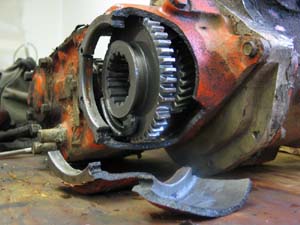 |
First case explosion.
So much for my first competition! |
|
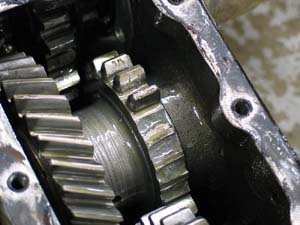 |
And again, the result
of a hard climb. The little straight-cut spur gears on the Dana20 low-range
and intermediate gears just aren't up to the task of pushing a 5000lb buggy
on 42" tires up near-vertical rocky climbs! |
About the Atlas-4SP
The Atlas-4SP was designed so that users could have ultra-low gearing for rock crawling, a low gear for trail use, and mid- and high-ranges for sand, mud, and street, all in a single, short, light, top-quality, custom-made, brand-new package. Sweet! That's exactly what I wanted.
Here's a look at the basic data:
CASE:
Material ....................356-T6 Heat Treated Aluminum
Weight.......................125 lbs. (dry)
INTERNAL COMPONENTS:
Gears .........................Helical Cut
Planetary Gears .......6 Gears Helical Cut
Bearings ....................Needle & Taper Rollers
Synchronizers ...........Borg Warner
Available Input Shaft Splines: 21, 23, 27, 29, 31, 32, 34
Tail Shaft ..................H.D., 32 Spline,
Front Output ............32 Spline
RATIOS:
Low Range ................2.0:1, 2.72:1, & 5.44:1 or 2.72:1, 3.8:1, & 10.34:1
High Range............... 1 : 1
LUBRICATION:
Preferred: Torco GL-4 Professional Series MTF (Manual Transmission Fluid)
Optional: Castrol Syntec 5w-50, Valvoline Synthetic 20w-50 or Mobil 1 Synthetic 15w-50.
Quarts .......................Liters
2.5 ..............................2.36
LENGTH COMPARISON:
Atlas Short tail - 15”
NP 231 - 20.5"
Atlas Long tail - 17”
NP241 Rock Trac T/C - 15-1/4"
Dana 300 - 12"
The Atlas-4SP is essentially two parts cleverly combined in a single compact package - like a doubler all in one. The first part is the planetary reduction assembly which is mated directly to the main case.
The planetary reduction assembly is a New Process Gear design - the same used in the NP241-HD transfer case. This assembly has been rated to withstand 5,555 ft./lbs. of torque, and up to 11,000 lbs. gross vehicle weight. It has been used in many heavy-duty vehicles including the original H1 Military Hummer and one-ton Dodge trucks. The planetary is shifted separately from the transfer case via a cable or electronic shifter and has a low range of 2.72:1 and a high range of 1:1. The six-planetary design makes it quiet, strong, and easy to shift. However, the planetary is not a synchronized shift-on-the-fly design and must be operated when the vehicle is stopped.
The main case of the 4SP is similar to the 2-speed Atlas but it does have some differences. All of the gears, with the exception of the input gear, are the same. The front output uses all of the same parts. The rear output shaft is different in the 4SP and different bearings are used in some spots. Both front and rear outputs are 32-spline standard. The main case of the 4SP is the same raw casting as the 2SP, but has some machining differences to make it into a 4SP. The main case functions independently from the planetary reduction assembly and retains all of the normal Atlas features such as: front and rear outputs controlled independently, the “front only” option, and synchronized shift-on-the-fly design. The main case can be shifted via standard twin-sticks or by the new cable shifters. It is available in either 2.0:1 or 3.8:1 low-range options. Combined with the planetary reduction assembly's 2.72:1 low range the available 4SP rations are 1:1, 2.0:1, 2.72:1, & 5.44:1 or 1:1, 2.72:1, 3.8:1, & 10.34:1.
The 4SP mates directly to 21, 23, 27, 29, 31, 32 and 34 spline transmission outputs. It has a circular bolt pattern on the front, identical to the one found in Jeep vehicles. Advance Adapters has a variety of different adapters available to retrofit the 4SP into nearly any application. I used a combination of AA parts to fit mine neatly behind my old 10-spline SM465 4-speed manual transmission.
The 4SP can also be custom-ordered with a dizzying array of options/configurations: CV or non-CV outputs, yokes or flanges, speedometer or VSS tail housings, ultra-short competition tail housing, left- or right-hand front output, cable, electric, or lever shift - the list is endless and each case is a custom unit built to your specifications. Rather than try to list each possible option or configuration I refer you instead to the Atlas Transfer Case Installation Guide that contains a wealth of information on everything from gear ratio options to custom rotations to input spline configurations and adapter selection.
My Atlas-4SP
To fit my application I ordered the following:
- Atlas-4SP with 1:1, 2.72:1, 3.8:1, & 10.34:1 ratios - because I wanted the lowest possible crawl ratio and felt the 1 - 2.7 - 3.8 - and 10 to 1 ratios give the best possible range of available ratios. Think of it like this - 1:1 for high-speed work, 2.7:1 (like a stock Jeep) for mild trails, 3.8:1 (like a normal aftermarket low-range) for tough trails and 10:1 for crazy rock crawling!
- Right-hand-side front drop to match my Chevy D60 front axle.
- 1350 non-CV yokes - because this is the option that comes with the correct output seal diameter to work with High Angle Driveline's 1350 CV shafts that come with their own custom flanges.
- Cable shift option - for maximum shifter-mounting flexibility, not only in this rig but in any possible future rig. I also wanted to try the cable shifters having rowed manual-shift levers for many years.
- 10-spline SM465 to 23-spline Jeep transfer case adapter, originally intended for swapping an SM465 into a Jeep - to mate the Atlas 4SP to my old 10-spline SM465.
- 23-spline input - to match the output of the adapter kit.
Here's what I got: |
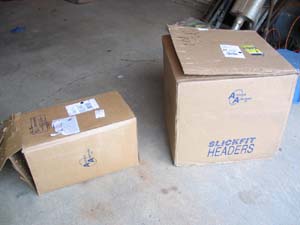 |
Two boxes arrived
on the holiest of holy days! The large one on the right holds the Atlas-4SP
and the smaller on the left has two more boxes inside with all the other
bits in them. |
|
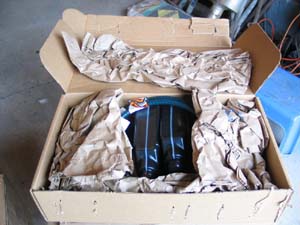 |
Everything was well
packed and well protected. |
|
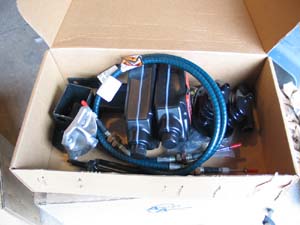 |
One of the smaller
boxes contains the twin-stick cable shifters and the MTF (oil) for the case. |
|
 |
The other was equally
well packed... |
|
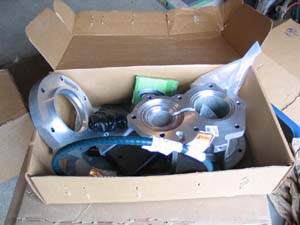 |
... and held the
tranny to T-case adapter and the cable shifter for the planetary reduction
box. |
|
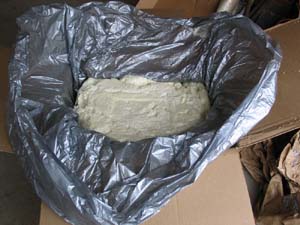 |
No chances are taken
with the Atlas itself - it comes completely packed in foam. |
|
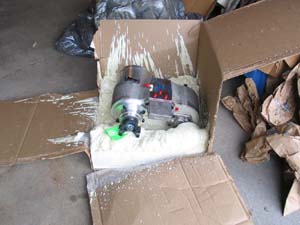 |
I had to cut the
box apart to get it out. Nice! |
|
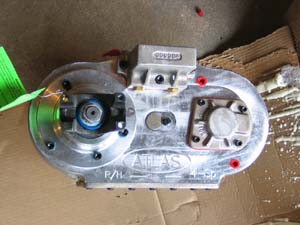 |
And then suddenly
there it is!
View from the back. Note engraving
showing that it's a right-hand drop 4-speed Atlas. |
|
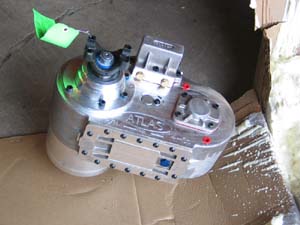 |
The green tag affixed
to the rear output yoke warns the user that the case is shipped dry and must
be filled with lube before operation. |
|
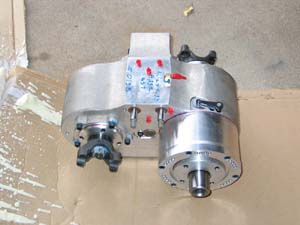 |
All the threaded
holes and openings are covered with or plugged by red stoppers that keep
debris out of the case during shipping and handling. |
|
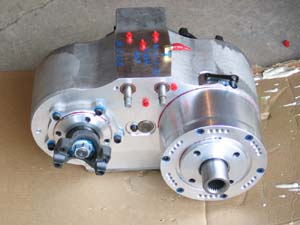 |
It's really quite
a work of art - even with all these pictures it's hard to appreciate the
compactness or light weight until you see one up-close and in-person. |
|
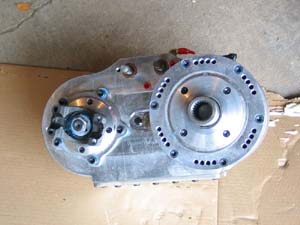 |
View from the front. |
|
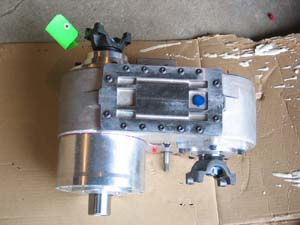 |
The underside of
the unit showing the access cover and blue-anodized drain plug. |
|
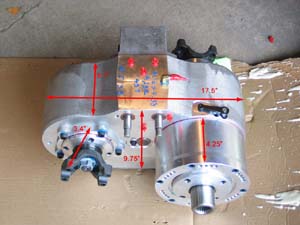 |
Atlas-4SP dimensions. |
|
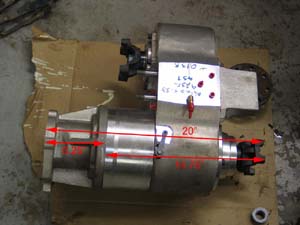 |
Atlas-4SP length
with short tail housing (no speedometer) and 32-spline 1350 non-CV yoke. |
|
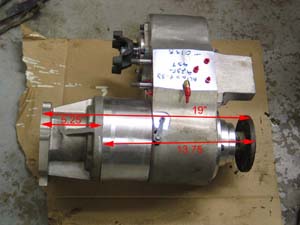 |
Atlas-4SP length
with short tail housing (no speedometer) and 32-spline High Angle Driveline
1350 CV flange. |
The Parts
Twin-stick
Cable Shifters |
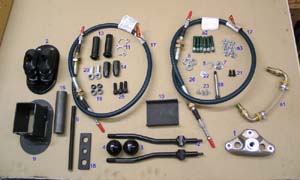 |
This is a layout
of all the parts for the twin-stick cable shifters (for shifting the main
case) plus the lubricant-level sight tube and the studs and nuts to mount
the case to the transmission adapter.
All the parts here, along with
the supplied lubricant, Torco MTF, form the kit: part no. 303009. This
kit is sold with the Atlas-4SP (included in the price) if you specify
"cable shift" as an option.
The parts key is below: |
Key:
No. |
Quantity |
Part No. |
Description |
1 |
1 |
302051 |
Twin-stick base mount |
2 |
1 |
302060 |
Twin-stick shift boot |
3 |
1 |
302061 |
Front shift knob |
4 |
1 |
302062 |
Rear shift knob |
5 |
1 |
302075 |
1/2" inside star washer |
6 |
1 |
302080 |
1/2"-NC13 x 7" all-thread |
7 |
1 |
303120 |
1/2"-NC13 serrated locknut |
8 |
3 |
303121 |
1/2"-NC13 jam nut |
9 |
1 |
303301 |
Shifter body |
10 |
1 |
303302 |
Shifter body bottom cover plate |
11 |
1 |
303303 |
Barrel retainer plate |
12 |
2 |
303304 |
Shifter handle |
13 |
2 |
303305 |
Cable barrel |
14 |
2 |
303306 |
Shift rail adapter |
15 |
1 |
303307 |
Extension tube bracket |
16 |
1 |
303308 |
Extension tube - 4.85"
long |
17 |
2 |
303309 |
Shifter cable - 48" long |
18 |
1 |
303310 |
5/16" x 2-1/2" pivot
shoulder bolt |
19 |
4 |
303312 |
Shifter handle pivot bushing |
20 |
2 |
303313 |
1/4" female Heim joint |
21 |
3 |
FJ4544 |
1/4"-NC20 x 5/8" button
head cap screw |
22 |
1 |
722523 |
1/4" flat washer |
23 |
4 |
722542 |
#10 x 1/2" self-drilling
screw |
24 |
1 |
723141 |
5/16"-NC18 locknut |
25 |
3 |
723731 |
3/8"-NC16 x 1" socket
head cap screw |
26 |
3 |
920026 |
Handle cotter pin |
a1 |
1 |
301600 |
Sight tube kit |
a2 |
6 |
302069 |
Atlas stud |
a3 |
6 |
302071 |
3/8"-NF24 nut |
|
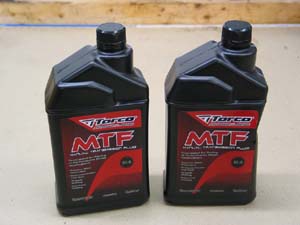 |
This is the transfer
case lubricant that is recommended for the Atlas 4-SP and is supplied with
unit. You're supposed to get 2 quarts if you order a regular 2-speed Atlas
(capacity 2 qts) and 3 quarts if you order a 4-speed Atlas (capacity 2.5
qts). For some reason I only received 2 quarts with my Atlas-4SP. |
|
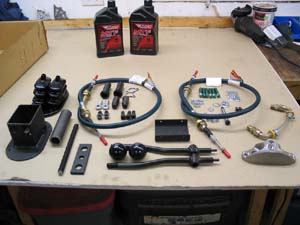 |
The complete kit,
part number 303009. |
|
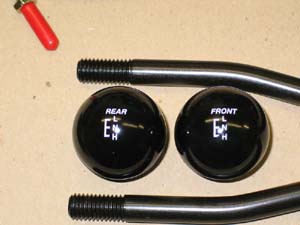 |
Close-up of the
shift knobs. |
|
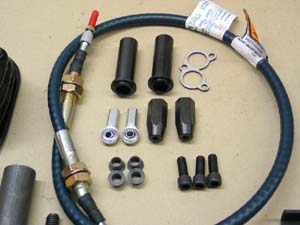 |
Close-up, parts
of kit 303009. |
|
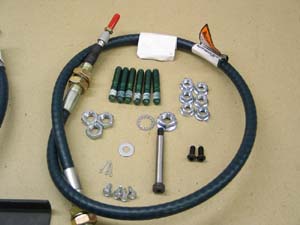 |
Close-up , parts
of kit 303009. |
Reduction
Box Cable Shifter |
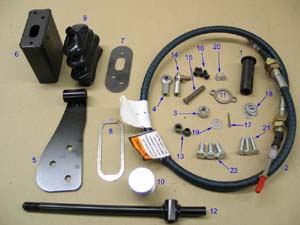 |
This shows all
the parts of the cable-shift mechanism for the planetary reduction box.
