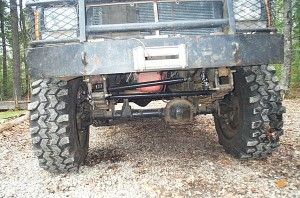 |
This is a
combination crossover and Hy Steer setup. |
|
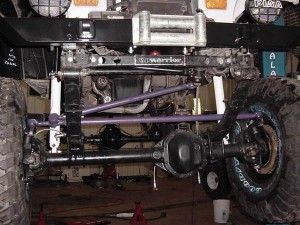 |
This is a
Hy Steer Inverted T
Photo: Ron Hollatz |
|
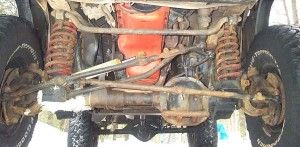 |
This is
an Inverted Y (and a horrible one at that!) |
|
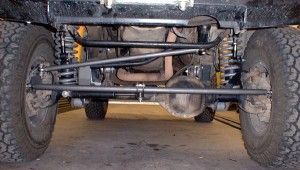 |
This is a
crossover, but not Hy Steer setup. |
The first thing you need for a Hy Steer setup is a set of flat-top knuckles.
Where
do you find the Dana44 flat top knuckles?
73-77 Chevy / GM 1/2 ton 4X4 with Dana44 passenger knuckles are flat tops.
73-87 Chevy / GM 1/2 ton 4X4 with Dana44driver's knuckle are flat tops.
74-77 Full Size Jeep (FSJ) (including Waggoneer, J series trucks, and narrowtrack Cherokee SJ) Driver and Passenger side.
69-77 early Ford Bronco Dana44 knuckles are different from the Gm and Jeep, but are machinable flat.
Mid 70's Dodge's with Dana44 front axle (don't know details)
The advantage to the GM driver's side knuckle is that it's already drilled and tapped.
Some of these knuckles are flat and some have a peak in the center that is machinable.
NOTE - as with all things truck, Jeep, and 4X4 - the years have to be taken with a grain of salt.
I have heard of 77's that are flat top, and 76's that are not - the pictures provided below will help you check.
OK
- so which Dana44 front axles DON'T have flat top knuckles?
78 and later FSJ
78 and later GM passenger side
78 and later Ford F150 / Bronco
Scout II Dana 44.
How
do I tell the difference by looking? |
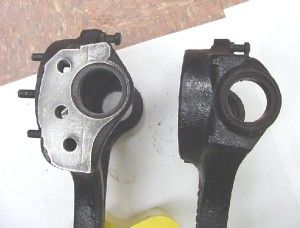 |
Flat top
knuckle on the left.
Non flat top knuckle on the right |
|
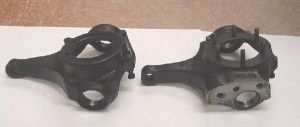 |
Non flat
top knuckle on the left
Flat top knuckle on the right. |
|
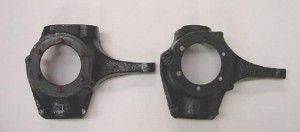 |
Flat top
knuckle on the left.
Non flat top knuckle on the right |
|
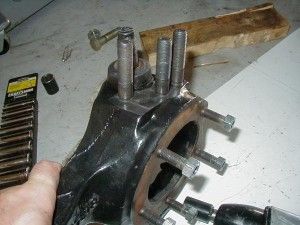 |
This is
an early Bronco D44 flat top knuckle |
|
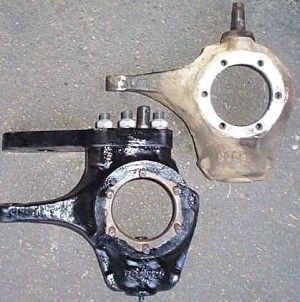 |
Non flat
top knuckle, upper right.
Flat top knuckle with steering arm attached, lower left. |
What
parts do I need to run a flat top knuckle Dana44 with a 5x5.5" bolt
pattern?
Essentially
you run the Chevy or FSJ knuckle out, but you use a '76-'92 Ford F-150
Hub, rotor, and Inner Wheel bearing seal. (Except the '87-early '88 model
Fords with the weird flange mount hub). The manual lockout is the
same part for both.
Timken Bearing Numbers
76 Chevy / 85 F-150 inner wheel bearing:
Set 37
76 Chevy / 85 F-150 outer wheel bearing:
Set 45
76 Chevy / 85 F-150 Front Axle Spindle Outer oil seal
722109
76 Chevy / 85 F-150 Front Axle Spindle Inner oil seal
722108
76 Chevy / 85 F-150 Spindle bearing
B2110
Inner wheel bearing seal (fits in back of hub)
Chevy 24898
Ford 24917
Warn premium locking hub applications that work
Part # 20990
Locking hub applications that work:
Chevrolet/GMC
Blazer, Jimmy, Suburban '69-91
1/2 Ton Pickup '69-87
3/4 Ton Pickup '77-87
DODGE
1/2 Ton Pickup & Ramcharger '69-74
1/2, 3/4 Ton Pickup & Ramcharger '80-93
FORD
Bronco '66-96
1/2 Ton Pickup '59-96
3/4 Ton Pickup '59-75
3/4 Ton Pickup, Light Duty '77.5-97
JEEP
Full Size Wagoneer, Cherokee, J-10 Pickup, Commander '74-91
J-20 Pickup '77-87
F150 hub and rotor part #s
BRAKE
DISCS/ROTORS |
GUARDIAN |
52-60441 |
[Rotor] Frt.; 4WD |
WAGNER |
BD60441 |
[Rotor] Frt.; 4WD |
HUB,
SPLINED DRIVE |
GUARDIAN |
52-61706 |
[Rotor Hub] Frt.; 4WD; Use for Rotor {BD60441} |
WAGNER |
BD61706 |
[Rotor Hub] Frt.; 4WD; Use for Rotor {BD60441} |
Great,
so I've got the knuckles what next?
The
heart of a Hy Steer system is the steering arms, these are the
custom pieces that are attached to the top of the flat top knuckles, and
to which the steering linkage (drag link and tie rod) are attached.
They are available from many sources (see links at the bottom of the
page), or can be custom made if you have the tools and skill.
When making or buying, things to consider are:
- Mounting design (Chevy style cone washers, lug nuts, bolts and
locating dowels etc.) - see next section for important discussion on
this.
