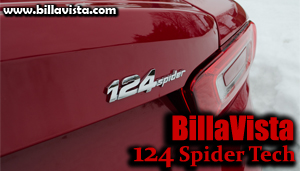 |
The Automotive Plumbing Bible
By Bill "BillaVista" Ansell
Photography: Bill Ansell
Copyright 2009 - Bill Ansell
(click any pic to enlarge)
|
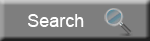 |
What is plumbing (in the automotive sense)?
Simply speaking, plumbing is the collection of components involved in moving a fluid from one place to another. The fluid could be a liquid (fuel, coolant, etc.) or a gas (compressed air, etc.).
There may be many different reasons we need to move a fluid from one place to another – it could be to cool the fluid, or it could be so the fluid can do some work - as in fuel moved from a tank to an engine.
What all plumbing shares in common is that its importance is often overlooked. |
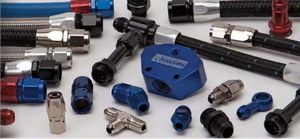 |
Why is plumbing important?
Why is plumbing important? The fact is, any piece of machinery, and particularly a vehicle subjected to the rigours of offroad or racing use, is a collection of inter-operating components – and failure of any of those components often means failure of the machine. Whether that failure results in a ruined weekend adventure or the loss of a checkered flag, it is something we wish to avoid. Whatever the machine in question, it is only as reliable as its weakest link. If the weakest link fails, the machine fails. In a vehicle, there are so many systems that rely on fluid movement that, combined with the tendency for folks to overlook the importance of something as seemingly “simple” as plumbing, odds are a plumbing failure will strike all of us at some point. But it doesn’t have to – and this article is all about, as much as possible, avoiding that failure.
Part of the problem with plumbing is that it is given little respect or thought. All too often it seems as if it would be easy (and cheap) to just use any old piece of hose and a hardware-store fitting to plumb something on the car. Sure, you could do this, and many do. We tend to find these people broken down and blocking the trail or sitting dejected in the pits. In fact, I would venture a guess that plumbing failure is one of the most common contributors to unnecessary failures and breakdowns. On the other hand, plumbing success need not be difficult or overly expensive – all it takes is a little knowledge compared with some care and thought.
For example, which would you say is the most important component in your car:
… is it the engine that produces the power?
… or the fuel that is burned by the engine?
… or the oil that cools and lubricates the engine?
… or the hose that carries the fuel from tank to motor?
… or the hose that carries the oil to the filter/cooler and back?
… or the oil cooler, oil filter, the fuel tank?
… or the fittings that connect the hoses to the components?
The answer is: all of them. When any one of these components fails, the machine fails – or at the very least is unable to operate at peak performance or efficiency. Since none of the components can be allowed to fail, they are all equally important! As a result – the car’s plumbing deserves every bit as much care and attention in its selection, fabrication, installation, use, and maintenance as any other part of the car!
The above example deals with just a couple of systems on the car – but there are many others where plumbing is an important factor, including:
- Brakes
- Fuel Supply and Return
- Engine Oil Cooling and Filtering
- Auto Transmission Fluid Cooling and Filtering
- Axle, Transmission, and Transfer Case Vents
- Engine Coolant
- Power Steering
- Hydraulics (steering, rear steer, hydroboost, etc.),
- Compressed Air (lockers, OBA (tools and tires), pneumatic shifting)
- Clutch
- Nitrous Systems
- Mechanical Gauges
So, plumbing is important and not to be overlooked.
Basic Components
The basic components of any plumbing system are relatively few and straightforward. Essentially, you have:
- Lines to contain and convey the fluid.
- Hose-ends to join the lines to the necessary components.
- Ports tapped into components into which fittings thread.
- Adapters and unions used to join hose-ends together or to join hose-ends to ports.
Let’s have a look at each now, and cover them each in greater detail later.
Lines
Fluid lines can be pipe, tube, or hose.
Pipe is rigid, heavy, and normally joined by threading, soldering, or welding. The water plumbing in your house is normally pipe. It is unsuitable for automotive use and so we will say no more about it, except that if someone says “pipe” in relation to automotive plumbing they probably mean “tube”. |
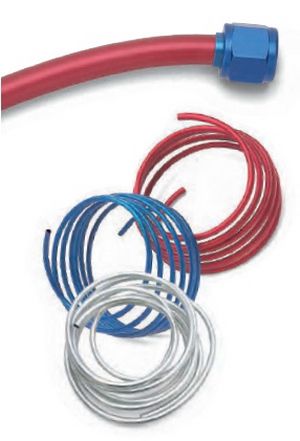
Russell Performance Aluminum Fuel Line (tubing) |
Tube is semi-rigid, lightweight, and can be joined with a large array of fittings. Brake “hardlines” are a common example of the use of tube in automotive plumbing. Being semi-rigid, it can easily be bent by using specialized hand tools. Although it can be bent by hand, tube is not truly “flexible” and must be secured along its length and not allowed to “flex” between components. Although cheaper than hose, it is more difficult to install and normally more challenging to join (often requiring the tubing to be “flared” for use with tube fittings). Tube may be made of steel, stainless steel, aluminum, or copper – each with its own properties.
Steel Tubing – Available in seamless SAE 1010 fully annealed and SAE welded types suitable for bending and flaring; steel tubing is the only tubing material approved without restrictions by SAE standards.
Stainless Steel Tubing – Available in both seamless 18-8 fully annealed and welded types suitable for bending and flaring; stainless steel tubing is recommended for use with very high pressures, where large diameter tubing is required, or where corrosion is a problem. Stainless steel tubing is expensive and not commonly used in automotive applications.
Aluminum Tubing – Available as seamless annealed, aluminum tubing is light-weight, corrosion resistant and is approved by the SAE for low-pressure applications.
Copper Tubing – Copper tubing tends to work harden when flared or bent and has poor resistance to vibration. Copper also acts as an oil-oxidation catalyst, causing sludge if used with petroleum based fluids. The use of copper tubing is not recommended in automotive applications.
|
|
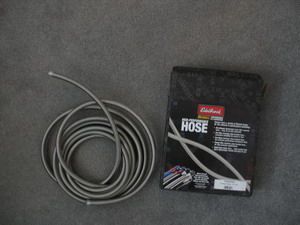
Russell Performance Proflex Hose |
Hose is flexible, relatively lightweight, and can be constructed of many different materials depending on the nature of the fluid to be conveyed. It can be used with crimped-on or re-usable “field attachable” hose-ends. A quality automotive hose will be constructed of multiple layers to maximize it’s vibration resistance, chemical compatibility, temperature resistance, flexibility, and abrasion & corrosion resistance. Hose is essential for use with components between which there is even the slightest relative movement. |
Hose Assembly
A hose with hose-ends connected to it is known as a “hose assembly”.
The most important thing to remember when constructing hose assemblies is to match the ratings of the hose and the hose-ends. It is possible to assemble a hose assembly with a hose-end(s) that have a performance rating (temperature or pressure rating) lower than the rating of the hose. Overall hose assembly performance will be limited to the lowest rating of the individual components used.
Hose assemblies can be built at home using bulk hose and field-attachable hose-ends or they can be custom ordered from a manufacturer with crimped-on hose-ends. If ordering complete, crimped hose-end hose assemblies, the end user must pay very careful attention to the length ordered. Normally hose assembly lengths will be specified as either:
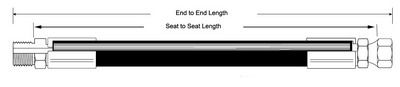
- end to end – the total overall length from the very end to the very end
- seat to seat – the hose assembly length measured between the sealing surfaces or “seats” of the hose-ends.
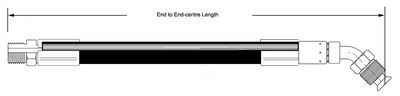
- end to end-centre – same as end to end but for hose assemblies with non-straight hose-ends. For these non-straight hose-ends, the "end centre" is the centreline of the hose-end at the seal surface.
We shall detail later in the article the process of creating your own custom-length hose assemblies using Russell Performance Proflex hose and full-flow aluminum filed-attachable AN hose-ends.
Fittings
The term "fittings" refers collectively to hose-ends, adapters, unions, and other small hard parts of the plumbing system. In general, fittings are used to join the lines together and to join the lines to the necessary components. Industrial fittings can be made of steel, brass, or aluminum but quality automotive fittings are almost exclusively aluminum. |
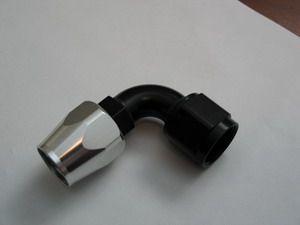
Russell Performance Aluminum Full-flow hose-end |
Hose-Ends
Hose-ends, also called couplings, are the parts that are crimped or screwed onto the ends of hose or tubing so that the lines may be joined to the necessary components. There are several different types common in automotive plumbing, each of which we shall examine in great detail a little later. |
|
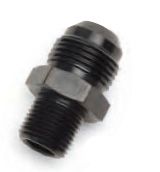
Russell Performance NPT (pipe) to AN adapter |
Adapters
Adapters are fittings that are used to connect other components that do not have common styles. They may be used to join hose-ends of differing types or sizes, or they may be used to connect a port of one style or size to a hose-end of a different style or size. For example, if you have an oil cooler with ½” NPT ports and are using oil cooler lines constructed from -10 stainless steel braided hose with -10 AN hose-ends, you would use a “½”NPT to -10 AN” adapter. Basically an adapter “adapts” one size or style of fitting to another size and/or style. |
|
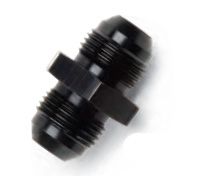
Russell Performance -10AN to -10AN union |
Unions
A union is a special type of adapter used to join hose-ends or to join a port and a hose-end when both parts being joined are the same size and style. If you wanted to connect two hoses, both using -10AN hose-ends, you would use a “-10AN to -10AN union”. |
|
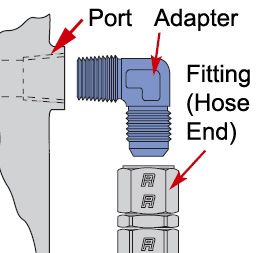 |
Ports
I use the term “ports” to refer to the holes into which hose-ends, adapters, or other fittings must fit. Depending on the component in question, they may be a straight hole in which a “bulkhead fitting” is used, or they may be threaded holes such as the oil line ports in an engine block or transmission casting. Normally, when plumbing a car one uses the necessary adapters and hose-ends to fit the existing ports in the components. However, if fabricating highly customized components, the plumber may be faced with a choice of what type of port to create. In this case, I have included some discussion on the matter in the sections on individual hose-end types and thread tapping. Essentially, the easiest port to construct is a straight hole in which a “bulkhead fitting” is used, the next simplest is probably some sort of female tapered pipe thread drilled and tapped, and the most difficult, but best, would be a port that uses a machined seat for an elastomeric seal such as an O-ring. |
|
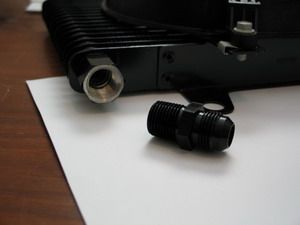 |
Oil cooler with NPT port and an NPT to AN adapter. |
|
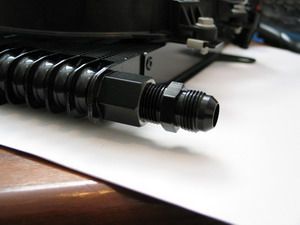 |
NPT to AN adapter fitted into NPT port. |
So, in short, the job of plumbing a car consists of selecting the right combination of tubing, hose, hose-end, and adapters to connect together all of the ports of the various components between which we need to transfer fluid.
Here’s how we go about doing just that.
Basic Principles
So what exactly distinguishes a quality, reliable, leak-free, high-performance plumbing job from a poor, unreliable, failure-prone one?