This kit, for right-hand drop
cases, is sold as part no. 344020R. It is sold separately from the Atlas-4SP,
presumably because a differently priced electronic-shift kit is optionally
available.
Parts key below. |
Key:
No. |
Quantity |
Part No. |
Description |
1 |
1 |
303305 |
Cable barrel |
2 |
1 |
303309 |
Shifter cable - 48" long |
3 |
1 |
303121 |
1/2"-NC13 jam nut |
4 |
1 |
303313 |
1/4"-NF28 female Heim joint |
5 |
1 |
340517-R |
Cable shifter bracket |
6 |
1 |
340600 |
Shifter housing |
7 |
1 |
340601 |
Shifter housing mount plate |
8 |
1 |
340602 |
Single stick boot ring |
9 |
1 |
340605 |
Single stick boot |
10 |
1 |
340607 |
Shift knob |
11 |
1 |
340610 |
Barrel retainer |
12 |
1 |
340611 |
Cable shifter handle |
13 |
2 |
340612 |
Handle pivot bushing |
14 |
1 |
340613 |
1/4"-NF28 ball joint |
15 |
1 |
340614 |
Clevis pin |
16 |
3 |
340615 |
1/4"-NC20 x 5/8" button
head cap screw |
17 |
1 |
340616 |
Cotter pin |
18 |
3 |
720015 |
3/8" flat washer |
19 |
1 |
722523 |
1/4" flat washer |
20 |
2 |
722542 |
#10 self-drilling screw |
21 |
3 |
722543 |
1/4"-NF28 x 1" shifter
housing bolt |
22 |
3 |
723720 |
3/8"-NC16 x 3/4" bracket
mounting bolt |
|
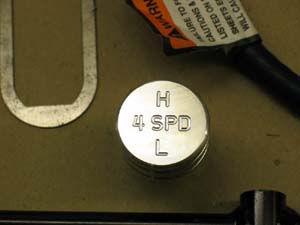 |
Close-up of 4-speed
reduction box shift knob, part number 340607. |
Adapter |
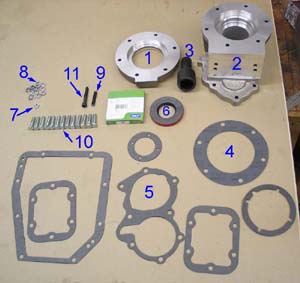 |
This picture
shows the complete adapter kit part no. 50-9808. This kit is sold as "GM
Truck 4WD 4SP Model SM465 10 Spline to Jeep NP231 23 Spline Transfer Case
(short design)"
As you can tell from the name
- it was originally designed to retrofit the SM465 4-speed tranny into
a Jeep.
Recall that the Atlas-4SP is
only available in input splines 21, 23, 27, 29, 31, 32 and 34 - essentially
NVG input spline counts because of the NVG 6-planetary design reduction
box on the front of the Atlas 4-SP.
That's why this SM465 to Jeep
23 Spline transfer case adapter kit is the ideal kit to fit the Atlas-4SP
behind my 10-spline SM465 and is also why I ordered the Atlas-4SP with
23-spline input.
Because I'm using it to fit
an Atlas-4SP behind an SM465 as opposed to using it to fit an SM465 into
a Jeep there are a few parts I didn't use. These are identified in the
parts key below.
The kit also includes a number
of gaskets that aren't strictly needed (unnumbered in the pic at left)
- a full set for overhauling the SM465 - but they're nice to have in case
you're rebuilding your tranny at the same time. |
Key:
No. |
Quantity |
Part No. |
Description |
1 |
1 |
51-0404 |
Spacer Adapter |
2 |
1 |
51-9808 |
Adapter casting - 5.250"
long |
3 |
1 |
52-9700 |
Spud shaft 10-spline internal
x 23-spline external |
4 |
1 |
716515 |
Gasket (Adapter to Atlas) |
5 |
1 |
716517 |
Gasket (SM465 to Adapter) |
6 |
1 |
716729 |
National Seal (NOT USED) |
7 |
1 |
723701 |
3/8"-NC16 hex nut |
8 |
14 |
723704 |
3/8" lock washer (only
8 used) |
9 |
1 |
723711 |
3/8"-NC16 x 2" stud |
10 |
12 |
723723 |
3/8"-NC16 x 1-1/2"
hex head cap screw (only 7 used) |
11 |
1 |
723740 |
3/8"-NC16 x 1-1/2"
socket head cap screw (NOT USED) |
|
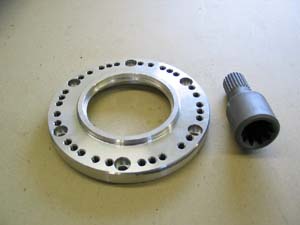 |
Now, just to
confuse things ever-so-slightly. This is a pic of the spacer adapter that
I used instead of the one that came with kit 50-9808.
The spacer adapter goes between
the Atlas-4SP and the tranny-to-Atlas adapter, for reasons we shall cover
shortly. The point to be made here is that you could use the spacer adapter
that comes with the kit (part no. 51-0404, identified as item #2 in the
preceding picture).
Or, as I discovered (with the
help of Vic at Advance Adapters!) you can substitute the spacer adapter pictured at left. It is part no. 51-8603 which normally comes with the "Jeep AX15 5 Speed to Jeep Dana 300 Transfer Case" adapter kit
(kit part no. 50-8603).
The advantages of using 51-8603
(left) instead of 51-0404 (above) is that it is 1/4" shorter and,
more importantly, has five (5) different bolt patterns drilled in it.
Since this goes between the tranny adapter and the Atlas it provides a
number of different clocking options that wouldn't otherwise be available.
This picture shows the side
that mates to the tranny adapter... |
|
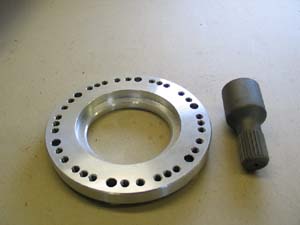 |
... and this is
the side that mates to the front of the Atlas-4SP. |
|
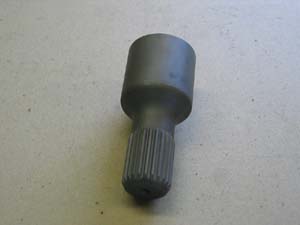 |
Close-up of part
no. 52-9700, the 10-spline internal x 23-spline external spud shaft that
connects the SM465's 10-spline output to the 23-spline input of the Atlas-4SP.
It is a "floating"
design, mounting between transmission and transfer case within the transmission
to Atlas adapter casting. |
|
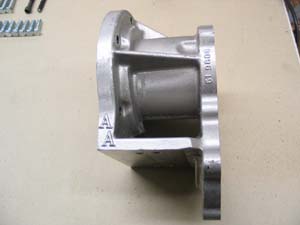 |
The next four
pics show the transmission-to-Atlas adapter, part number 51-9808.
It is cast aluminum, machine
finished, and measures 5.25" long.
In this pic the the transmission
would mount on the right, and the Atlas transfer case on the left. |
|
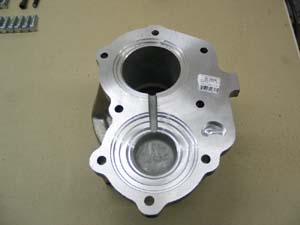 |
Transmission side
of the adapter - clearly showing the Chevy SM465 "figure-8" bolt
pattern. |
|
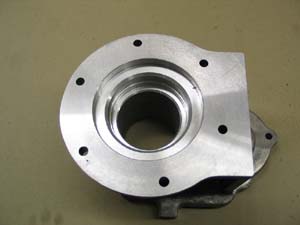 |
Atlas side of the
adapter. |
|
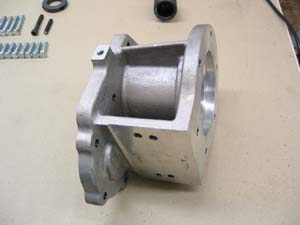 |
The adapter includes
a machined-flat bottom for mounting along with a threaded hole (red arrow)
that can be used for a "torque control arm" (more on this later).
As you can see in this picture,
the adapter's flat bottom has four pre-drilled and threaded holes
- doubtless useful for mounting in stock vehicles for which the part was
originally designed - i.e. for when it is used to swap an SM465 into a
Jeep.
The holes are 3/8"-NC16.
One pair are approximately 4.25" apart and the other 4-7/16"
apart.
I ended up not using either
and fabricated a different mount system as we shall see a little later. |
|
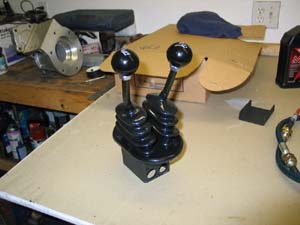 |
A first look at
the main case's twin-stick shifters. |
New vs. Old |
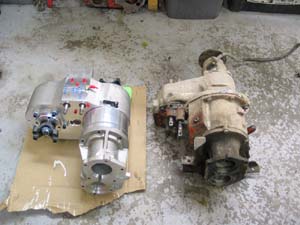 |
This next series
of four pics shows a comparison between the new Atlas-4SP and my old NP203/Dana
20 doubler.
The new Atlas-4SP is about
4" shorter, 70 lbs lighter, and provides a lowest gear ratio of 10.34:1
vice 4:1 for the doubler. |
|
 |
The Atlas weighs
128 lbs as pictured, the old doubler setup 198 lbs!!! |
|
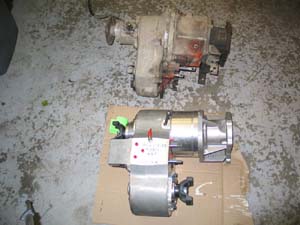 |
It's shinier too! |
|
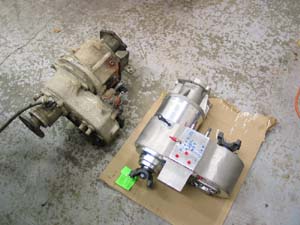 |
Despite being shorter
and lighter, comparing the relative sizes of the main cases gives some indication
of how much stronger the Atlas will be. Not to mention that the Atlas gears
are all helical-cut as opposed to those accursed spur-cut gears in the Dana
20. |
Installing
the Adapter |
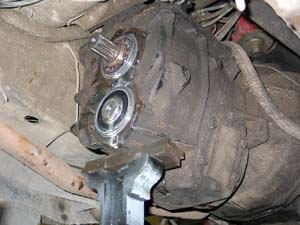 |
With the old
stock Chevy adapter removed, the back of the SM465 looks like this.
Make sure to give the mounting
surface a good cleaning. |
|
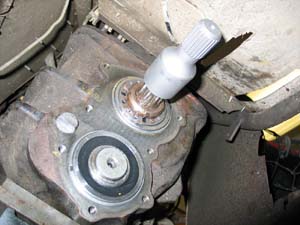 |
The 10 x 23 spud
shaft just slips on the SM465 output shaft.
The instructions from AA don't
mention it, but I smeared a good coating of lubricant inside the female
splines before slipping the spud shaft in place. I used good old Permatex
anti-seize - the gray"high temp" grease. I just feel that any
dry metal-to-metal contact should be avoided if possible and there isn't
a good technical reason to exclude lubricant. |
|
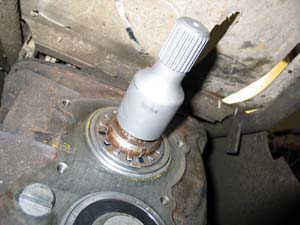 |
The spud shaft in
place on the transmission output shaft. |
|
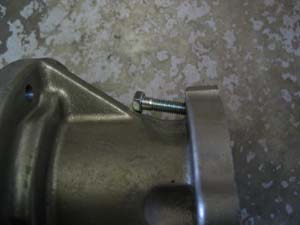 |
The adapter is
held in place with seven of the twelve 3/8"-NC16 x 1-1/2" hex
head cap screws (bolts) (pn 723723) and the 3/8"-NC16 x 2" stud
(pn 723711) with the 3/8"-NC16 hex nut (pn 723701).
Eight 3/8" lock washers
are also used (pn 723704)
This pic illustrates why the
stud is used. Due to the shape of the adapter, the top-most hole (the
one at "12 'o'clock" doesn't have sufficient clearance for a
bolt to be inserted. |
|
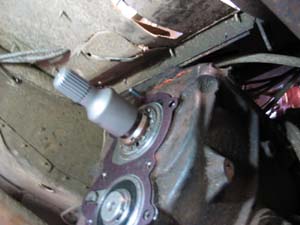 |
Instead, the
stud is inserted into the top-most hole first, before the adapter is fitted
in place. I used some blue Loctite thread-locker on the stud before installation,
as well as on all the bolt threads.
Before fitting the adapter
in place I also "glued" the gasket to the transmission using
Permatex spray-a-gasket sealant. |
|
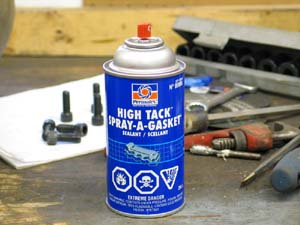 |
This is the stuff.
It's just a fancy spray adhesive for holding gaskets in place. |
|
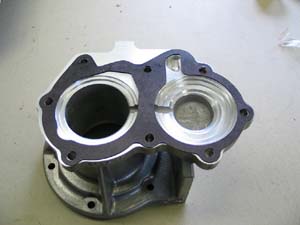 |
Alternatively you
could glue the gasket to the adapter before installation. |
|
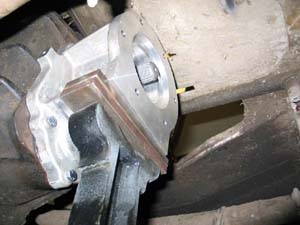 |
Fit the adapter
in place and secure with the remaining 7 bolts and lock-washers. Use blue
Loctite on the bolt threads and tighten to approx. 30 ft/lbs.
Don't forget to install the
nut on the stud, use a little Loctite on the threads, and also tighten
it to 30 ft/lbs. |
|
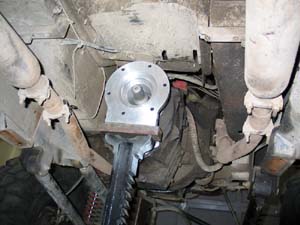 |
The installed adapter
looks like this. |
|
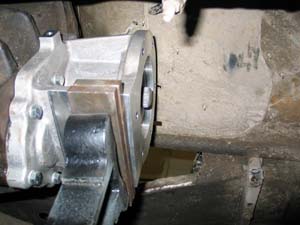 |
This picture
illustrates why the spacer adapter is required between the adapter and
the Atlas.
You can see that the tip of
the spud shaft protrudes just a fraction beyond the mounting face of the
adapter. The Atlas-4SP CAN NOT accept any kind of positive "stick-out"
like this. Installing the Atlas-4SP to any output shaft with positive
stick-out will cause the shaft to bottom out in the Atlas input and damage
the transfer case.
Many other transmissions and/or
adapters also have positive stick-out and, in most cases, any required
spacer adapter can be obtained free from AA when the Atlas is purchased. |
Preparing
the Atlas-4SP for installation
The Atlas-4SP is not shipped completely
ready to be installed. You must complete final assembly on the bench , and also
fill it with lubricant before installing it. It's also a good idea to test and
adjust the shifters before installation too.
The supplied instructions are quite
good in that they are thorough and cover everything. That said, they could certainly
use a little improvement as you actually have to jump back-and forth between
four different instruction books/sheets, and do so in a seemingly random order.