- Whether they are flat or "step up" to clear the springs
- Type of linkage mounting - TRE or Rod End, and whether the arms are
drilled or tapered for you choice
- Intended linkage design - True crossover will require 2 linkage
mounting holes in passenger side arm, 1 in drivers. Hy Steer
Inverted T will require only 1 hole in each steering arm.
- Placement of the draglink attachment hole (if crossover) - you want
this to be a distance from the center of the balljoint (point of
rotation of the knuckle) equal to the distance from the center of the
steering box shaft to the center of the TRE hole in the pitman
arm. In other words - balljoint to draglink hole on steering arm
= the horizontal "throw" of the pitman arm This
dimension will affect steering radius and Ackerman angle
- Placement of the TRE holes. With crossover design, proper
location is important to avoid binding between the tie rod and drag
link.
- Whether the arms "angle in" to allow clearance between the
steering joints and tire / wheel.
- Whether or not you need or want an angle machined in the face of the
arms so that the static angle of the steering joints is minimized.
Here
are some pics of some arms to give you an idea of what's available: |
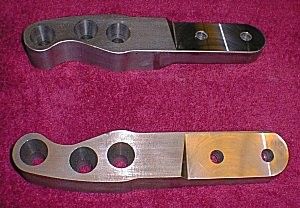 |
Arms from
Extreme Gear Offroad. |
|
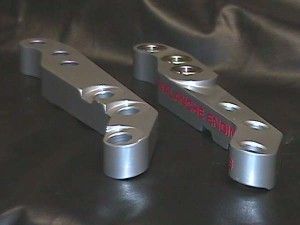 |
Avalanche's
new arms. |
|
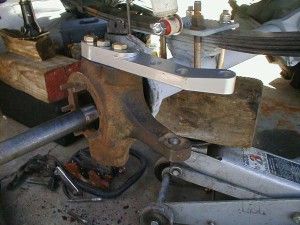 |
Avalanche
arm mounted. |
|
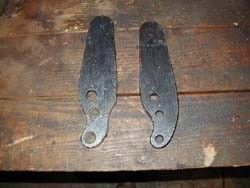 |
Basic
undrilled arms. |
|
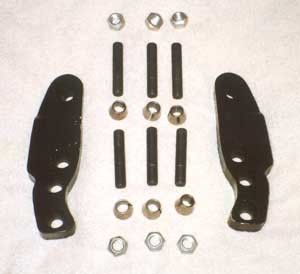 |
Arms and
mounting hardware from Tri County Gear. |
|
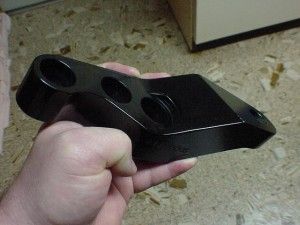 |
Super
trick step-up billet arms from OTT Industries. |
|
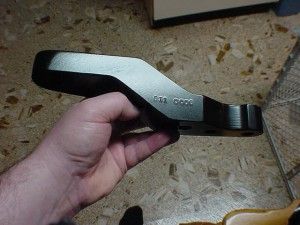 |
Super
trick step-up billet arms from OTT Industries. |
|
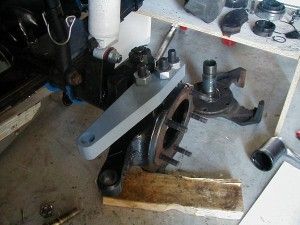 |
A
homemade arm attached with tapered lug nuts by Steve Meyers. |
|
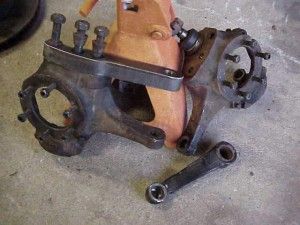 |
Basic
Arms from BR Fabworks (Bob Roggy). |
|
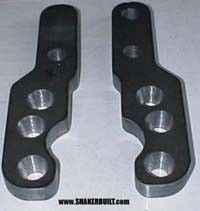 |
Nice "step in" arms from Shakerbuilt with good clearance from the
tire built in. |
|
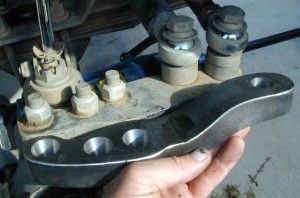 |
Cool
"step-up" arms from BR Fabworks. |
Alright
- but what's all the fuss about how you attach the arms to the knuckle - why
can't I just bolt them on?
I'll
let the text below explain, comments from knowledgeable folks (well, for
the most part - some of the comments are mine ! :-)
It's
actually pretty critical to have the two mating faces truly flat. This way
the clamping force of the bolts or studs is maximized- it's the
"friction" between the arm and the face milled into the knuckle
that does most of the work.
If
you simply rely on the bolts themselves, you're just begging for a failure.
Same
goes for drilling and tapping the holes square to the milled face- if the
bolts are crooked, they try to force the arm one way or the other. Or, if
the hole in the arm is a pretty close fit to the bolt/stud, the angle of
the bolt to the face will keep the arm from clamping correctly, and we're
right back where we started from.
Or
worse, you crank down on the bolt 'til the faces DO meet, then the bolt is
preloaded crooked, and more likely to break.
Being
a "competent part time machinist" myself, I very strongly suggest letting a skilled professional do the work. Even for a trailered-to-the-trail,
slow rock-rig, the steering is an extremely critical item.
-
Comments by DOC, a professional machinist.
The
steering arm obviously experiences continued cyclical loads that place the
mounting devices (bolts or studs) in shear load. ( I realize the strength
of the joint is primarily achieved by the friction between the mating
surfaces - none-the-less the fasteners still experience these loads - as
evidenced by them loosening) SAE bolts are not designed to be loaded in
shear, not to mention are not manufactured to close enough specs to allow
a tight enough fit so that play will not develop and they will not begin
to oval out the hole. Not to mention, drilling holes is not the proper way
to achieve an exact dimension hole - it should be rough drilled and then
reamed to final size. So if bolts are used, holes should be reamed, and
proper shear bolts (like AN - can't quote a number off the top of my head)
should be used. This is expensive and rare and more difficult, so GM came
up with the ingenious solution of using a stud with a split cone washer,
so that as the nut tightens, the cone cinches down and provides the
required zero clearance fit while still allowing use of SAE grade/spec
hardware.
You
can use bolts, but you have to use the right kind, or do something else to
compensate (like using interference fit locating dowels). |
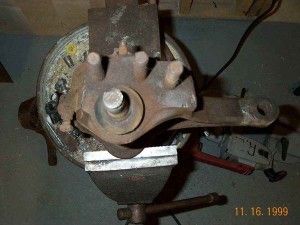 |
Here are
the stock studs in a GM knuckle. |
|
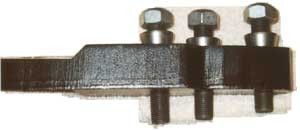 |
This
shows the studs, cone washers, and locking nuts.
