grease zerk (nipple) fitting
inward toward tubing.
Ensure that the grease
zerks at the transfer case and pinion ends of the shaft are both
on the same side of the shaft so that they can both be lubricated
at the same time without having to rotate the shaft. |
|
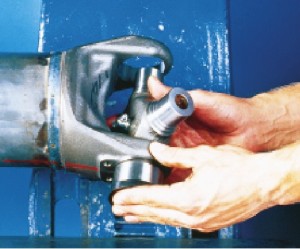 |
Move one end of the journal
cross to cause a trunnion to project through the cross hole beyond
the outer machined face of the yoke ear. Place the bearing cup assembly
over the protruding trunnion diameter and align it to the yoke cross
hole. |
|
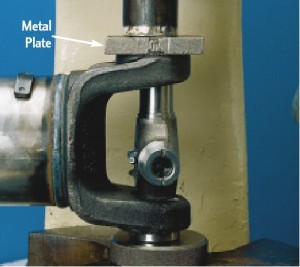 |
Align the yoke in an
arbor press with the bearing assembly resting on the base of the
press.
Cover the yoke ear with
a metal plate that has 0.25 inch minimum thickness. Push the yoke
onto the bearing cup assembly. |
|
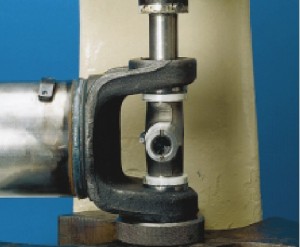 |
Turn the yoke over
180° and place a push rod that is smaller than the diameter
of the bearing cup assembly onto the bearing cup assembly and continue
pressing the bearing cup into the yoke cross hole until far enough
to install a snap ring.
Flip yoke over 180°,
place second bearing cup over the trunnion and align it to the yoke
cross hole. Align the yoke in an arbor press with the previously
installed bearing assembly resting on a support on the base of the
press.
Place a push rod that
is smaller than the diameter of the bearing cup assembly onto the
bearing cup assembly and continue pressing the bearing cup into
the yoke cross hole until far enough to install a snap ring. |
|
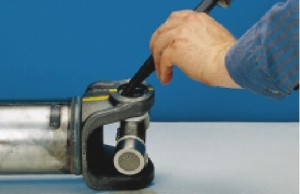 |
Remove yoke from arbor
press. Install a snap ring using snap ring pliers.
Seat installed snap rings
into grooves using a small chisel or punch. (See photo at left). |
|
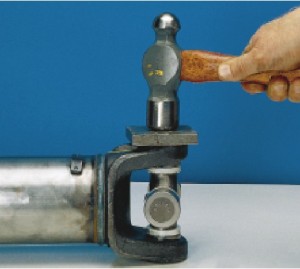 |
Flex the journal cross
to make sure it moves smoothly and freely in the bearings.
If the joint is stiff, place a plate on the yoke ear and hit the plate
with a hammer to seat the bearing cup assemblies. (See photo at left.) |
|
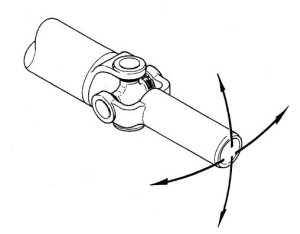 |
Flex the journal cross
to make sure it moves smoothly and freely in the bearings. If not,
disassemble and inspect the journal and bearing assemblies for skewed
or dropped needle rollers. |
Driveshaft
Installation:
Place the driveshaft
in place in the vehicle, use supporting straps if required. |
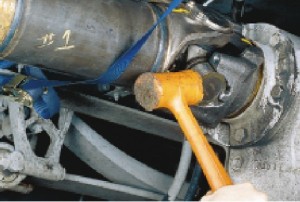 |
Working from the transfer
case end, use a soft-faced hammer to tap the universal joint into
the transfer case output end yoke. Make sure to align the universal
joint in end yoke, matching up the phasing marks made during removal
to ensure original driveshaft orientation. |
Install the bearing retainers
or new stamped straps and new bolts Torque the bolts down evenly
and to required specifications.