Also, most of the included pictures (and there aren't very many) are fairly
small, black&white, and quite fuzzy.
No matter - I will now outline for
you in complete detail (some might say painful detail!) every step of the process,
in order. Of course, it's entirely possible to do things successfully in a
different order - mine is not the only way (as my boss is fond of reminding
me!). However, if you proceed in this order at least you know you won't go wrong
or miss anything. I know this because along the way, as is my usual habit, I
pretty much screwed up anything and everything that could be screwed up - but
at least I can help you avoid any pitfalls. |
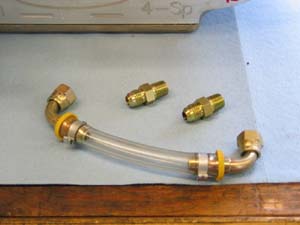 |
The first task
is to install the oil-level sight tube.
The tube itself comes crimped
onto two 90° AN-6 JIC swivel fittings, and there are two 1/4"
NPT to AN-6 male adapter fittings. On these fittings, the tapered threads
(to the right in this picture) are the NPT threads that thread into the
case.
It fits in place behind the
rear-cover of the front output shaft. |
|
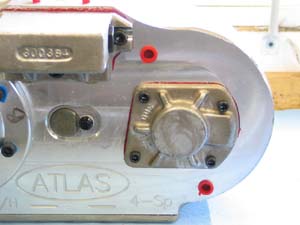 |
Remove the two small red dust-plugs
from the threaded holes. |
|
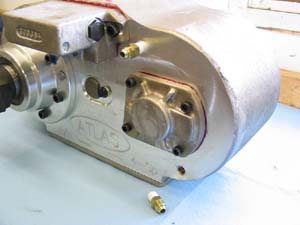 |
Tape the NPT threaded
ends of the adapter fittings with Teflon tape or coat with pipe sealant,
then thread them carefully into the case and tighten. |
|
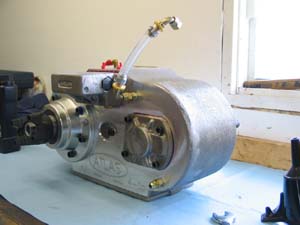 |
The swivel fittings
of the sight tube are then tightened in place on the adapters. No Teflon
tape nor pipe sealant is required nor should it be used on these JIC fittings.
Because the next task is to
fill the case with oil, and you do that through the upper sight tube fitting,
you actually want to attach just the lower fitting first, despite what
this picture shows. Remember what I said about cocking up anything and
everything possible along the way? I swear, it's a God-given talent of
mine! |
|
 |
The recommended
lubricant is the supplied Torco MTF. However, AA also recommend initially
using one of the alternate engine-oil lubricants for the first 500-mile
break-in of the transfer case.
I chose Castrol Syntec SAE
5W-50, but you can also use Valvoline Synthetic 20w-50 or Mobil 1 Synthetic
15w-50.
I will probably continue to
run the Castrol Syntec even after break-in as the Torco MTF isn't available
locally whereas the Castrol is available everywhere. Also, if I ever suffered
a partial lubricant loss, especially somewhere where the Torco MTF isn't
available, I'd rather not have to drain and flush the case before topping
up (mixing different lubricants isn't a good idea). If I stick with the
Castrol I'll be safe. |
How to fill the Atlas-4SP isn't completely
obvious. This actually raises one of the very few critique points I have for
the Atlas-4SP - it doesn't have a fill port, and the filling procedure is a
little unwieldy.
When you initially fill the case
with lubricant you do so by adding a specific amount of lubricant, rather than
the more traditional method of filling a case to a specific point (usually until
oil flows from the fill port.) This is because the Atlas has no fill port, and
instead uses a sight-tube for proper oil-level verification. However, since
the case can be installed at many different angles (rotations), and each rotation
will cause the oil in the sight tube to sit at a different level, it's not possible
for the sigh tube to be marked for correct level at the factory.
Instead, you fill the case with the
exact amount of lubricant required, install the case at the chosen rotation,
and THEN mark the proper level on the sight tube for later visual verification
of proper oil level. More on this later - for now we need to get 2.5 qts (2.36
L) of oil into the case and then tip it on it's front to ensure the lubricant
flows into the reduction box. |
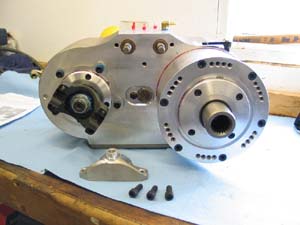 |
Because you need to tip the
case onto its front after filling (or fill it while it's on its front)
the first thing you need to do is install the twin-stick base mount because
the mounting holes pass through into the case and if the bolts aren't
installed oil can leak out of them. This would be a particular nuisance
because we're adding a specific volume of oil in order to establish the
right level on the sight tube. If you were to begin filling the case with
the carefully measured 2.36 liters of fluid only to find some has leaked
out during the process you pretty much have to drain the case, re-measure
2.36 liters and start again. Imagine how I know this!
The twin-stick base mount (pn
302051) along with its three 3/8"-NC16 x 1" socket head cap
screws (pn 723731) are shown in the foreground of this picture. |
|
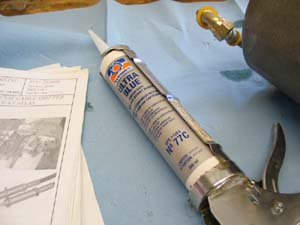 |
Because the mounting
holes pass through into the case the mounting screws must have a little
RTV sealant applied to their threads prior to installation. I used Permatex
Ultra Blue. |
|
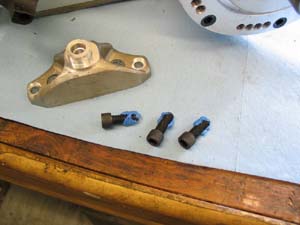 |
Apply a dab of blue
RTV to the threads of the mounting screws. |
|
 |
Slide the twin-stick
base mount over the shift rails, install the mounting screws, and tighten. |
You can now fill the case with the
required lubricant.
There is a note on oil filling towards
the end of the planetary box cable shifter instruction sheet that reads: "After
installing the sight tube per the instructions in the Atlas manual, add 2-1/2
quarts of included oil while still on the bench. After adding oil and before
installing transfer case into vehicle, tip the transfer case onto the input
shaft so that the rear yoke points straight up. This establishes the correct
amount of oil in the planetary's separate reservoir"
Note that this instruction says to
fill with "included oil" which actually contradicts point 12 on page
2 of the "Atlas Transfer Case" instruction sheet which says to use
an alternate motor-oil for the initial 500 mile break-in procedure. I assumed
that the latter was correct. In any case, I chose to just fill the case while
on its front. |
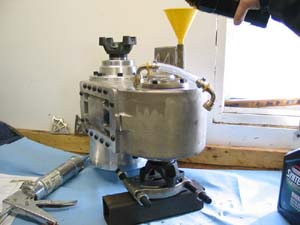 |
Stand the case
on its front so the rear output shaft points straight up as shown in the
pic and block it in place.
In order to fill it I disconnected
the upper end of the sight tube and installed a short length of rubber
tube connected to a funnel with a small-diameter neck over the fitting
in the case. Add the correct volume of oil. |
|
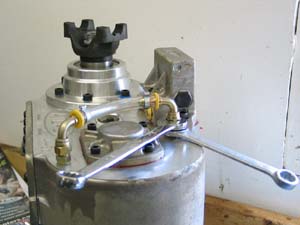 |
Once the case has
been filled, re-attach and tighten the sight-tube fittings. Be sure to hold
the adapter fitting with a wrench while tightening the swivel fitting, as
shown. |
|
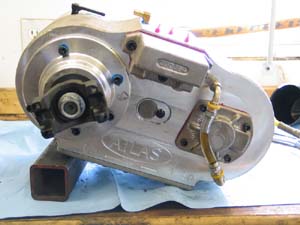 |
Here the case is
filled and is being tilted to simulate different installed rotations to
illustrate how this affects the level of the oil in the sight tube. |
|
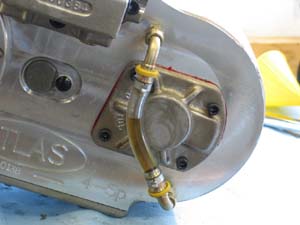 |
In this pic the
case is simulating being installed at a fairly large angle, and you can
see the level of the oil is quite high in the tube. |
|
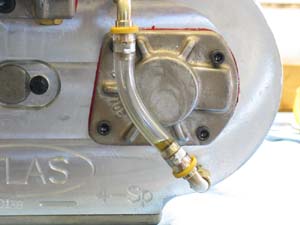 |
At the other
extreme, if you were to install the case clocked perfectly flat you can
see that the oil level barely shows in the sight tube.
When the case is installed
in the vehicle a permanent marker or small zip-tie will be used to mark
the "full" level on the sight tube. |
With the case filled and the sight
tube installed, it's time to complete the installation of the twin-stick cable
shifters and bench test / adjust the shifters. This would be equally true if
you were using manual shifters as opposed to cable shifters. |
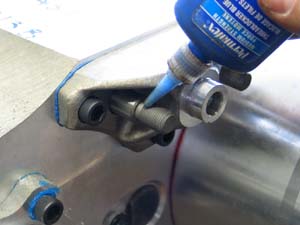 |
Apply a little thread
locker to the threads of the shift rails... |
|
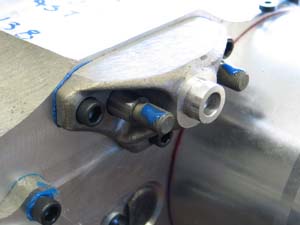 |
...like so. |
|
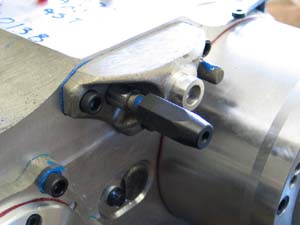 |
Thread the shift
rail adapters (pn 303306) on the shift rails and tighten. |
|
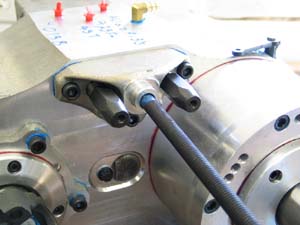 |
Apply a little thread
locker to the end of the 1/2"-NC13 all-thread (pn 302080) and thread
it completely into the twin-stick base mount. |
|
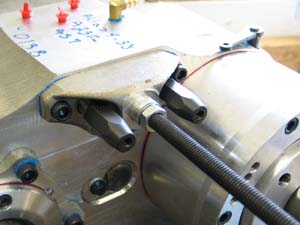 |
Install the 1/2"
star washer (pn 302075) and 1/2"-NC13 jam nut (pn 303121) on the all-thread... |
|
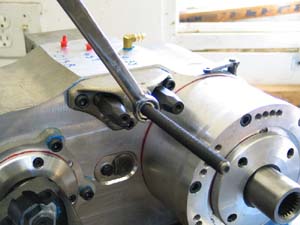 |
... and tighten
the jam nut securely against the base mount. |
|
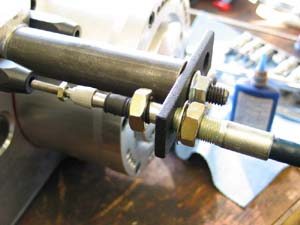 |
Slide the extension
tube (pn 303308) and extension tube bracket (pn 303307) over the all-thread
and tighten in place with the 1/2"-NC13 serrated locknut (pn 303120).
Make sure the tube butts completely
up to the case and hold the extension tube bracket level when you tighten
the locknut. |
|
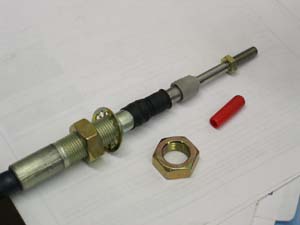 |
Remove the red
plastic end-cap and one jam nut from the end of the shift cable (pn 303309)
- it doesn't matter which end, they are the same.
Thread the remaining jam nut
towards the long end of the cable, just past half-way on the threads... |
|
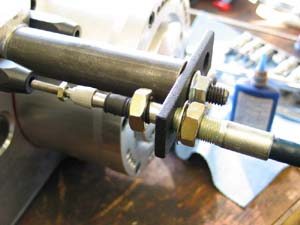 |
... so that when
you install the cable in the bracket it's approximately in the middle
of its range.
Insert the cable through the
hole in the extension tube bracket, then slide the other jam nut back
over the cable.
Sandwich the bracket between
the two jam nuts by tightening them against one another. |
|
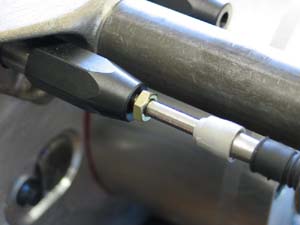 |
Thread the shift
cable's inner rod completely into the shift rail adapter, then tighten the
locknut. |
|
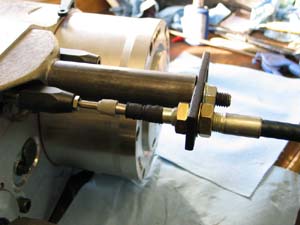 |
The completely installed
cable should look like this. |
|
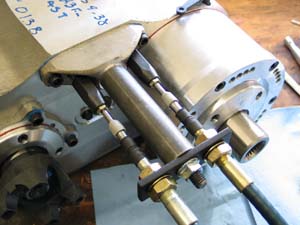 |
Repeat for the other
cable until you have this. |
|
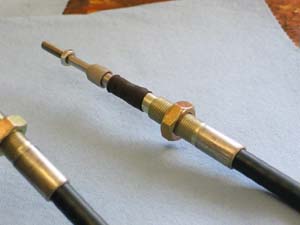 |
At the other
end of the cables (the shifter ends), remove the red plastic end-cap,
one jam nut, and the lock washer and discard.