And here are the studs and cone washers part numbers.
GM calls the cone washers "adapters".
Stud
3965137
Adapter (cone washer)
3965138
Each of these were about $3.50 a piece. So it cost me
under $24 for the studs and washers per side. And GM does not sell the nuts
(or at least my local dealer said they were not available). It is a
9/16-18 that's needed.
TriCounty Gear also sells the hardware separately.
$20 for the 3 9/16-NF studs, 3 conical "washers" and the 3 9/16
aircraft "stover" nuts. |
|
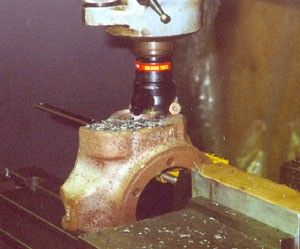 |
Knuckle
being machined flat. |
|
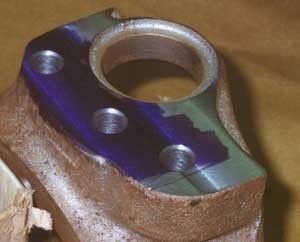 |
Knuckle
machined flat and drilled. |
OK
- you've got the knuckles and the arms all sorted out - time to build /
buy the linkage.
Since
you've come this far, it only makes sense to me to do a "true"
Hy Steer setup and mount the draglink and the tie rod above the springs.
You basically have 2 choices
1) A crossover design, where draglink and tie rod are independent.
The advantage being that toe and steering wheel center are easily adjusted
independently without having to disconnect anything, and that there is no
chance of the draglink "rolling" the tie rod before steering the
wheels. the disadvantage being the crowded linkage mounting on the
passenger side steering arm, and the possibility for bind between tie rod
and draglink.
2) An inverted T setup, where draglink mounts to tie rod. The
advantage being simpler mounting on passenger side steering arm, and
potentially less bind. The disadvantage being the draglink has to be
detached from the tie rod in order to adjust toe.
In either case, exactly how you lay out the linkage will depend on
things like spring height, location of steering box, type of steering arm
used etc.
You
can read about my crossover steering and the parts I used in parts 2 - 5 later in this article.
A very
popular Inverted T setup is to use '85 Chevy Blazer steering joints and
custom tubes.
The part
numbers required are:
Tie Rod:
ES2233L for pass side (reamed hole for TRE) NAPA PN 269-2554
ES2234R for driver side
Drag Link:
ES2027L for pitman arm (high angle)
ES2234R for pass side (mounts to TRE ES2233L)
The ES2027L and ES2026R are stock 85 Blazer drag link ends.
The ES2233L and ES2234R are stock 85 Blazer tre's. the ES2233L is the
tie rod end (not on the drag link) that has the steering stabilizer hole
that is re-tapered to the GM spec (1.5"/ft, but Drag link end has
same taper, but larger hole).
And all of these are 7/8-18" on the threaded ends
GM P/N's for the jam nuts (discontinued)
14024806
14024805
Below are some pics of this setup from Steve Meyers excellent page.
His article is linked below. |
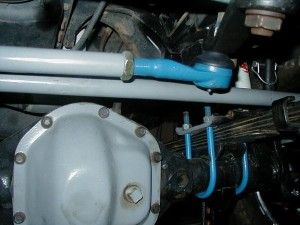 |
ES2027L
at Pitman arm.
Photo: Steve Meyers |
|
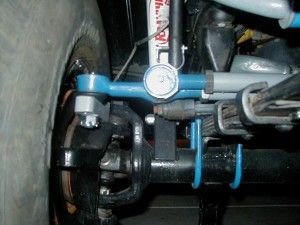 |
ES2233L
mounted to steering arm, with stock steering stabilizer hole re-tapered so
that ES2234R on end of draglink will fit to it.
Photo: Steve Meyers |
|
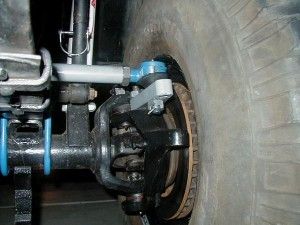 |
ES2234R
of tie rod attached to drivers side steering arm.
Photo: Steve Meyers |
|
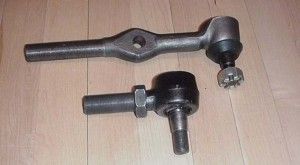 |
Top pic
is ES2233 which has a stock hole for steering stabilizer. This hole
has to be drilled and re-tapered from the other side for the TRE on the
draglink.
Bottom pic is of an ES2010
Photo: Steve Meyers |
|
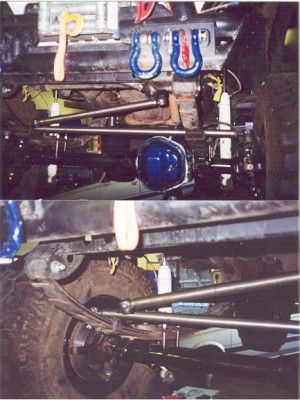 |
H8Mondays
has a unique and trick setup. he made his tie rod from
solid chromoly stock, and had an area on the rod machined flat, drilled,
and tapered to accept the end of his draglink.
I really like this setup for the clearance and no bind it gives between
draglink and tie rod.
Very cool! |
|
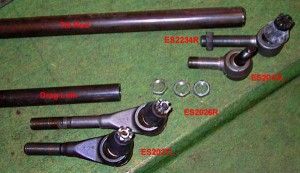 |
Some more
TRE part numbers and pics for your info. |
Part 2 - Design #1
Dana
44 Hy Clearance crossover steering Ver. 1
After
building my Hybrid front axle with D44 outers, including flat-top knuckles, it
was time to design the steering.