1310 and 1330 series joint
retention hardware should be tightened to 17 ft/lbs and 1350 joint
hardware to 20 ft.lbs. DO NOT over tighten the retention hardware
as it will distort the bearing cap and cause the bearings and joint
to fail.
Check to make sure the
bearing cup assemblies are fully seated in the yoke ears. Repeat
for the axle pinion yoke.
It may be necessary to
extend or collapse the slip member assembly to allow clearance to
install driveshaft into the axle pinion yoke.
Completely re lubricate
all the universal joints and the slip member assembly (if slip member
assembly is re lubable) as described in the lubrication section
Part
4 - U-joint tech
Choosing U-joints
When it comes to universal
joints of a given size or series, there are 2 decisions to make
- which brand to choose, and which style (permanently sealed or
re lubable)
The first decision is
simple in my opinion. Spicer Life Series no question. I believe
they are simply the best. Why? I'll let them explain it (below):
Why should
you use Spicer U-joints?
According
to Spicer:
Spicer has been the leader
in cardan universal joint technology since 1904, when Clarence Spicer
patented the first practical application of a universal joint to
replace the chain drives of his day. Since that time, we have refined
our universal joints with improved forging technology, metallurgical
studies, hardening processes and sealing capabilities to ensure
greater durability and low maintenance.
Spicer engineers research
and implement advanced hot and cold metal forming processes for
journal crosses, heat treating methods for case hardening bearing
cups, finite element analysis and three-dimensional modeling to
understand and control stress points, and perform myriad laboratory
and application tests to validate joint performance. We sweat the
details so all of our cardan joints provide you with longer, trouble-free
service.
There are 2 different
models to choose from - the Spicer Time-Tempered™ and the
Spicer Life™. Both are described below. As you will see, the
only choice for us is the Spicer Life™ series.
Spicer
Time-Tempered™ Replacement Cardan Universal Joints*
This OE-acceptable replacement
U-joint kit has a hot-forged steel journal cross that is heat treated
and through drilled for grease channels. It is equipped with a grease
fitting for ease of re lubrication. Journal cross trunnions are
hardened for long life, and the faces are grooved to ensure consistent
lubrication of the needle roller bearings. |
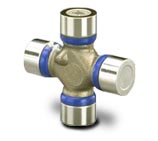 |
The Spicer
Time-Tempered replacement cardan U-joint's distinctive blue rubber
seals provide grease retention within the bearing assembly while
protecting it from contaminants and are designed to purge grease
upon re lubrication.
Bearing cups are carbonitrided
and uniformly case hardened for higher strength, then machined to
a higher tolerance for improved fit and driveshaft balance. This
machining process and its resulting higher tolerances add a level
of quality, putting this U-joint a step above average over-the-counter
replacement kits.
*Spicer Time-Tempered
universal joint kits should NOT be used in high-performance vehicles,
motor sport applications or vehicles frequently used in severe off-road
conditions. |
Spicer
Life™ Original Equipment (OE) Cardan Universal Joints |
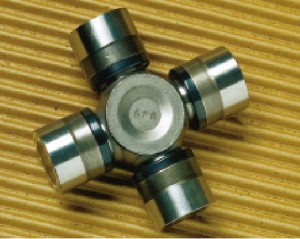 |
The newest cardan universal
joint in the Spicer product line offers advanced design features
for longer life and superior performance. Bearing cups are case
hardened through a carburizing heat treat process, and the inside
diameter and thrust washer surface are machined to the highest tolerances
of all Spicer bearing assemblies. The journal cross is cold-formed
for added strength, and trunnions are machined to give the best
possible surface for the needle roller bearings. |
Spicer Life OE cardan
universal joints stand above the rest for the tough, worry-free
performance demanded by today's discriminating consumer and are
the preferred choice of many automotive design engineers for passenger
cars, pickup trucks and sport utility vehicles. They also have proven
performance and are used extensively by professional motor sport
teams in IROC, NASCAR and NHRA. |
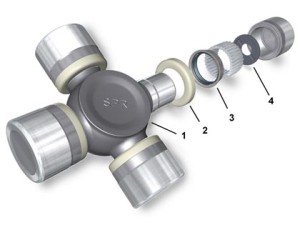 |
Spicer Life Series award
winning universal joint kits are specifically designed to give extended
driveshaft life. Flat ended needle bearings are used to withstand
oscillating loads while the driveshaft is rotating and to eliminate
skewing in the bearing cup. Thrust washers significantly reduce end
galling on trunnion ends and lower universal joint operating temperature.