Thread the remaining jam nuts
to about halfway along the threads. |
|
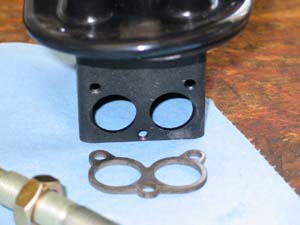 |
Note that the barrel
retainer plate (pn 303303) (the silver part in the foreground) only bolts
to the shifter body (pn 303301) one way. |
|
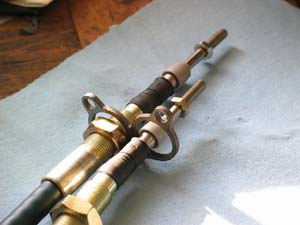 |
Slide the barrel
retainer plate over the ends of both cables... |
|
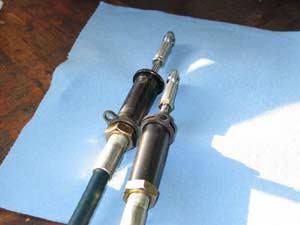 |
... then thread
the cable barrels onto the threads of the shift cables. |
|
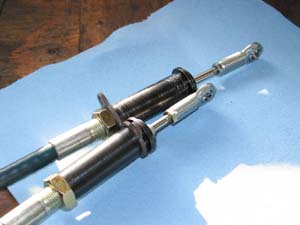 |
Thread the 1/4"
female Heim joints (pn 303313) completely onto the shift cables' inner rods
and tighten the jam nuts. |
|
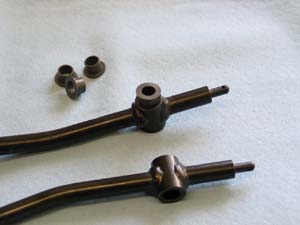 |
Using a mallet,
tap the shifter handle pivot bushings (pn 303312) into the shifter handles
(pn 303304). |
|
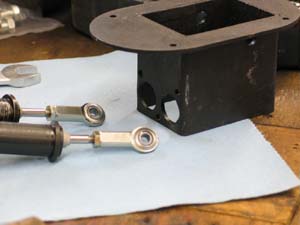 |
Insert the cables
through the holes in the back of the shifter body... |
|
 |
... and into the
shifter body. |
|
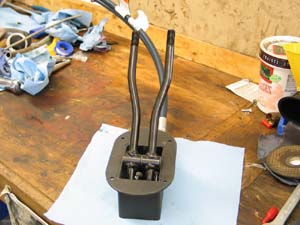 |
Orient the shifter
handles so that they bend away from each other and fit the handles into
shifter body through the top. |
|
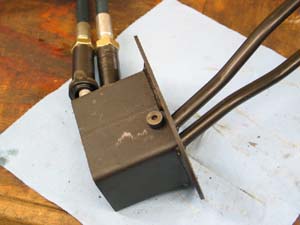 |
Insert the pivot
shoulder bolt (pn 303310) through the shifter body and the shifter handle
bushings... |
|
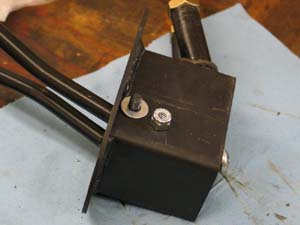 |
... and secure with
the 1/4" flat washer (pn 722523) and 5/16"-18 locknut (pn 723141). |
|
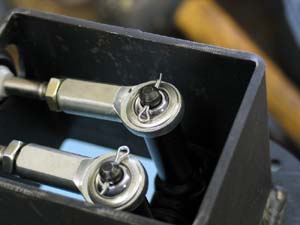 |
Slide the Heim
joints over the ends of the shifter handles and insert the cotter pins
(pn 920026).
Do not bend out the legs of
the cotter pins yet - you will have to disassemble the shifter handles
to install in the vehicle. |
|
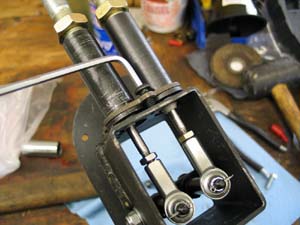 |
Slide the cable
barrel retainer plate up against the flanges on the cable barrels and fasten
it to the shifter body with three 1/4"-NC20 x 5/8" button head
cap screws (pn FJ4544). |
|
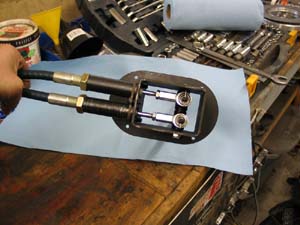 |
When you're done
it should look like this. |
|
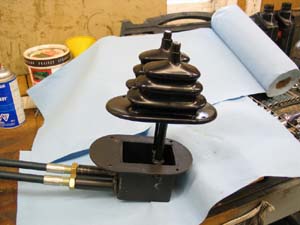 |
The next step is
to test and adjust the cable shifters. You don't really need to install
the shift boot to do this but I test-fitted it at this time anyway. |
|
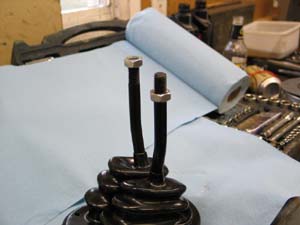 |
It does make the
testing a little easier if you install the 1/2"-NC13 jam nuts (pn 303121)... |
|
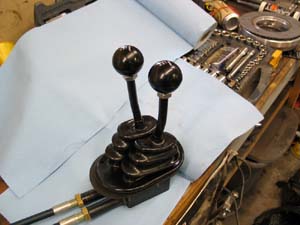 |
... and then
the shift knobs.
Looking at the shifter body
from the end where the cables enter, the left stick shifts the front axle
and the right stick shifts the rear axle. |
Testing and
Adjusting the Cable Shifters |
 |
Before beginning
the shift test and cable adjustment procedure, it's a good idea to back
off the shift-rail detent set-screws a quarter turn. They are the large
brass set-screws located on the underside of the back of the shift-rail
housing - illustrated here by the red arrows. This will allow for easier
initial shifting.
As the Atlas is operated and
breaks-in, the shift detent components will seat and the set-screws can
be re-tightened to their original position. |
The next series of 3 pics illustrate
the gear positions of the Atlas-4SP in terms of the position of the shift rails.
The left rail (left and right relative to the vehicle when installed) is the rear axle and the right rail is the front axle. The pics
are of the right (front axle) rail. The position of the shift rail is best illustrated
by examining the position of the shift rail adapter (the black hexagonal part)
in relation to the twin-stick base mount. |
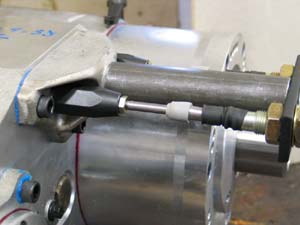 |
This is the "low-range"
position.
In this position the shift
rail is retracted into the case, and there is virtually no gap between
the shift rail adapter and the base mount.
This correlates to a shifter-handle
position of "away from the cables"
Assuming the shift cables run in a straight line to the shifter body, this would correlate to the shift lever
in the "front" or "forward" position. |
|
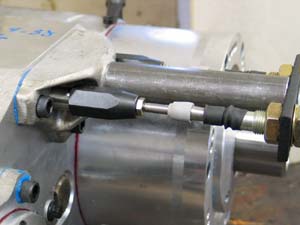 |
This is the "neutral"
position.
In this position the shift
rail is extended mid-way out of the case, and there is a gap between the
shift rail adapter and the base mount. About half an inch of shiny shift
rail is visible between the shift rail adapter and the base mount.
This correlates to a shifter-handle
position of "in the middle of the throw"
Assuming the shift cables run in a straight line to the shifter body, this would correlate to the shift lever
in the "middle" position. |
|
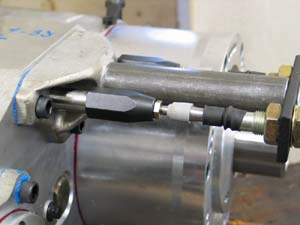 |
This is the "high-range"
position.
In this position the shift
rail is extended all the way out of the case, and there is a bigger gap
between the shift rail adapter and the base mount. About an inch of shiny
shift rail is visible between the shift rail adapter and the base mount.
This correlates to a shifter-handle
position of "towards the cables"
Assuming the shift cables run in a straight line to the shifter body, this would correlate to the shift lever
in the "back" or "rear" position. |
|
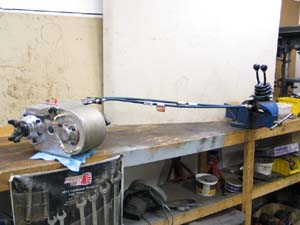 |
Now that we know
what the shift positions are, we can set up the case and shifters on the
bench to test and adjust the shifts.
I set the case on the bench,
stretched the cables out straight away from the case and clamped the shifter
body in a vice so I could operate the shifters. |
|
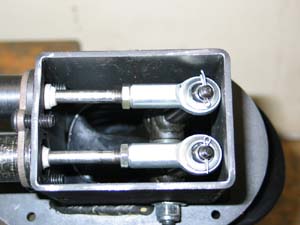 |
Essentially,
what we want to check (and adjust to achieve if necessary) is that the
throw of the shifters achieves a complete, positive shift, from L to N
to H, without any interference between the Heim joints and the inside
of the shifter body.
Here we can see that on my
initial setup (the jam nuts about halfway on the threads at both ends
of the cables) the Heim joints contact the front of the shifter body when
the levers are to the rear - i.e. when shifted to "High".
The other possible condition
would be that, with the shifters in the "Low" position, the
little jam nuts on the cable rod would bottom on the shifter body.
In extreme cases, there may
be interference early enough in the shifters travel to actually prevent
a complete shift. Regardless, the solution is to adjust the cables so
that the shifter throw is limited only by the completion of the shift,
with no interference inside the shifter body. |
You can make adjustments either at
the transfer case or at the shifter body - both achieve the same thing. Essentially,
what you are adjusting is the relationship of the cable's sheath to the cable's
inner rod (the rod that does the actual shifting)
The adjustments you want to make
are:
If the Heims hit the front of the
shifter body / the case won't shift into High:
- You need to move the sheath towards the case
If the Heims/jam nuts bottom on the
back inside of the shifter body / the case won't shift into Low:
- You need to move the sheath towards the shifters. |
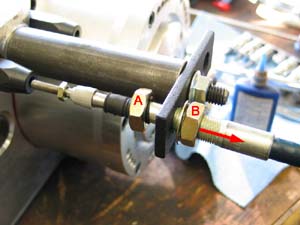 |
At the transfer
case end:
To move the sheath towards
the case:
- Loosen the inner jam
nut (A)
- Thread the outer jam nut (B) further onto the cable (in the direction
of the red arrow).
- Push the cable further into the extension tube bracket until the
outer jam nut (B) bottoms.
- Thread the inner jam nut (A) back up against the bracket
- Re-tighten the jam nuts.
To move the sheath towards the shifters use the same procedure except thread the outer jam nut towards the end of the cable (opposite to the direction indicated by the red arrow). |
Adjustment at the shifter end is
only slightly more complicated. |
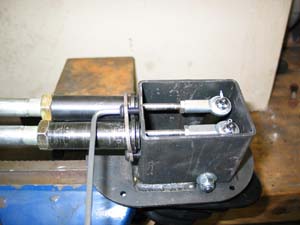 |
First loosen
the button-head cap screws holding the barrel retainer plate to the shifter
body.
It is not necessary to remove
them - just loosen them enough to allow the cable barrels to rotate in
the barrel retainer plate. |
|
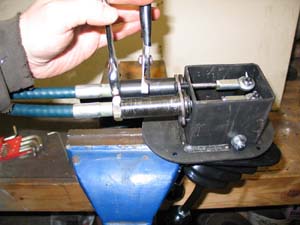 |
Hold the barrel
with a pair of channel-lock pliers and loosen the lock nut. |
|
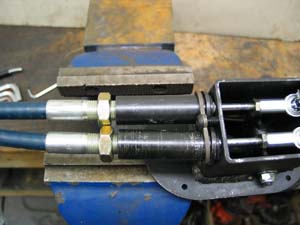 |
To move the sheath
towards the case:
- Back the nut off and thread
it further onto the cable
- Thread the barrel further onto the cable until it bottoms on the nut
- Push the shifter body back up against the cable barrels and re-tighten
the cap screws
To move the sheath towards
the shifters :
- Back the jam nut off
- Thread the barrel away from the cable
- Tighten the jam nut up against the barrel
- Push the shifter body back up against the cable barrels and re-tighten
the cap screws
|
The following two pictures illustrate
the results of my final adjustment. |
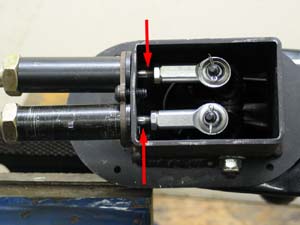 |
With the shifters
in "Low", and the levers forward, there is plenty of clearance
between jam nuts and shifter body, illustrated by the red arrows. |
|
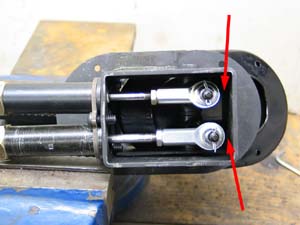 |
With the shifters
in "High", and the levers to the rear, there is plenty of clearance
between the Heim joints and the shifter body, illustrated by the red arrows.
Obviously, you want to have
both cables, front and rear axles, adjusted approximately the same so
the two levers are not way out of synch. |
|
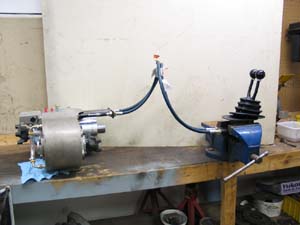 |
While I was adjusting
the cables, I decided to test the minimum bend radius of the shift cables.
That is - I wanted to see how
tightly they could be bent and still deliver a nice, smooth, positive
shift.
I was pretty amazed at the
results. |
|
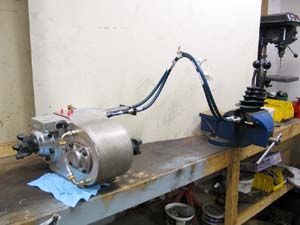 |
You can actually bend them
in more than one plane and they still shift just as well as when they
are straight. |
|
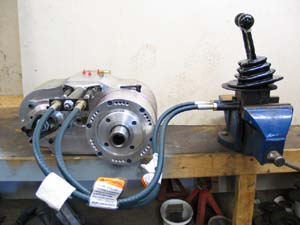 |
As long as you
don't actually kink the cables you can achieve some pretty tight bend
radii and the shift is still smooth and positive.
I was really quite impressed
with the results. |
|
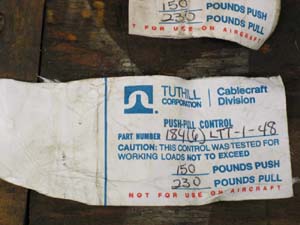 |
For interest's sake,
here is the label from the cable. All three cables for the Atlas-4SP are
the same part. |
Preparing
the Reduction Box Cable Shifter |
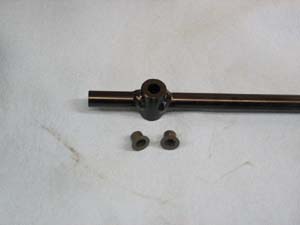 |
The last thing
to do before test-fitting the case into the vehicle is to assemble and
adjust/test the shifter for the reduction box.