This was my first attempt at the "Hy Steer crossover steering"
setup on my Jeep. In the end, some parts worked, some needed
redesign. I eventually went through 3 more setups before being
satisfied. I have included all 4 setups so as to show what I learned
along the way. This is the first setup, the next 3 are linked at the
bottom of the page. Each successive page just shows the parts that were
redesigned, so all 4 contain useful info. |
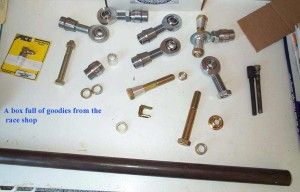 |
One of
the first decisions is whether to use rod ends (Heim joints) or TRE's
(standard automotive tie rod ends). I chose rod ends because they
are reasonably cheap, even for very good quality, available in many
different size bearings with 3/4-16 threaded shanks (the weld in threaded
bungs for the ends of the tubing are only available up to 3/4-16), and
since they do not require a tapered mounting hole, it is far easier and
cheaper to R&D different setups with rod ends. |
|
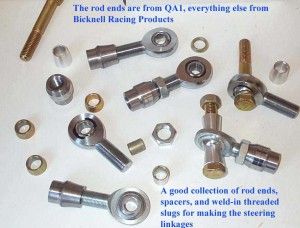 |
The Rod
Ends I chose are from QA1, | 21730 Hanover Avenue | Lakeville, Minnesota
55044 | Toll-Free: 800.721.7761.
I ordered them direct from the manufacturer.
All the other hardware is from the Bicknell
Racing Products catologue, ordered from my local race car supplier,
R&D Performance center, RR#5, Truro, N.S. 1-800-565-3795. |
These are the reasons I chose to use weld in threaded
slugs (or bungs) instead of just buying the correct ID tube and having it
tapped:
Using the threaded slugs might give you superior
threads than having the local shop cut the threads in the end of the
tubing, particularly if the
slugs have the threads rolled and not cut. In fact, it is now not
permissible to have cut threads on SAE rated fasteners.
I'd at least want to see how the shop is going to cut the threads,
especially in a 3' tube, and if they're just going to turn a big tap in
the end by hand I might be worried. Not to mention there are pages
and pages of references on different thread forms ( R type, J type etc.) ,
radius at the root, pitch, profile, different classes of thread (2, 3, 5
etc. - not to be confused with grades of fastener (2, 5, 8 etc.))etc and
I'd want to be sure the male threads on the TRE or rod end were the same
as those cut in the tube.
The rod
ends and radius slugs I use are designed to work together. However,
I’m probably overcomplicating the thread form concern (as usual) and
they’re all probably some sort of SAE standard, so this is likely not a
big concern (other than the previously mentioned bit about SAE not
allowing cut threads – I guess in the past some SAE bolts used to have
cut, rather than rolled threads, and they were not as good.)
One more thought about slugs vs. tapping tube.
Obviously tapping the tube you are limited to the alloy the tube is made
from, and I'm not sure your standard low carbon 1020 DOM mild steel is the
best thing for thread forms. On the other hand, the slugs can be
made from an alloy better suited to thread forms, as long as it is weldable
to the tube. |
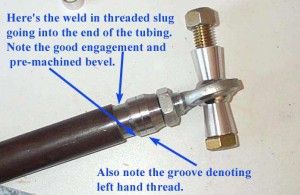 |
Essentially
they are a tight slip in fit inside the tube about an inch, and the edge
is beveled for the weld. |
|
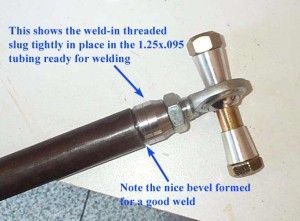 |
Also,
note the "radius" after the main body and before the end, where
the jam nut is. In terms of flow of stress and therefore fatigue
life, this is a superior feature over just having the threaded tube end
abruptly at the point where the threaded shank of the TRE or rod end
enters. The abrupt change in diameter causes a concentration of
stress and forms a weak point at this area, as the stress flowing along
the tube has to "bunch up and get around the sharp 90° corner"
formed at the abrupt change in radius. That's why I keep calling them
"radius" slugs. |
|
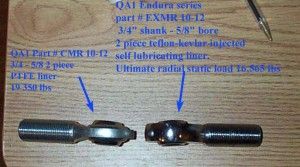 |
No matter
how much research you do before hand, sometimes you just need to handle
the parts. So I ordered 2 different styles of rod end from
QA1. Thes are them and their specs. I paid $16.29
for EXMR 10-12 and $12.14 for CMR 10-12.
The actual
part numbers are:
CMR10-12T - Right hand thread
CML10-12T - Left hand thread
EXMR10-12 - Right hand thread
EXML10-12 - Left hand thread |
|
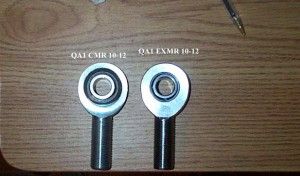 |
|
|
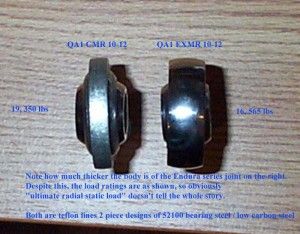 |
After
handling the, in my opinion, the EXMR are the superior part. And incidentally
the same ones Rubicon Express use in their products. |
|
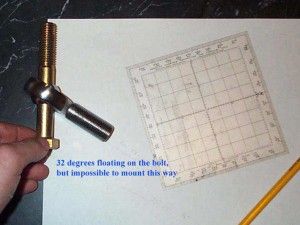 |
I have read many a good debate online about whether rod ends or TREs offered better "misalignment