A quality plumbing system will:
Be constructed of high-quality components of known reputation
The use of cheap, no-name or generic industrial components invites unpredictable performance and unwanted failure. The demands of offroad motorsports are extreme and unique. Maybe cutting a few corners saves you a few bucks, but more likely it costs you a bunch more eventually. Using components from a manufacturer such as Russell Performance, with a proven track record of producing quality plumbing components that withstand the rigours of high performance automotive use is the easiest and best way to be well on the way to creating a quality plumbing system.
Have the fewest joints/unions/connections & therefore fewest potential leak paths as possible
Each and every connection in a plumbing system is a potential leak path – a point where the system can leak. Minimizing the number of connections is one of the best ways to reduce the risk of potential leaks. This can be achieved through thoughtful design and layout, as well as by the use of the best fittings available. For example, if you need to route a hose assembly 180° from the component to which it attaches, you could go to the hardware store and use two 90° elbows with a straight nipple between them for a total of three potential leak paths; but the far better way to do it would be to use a quality 180° hose-end, like those available from Russell Performance. Russell manufactures hose-ends in straight, 45°, 90°, 120°, and 180° , allowing you to design a system that is neat, clean, and has minimal potential leak paths.
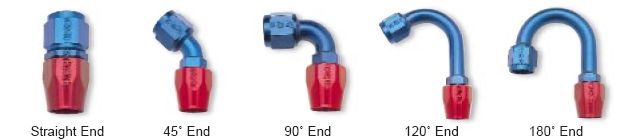
Be easy to install, inspect, diagnose, and maintain
Once again, quality components and thoughtful design & layout are key here. You should design your plumbing so that it can easily be inspected periodically, and use components that are readily available and easy to repair or replace. This is an area where using that Komatsu industrial hose and fitting you scavenged from a piece of heavy equipment may not be the best plan. On the other hand, stainless steel braided hose combined with AN/SAE37° field-attachable hose-ends, especially those that allow for clean routing, minimum hose length, and the minimum number of connections, are ideal for creating a system that is easy to install, inspect and maintain. We shall discuss hose-end types and their advantages in detail shortly. For abusive offroad use, particularly for systems that may be subjected to damage, the use of field-attachable hose-ends is a godsend, allowing a length of hose and spare hose-ends to be carried for easy trailside repairs.
Be built of components able to handle the minimum and maximum temperatures and maximum pressures that will be experienced by the system
Good hose and fittings will have published temperature and pressure limits that must be matched to the system being designed. It’s not only ineffective but also very unsafe to use hose that is unrated or that has an insufficient pressure or temperature rating to carry hot pressurized oil and other automotive fluids.
Be built of components that are chemically compatible with the fluids being carried
Not all hose is equal, not by a long shot. There are many different materials that can be used in the construction of hose. Particularly when plumbing fuels and oils you must ensure that the hose you use is chemically compatible with, and designed to carry, the fluids in question. Failure to do so puts not only the plumbing itself at risk, but also the components the plumbing connects since incompatible fluids can dissolve the inside of the hose creating debris that can be carried into the engine or fuel injectors or hydraulic steering components.
Be as light as possible
For those seeking the ultimate competitive edge in climbing or racing, weight is always an issue. Industrial hose and fittings can be bulky and heavy, whereas specialized racing hose and aluminum fittings are both strong and light weight.
Minimize pressure drop, turbulence, and friction-heating of the fluid being carried
Without going into excruciating detail on the laws of fluid dynamics, it is nevertheless necessary for me to cover the basics of pressure drop, turbulence, venturi effect, vapour pressure, and cavitation before we can make the best informed decision on component selection and design of our plumbing system. Don’t worry – I’ll keep it simple and summarize with some rules of thumb!
Pressure Drop
The short story is, anytime fluid is moved through a plumbing system there will be some pressure drop – the same way there is always some voltage drop through a wiring system. And like the electrical system where we want to minimize voltage drop and get maximum possible voltage delivered to the components that are using it; in a plumbing system we want to minimize pressure drop through the plumbing and deliver full-pressure fluid to the necessary components. Why is this important? First, imagine your home plumbing system. Pressurized water is delivered to the house, but it’s no good if you loose that pressure before the water gets to where you want to use it – we’ve all suffered standing under a dribbling shower head with no pressure at some point. Well, your engine’s bearings or your fuel system’s injectors are no different than you standing under that shower – they work best with full pressure delivered.
Pressure drop in a plumbing system is caused by any restriction in the system. The primary culprit is friction between the fluid and the inside of the plumbing. This in turn may be caused by:
- A hose or tube of insufficient diameter for the flow rate, fluid velocity, fluid viscosity or length of hose.
- Hose or tube that is bent, kinked, crimped, or hose routed with too small of a bend radius.
- Excessive use of couplings and adapters with different inside diameters.
- Low quality fittings or hose with excessively small inside diameter for the nominal size.
- Use of abrupt 90° hose-ends or fittings that are not mandrel bent and do not have a smooth, consistent ID.
- Restrictions caused by worn or damaged components.
Venturi Affect
The other major cause of pressure drop is due to what is known as the “venturi effect”. Basically, a venturi is an area of narrowed or reduced inside diameter – like the throat of a carburetor. When a fluid flows through a venturi, its speed increases but its pressure drops. This is due to the a law of fluid dynamics known as Bernoulli's principle that states that an increase in the speed of a fluid occurs simultaneously with a decrease in pressure or a decrease in the fluid's potential energy (it’s a specialized form of that old standby, the law of conservation of energy …”energy can never be created nor destroyed, just converted from one form to another”.) It’s the same principle by which aircraft fly. Now, in the case of the carb, the venturi is used to advantage to speed the airflow and help atomize the fuel. In the case of plumbing, we generally wish to avoid any venturi affect and attendant pressure loss.
|
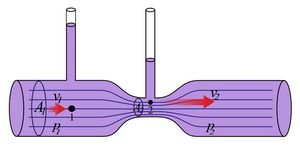 |
A model venturi.
At point (2) the speed of the fluid is increased and the pressure decreased, compared to the speed and pressure at point (1). |
Vapour Pressure and Cavitation
If pressure drop in a plumbing system is drastic enough, the fluid in question may actually spontaneously change state from a liquid to a vapour (gas). All liquids have a property known as a “vapour pressure”. This is the pressure below which the liquid changes from a liquid to a gas. This is similar to the way boiled water changes state from a liquid to a gas (steam). When this change of state happens, tiny vapour bubbles will form in the fluid. The process is called cavitation. The vapour bubbles may then collapse very rapidly as they are exposed to higher surrounding pressure. The individual bubbles formed and then collapsing are very small, even microscopic, but they from and collapse very quickly and with great force and in great numbers. Cavitation can be extremely damaging to components such as pumps. Left unchecked, the vapour bubbles that form will mix with the liquid - a process called aeration. The resultant mixture of oil and vapour inhibits the functioning of the fluid – whether it be lubrication, cooling, or delivering hydraulic power.
Friction Heating & Turbulence
In most cases, we expend significant effort cooling the fluids in our vehicles. Unfortunately, many of the factors listed above as causing friction induced pressure drop, also cause friction heating of the fluid – obviously, this is the last thing we need in our plumbing. All these factors can also contribute to excessive turbulence of the fluid in the plumbing, which is also something we wish to avoid, as turbulence can lead to aeration of the fluid.
The bottom line is, to avoid all of these pitfalls we must pay close attention to the components we select and the way we install them. Choosing mandrel-bent, “full flow” hose-ends combined with properly rated hose or tube of the correct diameter for the flow rate and length, along with following proper installation practices such as adhering to hose minimum bend radius specs, will allow us to minimize pressure drop, turbulence, and friction heating of the fluid being carried.
In summary, if our goal is a quality, reliable, leak-free, high-performance plumbing job - when selecting a product, the total system design must be considered to ensure safe, trouble-free performance. Function, material compatibility, adequate ratings, proper installation, operation, and maintenance are the responsibilities of the system designer and user.
We will explore how shortly, but first a word about safety is in order.
Plumbing Safety
If plumbing itself is often overlooked – plumbing safety is something that is rarely considered. This is a gross and dangerous error. Plumbing safety needs to be a serious concern to all of us. Many of the builds or installs that I see contain at least some seriously dangerous plumbing practices - they should be a source of great concern to those involved – here’s why:
Automotive plumbing is used to convey hazardous chemicals, steam, hot liquids and high-pressure oil which, if released accidentally, can cause serious bodily injury including burns, pressure wounds or chemical exposure .
Selection of the proper hose and fittings for the application is essential for the proper operation and safe use of the system. Inadequate attention to the selection of components or to the design and installation of the plumbing system can result in serious personal injury or equipment damage from:
- Fittings thrown off at high speed.
- Dangerously whipping hose.
- High velocity fluid discharge.
- Contact with conveyed fluids that may be hot, cold, toxic or otherwise injurious.
- Explosion or burning of escaping fluid or vapour.
- Loss of control of the vehicle due to plumbing failure in critical components such as steering and braking systems.
- Injuries resulting from inhalation, ingestion or exposure to fluids.
All About Hose & Tubing
A hose is not a hose.
Obviously the hose or tube used in any particular plumbing system plays a huge role in whether the system achieves the requirements of a quality, reliable, leak-free, high-performance plumbing system. Fortunately, hose tech is fairly simple. The job of selecting the right hose consists of matching the specs of the hose in consideration with the job to be done. That, combined with purchasing from a reputable source, will have you well on the way. The important specifications of a hose are:
Pressure Rating: Obviously, the hose must be rated to safely carry fluid at the pressure intended. Be extremely wary of hose sold without a pressure rating - even for use in low-pressure applications. As we have discussed, all manner of injury and damage can occur when a hose fails under pressure. In addition, this is unlikely to be beneficial to the motor, transmission, or other component to which the plumbing is attached.
Temperature Rating: Both minimum and maximum operating temperatures published for the hose are important. If you drive or even store the car in a cold climate, cold-weather performance of the plumbing hose is crucial. All plumbing, regardless of climate, can be subjected to fluid at extremely high temperatures. Make sure to match the hose used with the maximum temperature that will be seen by the system in question. Be certain that fluid and ambient temperatures, both steady and transient, do not exceed the limitations of the hose. Temperatures below and above the recommended limit can degrade hose to a point where a failure may occur and release fluid. Properly insulate and protect the hose assembly when routing near hot objects (e.g. manifolds). Do not use any hose in any application where failure of the hose could result in the conveyed fluids (or vapours or mist from the conveyed fluids) contacting any open flame, hot manifold, or other potential fire ignition source that could cause burning or explosion of the conveyed fluids or vapours.
Abrasion Resistance: Although there isn't a specification or measurement given, a hose's abrasion resistance is nevertheless a critical indicator of its suitability for any given installation. Abrasion is probably responsible for 80 or 90% of hose failures and subsequent plumbing system failures. Good and proper installation procedures, as detailed later in the article, can go a long way, but starting with the right hose for the job is key to success. For this reason, I always recommend a quality stainless-steel braided plumbing hose in off-road and high-performance automotive applications because of the punishing environments of high heat, dirt, and vibration.
Vacuum Rating: If the hose in question is to be used as a "suction" line - for example the hose that supplies a power steering pump with fluid from a remote reservoir - it must have a suction or vacuum rating. Vacuum ratings are measured in inches of mercury or in/Hg, and a full suction rating is 28 in/Hg. Hoses used for suction applications must be selected to ensure that the hose will withstand the vacuum and pressure of the system. Improperly selected hose may collapse in suction applications. Any hose suitable for use as a suction hose will have this rating clearly indicated. If it doesn't - it's not the right hose!
Chemical Compatibility: Chemical compatibility is about matching the fluid you wish to convey with the material from which the inner core of the hose is made. There are many different materials used in hose construction - known in the industry as "hose elastomers" (an elastomer is just a flexible compound). Common hose elastomers include:
- NEOPRENE ( Poly-Chloroprene) - CR
- NITRILE (Acrylonitrile & Butadiene) - NBR
- HYPALON (Chlorosulfonated Polyethylene) - CSM
- EPDM (Ethylene Propylene Diene) - EPDM
- CPE(Chlorinated Polyethylene) - CPE
- POLYESTER (Polyamide Resin) - PE-E
- TEFLON (
Fluorinated
Thermoplastic) - PTFE
Each has its own strengths and weaknesses, including cost. In addition to chemical compatibility with the fluid carried, the overall hose construction (including the elastomer, any additional braids or layers, and the outermost braid or layer) confers upon the hose its overall properties and capabilities. These in term determine its suitability for a given installation and how it will perform. As with most things in life - you tend to get what you pay for - with the cheapest solution being cheap rubber hose generally acceptable for low pressure and temperatures and highly susceptible to abrasion - with other options available all the way up to CPE or Teflon inner hose with multiple layers of construction including 308 stainless steel inner and outer braids, compatible with all automotive fluids, flexible from -40°C to 350°C, and rated to 1500psi, - like Russell Performance ProRace Hose.