Begin by tapping the bushings
(pn 340612) into the shifter handle (pn 340611) using a mallet. |
|
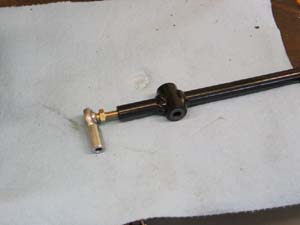 |
Thread the 1/4"-NF28
ball joint (pn 340613) into the handle and tighten. |
|
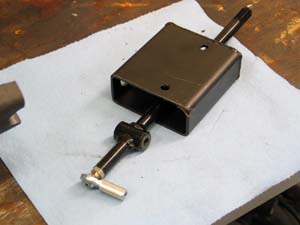 |
Slide the handle
up through the bottom of the shifter housing (pn 340600). |
|
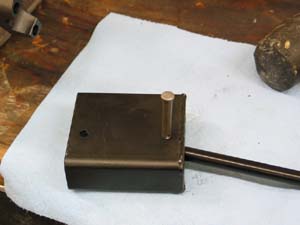 |
Align the handle's
through-hole (with the bushings in it) with the top-most hole of the shifter
housing, and insert the clevis pin (pn 340614)... |
|
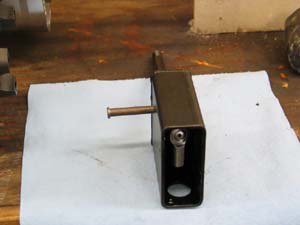 |
...like this. |
|
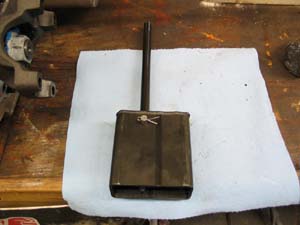 |
Insert the cotter
pin (pn 340616) through the clevis pin and spread the legs - unlike the
twin-stick shifters you will not have to remove it later for installation
into the vehicle. |
|
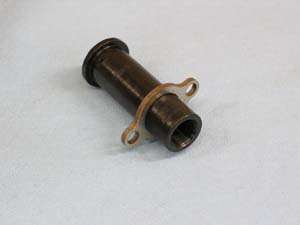 |
Slide the barrel
retainer (pn 340610) over the cable barrel (pn 303305) like this. |
|
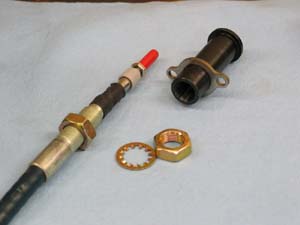 |
Remove the first
jam nut and star washer from the cable and thread the remaining jam nut
about halfway along the cable's threads, as shown. |
|
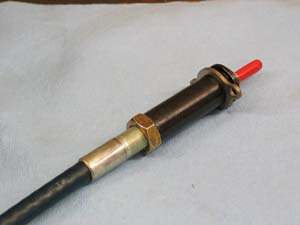 |
Thread the cable
barrel onto the cable until it bottoms against the jam nut. |
|
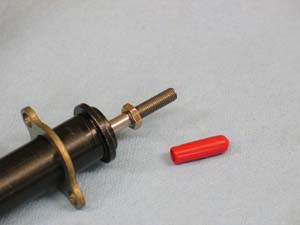 |
Remove the red plastic
dust cap from the end of the shift rod and thread the small 1/4"-NF28
jam nut completely on the rod. |
|
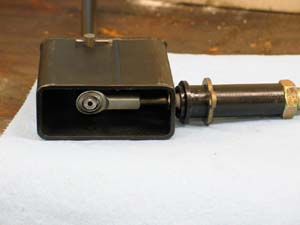 |
Insert the cable
through the hole at the back of the shifter housing and thread the rod into
the 1/4"-NF28 ball joint. |
|
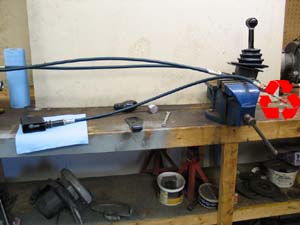 |
By grasping the
other end of the inner shift rod and turning (as shown), thread the shift
rod completely into the 1/4"-NF28 ball joint. |
|
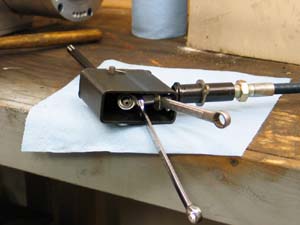 |
When the rod bottoms
inside the ball joint, tighten the jam nut to lock it in place. Be sure
to use a wrench to hold the body of the ball joint when tightening the jam
nut to avoid placing undue stress on the socket of the ball joint. |
|
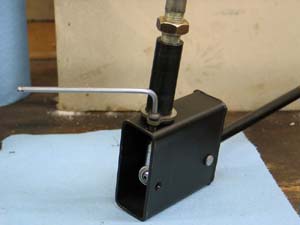 |
Seat the barrel
against the shifter housing and secure in place with the barrel retainer,
using the two 1/4"-NC20 x 5/8" button head cap screws (pn 340615). |
|
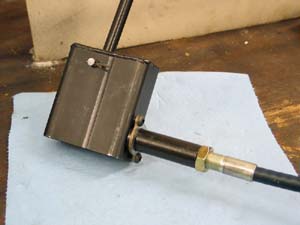 |
The completed shifter
assembly should look like this. |
|
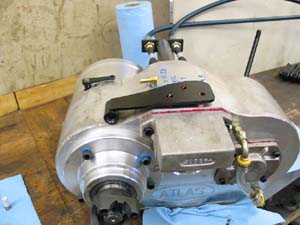 |
The next step
is to connect the other end of the cable to the Atlas.
This pic shows the placement
and orientation of the cable shifter bracket (pn 340517-R). |
|
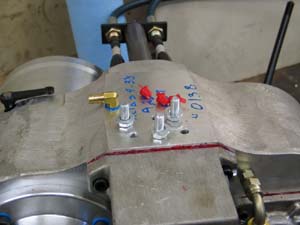 |
Remove the red
plastic dust plugs from the three holes on the top of the case and prepare
the three 3/8"-NC16 x 3/4" bracket mounting bolts (pn 723720)
and flat washers (pn 720015).
Place a dab of blue RTV on
the threads of the bracket mounting bolts to seal them as they pass through
into the case. |
|
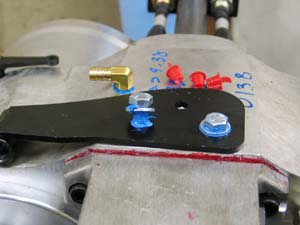 |
Fasten the bracket
to the case with the three bolts. Torque the bolts to 15-18 ft/lbs. |
|
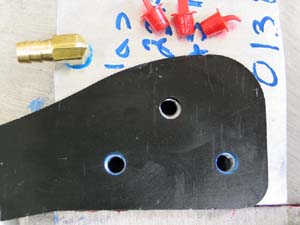 |
One of the very
few problems I had during the project was the fact that the holes in the
bracket didn't quite line up with the holes in the case, preventing all
three bolts from being able to be installed.
To remedy this I drilled out
the misaligned hole in the bracket until I could insert and tighten all
three bolts. |
|
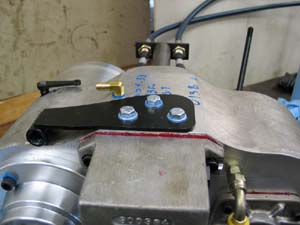 |
The installed bracket
should look like this. |
|
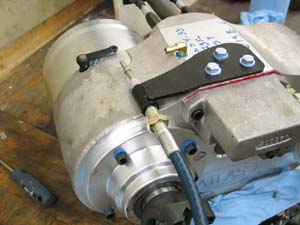 |
Remove red plastic
dust cap, the first jam nut, and the star washer from the free end of
the cable.
Thread the remaining jam nut
about halfway along the cable's threads then thread the cable into the
bracket by turning the whole shifter/cable assembly... |
|
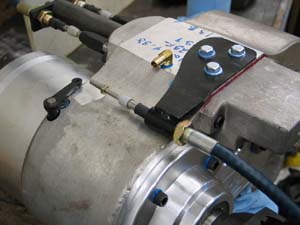 |
... until the jam
nut bottoms on the bracket. |
|
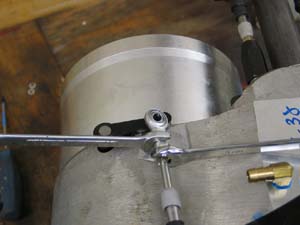 |
Thread the 1/4"-NF28
female Heim joint (pn 303313) completely onto the shift rod until it bottoms
out.
Align the Heim joint so that
the bore in the spherical bearing is centered in the race and vertical,
then hold the Heim joint in place with a wrench and tighten the jam nut. |
|
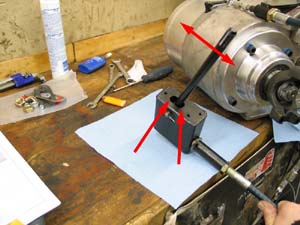 |
Hold the shifter
housing upright and move the stick through its full range of motion.
Check that there is no interference
between the stick and the housing where the stick passes through the oval
slot (red arrows) and ... |
|
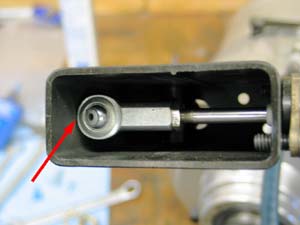 |
... that there
is no interference between the ball joint and the inside of the shifter
housing.
If there is any interference,
loosen the button head cap screws and the large jam nut on the cable.
Rotate the barrel independently to adjust the shift handle / ball joint
position. Recheck for interference and continue adjusting the barrel as
necessary. Once you are satisfied with the adjustment, securely re-tighten
the jam nut and button head cap screws. |
It is now time to adjust the reduction
box shift cable at the transfer case end to ensure that the range of motion
of the pivot lever (the mechanical arm on the case that shifts the reduction
box) falls entirely within the range of motion of the cable. |
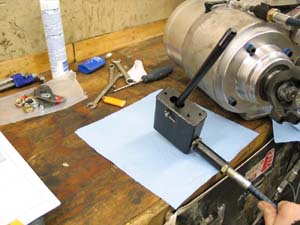 |
Recall that when
the shifter is aft (back towards the cable) this is the Low Range position
and when it is fwd (away from the cable) it is in the High Range position.
In this pic the shifter is
in Low Range position. |
|
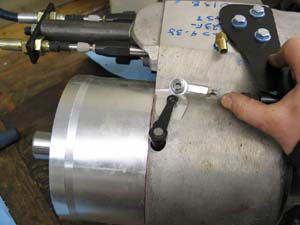 |
The pivot lever
on the case, just behind the planetary reduction box, moves fore and aft
to mechanically shift the reduction box.
When it is aft (towards the
back of the transfer case) the reduction box is in Low Range - as in this
pic. |
|
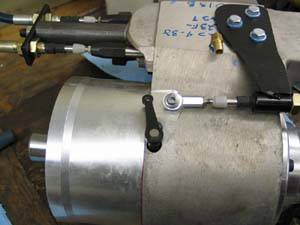 |
When it is forward
(towards the front of the transfer case) the reduction box is in High
Range - as in this pic. |
|
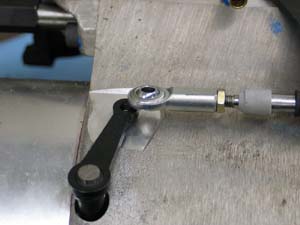 |
To begin the
adjustment, place the shifter in Low Range and move the pivot lever to
the Low Range position. Adjust the cable so that the bore in the Heim
joint is behind (more to the rear of the case than) the tapped hole in
the pivot lever by threading the cable/shifter assembly into or out of
the cable shifter bracket. |
|
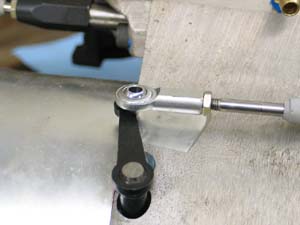 |
Move the shifter
and the pivot lever to the High Range position. Check that bore in the
Heim joint is forward of the tapped hole in the pivot lever.
In this picture you can see
that it is not, and so further adjustment is required.
Adjust the cable so that the
bore in the Heim joint is forward of the tapped hole in the pivot lever
by threading the cable/shifter assembly into or out of the cable shifter
bracket, as before. |
|
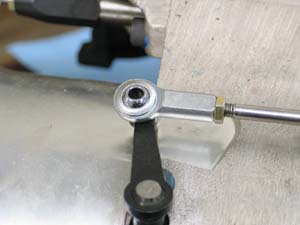 |
In this pic I have
threaded the cable into the bracket to move the Heim joint ahead. It is
now slightly forward of the tapped hole in the pivot lever as it should
be. |
|
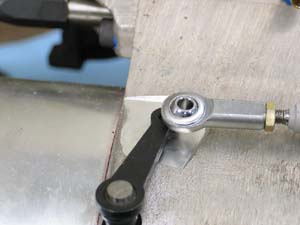 |
Move the shifter
and the pivot lever back to the Low Range position and double-check that,
in Low Range, the Heim joint is still behind the tapped hole in the pivot
lever.
In this case it is, so adjustment
is complete.
If it is not, you will have
to continue to fine tune the adjustment by threading the cable/shifter
assembly into or out of the cable shifter bracket until the pivot lever
travel is centered within the cable travel. |
|
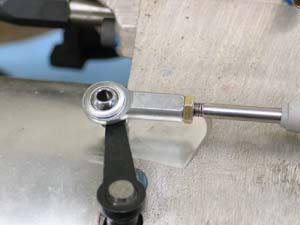 |
Final adjustment
position - High Range. |
|
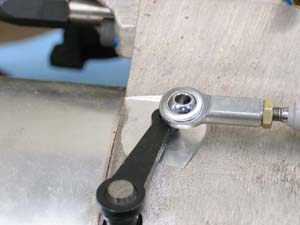 |
Final adjustment
position - Low Range. |
|
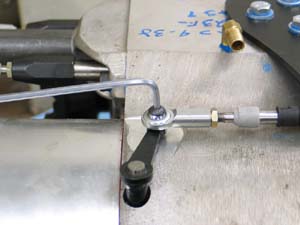 |
Attach the Heim
joint to the pivot lever using the 1/4"-NC20 x 5/8" button head
cap screw (pn 340615). |
|
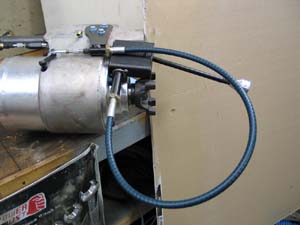 |
The reduction box
cable shifter is capable of the same impressive bend radii as the twin-stick
shifters while still providing a solid shift. |
Installing
the Adapter-Spacer Ring
In my installation, the final step
before test-fitting the Atlas into the vehicle was to install the adapter spacer.
This was required to ensure the 10 x 23 SM465 to Atlas spud shaft does not bottom
inside the Atlas input. As it turns out, because of the part I used as the spacer,
I also gained several clocking angles (a clocking angle is the rotation at which
the transfer case is installed - i.e. how much below the input the front output
hangs). |
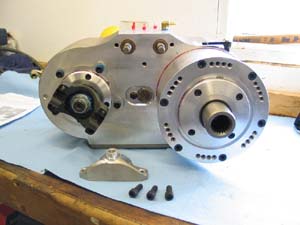 |
The front of
the Atlas-4SP's reduction box is equipped with four different spacings
of the 6-bolt round pattern. This alone would offer you four different
clocking angles, however many Advance Adapters' adapters will also have
more than one bolt pattern, meaning that eight clocking options are often
available.
Typical clocking options might
be:
Left drop case: 7, 14, 17,
21, 24, 28, 31, or 38 degrees.
Right drop case: 4, 11, 14,
18, 21, 25, 28, or 35 degrees. |
|
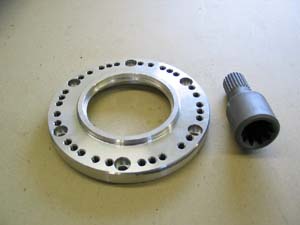 |
In my application,
because the adapter spacer itself has five different spacings, and it can
be bolted to any of the four spacings on the Atlas I have a "theoretical"
total of 5x4= 20 different clocking options.
In reality, not every combination
ends up being different, in fact, many are the same but at the very least
I had 5 or 10 different options. In my case I wanted the case to be clocked
fairly flat for clearance, but without causing too many clearance problems
with frame, floor, etc. The next section details test-fitting the case
at different clocking angles and selecting the best fit.
The many different transmission
and adapter combinations that can be used with the Atlas-4SP mean that
there are far too many possibilities to cover here - the best bet is to
do some research in the Atlas Transfer Case
Installation Guide which details many combinations and options, and
then talk to one of the techs at Advance. |
|
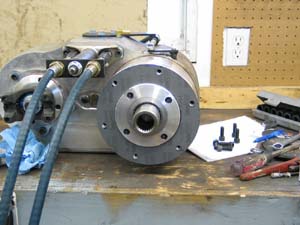 |
If you're using
a spacer adapter like I did, first install one of the 6-bolt round gaskets
on the face of the reduction box. |
|
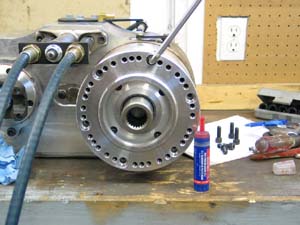 |
Fit the spacer adapter
in place and install with the six socket-head cap screws. |
|
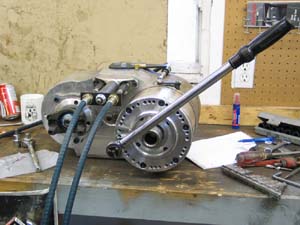 |
Torque them to 28-30
ft/lbs. |
The Atlas-4SP is now assembled, lubed,
and ready for test-fitting into the vehicle.