angle". Since I had already decided on TREs for the reasons stated, I decided to do some first hand testing. |
|
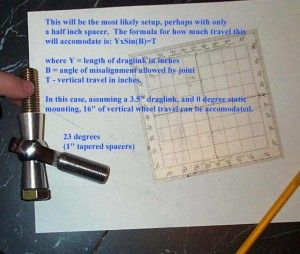 |
Slight
typo on the pic label, it should read: "assuming a 3.5 FOOT
draglink" |
|
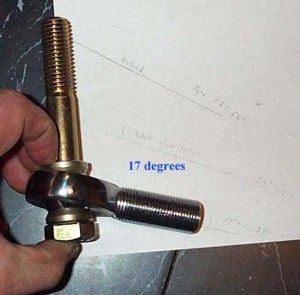 |
Misalignment
of 17 degrees with the minimum 1/4" spacers. |
|
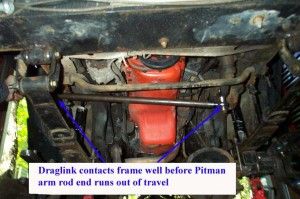 |
Here are
the "on the Jeep" testing shots. |
|
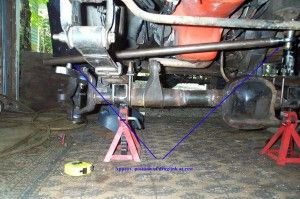 |
|
|
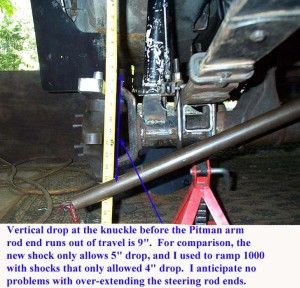 |
|
|
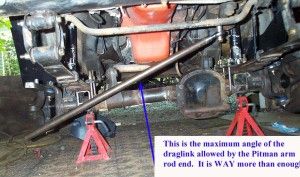 |
|
|
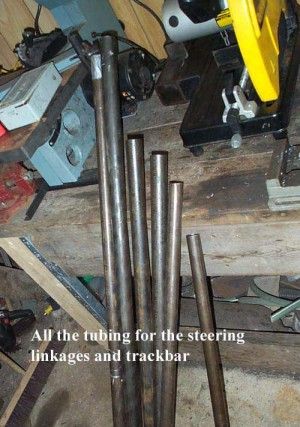 |
Here's
the pile of tubing I ordered for the linkages. |
|
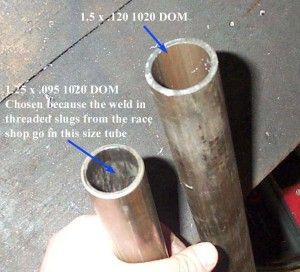 |
The weld
in threaded slugs are made to fit in 1.25" x .095 wall tubing - light
and strong for the race car builders. I wanted something a little
beefier for trail use, so I ordered some 1.5" x .120 tube so sleeve
over the other. That's a total of .215" thick - almost
1/4"!! |
|
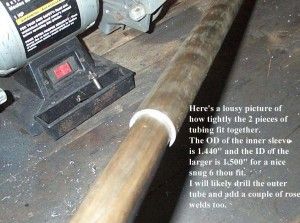 |
|
|
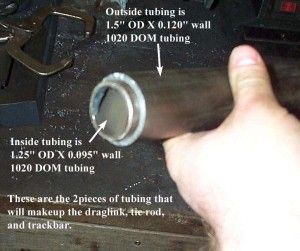 |
|
|
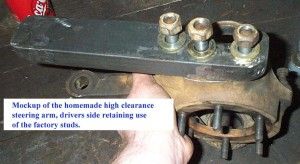 |
There's a
ton of info on the research page about D44 steering arms, who makes them,
how, why, etc. These are my home-made arms. |
|
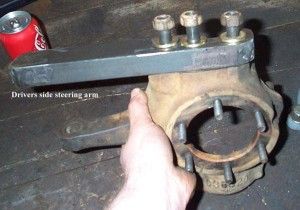 |
To make
them I cut the shape from 1" thick steel. For the drivers side,
I tacked the stock Chevy steering arm to the blank, and drilled the 3
holes. That was all that was required since the stock drivers side
Chevy steering knuckle is already drilled and tapped. I retained the
use of the 3 9/16 studs and added new hardened washers and ovalated
locking nuts. |
|
 |
The
passenger side was a bit more work. First the "flat"
surface of the knuckle has to be machined flat. Then I tacked the
arm on the knuckle, and drilled through both together with a 33/64 drill
bit (the size required for tapping the knuckle). Then I knocked the
arm off the knuckle, tapped the 3 holes in the knuckle with 9/16-NF tap,
and drilled the holes in the arm out to 9/16" for the bolts. On
this side I used Grade 8 SAE 9/16-NF bolts and hardened washers from
Bowman. |
|
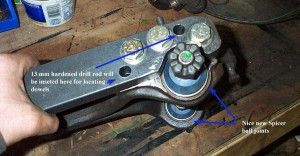 |
Because I
was not re-using the stock Chevy tapered hole and split conical washer
system for positive zero tolerance location of the steering arm (an
excellent design, but requiring more expensive machining and the
rob-you-blind Chevy hardware [see research page]), I needed another method
for assuring a tight positive fit that won't loosen, develop play, and
place dangerous shear loads on the bolts. The bolts alone are not
sufficient since, in order to be able to fit the bolt in and out of the
hole, there is too great a clearance between the OD of the bolt and the ID
of the hole. remeber, the bolts are not for locating, just clamping. |
|
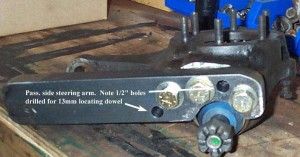 |
I decided
on using locating dowels of hardened steel, pressed (pounded!) into
slightly undersize holes for a tight fit. |
|
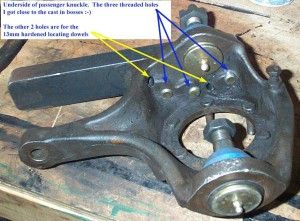 |
|
|
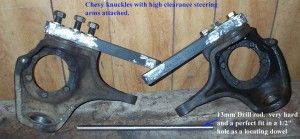 |
|
The
next pics show how the linkage all went together, and some of the things I
wasn't happy with. |
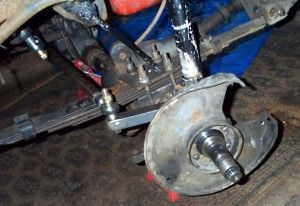 |
This is
the drivers side. The hole for the tie rod was drilled the same
distance from the center of the balljoint as the stock Chevy hole was. I
used 2 tapered 1/2" steel spacers on either sides of the rod end, and
a 5/8" Grade 8 bolt with oval locking nut.
It's not a good design since the bolt is too long, and really the rod
end should only be mounted in double-shear, especially with spacers on
either side. As it is, the bolt is not a precise fit in the arm (no
SAE bolt and drilled hole assembly is - precision fit for an assembly such
as this can only be accomplished by drilling the hole undersize and
reaming to final size, then using an appropriate precision bolt like an AN
spec bolt), and the rod end will place bending loads on the bolt, which
will fatigue and / or begin to wear the hole, leading to looseness and
more wear in a vicious cycle until something fails. A proper
"double shear" assembly would have the arm forming a
"bracket" on either side of the rod end. |
|
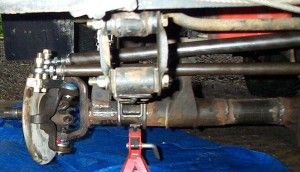 |
On the
drivers side, I used the same two 1/2" steel spacers for the tie rod,
and a 1.5" spacer underneath the drag link rod end and 1/2"
spacer on top. This was required to space the drag link up enough to
clear the tie rod (notice too that I could only build the tie rod out of
the single thinner tube, or it would have been too large and interfered
with the drag link).