The following tables give general properties of different hose elastomers, followed by specific chemical compatibilities for some chemicals common in automotive applications. Be careful using them in isolation, especially the first, in order to make purchasing decisions - as many of the properties listed (like flame resistance and abrasion resistance) can be modified or greatly affected by other materials used in the hose's construction, multiple layers used in the hose, and outer coverings, braids, and sleeves.
Table of Elastomer Properties
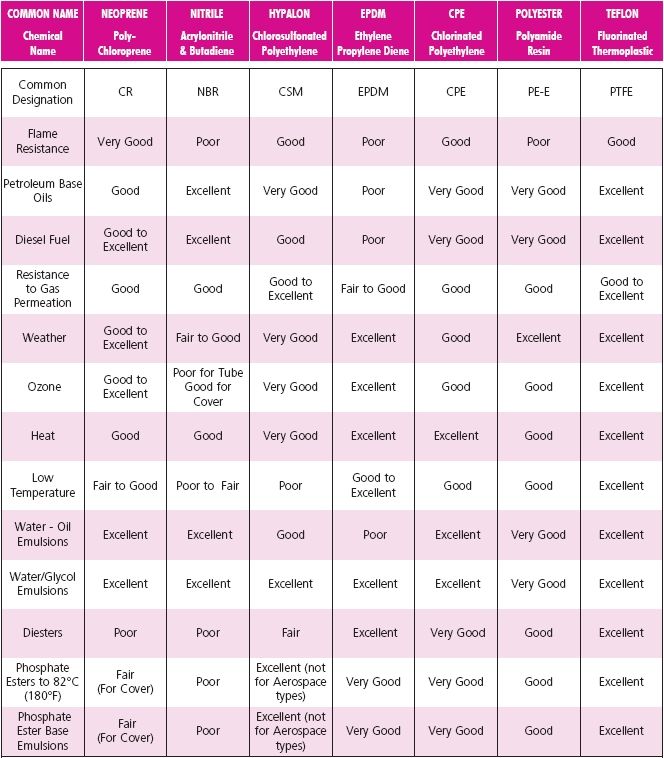
Table of Chemical Resistance.
The following table is an example of a table of chemical resistance. Depending on the hose you plan on using, and the use you have in mind for it, you may need to consult such a table to make sure your design is sound. An alternative can be to purchase a hose, such as Russell ProFlex or Russell ProRace, that is certified compatible with all automotive fluids.
Fluid |
Elastomer |
|
|
|
|
|
|
|
Neoprene |
Nitrile |
Nitrile PVC |
CPE |
Hypalon |
Polyester |
PTFE (Teflon) |
Air - 166°F |
E |
E |
E |
E |
E |
E |
E |
Air - 180°F |
G |
G |
G |
E |
G |
G |
E |
Air - 199°F |
N |
N |
N |
E |
G |
N |
E |
CO2 - dry |
G |
E |
E |
E |
E |
? |
E |
CO2 - wet |
G |
E |
E |
E |
E |
? |
E |
Diesel Fuel - under 122°F |
N |
E |
N |
G |
N |
E |
E |
Ethanol |
E |
E |
? |
E |
E |
G |
E |
Ethylene Glycol (coolant) - under 151°F |
E |
E |
E |
E |
E |
E |
E |
ASTM Fuel A |
N |
G |
G |
E |
E |
? |
? |
ASTM Fuel B |
N |
G |
N |
G |
N |
? |
? |
Fuel Oil |
N |
E |
N |
E |
N |
G |
N |
Glycerol |
E |
E |
E |
E |
E |
E |
E |
Grease (petroleum base) |
G |
E |
G |
? |
G |
E |
E |
Hydraulic Fluid (Phosphate Ester Base) |
N |
N |
N |
E |
E |
G |
E |
Hydraulic Fluid (Std. Petroleum Oils) - 212°F |
G |
E |
G |
E |
E |
E |
E |
Isopropyl Alcohol |
G |
G |
G |
E |
G |
? |
E |
Kerosene |
N |
G |
N |
E |
N |
G |
E |
Lubricating Oils - under 122°F |
G |
E |
G |
E |
G |
E |
E |
Methyl Alcohol (Methanol) 100% |
E |
E |
E |
E |
E |
G |
E |
Naphtha (Low Aromatics) |
N |
G |
N |
E |
N |
N |
E |
Vegetable Oils |
G |
E |
G |
E |
G |
E |
E |
|
E - Excellent Resistance |
G - Good Resistance |
N - Not Recommended |
? - No Data Available |
Here are some additional, more extensive, fluid compatibility charts from:
Aeroquip
DANA Boston Weatherhead
Ryco
Size: Calculating the required size of a hose can be a complicated business, involving calculations of fluid velocity, flow rate, and pressure drop - but fortunately for us it doesn't have to be. This is because many years of experience have taught us some very good rules of thumb for sizing hose in automotive plumbing applications. We'll get to those shortly, but for those who enjoy math and theory or for those who are perhaps working with a truly custom project, we'll cover a little theory first.
DO NOT WORRY if you get bogged down in the math and theory that follows. It's not critical to understand - the rules of thumb will serve us well - the theory is provided as optional for true tech nerds only!
Remember from our previous discussion that fluid velocity and pressure are related (as velocity, or speed, of the fluid goes up - pressure goes down) and that we wish to keep pressure drop in any plumbing system to a minimum. It stands to reason, then, that we would want to keep fluid velocity in the plumbing from becoming too high. Of course, we don't want it to be zero either, so we actually want to achieve a fluid velocity that is within a reasonable range.
Standard industry recommended fluid velocity ranges, in feet per second, are:
Suction or intake lines - 2-5 ft/s (e.g. power steering pump supply hose)
Low pressure or return lines - 4-15 ft/s (e.g. transmission cooler lines)
High pressure lines - 7-18 ft/s (e.g. hydraulic steering power lines)
If only there were an equation that relates fluid velocity to hose diameter!
Of course, there is:

To use the equation, flow will be taken from the spec of the pump that is moving the fluid. For example, a high-performance oil pump may pump at 10-12 gpm, an EFI fuel pump at 0.7 to 1.5 gpm, a water pump at anywhere from 15-60 gpm, and a power-steering pump at 2-4 gpm.
Now, obviously there is quite a range in the acceptable fluid velocity ranges given above, and so this equation can produce quite different values, depending on which end of the velocity range you are using. Knowing which velocity will work for which application is a complicated engineering problem - which brings us back to the rules of thumb, but for those so inclined it is nice to know where the rules come from.
For example, if we were to calculate the hose size required for the intake, pressure, and return lines of a hydraulic steering circuit using the above equation, a 4 gpm pump, and both extremes of fluid velocity, we would come up with:
Intake: 0.9 - 0.6" diameter (1" to 5/8" or -16 to -10 AN)
Return: 0.6 - 0.3" diameter (5/8" to 5/16" or -10 to -05 AN)
Pressure: 0.5 - 0.3" (1/2" to 5/16" or -08 to -05 AN)
For those that want to do their own calculations or comparisons without having to do a bunch of equations, you can use a chart called a "nomogram" and a straight edge. Click on the picture below to open or download a PDF file of just such a nomogram, complete with instructions and an example problem.
Hose Diameter Selection Nomogram
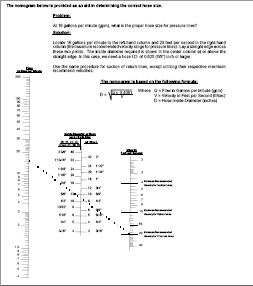
One of the things that accounts for the different velocity recommendations is the other factor that affects the required size for a hose - the length of the hose assembly. The longer the hose, the lower the velocity that is allowable. In addition - the longer the hose, the greater the pressure loss over its length and the greater the potential for friction induced heat generation or excessive fluid turbulence.
Once again, calculating specific pressure losses is something of a complex problem, requiring knowledge of flow rate, hose diameter, the specific gravity and viscosity of the fluid in question, the length of hose as well as the number, diameter, and bend radius of all bends in the hose; along with the dimension of any other restrictions to flow such as reduced inside diameters of any fittings.
The following diagram (click for full size) gives flow rate versus pressure drop for 100 foot length of different size hoses (hose ID's) for WATER. To read the diagram, first determine the flow rate and select this along the left-hand side. Follow that horizontal line across to the right until it intersects the diagonal line of the hose size of interest. At this intersection, draw a vertical line straight down and read off the pressure drop in PSI. Be aware that the values so given are for a 100' length of hose. To correct for shorter lengths of hose, divide the result by the percentage of 100' that the shorter length is. For example, for a 20' hose, multiply the result by 20% or 0.2, since 20 feet is 20% of 100 feet.
Flow Rate vs. Pressure Drop Diagram
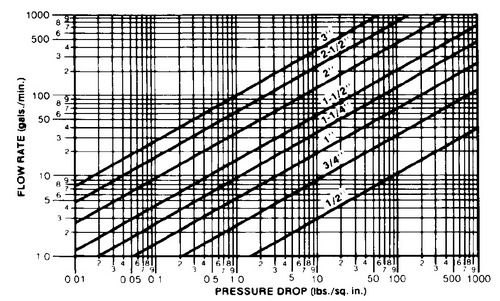
This length-corrected result must then be corrected for the actual fluid conveyed if it is not water. This correction takes into account the differences between the specific gravity and viscosity of water versus the fluid in question. To make the correction, DIVIDE the water value by the correction factor for the fluid of interest. Correction factors are shown in the following table:
Ethyl Alcohol |
0.93 |
No.1 Fuel Oil (30-40 SSU) @ 100°F |
0.85 |
No.2 Fuel Oil (35-50 SSU) @ 100°F |
0.75 |
No.3 Fuel Oil (55 SSU) @ 100°F |
0.66 |
No.5 Fuel Oil (60-450 SSU) @ 100°F |
0.47 |
No.6 Fuel Oil (430-2900 SSU) @ 100°F |
0.49 |
Gasoline - Type 1 |
1.04 |
Gasoline - Type 1 |
1.11 |
Gasoline - Type 1 |
1.19 |
Glycerol 100% @ 150°F |
0.45 |
Glycerol / Water 50/50 (coolant) |
0.72 |
Kerosene |
0.89 |
Lubricating Oil - Machine |
0.35 |
Lubricating Oil - Automotive |
0.39 |
Methanol |
1.07 |
Motor Oil |
0.39 |
For interest's sake, I extracted some figures from the diagram, corrected them for a 10' length of hose, corrected them for different fluids, and charted them below for 1/2", 3/4", and 1" hose. The colour-highlighted areas represent typical fluid flow-rates for different systems as shown in the key. For a 20' hose, double the value in the table, for a 30' hose triple it, and so on.
Note that I didn't include data for coolant and coolant-sized hoses as even a quick glance at the flow vs pressure drop diagram shows that: even if you had a monster 150 gpm water pump, a small 2" hose, and a long 20' length, pressure drop would only be about 4psi and since most water pumps are closer to 20 gpm and coolant hoses only a couple of feet in length it didn't seem worth extrapolating the data.
Pressure Drop in PSI per 10 foot length of hose for various fluids, hose diameters, and flow rates.