Test-fitting
the Atlas-4SP and Clocking Options
In this phase we will install the
case temporarily in place, experiment with various clocking angles and check
clearances. |
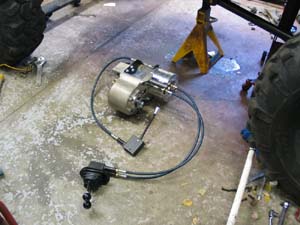 |
Here's the completely
assembled unit ready for installation. |
|
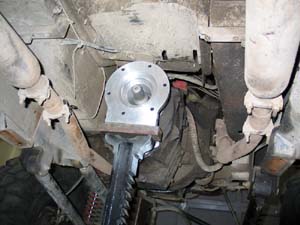 |
And here is the
tunnel where it will be installed.
Before you hoist it into place
it's a good idea to spend some time with the tape measure doing some preliminary
clearance checks - once you get it up into place and ready to slide onto
the splines it's pretty heavy and a little cumbersome and that's not the
time to find out the exhaust is in the way.
Remove any offending components,
place the transmission in neutral, and fit the case onto the adapter.
The use of a proper transmission jack is highly recommended. I have intentionally
omitted pictures of my old-drywall-compound-pail-couple-of-4x4s-and-wobbly-floor-jack
method! |
|
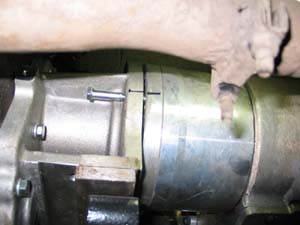 |
With the case
in place, leave a tiny gap between the face of the adapter and the mounting
face of the case so that you can just see the bolt holes in the mounting
face of the case.
Tilt / rotate the case around
the input shaft while fishing a bolt through from the front of the adapter,
through one of the mounting holes in the adapter, until you get it engaged
in one of the threaded holes in the case. |
|
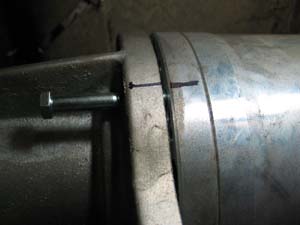 |
Mark this position
on both the adapter and the case (as shown by the black marker lines in
pic at left) - this you can now use as an alignment reference mark. |
|
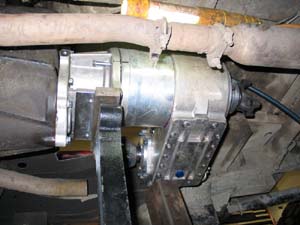 |
Slightly different
view of the process. |
|
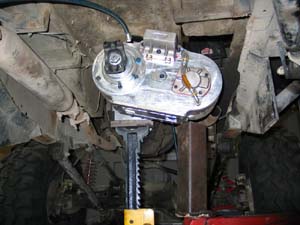 |
You can now rotate
the case to different "clocking angles' and check for clearances
etc. in order to determine your preferred clocking angle.
I used a floor jack and piece
of square tube to support the right side of the case in different positions
as I checked.
This is the view from the rear
with the case clocked at 11°. |
|
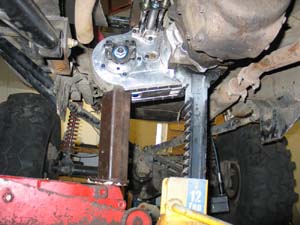 |
View from the
front at 11°.
At 11° I measured 28-7/16”
clearance between the floor and the lowest part of the case. |
|
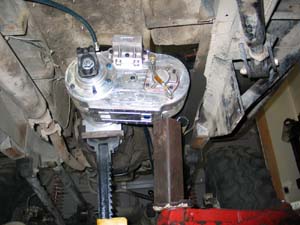 |
The next hole
in the pattern on the front of the case allowed me to clock the case to
5°.
This is the view from the rear
at 5°. |
|
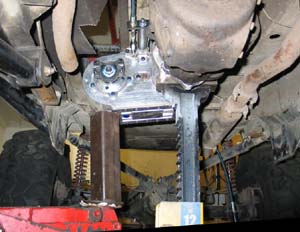 |
View from the
front at 5°.
At 5° I measured 29-7/16”
clearance between the floor and the lowest part of the case.
In other words, I gained a
whole inch of clearance.
It was a tighter fit at 5°
than at 11° (in the pic at left you can see where I had to cut the
exhaust) but I settled on 5° for the improved ground clearance. |
|
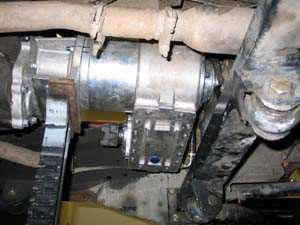 |
Side view at 5°.
You can see the alignment marks I made at both 5° and 11°. |
Installing
the Atlas-4SP
Once you have your desired clocking
angle figured out and marked, it's time to remove the case and prep it for final
installation into the vehicle. |
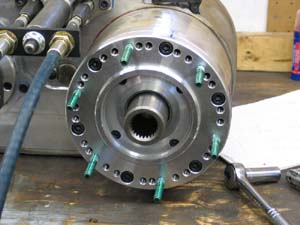 |
Using the alignment
marks made during the test-fitting procedure, install the six Atlas Mounting
Studs (pn 302069) finger tight into the mounting face of the Atlas / Adapter
Spacer (as applicable).
Thread in each one, inserting
the end that has the pre-applied thread locking compound.
Make sure you get each one
in the correct position relative to its neighbors (i.e. that there are
the same number of holes between each pair).
You can always slip on the
gasket to check before tightening them. |
|
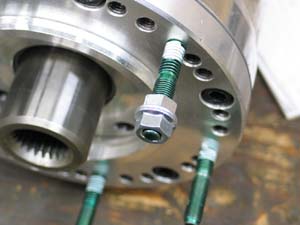 |
The studs are
a special tapered-fit aluminum design and so must be installed carefully
and tightened securely without over tightening.
Getting them properly seated
and tightened is a bit of a trick. The procedure I used is as follows:
First I threaded on two nuts
back-to-back... |
|
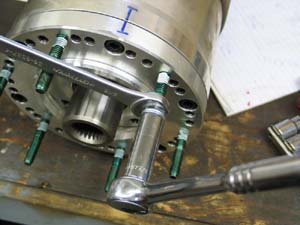 |
Then with a wrench
on the inner nut to keep the outer nut from turning I used a socket on
the outer nut to turn the stud into its hole.
It's a bit tricky as you have
to hold the inner nut fast against the outer while rotating the whole
assembly together but you will soon get the hang of it. |
|
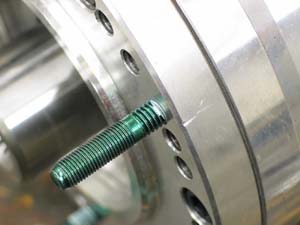 |
Without a depth
gauge, spec, or torque measurement given, and the instruction manual providing
only a caution to "not over-seat the studs into the front of the case."
it was a matter of professional estimation (aka wild-ass guess) as to how
deep to install the studs. I chose to tighten them just to the end of the
thread locker as shown. |
|
 |
This pic shows an
approximation of how deep they are seated when so installed. |
|
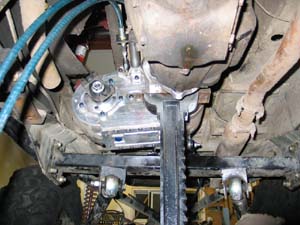 |
Install the case
into the vehicle, sliding the input over the splines of the output shaft
and inserting the six mounting studs through their holes on the adapter.
Apply pressure from the rear
of the case until the mating face of the adapter and case are together
with no gap. Do not use the fasteners to draw the components together
- if they do not readily mate without a gap, disassemble and investigate
the cause of any interference. Make particularly sure that the transmission
output shaft / stub shaft is not bottoming inside the Atlas input. |
|
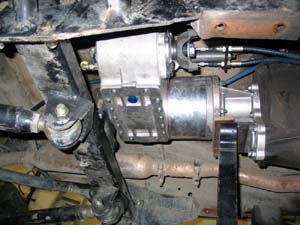 |
With everything
in place, and using a little Loctite thread locker, install the nuts on
each of the studs and tighten to 26-28 ft/lbs. |
|
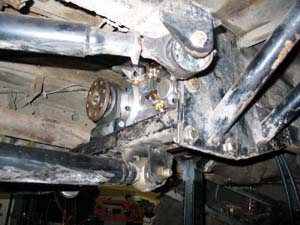 |
With the Atlas
securely in place at your chosen rotation, it's time to mark the correct
oil level on the sight tube.
I first drew a line with a
permanent marker, and then attached a small zip tie to mark the level
of the oil within the sight tube. |
Installing
the Cable Shifters in the Vehicle |
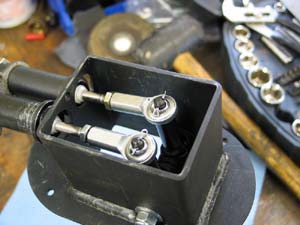 |
With the case
in place, it's time to install the shifters.
The single-stick shifter for
the reduction box installs from under the rig and so can remain attached
to its cable.
On the other hand, the twin-stick
assembly is installed down through the floor and so must be removed from
the cables for installation.
Pull the cotter pins (remember
I said not to spread the legs earlier!) and slip the Heim joints off the
shifters, then remove the cap screws securing the barrel retainer plate
to the shifter body. Remove the cables from the shifter body and keep
the cotter pins and cap screws handy. |
|
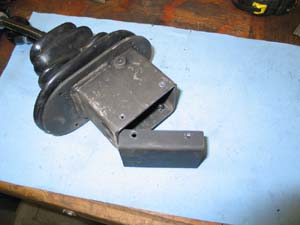 |
The instructions
state that the shifter body bottom cover plate (pn 303302) is to be secured
to the shifter body using the four small #10 x 1/2" self-drilling
screws (pn 722542).
Since I knew the shifter body
would be installed in tight quarters up under the rig where it would be
difficult to get to with a drill, I pre-drilled the holes in the shifter
body to match the bottom cover plate. This way I would be able to install
the self-drilling screws with a small 1/4" ratchet and socket. |
|
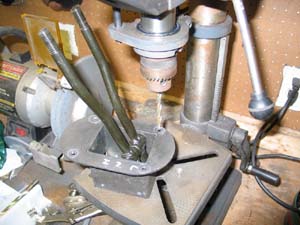 |
Before installation
I drilled out the mounting holes in the shifter body to accept a 1/4"
bolt.
This required that I first
remove the shift knobs, jam nuts, and twin-stick shift boot. |
|
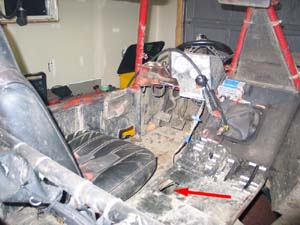 |
Using the bottom
of the shifter body as a template, make a rectangular cutout in the floor
where you want the shifters located. When you choose the location, make
sure you have clearance under the floor for the shifter body.
Stop and pause to admire my
sparkling clean interior...not! |
|
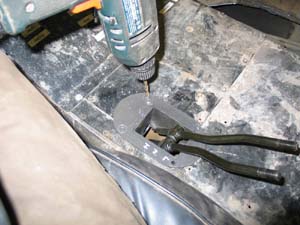 |
Slip the shifter
body through the cutout and use it as a template to drill the four 1/4'
mounting holes in the floor. |
|
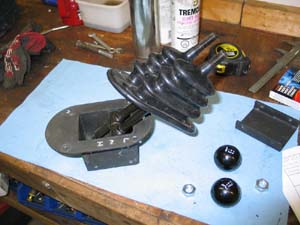 |
Remove the shifter
body and slip the twin-stick shift boot (pn 302060) over the shifters and
stretch the lip over the flange on the shifter body. Reinstall the jam nuts
and shift knobs. |
|
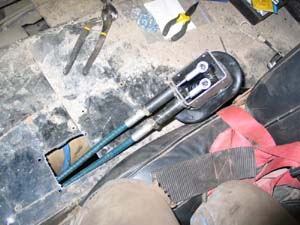 |
Pull the cables
up through the cutout in the floor and insert them into the shifter body.
Slip the Heim joints over the shifters, re-insert the cotter pins, and
spread the legs.
Fit the barrels to the shifter
body and secure in place by bolting the barrel retainer plate back onto
the shifter body with the three button-head cap screws.
Ummmm...make sure you connect
the correct cable to the correct shifter (don't ask!) |
|
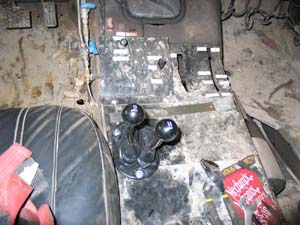 |
Fit the shifter
body back into the cutout and use 1/4" bolts, washers, and nuts to
bolt through the shift boot , shifter body and floor. |
|
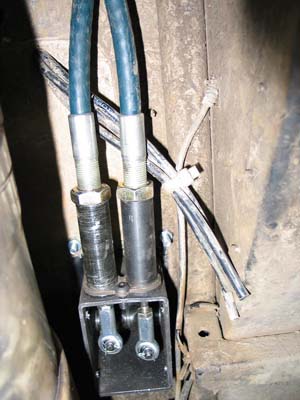 |
From underneath
the vehicle, screw the shifter body bottom cover plate (pn 303302) to the
shifter body using the four small #10 x 1/2" self-drilling screws (pn
722542). |
|
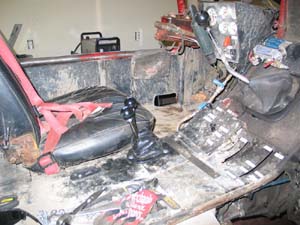 |
Completed twin-stick
installation. |
|
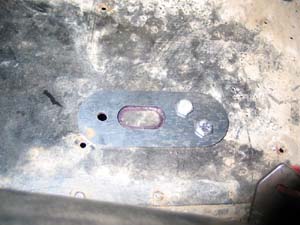 |
Begin the installation
of the reduction box shifter by using the shifter housing mount plate (pn
340601) as a template to mark the small oval slot required for the stick
to pass through the floor. |
|
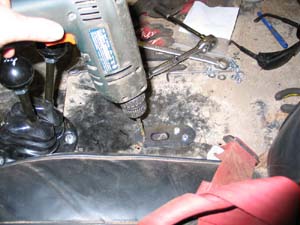 |
And to drill
the three 1/4" mounting bolt holes.
NOTE: In this pic I have the
plate the wrong way round. Of the two bolt-holes behind the slot, the
front-most should be on the LEFT to properly match the shifter housing
- not on the right as shown! Doh! |
|
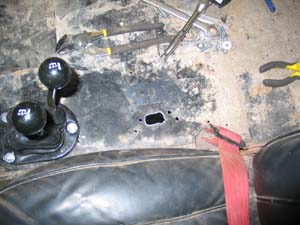 |
These are the only
holes you need to make in the floor for the shifter. |
|
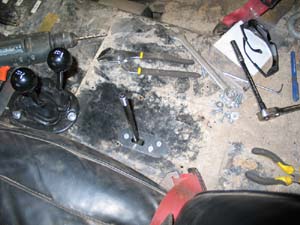 |
From underneath
the vehicle, pass the shift lever up through the floor and position the
shifter housing under the mounting holes you drilled (note the proper
orientation of the holes in this pic). It's quite helpful to have a helper
to hold the shifter housing from underneath at this stage as you get everything
lined up.