The result is an ungodly mess of spacers and improperly loaded bolts
and just plain sucks from an engineering standpoint. |
|
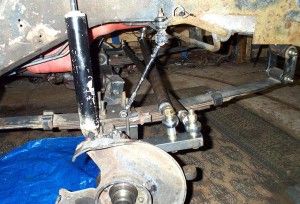 |
This is
almost too embarrassing to show, but hopefully you can learn from my
mistakes. I had to stack 2 spacers under the drag link to get the
1.5", one of which was aluminum and began to deform when the 5/8" bolt was torqued. Yeuch !!
The drag link hole in the steering arm was drilled the same distance
from the center of the balljoint as the end of the pitman arm is from the
steering box output shaft - namely 6" in my case. |
|
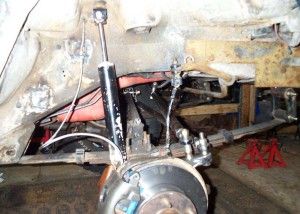 |
I had to
bend the swaybar disconnect to clear the drag link, and the track bar axle
mount used the old drivers upper control arm bracket on the axle. In
the end, I removed the swaybar and trackbar altogether and do not regret
it. |
|
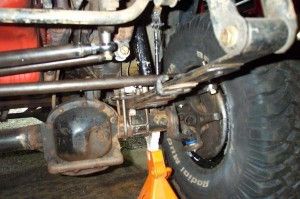 |
Another
pretty gross setup. A 1" aluminum spacer on one side of the
pitman arm rod end, and a 1/2" steel on the other.
The automotive industry designed and uses TREs for a reason !! |
|
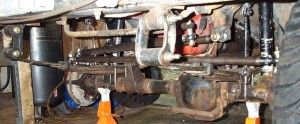 |
The frame
side trackbar bracket was the only bit that was sort of OK, nut I ended up
junking it anyway. |
|
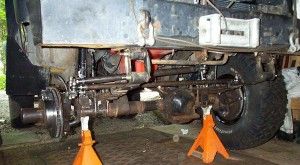 |
Looks
good if you didn't know any better !! |
|
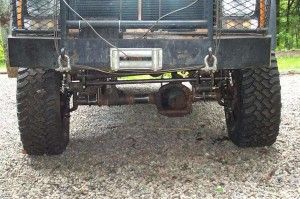 |
At least
it was all up out of the way. |
|
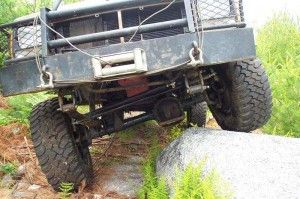 |
Well, it
was all tucked up nice and safe, so that was something. |
|
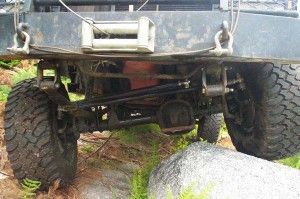 |
The
problem was, even with the awful mess of spacers the drag link and tie rod
still intefered |
|
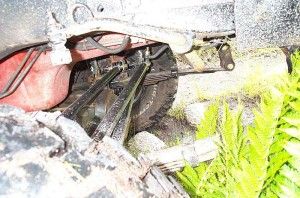 |
This
shows the problem |
Part
Numbers Used:
Part |
Description |
Part
Number |
Price
(Cdn $) |
Weld in
threaded slug |
3/4"-16
RH thread, for 1.25x.095 tubing |
BRP1492 |
6.58 |
Weld in
threaded slug |
3/4"-16
LH thread, for 1.25x.095 tubing |
BRP1493 |
6.75 |
Jam nut |
3/4"-16,
steel, RH thread |
BRP788 |
1.40 |
Jam nut |
3/4"-16,
steel, LH thread |
BRP789 |
1.64 |
Steel
tapered spacer |
5/8"
bore, 1" OD, 1/4" tall |
BRP724 |
2.00 |
Steel
tapered spacer |
5/8"
bore, 1" OD, 1/2" tall |
BRP721 |
1.46 |
Aluminum
tapered spacer |
5/8"
bore, 1" OD, 3/4" tall |
BRP736-1 |
1.98 |
Aluminum
tapered spacer |
5/8"
bore, 1" OD, 1" tall |
BRP737 |
1.65 |
Steel
tubing |
1.25"
X .095, 1020 DOM |
MAT1.250X095DOM |
4.50 / ft |
Steel
tubing |
1.50"
X .120, 1020 DOM |
|
6.00 / ft |
Summary: A good start, but definitely not the complete solution. The use of rod ends is not the best, and the draglink and tie rod bind with any suspension movement. On to Version 2.
Part 3 - Design #2
Version 1 didn't work perfectly so I made it worse. A lesson in what NOT to do!
This was pretty much a disaster - it's sole purpose is now to serve as a warning to others.
The main issue to be resolved was addressing the binding between the drag
link and tie rod. I accomplished this by raising the draglink
attachment at the knuckle, and reducing the spacers under the tie rod rod
ends. Since I was still doing R&D, i kept the rod ends for now -no
point reaming a bunch of tapered holes for TREs and then having to re do
them. The nice thing about the rod ends was the ease of changing
spacers and moving stuff around. It worked as far as eliminating contact
between the linkages, but using that great big spacer under the drag link
is not a good design, and even with the weenie little 1/4" extra
bracket, this was not a proper "double shear" arrangement.