0.2 |
0.5 |
1.0 |
1.7 |
2.5 |
3.5 |
4.5 |
5.0 |
7.0 |
9.5 |
16.0 |
30.0 |
45.0 |
65.0 |
0.0 |
0.1 |
0.2 |
0.3 |
0.4 |
0.5 |
0.7 |
0.9 |
1.0 |
1.3 |
2.4 |
4.5 |
6.5 |
9.0 |
0.0 |
0.0 |
0.0 |
0.1 |
0.1 |
0.1 |
0.2 |
0.2 |
0.3 |
0.3 |
0.6 |
1.2 |
1.6 |
2.5 |
|
|
|
|
|
|
|
|
|
|
|
|
|
|
0.1 |
0.5 |
0.9 |
1.5 |
2.3 |
3.2 |
4.1 |
4.5 |
6.3 |
8.6 |
14.4 |
27.0 |
40.5 |
58.6 |
0.0 |
0.1 |
0.1 |
0.2 |
0.3 |
0.5 |
0.6 |
0.8 |
0.9 |
1.2 |
2.2 |
4.1 |
5.9 |
8.1 |
0.0 |
0.0 |
0.0 |
0.1 |
0.1 |
0.1 |
0.1 |
0.2 |
0.2 |
0.3 |
0.5 |
1.1 |
1.4 |
2.3 |
|
|
|
|
|
|
|
|
|
|
|
|
|
|
0.4 |
1.3 |
2.6 |
4.4 |
6.4 |
9.0 |
11.5 |
12.8 |
17.9 |
24.4 |
41.0 |
76.9 |
115.4 |
166.7 |
0.1 |
0.2 |
0.4 |
0.6 |
0.9 |
1.3 |
1.7 |
2.2 |
2.6 |
3.3 |
6.2 |
11.5 |
16.7 |
23.1 |
0.0 |
0.0 |
0.1 |
0.2 |
0.2 |
0.3 |
0.4 |
0.5 |
0.7 |
0.8 |
1.5 |
3.1 |
4.1 |
6.4 |
Key:
|
typical EFI fuel pump |
|
typical high performance oil pump |
|
typical high performance power steering pump |
So, what can we learn from all this? First, it's important to note that the data presented is drawn from average data from available sources. It includes many assumptions and possible sources of errors, not the least of which is my extrapolation-by-eyeball from the pressure-drop chart. All told, the data should not be used for precise engineering of custom solutions. Rather, it is offered merely to illustrate the principles that affect selection of hose size regarding pressure drop. For example, notice that, for oil at 10 gpm, a 10" 1/2" hose could result in as much as 24 psi pressure loss, whereas increasing the hose size to 3/4" drops this loss all the way to a mere 3 psi! In short, it is a very long winded way of saying:
"Hose inside diameter can have a very big effect on pressure loss, especially at higher flow rates, and this effect is multiplied the longer the hose is"
Which is, in itself, a long-winded way of saying:
"Use the largest reasonable hose size you can afford, fit, tolerate the weight of, and for which the correct size hose-ends are made."
Although it would be great from a pressure-drop perspective, you probably want to avoid plumbing the entire car with 1" hose as it would be prohibitively expensive, needlessly heavy, very hard to install and route nicely, and would result in some god-awful multi-adapter / reducer contraptions to adapt the 1" hose to smaller ports on the car. Which brings us rather nicely to the rules of thumb:
Rule of Thumb Automotive Plumbing Hose Sizes
-04 |
¼” |
Small fuel lines,
gauges, brakes, vent, compressed air, and vacuum lines. |
-06 |
3/8” |
Fuel, transmission, hydraulic power, return lines, compressed air. |
-08 |
½” |
Oil, fuel, transmission, hydraulic power, return lines. |
-10 |
5/8” |
Oil, fuel, transmission, PS pump supply . |
-12 |
¾” |
Oil, fuel, transmission, PS pump supply, heater hoses. |
-16 |
1” |
Oil, PS pump supply, heater hoses. |
-32 |
2” |
Coolant. |
-40 |
2.5" |
Coolant. |
Typical OEM applications make extensive use of -04 and -06 hoses. High performance applications with higher flow and / or longer lines must use larger sizes accordingly. For example, the sizes I run on my rig are as follows:
-04 |
¼” |
Brakes, air lockers. |
-06 |
3/8” |
Fuel return, hydraulic steering power, hydraulic steering return lines.
Vent lines for axles, transmission, transfer case and fuel tank. |
-08 |
½” |
Fuel supply, transmission cooler. |
-10 |
5/8” |
Remote oil filter, oil accumulator, and oil cooler. |
-12 |
¾” |
PS pump supply. |
-40 |
2½” |
Coolant. |
All About Fittings
There are hundreds if not thousands of different fittings that exist amongst the pneumatics, hydraulics, and plumbing industries. However, there are only a couple of dozen that you are likely to run into in the automotive world and I’m only going to cover those most common in North America. I will not be covering brake fittings, metric, Japanese, European, sizes above 2”, specialized hydraulic, flanges, or quick-disconnect fittings.
Regardless of the style, any fitting must do two things:
- Hold the joined components securely together, and
- seal the fluid.
For all the fittings we shall discuss, the method of holding is via mechanical threads. That leaves the two major criteria that define a fitting as
- the style or type of threads used, and
- the method of sealing.
Threads are identified by their “form” and “series”. Male and female threads must be of the same form and series in order to screw together.
Methods of sealing are various, including by way of an O-ring, a soft sealing washer, machined metal-to-metal contact, or by interference fit of the threads themselves.
Threads and sealing methods may be combined in many different ways, but there are “most common” configurations – especially when confining our discussion to automotive-type fittings and plumbing.
For example, a common method of sealing for hydraulic fittings (and very likely to be found somewhere on off-road rigs with “full hydraulic steering” ) is the ORB or O-ring Boss. This style of fitting is available with UNF (aka SEA or standard or imperial or inch) threads, Metric (ISO 6149) threads, or BSPP (JIS B2351) threads – depending on, amongst other things, what part of the world you are in.
However, in North America, the ORB fitting is most often manufactured with UNF threads. As such, I shall list it and refer to it in this article in this configuration. Just be advised that it is possible to combine sealing methods and thread forms in combinations not shown here. In fact, there are several fitting specialty companies, especially those that deal with hydraulics and pneumatics, whose catalogues run to many hundreds of pages.
Essentially, for our purposes, and the purposes of this article, we will examine fittings as if certain threads are always combined with certain sealing methods – and this is certainly the case with 99% of those you’re likely to encounter, at least in North America. I just didn’t want to leave you with the impression that it always HAS to be that way.
Thread and Sealing Method Basics
Thread Basics
Since the threads are a major component of fittings, it behoves us to cover the basics to ensure a complete understanding. |
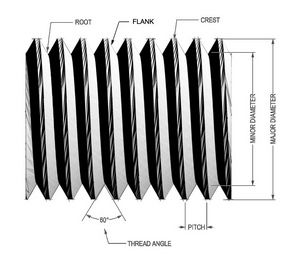 |
The basic parts and most important dimensions of a thread are illustrated in the diagram at left. A male thread is depicted, but the terms apply equally to female
threads.
The crest of a thread is the tip, the root of the thread is the bottom or valley between threads, and the flank of a thread is the “side” between the crest and root.
Thread pitch is the distance from a point on the thread to a corresponding point on the next thread measured parallel to the fitting’s axis. In other words, It is the distance between threads and is often expressed as the number of threads per inch.
The OD or major diameter is the largest diameter of a thread (measured across the crests of the thread)
The ID or minor diameter is the smallest diameter of a thread (measured across the roots of the thread).
The flank angle, also known as the “thread angle”, is the angle formed between two adjacent flanks.
The taper angle, for threads that are not parallel, is the angle at which the threads taper. |
Not all threads are made the same way. Different types of threads, or “thread forms”, will have different dimensions such as the flank angle used. Obviously it’s important to be able to distinguish between different threads so that we know what can be screwed into what. In order for threads to mate, they must be the same size, thread form and series, and have the same pitch (# of threads per inch).
Thread Form
The thread form is a the “group” to which particular threads belong based on a published industry standard that sets out the shape, dimensions, and tolerances for the formation of the threads. Examples of thread forms include:
- American National (obsolete).
- Unified National (UN) – unified Canadian/ US/ British standard, UN is the most common thread form used for inch-size (imperial or SAE) threads.
- Whitworth – British Standard (GB).
- National Pipe (NP) – US pipe thread standard.
Thread Series
Thread Series – often within a thread form, threads are grouped into series, based on their combination of size, pitch, and any taper (if applicable). For example, UNF stands for Unified National Fine and is a thread series within the UN thread form. Other common series include:
UN |
60° flank angle |
UNC |
UN coarse thread, common in nuts and bolts, not used in plumbing fittings. |
UNF |
UN Fine thread, very common in plumbing fittings. |
UNEF |
UN Extra Fine thread, used for short lengths of engagement or where a fitting screws into a thin-wall section. |
12-UN |
UN series where all threads have 12 TPI, regardless of their size (diameter) |
16-UN |
UN series where all threads have 16 TPI, regardless of their size (diameter) |
|
|
NP |
60° flank angle. |
NPT |
American National Standard Taper Pipe Thread |
NPTF |
Dryseal USA (American) Standard Taper Pipe Thread |
NPSM |
American National Standard Straight Pipe Thread for Free-fitting Mechanical Joints |
Whitworth |
55° flank angle. |
BSPT |
British Standard Pipe Thread - Taper |
BSPP |
British Standard Pipe Thread - Parallel |
Not all threads of a given form fit into a series. For example, a UN thread having ¾” diameter and 18 TPI is neither course thread (UNC series) nor fine thread (UNF series). Odd and special sizes such as these that do not fit into a series, if they are UN form, are referred to as UNS or Unified National Special.
Basically, for threads to thread together, they must have matching diameter and pitch (TPI), the “series” is just a convenient way of grouping threads. For example, one could refer to ‘¾” fine thread', or ' ¾” UNF’ instead of specifying ¾”-16 TPI; although it is always best practice to refer to any thread by its specific size and pitch.
Threads on Fittings
As mentioned, in order to function, fittings must accomplish two things – they must securely attach the components which they join, and they must seal the fluid they carry.
Fittings use threads for mechanical attachment, and one of a number of different sealing methods – including using the threads themselves.
That is to say, depending on the fitting, it will attach via threads and either seal also via the threads or seal by some other method. In other words, there are two broad groups of thread found on fittings: those that attach AND seal, and those that just attach. Threads that both attach and seal are tapered threads, and those that simply attach are parallel or “straight” threads.
There are three thread forms of interest to us in automotive plumbing – American National Pipe threads (NP), British Standard Pipe threads (BS), and Unified National (UN) threads. NP and BS threads have both a tapered and parallel thread variant, whereas all UN threads are parallel.
Tapered threads seal by means of an interference fit between the male and female threads. That is, as the threads are screwed together, metal deformation occurs between the threads and a metal-to-metal seal is achieved. However, tapered threads often use some supplement to this seal in the form of a sealing compound between the threads. The most commonly used is Teflon “plumber’s tape”. The purpose of the tape is actually two-fold.
First, it provides some “lubrication” between the male and female threads, reducing the amount of thread-galling that occurs as the threads are screwed together. This is particularly important if the threads are ever to be disassembled and re-used. |
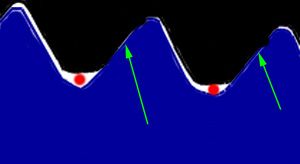 |
Secondly, in the case of some tapered threads, the seal is made when the flanks make contact (green arrows). In this case, there is a gap between the crest and roots of the male and female threads. This gap leaves a spiral leak path in the joint (red) which must be sealed by the use of a sealing compound such as Teflon tape. American NPT threads suffer from this problem. |
Normally, 2 to 3 turns of Teflon tape wrapped around the male thread before assembly is adequate. Liquid Teflon-based sealants are also used successfully to ensure a pressure tight seal. It is always important to use care when applying sealants to avoid introducing the sealant material into the system flow path. This is particularly true in critical hydraulic applications such as steering and braking systems where even a tiny piece of debris in the plumbing can block a crucial orifice or port, causing system failure.
NP Threads
NP threads are manufactured to various ANSI/ASME and SAE standards. There are both tapered and straight versions, however all NP threads have a 60° flank angle and have thread pitch measured in threads per inch. There are also a number of variants of NP threads. The two most important to us are:
NPT – American National Standard Taper Pipe Thread (ANSI B1.20.1).