Synthetic rubber seals and plastic seal guards provide lubricant retention
and help prevent the entry of foreign material, significantly increasing
universal joint life. The centrally located grease zerk (nipple) fitting
increases the strength of the journal cross and allows more torque
carrying capacity. |
Features include:
Cold-Formed Journal
Cross
Cold-formed for increased strength, the journal cross is not through
drilled with grease channels, but rather partially drilled to increase
strength and retain the appropriate amount of premium, lithium-based
grease for maintenance-free operation.
Thermo-Plastic Seal Guard
Helps prevent contamination in the bearing assembly and secures
the bearing onto the trunnion of the journal cross. |
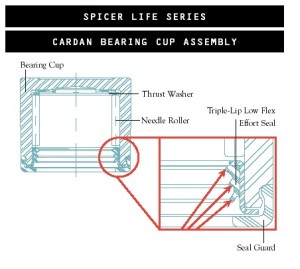 |
Triple-Lip
Seal
Enhances grease retention and prevents contamination in the bearing
assembly by utilizing three lips instead of two.
Composite Thrust Washer
Spicer Life series u joints feature a thermoplastic thrust washer
in the bearing cup. This Eliminates metal-to-metal contact between
the trunnion end and bearing cup. Prevents wear and end galling,
and lowers the overall operating temperature of the universal joint. |
To lube
or not to lube
So the only remaining
question is - do I use permanently sealed U-joints or re lubable
U-joints (assuming there is a choice in the size/series you are
using)
This
is not so simple to answer, and has long been the topic of many
fierce debates. It may well come down to personal preference, but
there are some points to consider.
Most
importantly - relubable U-joints MUST BE re lubed. It sounds obvious,
but the one thing you do not want to do, is to kid yourself that
you will do regular routine maintenance on your driveshaft and U-joints,
and the not. And yet, this is exactly what a HUGE number of people
do. Avoid it. Be honest with yourself. If you aren;t going to re
lube them - use the "permanently" sealed kind, if not,
you will experience premature failure.
So, we
have to be brutally honest with ourselves, fine. But what if we
are the kind that actually would re lube the joints EACH and EVERY
time they require it, properly, completely (see Part 3), and without
fail (am I making a point here? There aren;t many people who fit
into this category). Is there then any reason to prefer on kind
over the other? You have to decide for yourself, but some advantages
and disadvantages to consider are:
Re-lubable
- (-)
They have to be religiously re-lubed, a PITA
- (-)
They generally are not as strong, due to the grease channels in
the cross
- (-)
If you lose or break a grease zerk (not uncommon) the joint is
useless (you could just replace it, but it it's been out for a
while, way more contaminant will have ingressed into the joint
than can even be flushed out by proper lubrication
- (-)
Slightly more of a pin to install, as you have to get the grease
zerks in the right place and all lined up
- (+)
They are generally cheaper
- (+)
Depending on environment, they may last longer (if conditions
are wet and muddy, the ability to purge the joint and relubricate
it, may well extend the life of the joint beyond that of a joint
that cannot be relubricated. However, in dry condition, this will
likely be much less of a factor.
Sealed
- (-)
Depending on environment, may have a reduced service life than
a relubable, since nothing is ever really 100% sealed, so that
if contaminants do get in, there is no way to flush them out
- (-)
More expensive
- (-)
A bit more of a PITA to install, as you have to make sure you
have sufficient lubricant in the caps before you install the joint,
since you cannot add any afterwards.