I ran and wheeled this setup for a while, but just wasn't comfortable with
it, so it went in the bin, and version 3 was born. Anyway - here's a
look at the ill fated version 2. |
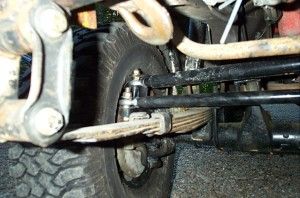 |
Much
better clearance between the linkages. |
|
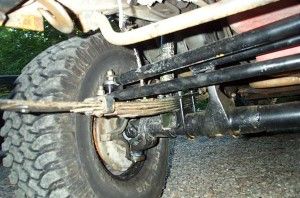 |
Much
better clearance between the linkages. |
|
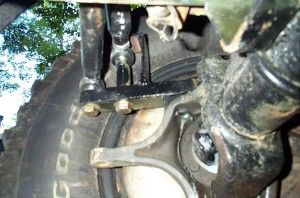 |
But that
drag link attachment is just ugly! |
|
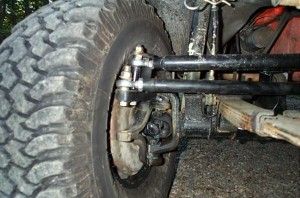 |
It might
work with proper bracing / brackets |
|
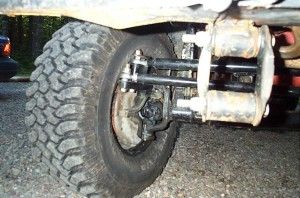 |
|
|
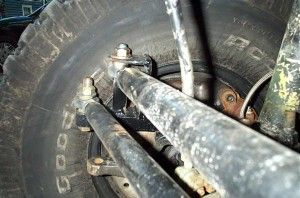 |
The drag
link was nice and flat for no bump steer |
|
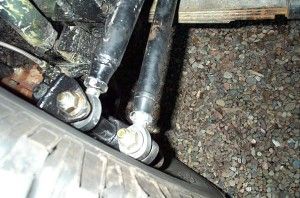 |
|
|
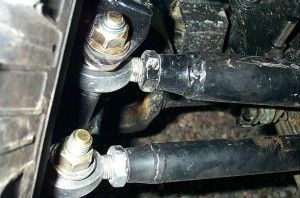 |
But that
bolt is potentially under tremendous force. |
|
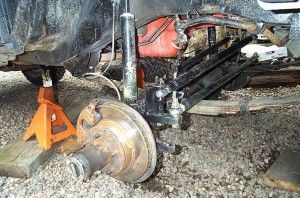 |
I didn't
bend or break it, but that "warm fuzzy" feeling just wasn't
there. |
|
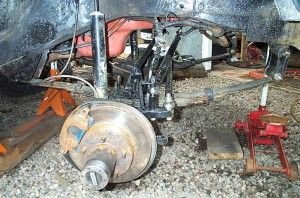 |
|
|
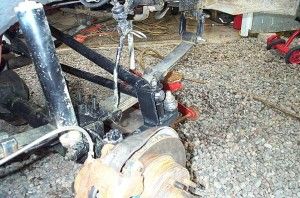 |
|
|
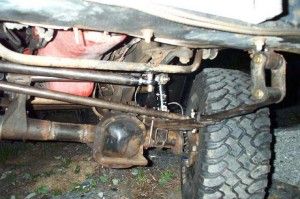 |
With the
tie rod sitting on 1/4" vice 1/2" spacers, it did get a little
close to the springs. |
|
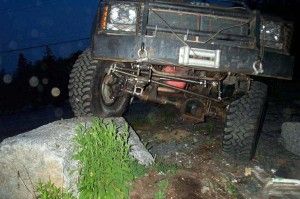 |
The
clearance was ok, much improved |
|
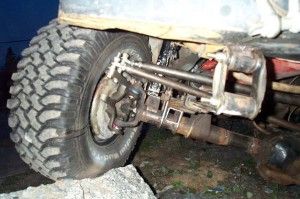 |
|
|
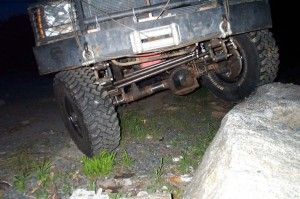 |
But still
a little close with the right side drooping. |
Summary: A
learning experience......which led to the even more ill fated Version 3
!!!
Part 4 - Design #3
From bad to worse - see me bend and brake this poor design. More of what didn't work.
Not happy with the setup of version 2, I tried something else. I
attached the drag link to the steering arm with the rod ends and only a
1/2" spacer. I then moved the tie rod down to the stock
location in the Chevy knuckles using TREs |
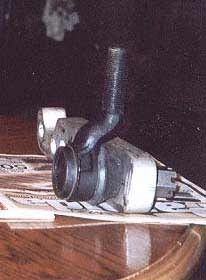
Photo courtesy Jeff Ayers |
This is
the ES375 TRE that I used.
The is the only one choice for a 3/4-16 TRE is with the
"big" taper, that is from .776"to .667" (same as the
TRE taper in stock Chevy and FSJ Dana44 knuckles)
The part numbers are:
Moog ES375L - Right hand thread, drivers side
"outer" tie rod end (left hand side) for '67-'72 1/2ton &
3/4ton GMC trucks
Moog ES375R - Left hand thread, Passenger side
"outer" tie rod end (left hand side) for '67-'72 1/2ton &
3/4ton GMC trucks
The catch with these is that they have a "dog
leg" in them, that can either really help or really hurt your design,
depending on application. This helped me as it helped the tie rod
clear the underside of the springs.
There is no "straight" TRE with 3/4-16 threads
and the "big" taper. |
|
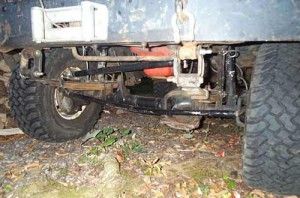 |
As you
can see, the tie rod is left much more vulnerable down here, and I bashed
the daylights out of it in just one trip. So much for driving
finesse! |
|
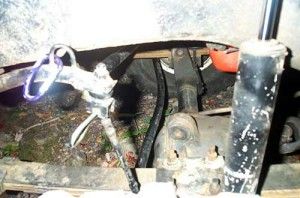 |
Nice bend
! |
|
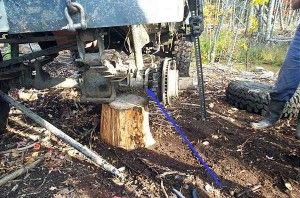 |
The final
really bad idea of version 3 was to make the tie rod double wall ( 1.25" x .095 wall tubing sleeved with 1.5" x .120 tube ).
That's a total of .215" thick - almost 1/4"!!
This was TOO strong, as the first
time I bashed it the $80 TRE snapped cleanly right where the threaded
shank entered the rod (arrow).
I was extremely lucky in that
there were 3 threads left on the stub of a TRE and after painstakingly
dressing them with a small file, I got the stub threaded back in enough to
limp off the trail. |
Summary: Back to the drawing board !!! On to version 4
Part 5 - Design #4:
See me figure it all out, actually build something that works and return to using good old fashioned Tie Rod Ends
OK - not happy with the rod ends of version 1 and 2, version 1 design caused binding, version 2 placed too much stress on the knuckle mount of the draglink, version 3 placed the tie rod in a vulnerable location - resulting in bending or TRE breakage. Time to put it all together in a system that will work. The major changes were the use of TREs at all 4 mounting points, and the use of a 2" spacer block of cold rolled steel placed between the knuckle and the steering arm.