Sandwich the floor between
the shifter housing mount plate and
the shifter housing using
the supplied 1/4"-NF28 x 1" shifter housing bolts (pn 722543).
It was here that I found another
of the very few gripes with the kit. The mounting bolts supplied are 1/4"-NF28
but the three holes in the top of my shifter housing were not tapped to
this. I didn't measure what they were tapped to, but thankfully it was
smaller than 1/4"-NF28 so I was able to drill them out and re-tap
them under the vehicle without having to disassemble the cable/shifter
mechanism. |
|
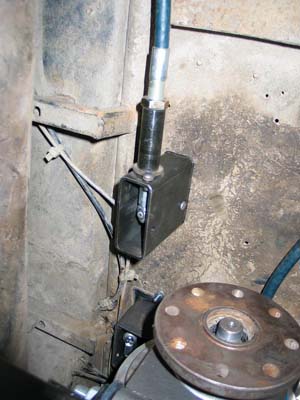 |
From underneath
the installed shifter housing looks like this.
Curiously, no bottom cover
plate is provided for the reduction box shifter as it is for the twin-stick
shifters? |
|
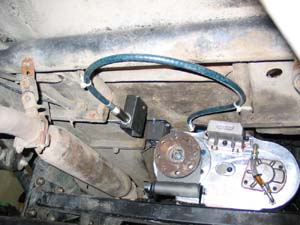 |
From underneath
showing the cable routing and reduction box shifter. Note the zip ties to
secure the cable. Be sure to keep the cables away from the exhaust. |
|
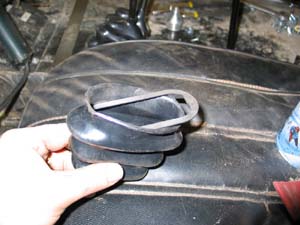 |
Back in the cockpit,
insert the single stick boot ring (pn 340602) into the single stick boot
(pn 340605). It lodges in the last of the wide folds. |
|
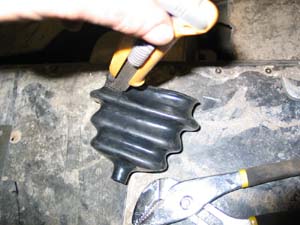 |
Trim off the excess
rubber below the ring. |
|
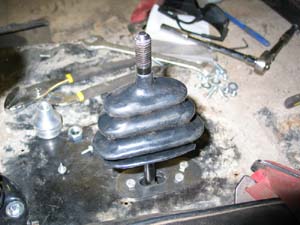 |
Slip the boot and
ring over the shift lever and push it down into place. Secure by screwing
through the rubber and boot ring and into the shifter housing mount plate
with the #10 self-drilling screws (pn 722542) |
|
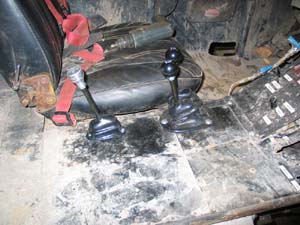 |
Finish by threading
the 1/2"-NC13 jam nut (pn 303121) onto the shift lever, followed by
the Shift knob (pn 340607). |
Following are a few pics of the installed
shifters. There's a little more work involved in installing and adjusting the
cable shifters than the traditional levers, but they offer great flexibility
in mounting position. I also think they're a great option as, should the need
arise, they make moving the case to a different vehicle easy.
Supporting
the Atlas - Main Crossmember |
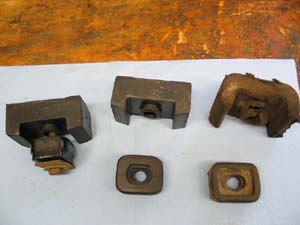 |
The extreme low
range of the Atlas-4SP means it will compound your motor's torque output
to phenomenal levels. As a result - a sturdy mounting system for the transfer
case is vital.
I liked the big, heavy-duty,
steel-impregnated rubber mounts used in my original setup - they are transmission
mounts from a 1980 CHEVROLET K30 PICKUP V8 5.7 Liter 4BBL.
In this pic you can see the
original piece after 26 years of abuse on the right. On the left are the
new pieces I ordered online from Advance
Auto Parts for only a few bucks each. |
Here are some other applications
for the same mounts:
1969 - 1984 BLAZER / 1968 - 1984
K10 SUBURBAN / 1961 - 1967 C10 PICKUP / 1986 K10 SUBURBAN / 1968 - 1984 C10
SUBURBAN /
1963 - 1985 K20 PICKUP / 1961 - 1967 C20 PICKUP / 1968 - 1984 K20 SUBURBAN /
1968 - 1984 C20 SUBURBAN / 1968 - 1974 K30 PICKUP
1961 - 1967 C30 PICKUP / 1977 - 1984 K30 PICKUP / 1982 C30 PICKUP / 1963 - 1965
P10 SERIES / 1984 C30 PICKUP / 1987 - 1989 P20 VAN /
1964 - 1966 G10 VAN / 1987 - 1990 P30 VAN / 1963 - 1984 K10 PICKUP |
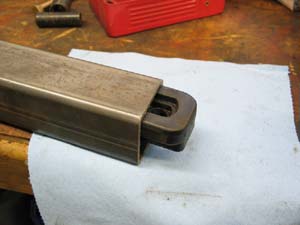 |
The smaller piece
slips perfectly inside 2.5" square, 3/16" wall H.S.S. |
|
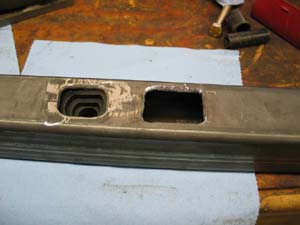 |
If you look closely
at the first picture of the mounts above, you can see that the larger
half (top, center of the pic) has a protrusion in the centre that fits
through a slot in the crossmember and into the recess in the smaller piece.
You can see the recess it fits
into clearly in the left slot in this picture.
The only reason the two slots
are different sizes in the crossmember here is that my fab skills are
legendary in their suckeyness! |
|
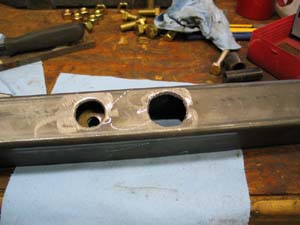 |
Opposite the
slots are two round holes cut large enough for a socket to fit inside
and onto the bolt heads.
In this case, the right hole
is intentionally larger as it needs to be big enough to insert the washers
through because the ends of the crossmember will be welded closed. |
|
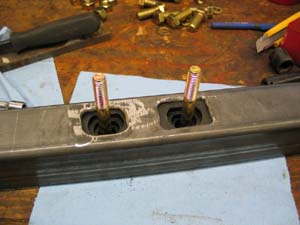 |
A 1/2"NC-13
x 5" bolt goes through the hole in the other side, through a washer,
through the smaller piece of the mount, and protrudes out the top of the
crossmember. |
|
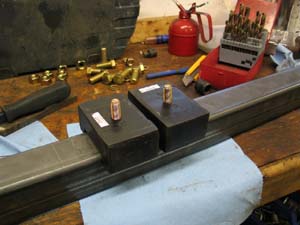 |
The larger pieces
of the mount go over the bolts and fit perfectly over the 2.5" square
tubing. |
|
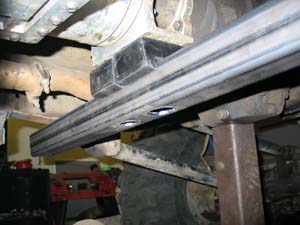 |
I then drilled
two holes in the mounting foot of the adapter and bolted on the mount
/ crossmember with washers and locknuts. |
|
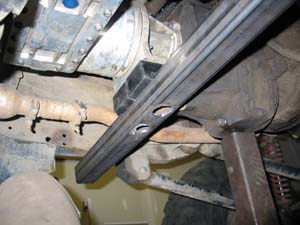 |
Here I am test-fitting the crossmember to figure out where it needs to be attached to the vehicle. |
|
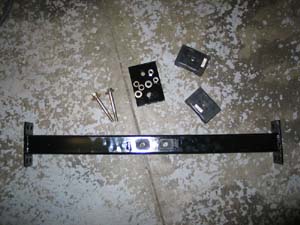 |
In order to get the crossmember positioned vertically in the vehicle where I wanted, I had to use a rectangular 3/8" steel spacer between the rubber mounts and the bottom of the transfer case adapter.
You can see it in this pic under the nuts and washers. |
|
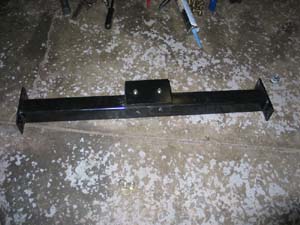 |
The assembled crossmember / mount looks like this. |
|
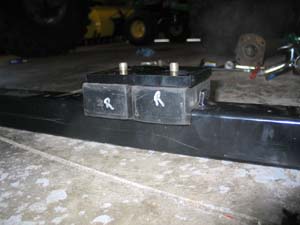 |
Close-up of the mount. You can clearly see the 3/8" thick spacer on top of the rubber mounts. |
|
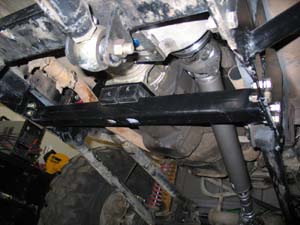 |
Crossmember installed.
It's mounted to the frame with eight 5/8" fine thread grade 8 bolts using red Loctite. |
|
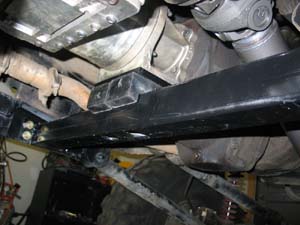 |
Close-up of the mount installed. |
|
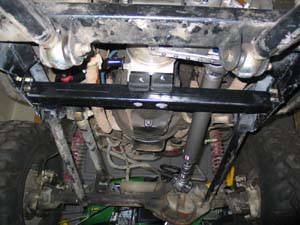 |
View of the crossmember and mount from below and behind. |
|
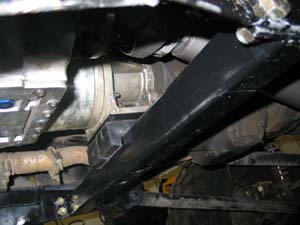 |
Final view of the crossmember and mount where it supports the transfer case adapter.
This simple setup should provide excellent vertical support to the drivetrain. |
Supporting
the Atlas - the Roark Fabworks Atlas Mount Kit
A sturdy crossmember is a given - but with a case capable of this kind of torque
multiplication a little extra thought is required regarding its mounting requirements.
With two widely spaced motor mounts and a single central transmission crossmember
what we have is a 3-legged stool arrangement (thanks to Randii for the metaphor).
Obviously our drivetrain needs to be supported vertically and laterally, lest
it depart the vehicle in a manner not altogether desired - and the stock-like
"bar-stool" arrangement fills this need well. However, the drivetrain
also needs to be supported, or rather, "restrained' rotationally - so that
it doesn't torque itself all over the place. It is here that the 3-legged bar
stool arrangement may not be adequate for a drivetrain capable of multiplying
a few hundred ft/lbs of torque by two or three hundred times!
To assist in rotational rigidity, as well as to help support the weight of
the fairly lengthy drivetrain, I turned to a really nifty product from an outfit called Roark Fabworks. Like most great things it's deceptively simple
- along the lines of "why didn't I think of that?" Well, in my case,
even if I had we all know how legendarily appalling my fab skills are - so a
neat little kit like this is just perfect. |
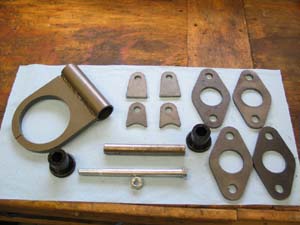 |
This is the kit.
The main component is the support ring (top left) that clamps around the tailshaft housing of the Atlas.
The ring is then supported by bushings and clamped between weld-on tabs.
Some very nice flanges are also included for use with tubular crossmembers. They are sized for those using 1.75" OD tube. |
|
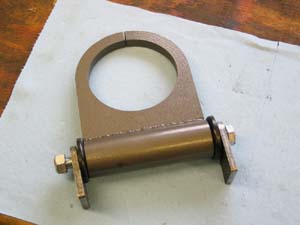 |
Here we see the support ring loosely assembled with the supplied weld-on tabs. |
|
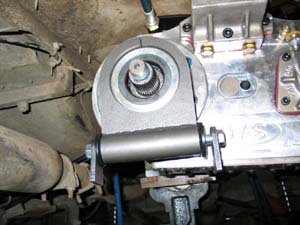 |
This is how the support clamps to the tailshaft housing of the Atlas.
It fits both the regular and the "short" competition tailshaft housing.
This is a trial-fitting picture - note that there is plenty of clearance, even with the short housing like mine, for the Roark support to sit flush with the end of the housing. |
|
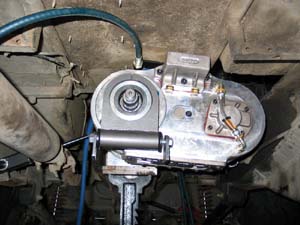 |
If you are using yokes on your Atlas the Roark mount will slip right on. If you are using a flange, you will need to remove the flange to position the mount over the tailshaft housing.
With the mount in place, tighten the small Allen screw that will clamp the mount tightly to the tailshaft housing. |
|
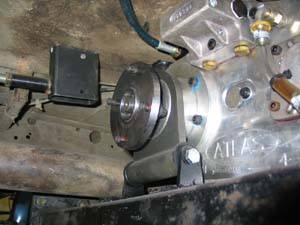 |
You can install the mount in any orientation.
Once you have the position selected, you can tighten the long bolt through the bushings and weld the tabs in place.
If you don't already have a crossmember in the right location, the supplied flanges can be very handy in fabricating a tubular crossmember to support the mount.
I was lucky and the mount lined up perfectly with my 4-link suspension crossmember. |
|
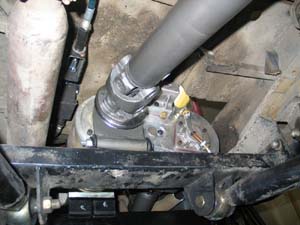 |
It's a trick little kit that would make an excellent addition to any Atlas. |
Controlling Rotational Moment - Building a Torque Arm |
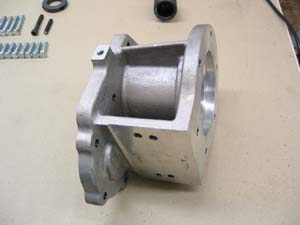 |
Even with the Roark Fabworks mount, I was still concerned about rotational stability, especially with the extreme torque multiplication of the Atlas-4SP, the aluminum transfer case mount, and reports of mounting bolts either stripping loose or breaking.