NPT threads are by far the most common NP thread. They are tapered interference fit threads where the crests and roots of the threads are truncated (cut off) so that the flanks come into contact to form the seal. This results in a spiral leak path at the crests and roots and therefore a sealant compound or Teflon tape must be used for a leak-free seal. The threads have a taper of 1° 47' 24" or 1.7899°, meaning the thread tapers ¾” for every foot in length or 1 in 16. NPT threads have a 60° thread angle and the thread pitch is measured in threads per inch (TPI). Each thread size has a defined number of threads per inch. Both the TPI and OD of the thread are required for positive identification of thread size because more than one size has the same TPI.
Pipe thread sizes are nominal only – meaning they are a name only. The “size” does not refer to any physical dimension – not the thread size, fitting ID nor fitting OD. For example, a male ¾” NPT fitting has a thread OD of 1.05 inches. To identify an NPT fitting by thread size the thread OD and pitch must be measured and the results compared to a chart like those given later in this article. However, as a rule of thumb, for NP sizes up to 1-1/4”, you can measure the diameter of the threads and subtract 1/4" to get the nominal size. For example, subtract 1/4" from a 1" thread O.D. to obtain the nominal pipe size of 3/4".
You may also see the abbreviation NPT defined as:
- American Standard Pipe Taper Thread
- National Pipe Taper (American)
- National Pipe Thread Taper
- American Standard Taper Pipe Threads for General Use
In addition, NPT threads may also be referred to as:
- MPT - male (external) National Pipe Taper threads
- MPT - Male Pipe Thread
- MNPT – Male National Pipe Thread
- NPT(M) – National Pipe Thread, Male
- FPT - Female (internal) National Pipe Taper threads
- FPT - Female Pipe Thread
- FNPT – Female National Pipe Thread
- NPT(F) - National Pipe Thread, Female
- MIP - Male Iron Pipe
- FIP - Female Iron Pipe
- IPT – Internal (female) Pipe Thread
- EPT – External (male) Pipe Thread
- Pipe threads
NPTF - Dryseal USA (American) Standard Taper Pipe Thread (ANSI B1.20.3) aka American National Standard Taper Pipe Thread - Fuel
Because of the spiral leak path problem with NPT threads, some years ago the Society of Automotive Engineers in cooperation with industry set up a standard for improvement in pipe threads. This improvement is known as the Dryseal Pipe Thread. With this thread design, there are controls on the crests and roots of both the male and the female threads to ensure the crest crushes into the root of the mating thread. The interference fit between the crest of one thread and the root of the other, along with the thread flanks matching, seals against spiral leakage.
Apart from this design improvement NPTF threads share remaining characteristics with NPT threads and will appear identical to the naked eye.
If both male and female threads are NPTF, strictly speaking thread sealant is not required to form a leak-free seal on first assembly (although it usually is on subsequent assemblies). This can be an advantage in applications where there is a risk of contaminating the fluid with extraneous thread sealant or bits of Teflon tape. However, in any tapered interference-fit thread, if possible, it is still a good idea to use some sealant to lubricate the threads and minimize galling.
Although not ideal, NPT and NPTF threads can be combined, but sealant will be required.
There are also a large number of other specialized NP thread variants in use - although rarely in the automotive industry. I list them here only so you may recognize what they are if you should come across them.
- NPSM – American National Standard Straight Pipe Thread for Free-fitting Mechanical Joints – Used where a straight thread for mechanical assembly would be more suitable or convenient than a tapered thread.
- NPTR - American National Standard Taper Pipe Thread for Railing Joints
- NPSC - American National Standard Taper Pipe Thread for Couplings
- NPSL - American National Standard Straight Pipe Thread for Loose-fitting Mechanical Joints with Locknuts
- NPSH - American National Standard Straight Pipe Thread for Hose Couplings
- NPSF – Dryseal USA (American) Standard Fuel Internal Straight Pipe Thread
- NPSI - Dryseal USA (American) Standard Intermediate Internal Straight Pipe Thread
- PTF-SAE SHORT – Dryseal SAE Short Taper Pipe Thread
- PTF SPL Short – Dryseal Special Short Taper Pipe Thread
- PTF SPL Extra Short - Dryseal Special Extra Short Taper Pipe Thread
- F-PTF – Dryseal Fine Taper Thread Series
- SPL-PTF – Dryseal Special Diameter-Pitch Combination Series
- ANPT - Aeronautical National Taper Pipe Threads - NPT threads manufactured to aerospace standard in accordance with the MIL-P-7105B / SAE AS71051. Essentially NPT threads that have undergone extensive gauging, testing, sampling, Non-Destructive testing (NDT) and other quality control procedures.
- API - American petroleum Institute - functionally identical to Dryseal NPTF threads.
British Standard (BS) Pipe Threads
BSP threads are of the Whitworth thread form. This thread form differs from both NP and UN threads by its use of a 55° flank angle (versus the 60° flank angle used on the NP & UN threads). Because of this difference, the thread forms are NOT interchangeable. The Whitworth thread form is common for pipe fittings in countries that otherwise use metric threads. BSP threads are rounded equally at the crests and roots.
There are two forms of British Standard Pipe Threads in use today - BSPT (British Standard Pipe Tapered) and BSPP (British Standard Pipe Parallel).
BSPT threads are a tapered interference fit, similar to NPTF threads, and also have a taper of 1° 47' 24" or 1.7899°, meaning the thread tapers ¾” for every foot in length or 1 in 16.
BSPT threads are also referred to as “R series threads”, the R coming from the German word “Rohr”, for pipe. As such, frequently BSPP threads are designated by the letter R for external (male) taper threads or the letters Rc for internal (female) taper threads, followed by the nominal pipe size in inches, such as:
R-1/2 or
Rc-3/4 or sometimes
½- R
Although you may also see the designation include the thread pitch in TPI, as in:
R-1/2-14
BSPT threads may also be referred to as:
- British Standard Taper Pipe or Pipe Taper or Conical Thread.
And / or be designated by the symbology:
BSPP threads are parallel threads and therefore require a separate sealing system apart from the threads. The male BSPP fitting has a 30° flare that mates with a matching female BSPP 30° cone, although frequently an additional sealing ring or washer is used to achieve a pressure-tight seal.
BSPP threads are also referred to as “G series threads”, the G coming from the German word “Gaz”, as the threads were originally designed for gas pipe. As such, frequently BSPT threads are designated by just the letter G, followed by the nominal pipe size in inches, such as:
G-1/2, or sometimes
½- G
Although you may also see the designation include the thread pitch in TPI, as in:
G-3/8–19
BSPP threads may also be referred to as:
- British Gas or British Pipe Parallel or Parallel Fastening thread.
And / or be designated by the symbology:
- BSP or BSSPI or BSPF or BSPG or PS or Rp – internal (female) parallel or Rs – external (male) parallel.
A BSPT male can be screwed into a BSPP female, but not the other way around.
British Pipe thread sizes
There are 16 thread sizes defined by the standards, ranging from 1/16” to 6”. The size number was originally based on the inner diameter measured in inches of a steel tube for which the thread was intended, but is simply a nominal size number in the modern version of the standard.
UN Threads
All UN threads used on plumbing fittings are parallel threads and only serve the function of attaching the fitting. Sealing is achieved by some other means, such as with an O-ring or machined surface.
UN threads have a 60° flank angle and are grouped into thread series based on pitch. The following UN thread series are common in automotive plumbing fittings:
UN Fine thread, very common in plumbing fittings. |
UN Extra Fine thread, used for short lengths of engagement or where a fitting screws into a thin-wall section. |
UN series where all threads have 12 TPI, regardless of their size (diameter) |
UN series where all threads have 16 TPI, regardless of their size (diameter) |
UN Special – for threads that do not fit into other UN series |
Thread Class
UN threads are also grouped by “thread class”. Thread classes are based on the amount of tolerance and allowance permitted in the manufacture of the threads. The higher the class, the tighter the tolerance. Classes are assigned a numeral, followed by the letter A for external threads or the letter B for internal threads, as follows:
Class 1A/1B – Designed for ordnance and other special uses, class 1 threads have large tolerances & allowances to permit quick and easy assembly, even with dirty or slightly damaged threads.
Class 2A/2B – Designed for most general commercial and industrial uses including nuts, bolts, and fittings. Class 2 threads are by far the most common and 99% of the threads you encounter are likely to be class 2.
Class 3A/3B – Designed for use where closer tolerance than afforded by class 2 threads is desired. Class 3 threads are such that the upper end of the male tolerance and the lower end of the female tolerance would produce threads with no clearance for assembly. Class 3 threads are uncommon and can be difficult to do up, especially if not perfectly clean.
Bottom line – most UN threads you will encounter are class 2.
UN Thread Sealing Methods
The various sealing methods used with UN thread fittings include:
- Metal-to-metal conical seal
- O-ring
- Fibre, plastic, copper, rubber-coated steel, or other elastomeric washer
The sealing method for each of the most common automotive plumbing fittings are detailed below in the sections on the individual fitting styles.
Drilling & Tapping
While this article is not intended to be a technical treatise on the fine art of drilling for and tapping threads, information is provided should you need to drill and tap a hole for a fitting for some reason. Of course, because all straight threads found on fasteners require some sort of sealing method other than the threads, unless you are capable of machining the appropriate surface or chamfer for an O-ring or soft sealing washer or the like, most home-brew tapping for plumbing fittings is probably best confined to the tapered thread forms (NPT / NPTF / BSPT). That said, if it is a low pressure non-critical function you have in mind (such as a vent port for an axle or transmission), and you don’t want to use a tapered thread form (and who can blame you!) you can use the information provided to, for example, drill and tap an ORB fitting hole in an axle housing and then use an ORB to AN / SAE 37° fitting in the hole allowing you to run a hose with AN fittings on it. The advantage to this over tapered threads is that you are likely to already have many more UN taps than NP taps. Of course, if you’re stuck, you could also always use the information provided to decide what chance of success you might have of ramming two mismatched fittings together…not that I would EVER do that ;-)
The recommendations given in the tables in this article for min and max hole sizes and the accompanying drills to be used for drilling holes to be tapped are based on the following assumptions, guidelines, and rules-of-thumb:
- Generally, to avoid breaking taps, one uses the largest hole size possible that can be tapped to create the desired thread.
- Thread Depth of 65-75%. Thread Depth is the amount by which mating threads engage each other or “overlap”. Too little thread depth results in weak and insecure thread engagement. Too much results in hard to assemble parts (especially when dirty or worn) and a real risk of braking taps when cutting the threads. Test have shown little strength increase in the threads over about 60% thread depth, although 65-75% is very commonly used for a small extra measure of safety. Obviously, for a given thread size/pitch, the larger the hole drilled, the less thread depth will result.
- Depth of Engagement. The size of the hole required depends on the depth of engagement of the threads, or how much is the fitting going to be threaded into the tapped hole. The basic premise is to avoid tapping a thread that will strip too easily. Therefore, the greater the depth of engagement, the more resistance there is to stripping, and the larger the hole can be. Conversely, fittings threaded into thin wall sections require smaller holes be tapped so that risk of stripping is minimized. Depth of engagement is normally expressed as a fraction or percentage of the fitting’s diameter (D). This article assumes a depth of engagement of 2/3D to 1-1/2D.
- Thread Class. Obviously, the tighter the tolerances imposed by the thread class, the tighter the tolerances of the tapped hole must be, and therefore the smaller the drilled hole must be. Generally holes required for class 3b threads will be smaller than those required for class 1B / 2B threads. This article assumes class 2B threads are in use.
Once the hole size for the tapping has been calculated by considering the thread depth, depth of engagement, thread class, the material to be tapped, and the type of tap to be used – you still need to actually drill the hole; and as such are limited by the size of drills available to you. These variables are the reason that a range of hole sizes and accompanying drill sizes are given in the tables later in the article (these hole-size and drill-size listings are included with the data tables for each type of fitting).