Due
to the fact that the weld in radius slugs I used on my linkages have a
3/4-16 female thread, my choice of TREs was somewhat limited.
There are only 2 TRE's available with 3/4-16 threaded
shanks. They are
1) Moog ES-150L left hand thread and Moog ES-150R right
hand thread
These have the "medium" size taper that is
from .714" to .636"
The stock application include:
FORD TRUCK F100/F250 61-65
GMC TRUCK K1500/K2500 63-66
CHEVROLET TRUCK K10 64-66
They will be listed as "inner" and "outer"
tie rod ends, with the inner being the left/drivers side (left hand thread,
PN ES150L) and the outer being right/passenger side (right hand thread,
PN ES150R)
They are also available from: http://www.afcoracing.com/ and http://www.stockcarproducts.com/
2) The other choice for a 3/4-16 TRE is with the
"big" taper, that is from .776"to .667" (same as the
TRE taper in stock Chevy and FSJ Dana44 knuckles)
The part numbers are:
Moog ES375L - left hand thread, drivers side "outer"
tie rod end (left hand side) for '67-'72 1/2ton & 3/4ton GMC trucks
Moog ES375R - right hand thread, Passenger side
"outer" tie rod end (left hand side) for '67-'72 1/2ton &
3/4ton GMC trucks
The catch with these is that they have a "dog
leg" in them, that an either really help or really hurt your design,
depending on application.
There is no "straight" TRE with 3/4-16 threads
and the "big" taper. |
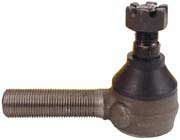 |
This is
the Moog ES150. |
|
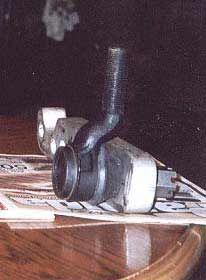
Photo courtesy Jeff Ayers |
This is
the Moog ES375. |
|
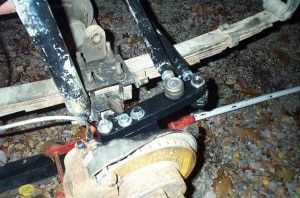 |
The
"trick" that made the setup work for me was mounting the
draglink to the top of the steering arm with an ES150 TRE, and mounting
the tie rod underneath the steering arm using an ES375 TRE. The
2" spacer under the steering arm and the dog leg in the ES 375
allowed the tie rod to clear the springs, even mounted under the arm. |
|
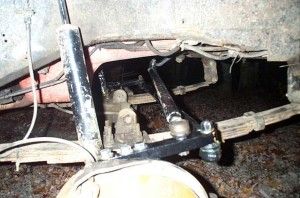 |
Chad and
I bought a Tapered reamer for $200 Cdn from www.afcoracing.com
This expensive but cool tool allowed me to taper the original 5/8"
straight holes drilled for the rod ends to be tapered for both the ES150
and ES375 Tie Rod Ends.
The tie rod attachment points remain vertically above the stock Chevy
knuckle locations. The draglink attaches to the steering arm
5.75" from the balljoint center. I moved it back 1/4" from
the original 6" location to ensure no clearance issues between the
linkages. |
|
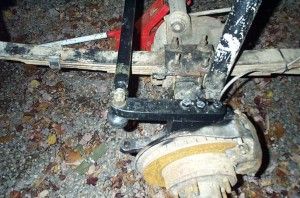 |
Drivers
side, tie rod mounted under the steering arm with Moog ES375L. |
|
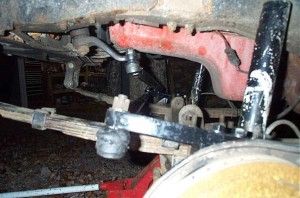 |
In this
pic you can see the drag link mounted to the (stock) pitman arm with a
Moog ES150L. |
|
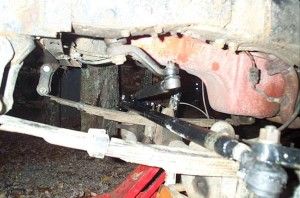 |
There is
plenty of clearance between the tie rod and springs. |
|
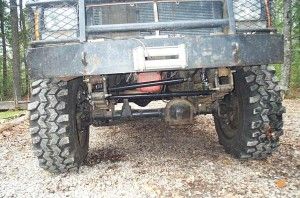 |
Up and
out of the way again, perfect for my driving style :-) |
|
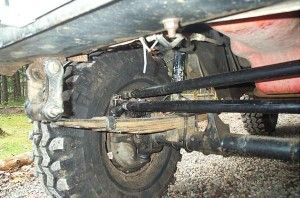 |
There is
also plenty of clearance between the drag link and the tie rod, no more
linkage bind. |
|
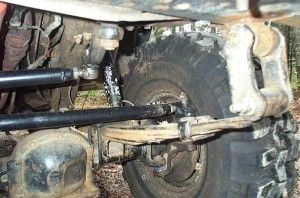 |
|
|
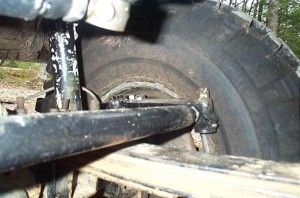 |
|
|
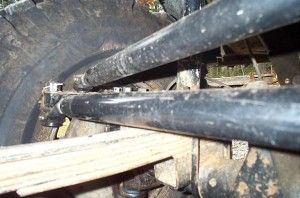 |
The
2" spacer, however, raises the steering arm to the point where is
just rubs on the tire. No worries - custom beadlock wheels with less
backspacing are on the way !! |
|
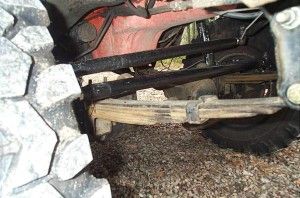 |
The
2" spacer also raises the draglink attachment enough for really nice
angles on the draglink, resulting in no bumpsteer and plenty of allowable
droop. |
Summary: Well,
I think I have it now! In retrospect, if I were to start all over
again. I would probably use an inverted T setup using '85 Chevy Blazer
parts, where the drag link connects to the tie rod. Only trick would
be either tapping the right size tube for the 7/8-18 threaded shanks of
the Blazer TREs, or having the machine shop drill out and re-taper the
weld in radius slugs (only issue is - try finding a local machine shop
with a 7/8-18 Left hand tap, and even worse finding jam nuts in 7/8-18 (if
they don't come with your TREs) is virtually impossible, and they too have
to be custom made. See the RESEARCH page for details on this kind of
setup. Right now, I'm very happy with my setup. |