- (+)
Stronger, due to absence of through-cross grease channels
- (+)
Less to worry about - don't require any maintenance.
Personally, I choose
to run Spicer Life Series permanently sealed (NON-relubable) U-joints
in my 1350 CV driveshaft, for the following reason: With my type
of rig and the wheeling it does, the fact that it's a trailer queen,
sees very little high speed use, sees very little total mileage
in a year, and yet must be as strong and reliable as possible -
I need to squeak every little bit of strength I can from every component,
and things are much more likely to break catastrophically way before
their time, rather than wear to due to a lack of lube.
Spicer
Life Series Universal Joint Cross-Over Index:
Series |
Kit
Part # |
1310 |
SPL22-1X |
1310/Ford 1-1/8" |
SPL22-3X |
1310/7260 |
SPL22-4X |
1330 |
SPL25-1X |
1330/Ford 1-1/8" |
SPL25-3X |
1330/S44 |
SPL25-4X |
S44/S44 |
SPL25-6X |
1330/7290 |
SPL25-7X |
7290/7290 |
SPL25-9X |
1350 |
SPL30-1X |
1410 |
SPL36-1X |
Causes,
Analysis, and remedies for Driveshaft failure
Causes and remedies of
driveshaft vibration include:
- Improper universal
joint operating angles / improper driveshaft geometry
- Measure and set
proper geometry (see Part 2)
- Too extreme universal
joint operating angles
- Switch to higher
angle capable U-joint series or CV joint
- Reduce operating
angles (usual. by reducing suspension height)
- Poor balance of driveshaft
assembly
- Have driveshaft
professionally balanced
- Driveshaft balance
weights damaged or missing
- Have driveshaft
professionally balanced
- Worn-out / improperly
lubricated U-joints
- Inspect, lubricate,
replace U-joints as required
- Worn tail-cone / slip
yoke or slip member
- Inspect and replace
worn components as required
- Bent, dented, fractured
tubing
- Inspect and repair/replace
as required
Driveshaft
Failure analysis Guide
Yokes |
|
|
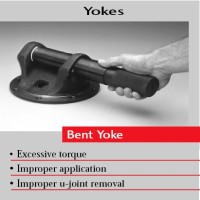 |
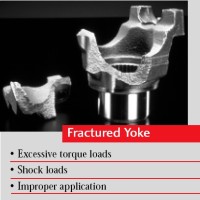 |
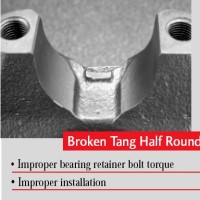 |
Universal Joints |
|
|
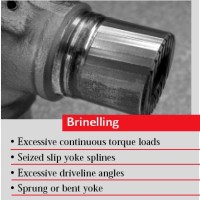 |
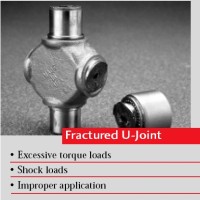 |
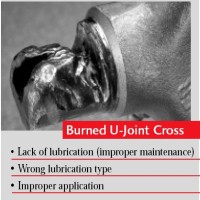 |
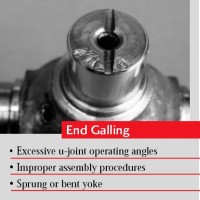 |
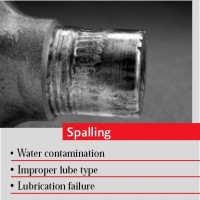 |
|
Tubing |
|
|
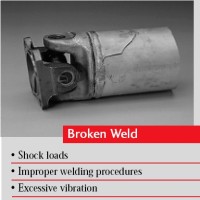 |
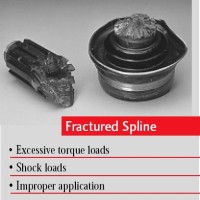 |
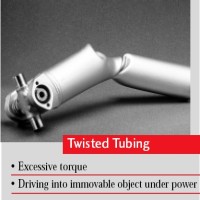 |
|
|
|