Where two drill sizes are given, I normally use the smaller size:
- if the strength of the assembly is critical; and
- if there is a risk of the fitting stripping during service; and
- if access to the hole is easy (and therefore extracting a broken tap is possible / easy); and
- if the material being tapped is not too hard; and
- The fitting is less than 1” in diameter; and
- the assembly rarely needs to be disassembled (i.e. the fitting unscrewed from the tapped hole) ; or
- the length of the tapped threads will be less than 2/3 the diameter of the fitting threads; or
- I’m using old, worn-out drills or I suspect some other part of the tool or process I’m using will tend to increase the amount by which drills tend to over-size holes above the average of 2-8 thou.; or
- there is no larger size given
Otherwise I would use the larger of the two drill sizes given.
Plumbing Sizing
Sizing hose, tube, and fittings can be a little confusing for the beginner. This is because the nominal size rarely, if ever, corresponds to an actual measurable dimension. This seems counterintuitive at first, but actually simplifies things once you understand the systems.
Nominal sizes refer to the named size – i.e. the size that would be printed on the package or stamped on the fitting. The most important thing to understand is that these nominal sizes are a close approximation to the tube or bore size of the plumbing component in question and NOT the thread size.
For example, a ½” fitting, whether it be NPT, AN/SAE 37, SAE 45° flare, or ORS (O-ring Face Seal) has an ID or bore of “approximately” ½”. The actual ID or bore will be something less than ½”, but it will be close. Depending on the style of fitting, the THREAD size of a ½” fitting may range from ¾” to 13/16”. Actual thread sizes can be measured to aid in the identification of fittings, as will be explained shortly, but again the important point here is that a ½” fitting will not have any dimension that is actually ½”. The same is true for hose and tube. A ½” hose will have an OD greater than ½” and an ID somewhat smaller than ½”. For example, ½” Russell performance Proflex hose has an ID of 7/16” and an OD of 5/8”. Other brands of ½” hose may well have different precise dimensions, depending on the construction method. The same is true for different brands or styles of fittings – they may well have slightly different bore diameters.
Imagine the headache if you had to measure, verify, and match all those different dimensions in order to design and construct a plumbing system! This is where the advantage of a “nominal” system comes into play. Regardless of the manufacturer in questions, as long as the hose and fittings in question are designed to be used together, it doesn’t much matter what the precise dimensions are – a ½” hose is a ½” hose and would be used with a ½” fitting – be that fitting AN, NPT, or SAE 45° flare.
AN or Dash Sizing
The AN (Army-Navy) standard was established many years ago by the U.S. military to set a common system for designating the size of hose and fittings. The system is based on the nominal outside diameter (O.D.) of the ridged metal tube that is compatible with each size of fitting – the same as “inch sizing” that we have just discussed. The only difference is, AN sizes always refer to the size in sixteenths of an inch, and are expressed as a dash, followed by a two digit number. For example, AN size -08 translates to 8 sixteenths of an inch or ½”. The system is so convenient and simple to use that it is often used with hose and fittings that are not AN standard, and as such is sometimes referred to as “dash sizing” because of the dash in the designation.
To convert from dash sizing to inch sizing, simply place the dash number over a denominator of 16 and reduce the fraction as required. The following table shows the conversion for most common sizes.
-02 |
1/8” |
0.1250" |
-03 |
3/16” |
0.1875" |
-05 |
5/16” |
0.3125" |
-07 |
7/16” |
0.4375" |
-09 |
9/16” |
0.5625" |
-14 |
7/8” |
0.8750" |
-18 |
1.1/8” |
1.1250" |
-20 |
1.1/4” |
1.2500" |
-24 |
1.1/2” |
1.5000" |
-32 |
2” |
2.0000" |
The most commonly used size for hose and fittings in automotive plumbing are indicated in the table in bold text.
Let’s have a look at some universal fitting tech, and then finally get into the details of each of the most common types of fittings in automotive plumbing.
Fitting Construction - aluminum vs steel vs brass
Fittings are commonly constructed of steel, brass, or aluminum. |
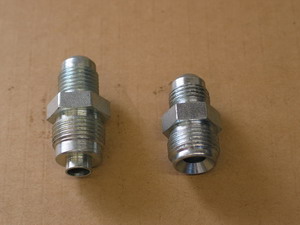 |
Steel – strong, hard, heavy, susceptible to corrosion if not plated. As steel is much harder than brass or aluminum, use of steel tapered threads joined to any other metal can lead to problems like port cracking. For example, I wouldn’t thread a steel male tapered pipe thread into an aluminum female port for risk of cracking the aluminum. |
|
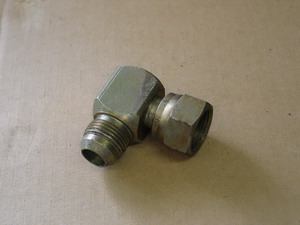 |
Brass – Strong, very heavy, softer than steel, tapered threads tend to gall and deform easily. Mostly used in industrial / hydraulic applications. |
|
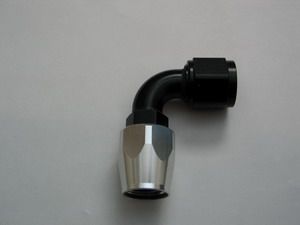 |
Aluminum – strong, corrosion resistant, lightweight, good compromise between thread strength and softness giving low risk of assembly damage and good ability to be disassembled and reassembled. |
Crimp vs field attachable vs hose barb (Twist-Lok)
Hose-ends can be attached to hose by one of three methods |
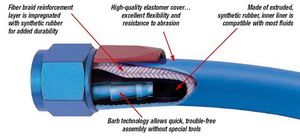 |
Hose Barb – for use only with low pressure hose. Easy to make custom-length hose assemblies at home. Newer, high-quality systems like Russell’s Twist-Lok system do not require any hose clamps. Because of the tight one-way union between barb and hose, removal of hose-end from hose often requires cutting the hose, shortening the length of the hose and making reassembly problematic. |
|
 |
Crimp – crimped hose-ends, if done using the proper equipment by trained personnel, offer very secure and reliable connections. The disadvantages are that you must know the exact length of the required hose assembly before ordering, they cannot be easily made at home without expensive equipment, and they are not field serviceable – if a hose-end fails the entire hose assembly must be replaced. |
|
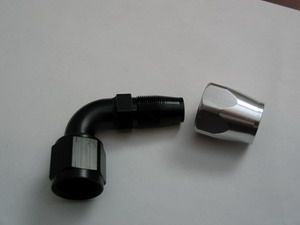
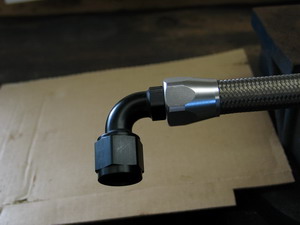
|
Field Attachable – also known as "socket hose-ends" or "reusable hose-ends", this style of hose-end is easily attached to the hose at home. The advantages are:
- it is easy to make truly custom-length hose assemblies in place on the car, leading to the cleanest installation and no wasted hose.
- Finished hose assemblies are equal in performance to crimped-end hose assemblies.
- No special tools or equipment required for attaching the hose-ends to the hose.
- If a hose-end or hose should fail in the field, an entirely new hose assembly can be constructed and installed trailside or track side.
|
Swivel or not?
Once you have decided on a hose-end style, material, and hose attachment style, the only choice remaining is whether or not to use a swivel hose-end or not. For example, suppose you have chosen to use an AN/SAE 37° hose-end style in field-attachable aluminum. This type of hose-end is available in both regular and swivel styles. Both styles can be rotated at the hose-end to adapter point to allow the hose to be oriented as required on installation simply by holding the hose in place as the nut is tightened. However, a swivel hose-end is also able to rotate freely at the hose-end to hose joint after installation. This means the hose can be rotated (or is free to swivel along its length - around its longitudinal axis) after assembly. The benefits are that swivel hose-ends are more easy to install since the hose can swivel after the hose-ends are tightened, which can considerably ease routing the hose. However, the most important advantage is that, since it is able to rotate or swivel in service, a swivel hose-end can prevent unnecessary twisting loads on the hose assembly during use. This can be very important since twisting forces can lead to significantly reduced hose life or hose failure. The disadvantage to swivel hose-ends is the increased cost and the addition of an additional potential failure point in the swivel mechanism. The decision on which to use is best left to particular installation conditions in consideration of the mechanical loads on the hose assembly in service. |
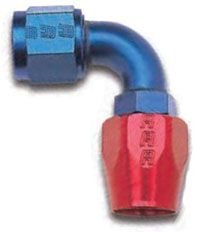 |
Standard hose-end fitting. |
|
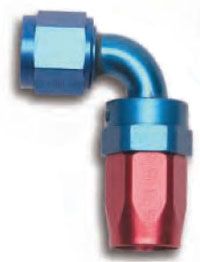 |
360°swivel hose-end fitting.
Note the swivel assembly above the red socket. |
Fitting / Thread Examination
In this section I will detail each of the most common style of fittings found in automotive plumbing. In the diagrams, I have tried to indicate the actual sealing surfaces in red. To the uninitiated, some of the naming conventions can be confusing. For example - what is the difference between an SAE 45° Flare and an SAE 45° Inverted Flare - and how can I remember them and identify them later by sight? In this regard I find it helpful to think in terms of the female (internal thread) fitting or seat. That is, if you look at SAE 45° Flare fittings, the female seat is either flared tube, or a machined seat the same shape as flared tube - that is, the female sealing surface is concave or "flared" in shape. On the other hand, if you look at SAE 45° Inverted Flare fittings you find that the female (internal thread) sealing surface or seat is a convex, conical shape - i.e. it is the opposite of a flare - an "inverted flare." In other words - "flare" fittings have a female fitting the sealing surface of which is concave or "flared" in shape and a male fitting the sealing surface of which is convex or "cone" in shape. "Inverted flare" fittings are the opposite - the female is convex or "inverted flare", the male is concave or "flared".
The pressures listed below for the different style fittings are intended as rough guide for comparative purposes between the different fitting styles only. They are not intended to indicate a design specification, safe working pressure, standard or guaranteed capability. This is because there are many factors that influence the pressure at which a hydraulic or plumbing system will or will not perform satisfactorily. For example, torque settings,
size (bore), length, flow, fluid velocity, assembly procedures, material, construction, alignment, support, pressures (internal and external), temperature limits, environmental, installation, vibration,
damage, chemical exposure and resistance, cleanliness and regular maintenance all affect specific
allowable working pressures. The actual numbers below are taken from a single manufacturer's listings for -08 fittings under ideal conditions. Again, they are simply a comparative guide. Finally, note that, on the whole, virtually any fitting's actual pressure rating is likely to be far in excess of any automotive needs.
AN / SAE 37
Army-Navy / Society of Automotive Engineers 37° Flare
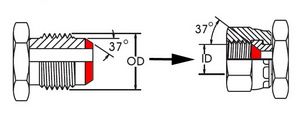 |
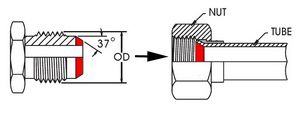 |
Threads |
UN thread form, 60° flank angle, straight (parallel) threads. UNF & 12-UN Thread Series, depending on size. |
Sealing Method & Material |
Metal to metal contact seal between male cone and female flare (conical seat). |
Sealing Surface Angle |
37° |
Typical Applications |
Hydraulics, aerospace, racing and performance automotive, industrial instrumentation and chemical processing systems. |
Used in |
Hose-ends / adapters / unions |
Pressure |
7000 psi |
Vibration |
Good vibration resistance |
Advantages |
- Easy to assemble.
- Fittings and hose-ends can easily by oriented and held in position while threads are tightened.
- Available in field attachable.
- No supplemental sealing compound required.
- Can be disassembled and reassembled many times without damage and no loss of sealing.
- Huge number of high quality fittings and styles available from Russell Performance.
|
Disadvantages |
- Few, if any, ports are AN / SAE 37° so normally some form of adapter is required to convert AN / SAE 37° hose-ends to the port style in question.
|
Standards |
SAE J514 / ISO 8434-2 |
Also Known As |
JIC, JIC 37°, 37° Flare |
Interchange |
SAE 37°and JIC 37° interchange completely. AN fittings interchange but are of higher rating / quality. |
This style of fitting goes by several names. Originally it was designed by the US military as part of the AN standard and so became known as AN style fittings. Later, for industrial and hydraulic use, the Joint Industry Council (JIC) developed a standard based on the same style and it was know as JIC 37 (the 37 for the angle of the taper on the fittings). The JIC is no longer in existence today (although the name persists in the hydraulics world) and the standard was taken over by the SAE, and thus it is properly known today as the SAE 37 fitting.