There is a small threaded boss on the side of the transfer case adapter, on the side of the transmission-side flange. |
|
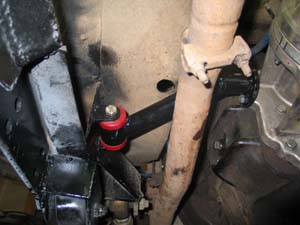 |
I used it to bolt on a flange that I welded to a tubular torque arm which I then attached to the frame with a bushing mount. |
|
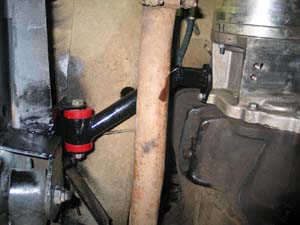 |
Shot from below. It won't win any awards for fabrication but it should do the job. |
|
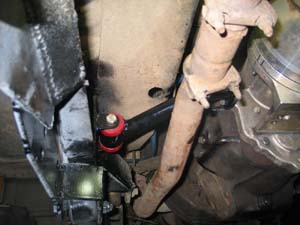 |
My theory is that, by adding this additional support perpendicular to the drivetrain, the drivetrain won't rotate under torque enough to cause any problems. |
Heavy Duty Driveshafts - High Angle Driveline 1-ton 1350 C.V. Shafts with 1410 axle yokes |
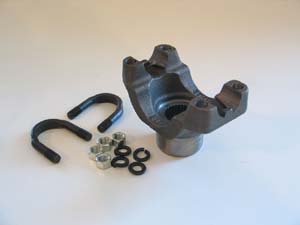 |
With a kick-ass, one-of-a-kind new 4-speed transfer case installed, I wanted bulletproof driveshafts to match.
For my new shafts I turned to one of the most highly respected names in the business - High Angle Driveline (HAD).
While I was at it I also decided to upgrade the puny stock 1310 joint of my front Dana 60 to this 1410 monster from HAD. |
|
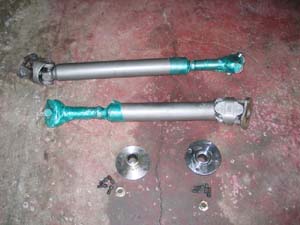 |
I had already been running one of HAD's 1-ton 1350 CV shafts in the rear, with a 1410 joint at the 14-Bolt pinion.
Since the Atlas-4SP is actually some 4" or so shorter than my old 203/D20 doubler, I sent the rear shaft back to HAD to lengthen and asked Jess to make me a front shaft to match - 1350 CV joint at the 'case and 1410 joint at the axle.
I also needed two of HAD's patented CV flanges to install in the Atlas. They come with flange-to-CV bolts and new locknuts to secure the flanges to the Atlas output shafts. |
|
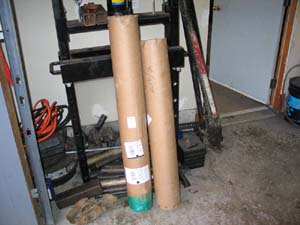 |
The shafts arrived in these super-tough tubes, complete with wooden end-caps screwed on. |
|
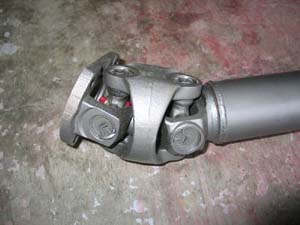 |
This is the 1-ton 1350 CV joint... |
|
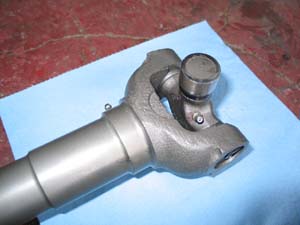 |
... and this is the 1410 joint at the axle end of the shaft. |
|
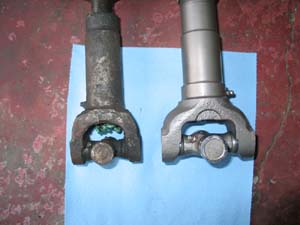 |
Comparison between the old 1310 shaft on the left, and the new 1410 shaft on the right. |
|
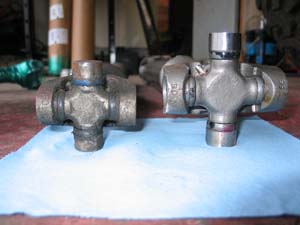 |
1310 on left, 1410 on right. |
|
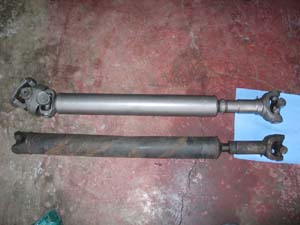 |
The new front shaft above the old, single-cardan shaft. |
|
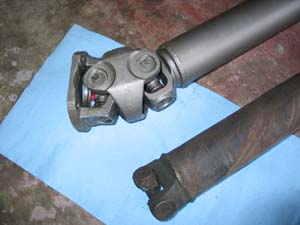 |
Comparison between the transfer-case ends of the new and old shafts. |
|
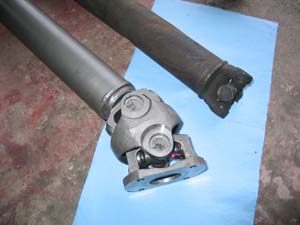 |
1310 single-cardan joint vs. 1350 CV joint. |
|
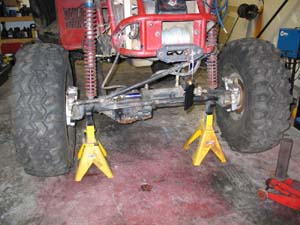 |
Before installing the new driveshafts the first step was to install the 1410 yoke on the Dana 60 pinion.
Start by jacking up the front wheels and placing the front axle on jack stands so you can rotate the pinion freely. |
|
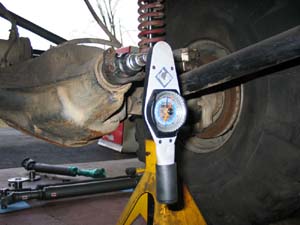 |
Before disassembling anything, use a dial-type inch-pound torque wrench on the pinion nut (1-5/16") to measure the torque required to rotate the pinion, and record this value.
You must measure the torque it takes to rotate the pinion by the nut while it is in motion. If you simply measure the torque it takes to start the pinion rotating you will get an artificially high reading. This is why a dial-indicating torque wrench is best as you can start the pinion rotating, then read the indication from the dial while you continue to rotate the pinion.
In my case it was about 25-30 in/lbs |
|
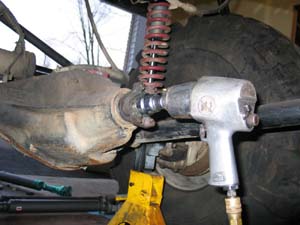 |
Remove the pinion nut and the old yoke. |
|
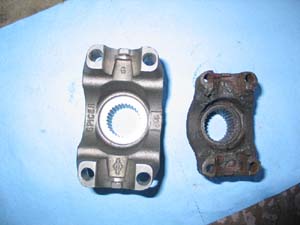 |
With the old yoke removed, marvel at the difference between the puny 1310 piece and the beefy 1410 yoke. |
|
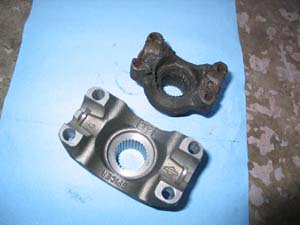 |
I love big, Heavy Duty upgrades! |
|
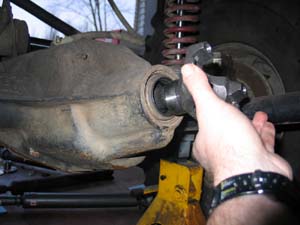 |
Slide the new yoke onto the pinion... |
|
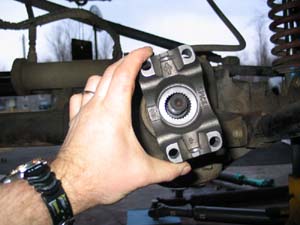 |
...making sure the splines line up and the yoke seats against the seal. |
|
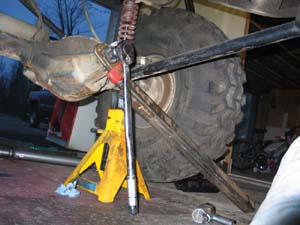 |
Install a new flanged lock nut and tighten to the minimum torque spec for the axle (220 ft/lbs for a D60).
Reinstall the inch-pound torque wrench on the pinion nut and again measure the torque required to rotate the pinion. Compare this value to that which you previously recorded.
If the second value is approx. 1-5 in/lbs more than the first you are done.
If not, continue tightening the pinion nut in small increments until you reach a point where the torque-to-rotate is approx. 1-5 in/lbs more than it was originally. Do not exceed the maximum torque value for the axle (280 ft/lbs for a D60). |
|
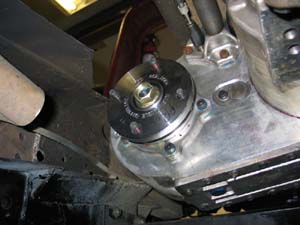 |
The next step is to install the flanges onto the Atlas.
A note on the flanges. If you are planning on using HAD 1350 flanges and driveshafts with your Atlas, you actually need to order your Atlas with 1350 non-cv yokes. This is because the HAD flanges use the same seal diameter as the Atlas non-cv yokes.
Of course you could always order your Atlas from HAD and get it with the flanges installed. |
|
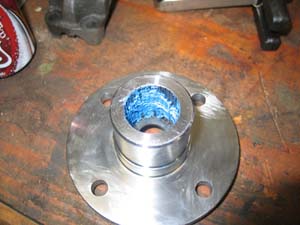 |
The next six steps apply to both front and rear flanges.
1 - Smear a little blue RTV on the inside to prevent oil from leaking past the splines. |
|
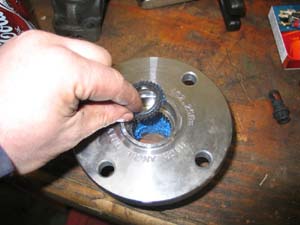 |
2 - Insert the little rubber washer (that would have come off when you removed the yokes the Atlas shipped with). |
|
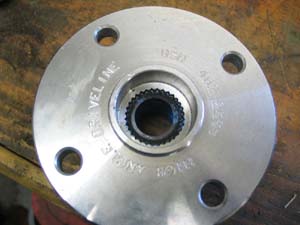 |
Rubber washer installed. |
|
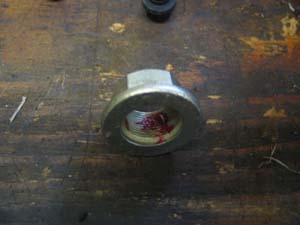 |
3 - The flange nuts are locking-type, but I feel a little dab of red Loctite is good insurance. |
|
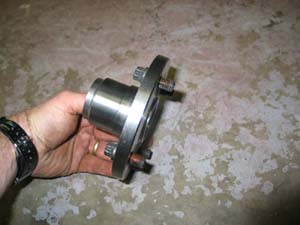 |
4 - Because of limited clearance between the transfer case and the back of the flange you need to pre-install the 12-point bolts that secure the driveshaft. |
|
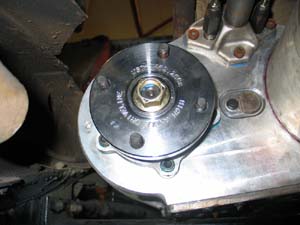 |
5 - Slip the flange over the splines and install the locknut. |
|
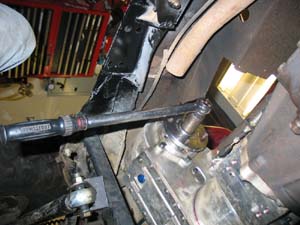 |
6 - Torque the flange nut to 150 ft/lbs |
|
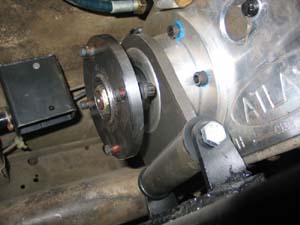 |
Rear flange installed. |
|
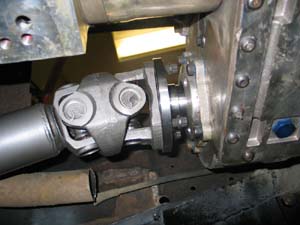 |
Hold the driveshaft in place and and start the bolts into the threaded holes in the CV joint flange with your fingers.
Because of the limited clearance, there is insufficient room to get a wrench on the bolt heads until they are threaded partly into the driveshaft.
You may find that you have to use needle-nose pliers or vice-grips to tighten the bolts sufficiently to get enough room to get a wrench on the bolt heads. |
|
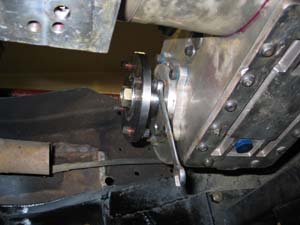 |
The 12-point bolts are tightened with 12-point 12mm box-end wrench.
The bolts come with thread locker pre-installed so you needn't add any.
You want to tighten the bolts to about 35 ft/lbs. It's impossible to get a torque wrench in there, so you'll have to use a "calibrated hand". Unless you're a gorilla, almost as tight as you can get them with the 12mm wrench is probably pretty close. |
|
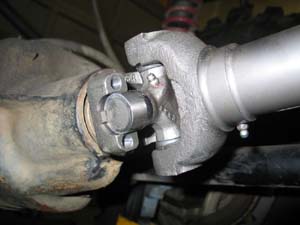 |
At the axle end of the shaft, set the U-joint in place in the yoke. Make sure the U-joint caps are seated completely and evenly between the little locating tabs on the yoke. |
|
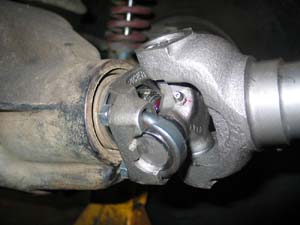 |
Then install the U-bolts, lock washers, and nuts. |
|
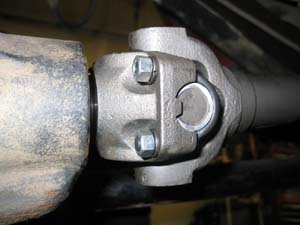 |
Tighten the nuts evenly with a 9/16" wrench. |
|
 |
Transfer case end of front shaft. |
|
 |
Axle end of front shaft. |
|
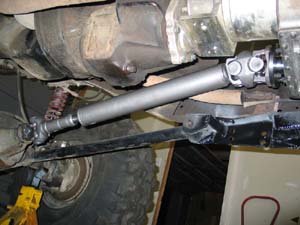 |
Front shaft installed.
Doh! I think I just made the Dana 60 R&P the weak link. |
|
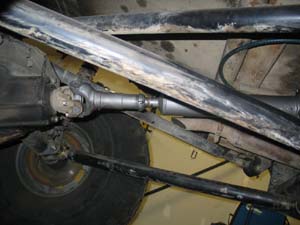 |
Rear shaft installed. |
The Finished Install
A gallery of shots of the installed Atlas-4SP, Roark Fabworks Mount, and High Angle Driveline 1350 CV shafts.
Conclusion
Reliable, strong, short, lightweight, four-speed, synchronized, leak free, and with long-term proven reliability - it's my considered opinion that the Atlas four speed transfer case simply has no equal in the market - simple as that.
The following table, showing my available gear ratios, really says it all.
Gear |
Atlas (Case / Reduction box) |
Ratio |
1 |
L/L |
278 |
2 |
L/L |
152 |
1 |
L/H |
102 |
1 |
H/L |
73 |
3 |
L/L |
67 |
2 |
L/H |
56 |
4 |
L/L |
42 |
2 |
H/L |
40 |
1 |
H/H |
27 |
3 |
L/H |
24 |
3 |
H/L |
18 |
4 |
L/H |
16 |
2 |
H/H |
15 |
4 |
H/L |
11 |
3 |
H/H |
6 |
4 |
H/H |
4 |
Combined with the trick Roark mount and bulletproof CV driveshafts from High Angle the Wolf now has a killer drivetrain that can go toe to toe with any other on the planet. Period.
References:
|