Note that AN and SAE 37 fittings are not identical, although they use the same style fittings. Strictly speaking, in order to be designated AN, all types of hardware, including fittings, must undergo much stricter quality control and testing procedures than their SAE counterparts. Despite this, the designation AN has become synonymous with both dash sizing and 37° flare fittings and so you will likely see it referred to a lot, even if the products in question are not actually AN spec components. |
AN / SAE 37 Data Table
AN Size (1) |
SAE size (2) |
Threads (3) |
Thread
Series (4) |
Thread OD
(inches) (5) |
Thread ID
(inches) (6) |
Min Torque
(ft/lbs) (7) |
Max Torque
(ft/lbs) (8) |
Hex (9) |
Min hole
(inches) (10) |
Min
Drill (11) |
Max hole
(inches) (12) |
Max
Drill (13) |
-02 |
1⁄8 |
5/16 - 24 |
UNF |
0.31 |
0.27 |
6 |
7 |
2 |
0.272 |
I |
0.277 |
J |
-03 |
3⁄16 |
3/8 - 24 |
UNF |
0.38 |
0.33 |
8 |
9 |
2 |
0.335 |
Q |
0.340 |
R |
-04 |
1⁄4 |
7/16 - 20 |
UNF |
0.44 |
0.39 |
11 |
12 |
2 |
0.389 |
25/64 |
0.395 |
X |
-05 |
5/16 |
1/2 - 20 |
UNF |
0.50 |
0.45 |
14 |
15 |
2 |
0.452 |
29/64 |
0.457 |
- |
-06 |
3/8 |
9/16 - 18 |
UNF |
0.56 |
0.51 |
18 |
20 |
1.1/2 |
0.509 |
- |
0.515 |
33/64 |
-08 |
1/2 |
3/4 - 16 |
UNF |
0.75 |
0.69 |
36 |
39 |
1.1/2 |
0.689 |
11/16 |
0.696 |
- |
-10 |
5/8 |
7/8 - 14 |
UNF |
0.88 |
0.80 |
57 |
63 |
1.1/2 |
0.806 |
51/64 |
0.814 |
13/16 |
-12 |
3/4 |
1.1/16 - 12 |
12-UN |
1.06 |
0.98 |
79 |
88 |
1 |
0.981 |
63/64 |
0.990 |
1 |
-14 |
7/8 |
1.3/16 - 12 |
12-UN |
1.19 |
1.11 |
94 |
103 |
1 |
1.106 |
1.7/64 |
1.115 |
1.1/8 |
-16 |
1 |
1.5/16 - 12 |
12-UN |
1.31 |
1.23 |
108 |
113 |
1 |
1.231 |
1.15/64 |
1.240 |
1.1/14 |
-20 |
1-1/4 |
1.5/8 - 12 |
12-UN |
1.63 |
1.54 |
127 |
133 |
3/4 |
1.544 |
- |
1.553 |
1.9/16 |
-24 |
1-1/2 |
1.7/8 - 12 |
12-UN |
1.88 |
1.79 |
158 |
167 |
3/4 |
1.794 |
- |
1.803 |
1.13/16 |
-32 |
2 |
2.1/2 - 12 |
12-UN |
2.50 |
2.42 |
245 |
258 |
3/4 |
2.419 |
- |
2.428 |
2.7/16 |
- AN "dash" size (in sixteenths of an inch).
- Inch size equivalent, based on (nominal) Tube OD or Hose ID.
- Actual thread size and pitch.
- UN Thread Series.
- Male thread major diameter (OD).
- Female thread major diameter (ID).
- Minimum torque in ft/lbs – note torque values are approximate and will vary depending on coating, cleanliness, and condition of threads.
- Maximum torque in ft/lbs – note torque values are approximate and will vary depending on coating, cleanliness, and condition of threads.
- Number of hex turns from finger tight – alternative tightening spec when torque wrench not practical.
- Minimum size hole to drill for tap (inches) assuming 75% thread depth, class 2B threads, & fitting thread depth of engagement ranging from 1/3 the diameter of the fitting to 1.5 times the diameter of the fitting.
- Nearest drill bit size corresponding to the min size hole.
- Maximum size hole to drill for tap (inches) assuming 75% thread depth, class 2B threads, & fitting thread depth of engagement ranging from 1/3 the diameter of the fitting to 1.5 times the diameter of the fitting.
- Nearest drill bit size corresponding to the max size hole.
|
NPT / NPTF
NPT – American National Standard Taper Pipe Thread
NPTF - Dryseal USA (American) Standard Taper Pipe Thread aka American National Standard Taper Pipe Thread - Fuel
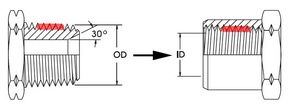 |
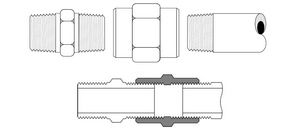 |
Threads |
NP thread form, 60° flank angle, tapered threads. Thread taper is 1° 47' 24" or 1.7899°, or ¾” per foot (1 in 16). |
Sealing Method & Material |
Interference fit of tapered threads:
NPT - at flanks, thread sealant (Teflon tape) must be used.
NPTF - at crests and roots of threads. No sealant required for first assembly. |
Sealing Surface Angle |
N/A |
Typical Applications |
Hydraulic systems, grease systems, and practically all plumbing |
Used In |
Hose-ends / adapters / unions (pipe nipples) / port fittings |
Pressure |
5000 psi |
Vibration |
Fair vibration resistance. |
Advantages |
- Extremely common & readily available.
- Easy to drill and tap ports for, without having to machine a surface or location for a sealing washer or O-ring.
|
Disadvantages |
- Supplemental sealant required for NPT.
- Some risk of sealant contaminating fluid system for NPT.
- Tapered threads act as mechanical jack and can crack cast housings when over-tightened.
- Difficult to establish accurate torque ratings due to tapered threads.
- No swivel-action on assembly.
- Shaped fittings such as elbows and Tees can be difficult to tighten so that they are both correctly oriented and tightened sufficiently to seal.
- Poor disassembly / reassembly performance due to inerrant thread damage.
- Any side-load on fitting will cause leaks.
- Can be easily cross-threaded on assembly without realizing it as user assumes tightness is due to tapered thread instead of correctly identifying a cross-threaded condition.
- Few options available as hose-ends from high performance aftermarket.
|
Standards |
NPT - ANSI/ASME standard B1.20.1 NPTF - ANSI B1.20.3 / SAE J476 |
Also Known As |
NPT - Pipe Thread NPTF - Dryseal, Dryseal Pipe Thread (also see discussion above on thread forms) |
Interchange |
NPT male can be screwed into:
- NPT female - thread sealant required.
- NPTF female - thread sealant required.
- NPSM female (not ideal) - thread sealant required.
- NPSF female (not ideal) - thread sealant required.
NPTF male can be screwed into:
- NPTF female - NO thread sealant required.
- NPT female - thread sealant required.
- NPSF female - NO thread sealant required.
NPT/F threads are not compatible with BSP threads as the flank angle is different (60° vs. 55°) and most of the sizes have different thread pitch. However, the 1/2" and 3/4" sizes have the same pitch (all are 14 TPI) and can be used together in a pinch with enough thread sealant.
PTF-SAE Short, PTF SPL Short, and PTF SPL Extra Short male threads can be used with their corresponding female threads, or with NPTF, NPSF, & NPSI internal (female) threads.
PTF series threads are identical to NPTF threads except that one or more thread turns has been eliminated on the small end of the external thread.
The NPSI thread is very similar to the NPSF thread but is designed for use in less resilient materials. |
NPT/F fittings are widely used in many industries to convey everything from air to steam to hydraulic fluid and as such are available in steel, brass, aluminum, as well as PVC, nylon, bronze and cast iron. Only the first three are suitable for automotive plumbing use.
Despite their popularity, they are far from ideal, as evidence by the long list of disadvantages given above. However, the fact that the threads do double duty as both mechanical attachment and sealing method makes them cheap and easy to use. It is particularly easy to drill and tap NPT ports compared to other fitting styles. For this reason, you are very likely to find many NPT connections on your car - for example, in oil coolers, transmission cases, engine blocks, manifolds, and many others.
However, because of the difficulty in simultaneously aligning and tightening the fitting to seal, I avoid NPT hose-ends like the plague. Where I have NPT ports, my preference is to use a quality NPT to AN / SAE 37 adapter screwed into the port with Teflon tape, and then use hose assemblies with AN / SAE 37 hose-ends. |
NPT / NPTF Data Table
AN Size (1) |
SAE size (2) |
Threads - nominal
(3) |
Threads - actual
(inches) (4) |
Thread (OD)
(inches) (5) |
Thread (ID)
(inches) (6) |
Drill (7) |
-02 |
1⁄8 |
1/8 - 27 |
3/8 |
0.41 |
0.38 |
R |
-04 |
1⁄4 |
1/4 - 18 |
1/2 |
0.54 |
0.49 |
7/16 |
-06 |
3/8 |
3/8 - 18 |
5/8 |
0.68 |
0.63 |
37/64 |
-08 |
1/2 |
1/2 - 14 |
3/4 |
0.84 |
0.77 |
23/32 |
-12 |
3/4 |
3/4 - 14 |
1 |
1.05 |
0.98 |
59/64 |
-16 |
1 |
1 - 11.1/2 |
1-3/8 |
1.32 |
1.24 |
1.5/32 |
-20 |
1-1/4 |
1.1/4 - 11.1/2 |
1-5/8 |
1.66 |
1.58 |
1.1/2 |
-24 |
1-1/2 |
1.1/2 - 11.1/2 |
1-7/8 |
1.90 |
1.82 |
1.47/64 |
-32 |
2 |
2 - 11.1/2 |
2-3/8 |
2.38 |
2.30 |
2.7/32 |
- AN "dash" size (in sixteenths of an inch).
- Inch size equivalent, based on (nominal) Tube OD or Hose ID.
- Nominal thread size and pitch.
- Actual thread size - approximate. For sizes up to 1", add 1/4" to nominal thread size to get actual size of threads and vice versa.
- Male thread major diameter (OD).
- Female thread major diameter (ID).
- Drill bit size for appropriate tap.
There are no published standard torque values for tightening NPT / NPTF fittings. This is because, with tapered threads, the torque required for a secure, leak-free, reliable joint varies with thread quality, condition, cleanliness, port & fitting materials, and the sealant used.
So how tight do you do it up?
There are a few different methods that are commonly used, you will have to select one appropriate to your situation:
By Torque Spec
Despite what I just said, you may find a torque value given for the components you are using. If you do, and you can fit a torque wrench, go ahead and use the value given. Just be aware of the following pitfalls:
- a fitting that is out of spec and bottoms out in the port before reaching torque.
- a fitting that still leaks even though you have applied the specified torque.
- a fitting that is left pointing in the wrong direction after you reach the specified torque.
By Feel
Many experienced mechanics will simply tighten NPT/F fittings until they “feel right”. When backed up by a proper leak-test under safe conditions prior to being put into service, this is a perfectly acceptable method – once you have the experience and have developed the feel. When screwing the fitting in, start by hand, the fitting should gradually get tighter. When you tighten by wrench, the torque should continue to rise smoothly. If it suddenly gets tighter, you may have bottomed the fitting. If it suddenly gets looser you may have stripped the threads and will now want to curse and wish you had selected a different method. Be careful of over tightening fittings into aluminum castings as the tapered threads act as a mechanical jack and can crack the casting – particularly if the thread sealant in use acts as a lubricant which will tend to mask over-tightening until it’s too late.
By Engagement Length
For each size pipe fitting there are two specified distances. The first is the “length of engagement” which is the linear distance along the thread, or number of turns, that the fitting should be able to be screwed in by hand. The other spec is called the “length of effective seal” and is the linear distance along the thread required to achieve a leak-free seal. The table below gives examples. By examining the table and doing some math, we can calculate how many turns, first by hand, then by wrench, that it takes to screw the fitting in a distance equal to the total “length of effective seal”.
Nominal Pipe Size |
Length of Engagement
(tightened by hand) (inches) |
Effective Thread
(inches) |
1/8 |
0.124 or approx. 3.3 turns |
0.260 |
1⁄4 |
0.172 or approx. 3.1 turns |
0.401 |
3/8 |
0.184 or approx. 3.3 turns |
0.408 |
1/2 |
0.248 or approx. 3.4 turns |
0.534 |
3/4 |
0.267 or approx. 3.7 turns |
0.546 |
1 |
0.313 or approx. 3.6 turns |
0.682 |
The problem with this method is two-fold. First, it’s too damn complicated. Second – the real world never seems to play nicely with theoretical standards. For all the same reasons listed as to why torque specs are difficult to give, real-world fittings rarely screw in by hand the distance or number of turns the spec says they should. However, this theory does lead to a rule-of-thumb that is probably the best method for tightening NPT/F fittings – that method is the "number of rotations" method.
By Number of Rotations
As a general guideline, after hand-tight engagement, tighten 2-3 full turns for sizes up to 1 inch for NPT/F fittings. You should have between 3.5 and 6 engaged threads. Any number outside of this range may indicate either under or over tightening of the joint or out of tolerance threads. On all shaped fittings, such as elbows and tees, tighten approximately 2 turns past finger tight and orientate the fitting on the third turn. Never back off the thread to orient the fitting after completing the tightening process, as this may cause the fitting to leak.
|
NPSM
American National Standard Straight Pipe Thread for Free-fitting Mechanical Joints
Threads |
NP Thread Form, 60° flank angle, straight (parallel) threads. |
Sealing Method & Material |
Metal-to-metal seal between male flare and female cone; or
Soft sealing washer of plastic, copper, rubber coated steel, etc. |
Sealing Surface Angle |
30° for cone & seat, flat for washer-style. |
Typical Applications |
Hydraulic and plumbing systems. |
Used In |
Port fittings / adapters. |
Pressure |
5000 psi. |
Vibration |
Fair vibration resistance. |
Advantages |
- No thread sealant required, no chance of thread sealant fouling fluid system.
- Straight threads less susceptible to galling on assembly than tapered threads.
|
Disadvantages |
- Uncommon.
- Sealing surfaces for washer must be flat and true.
- Not available as hose-ends from high performance aftermarket.
|
Standards |
ANSI/ASME B1.20.1 |
Also Known As |
American National Standard Straight Pipe Thread
Straight Pipe Threads for Mechanical Joints
Free-Fitting Mechanical Joints for Fixtures |
NPSM Data Table
AN Size (1) |
SAE size (2) |
Threads (3) |
Thread
Series (4) |
Thread OD
(inches) (5) |
Thread ID
(inches) (6) |
Drill (7) |
-02 |
1⁄8 |
1/8 - 27 |
NPS |
0.41 |
0.38 |
S |
-04 |
1⁄4 |
1/4 - 18 |
NPS |
0.54 |
0.49 |
29/64 |
-06 |
3/8 |
3/8 - 18 |
NPS |
0.68 |
0.63 |
19/32 |
-08 |
1/2 |
1/2 - 14 |
NPS |
0.84 |
0.77 |
47/64 |
-12 |
3/4 |
3/4 - 14 |
NPS |
1.05 |
0.98 |
15/16 |
-16 |
1 |
1 - 11.1/2 |
NPS |
1.32 |
1.24 |
1.3/16 |
-20 |
1-1/4 |
1.1/4 - 11.1/2 |
NPS |
1.66 |
1.58 |
1.33/64 |
-24 |
1-1/2 |
1.1/2 - 11.1/2 |
NPS |
1.90 |
1.82 |
1.3/4 |
-32 |
2 |
2 - 11.1/2 |
NPS |
2.38 |
2.30 |
2.7/32 |
- AN "dash" size (in sixteenths of an inch).
- Inch size equivalent, based on (nominal) Tube OD or Hose ID.
- Actual thread size and pitch.
- Thread series.
- Male thread major diameter (OD).
- Female thread major diameter (ID).
- Drill bit size for appropriate tap.
|
SAE ORB / UNO
Society of Automotive Engineers O-ring Boss / Unified National O-ring
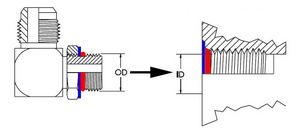 |
Threads |
UN thread form, 60° flank angle, straight (parallel) threads. UNF & 12-UN thread series, depending on size. |
Sealing Method & Material |
O-ring on male fitting seats in machined boss (12 to 15° seat) on female port. Fitting threads into port, then separate nut and retaining washer compress O-ring into boss for seal, allowing for fitting alignment separate from seal tightening.
O-ring of rubber, Buna-N, Nitrile, Viton, etc. |
Sealing Surface Angle |
Flat. |
Typical Applications |
High pressure / high flow / high temperature hydraulic systems. |
Used In |
Port fittings / adapters. |
Pressure |
6000 psi. |
Vibration |
Excellent vibration resistance. |
Advantages |
- Extremely good pressure and temperature capability.
- No thread sealant required, no chance of thread sealant fouling fluid system.
- Straight threads less susceptible to galling on assembly than tapered threads.
- O-ring provides excellent hydraulic seal.
- Convenient separate alignment and seal tightening.
|
Disadvantages |
- Machining required to create O-ring boss if creating an ORB / UNO port.
- Not available as hose-ends from high performance aftermarket
|
Standards |
SAE J1926 |
Also Known As |
SAE straight thread O-ring boss
/-ring boss
UN /-ring boss
/-ring style
/-ring style straight thread
/-ring in chamfer
Straight thread O-ring
|
ORB / UNO fittings are excellent fittings for port connections. Although uncommon in the automotive world they are common in hydraulics, heavy equipment and aerospace. Combined with hose assemblies using high quality braided stainless steel hose and AN / SAE 37 hose-ends they make an ideal plumbing system. If I had the means I would use this system exclusively for plumbing. Unfortunately, in many cases it is not possible or practical to convert existing ports such as NPT to ORB / UNO but if you have the means I highly recommend it. |
ORB / UNO Data Table
AN Size (1) |
SAE size (2) |
Threads (3) |
Series
(4) |
Thread (OD) (5) |
Thread (ID) (6) |
Min Torque (7) |
Max Torque (8) |
Min hole (9) |
Drill
(10) |
Max hole (11) |
Drill
(12) |
-02 |
1⁄8 |
5/16 - 24 |
UNF |
0.31 |
0.27 |
- |
- |
0.272 |
I |
0.277 |
J |
-03 |
3⁄16 |
3/8 - 24 |
UNF |
0.38 |
0.33 |
8 |
10 |
0.335 |
Q |
0.340 |
R |
-04 |
1⁄4 |
7/16 - 20 |
UNF |
0.44 |
0.39 |
14 |
16 |
0.389 |
25/64 |
0.395 |
X |
-05 |
5/16 |
1/2 - 20 |
UNF |
0.50 |
0.45 |
18 |
20 |
0.452 |
29/64 |
0.457 |
- |
-06 |
3/8 |
9/16 - 18 |
UNF |
0.56 |
0.51 |
24 |
26 |
0.509 |
- |
0.515 |
33/64 |
-08 |
1/2 |
3/4 - 16 |
UNF |
0.75 |
0.69 |
50 |
60 |
0.689 |
11/16 |
0.696 |
- |
-10 |
5/8 |
7/8 - 14 |
UNF |
0.88 |
0.80 |
72 |
80 |
0.806 |
51/64 |
0.814 |
13/16 |
-12 |
3/4 |
1.1/16 - 12 |
12-UN |
1.06 |
0.98 |
125 |
135 |
0.981 |
63/64 |
0.990 |
1 |
-14 |
7/8 |
1.3/16 - 12 |
12-UN |
1.19 |
1.11 |
170 |
190 |
1.106 |
1.7/64 |
1.115 |
1.1/8 |
-16 |
1 |
1.5/16 - 12 |
12-UN |
1.31 |
1.23 |
200 |
220 |
1.231 |
1.15/64 |
1.240 |
1.1/14 |
-20 |
1-1/4 |
1.5/8 - 12 |
12-UN |
1.63 |
1.54 |
210 |
280 |
1.544 |
- |
1.553 |
1.9/16 |
-24 |
1-1/2 |
1.7/8 - 12 |
12-UN |
1.88 |
1.79 |
270 |
360 |
1.794 |
- |
1.803 |
1.13/16 |
-32 |
2 |
2.1/2 - 12 |
12-UN |
2.50 |
2.42 |
350 |
430 |
2.419 |
- |
2.428 |
2.7/16 |
- AN "dash" size (in sixteenths of an inch).
- Inch size equivalent, based on (nominal) Tube OD or Hose ID.
- Actual thread size and pitch.
- UN Thread Series.
- Male thread major diameter (OD).
- Female thread major diameter (ID).
- Minimum torque in ft/lbs – note torque values are approximate and will vary depending on coating, cleanliness, and condition of threads.
- Maximum torque in ft/lbs – note torque values are approximate and will vary depending on coating, cleanliness, and condition of threads.
- Minimum size hole to drill for tap (inches) assuming 75% thread depth, class 2B threads, & fitting thread depth of engagement ranging from 1/3 the diameter of the fitting to 1.5 times the diameter of the fitting.
- Nearest drill bit size corresponding to the min size hole.
- Maximum size hole to drill for tap (inches) assuming 75% thread depth, class 2B threads, & fitting thread depth of engagement ranging from 1/3 the diameter of the fitting to 1.5 times the diameter of the fitting.
- Nearest drill bit size corresponding to the max size hole.
|
SAE 45° Flare
Society of Automotive Engineers 45° Flare
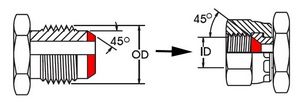 |
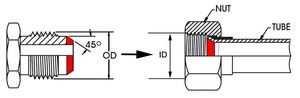 |
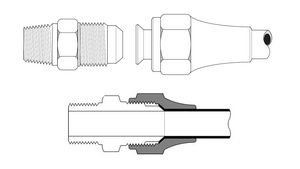
SAE 45° flare connection disassembled above and assembled below |
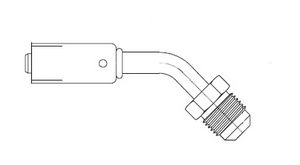
SAE 45° flare male hose-end fitting |
Threads |
UN thread form, 60° flank angle, straight (parallel) threads. UNF, UNEF & UNS thread series, depending on size. |
Sealing Method & Material |
Metal to metal seal - male 45° cone seats against 45° female flare (seat).
Female seat may be fixed (top left pic), or may be flared into tubing and a loose female nut used (top right & bottom left pics). |
Sealing Surface Angle |
45° |
Typical Applications |
LP and natural gas, flammable liquids, instrumentation, refrigeration, power steering, hydraulic and pneumatic systems. |
Used In |
Hose-ends / adapters / unions. |
Pressure |
5000 psi. |
Vibration |
Good vibration resistance. |
Advantages |
- Reusable
- Common automotive style, good sealing and holding characteristics.
- No thread sealant required, no chance of thread sealant fouling fluid system.
- Straight threads less susceptible to galling on assembly than tapered threads.
- Convenient separate alignment and seal tightening.
|
Disadvantages |
- Machining required to create female seat if creating an SAE 45° port.
- Flaring tube with hand tools can be tricky, especially in confined spaces.
- Not available as hose-ends from high performance aftermarket.
|
Standards |
SAE J512 |
Also Known As |
SAE Flare
a/c fitting
SAE auto refrig
|
SAE 45° Flare fittings are very common in OEM automotive plumbing - particularly fuel lines, air conditioning, and power steering. They are fairly similar to AN / SAE 37° fittings except that hose-ends and tube fittings may be either male or female whereas AN / SAE 37° hose-ends are normally female. They are not as universally common across industries (aerospace, hydraulics, etc.) as AN / SAE 37° and also not as common in the automotive high performance / racing aftermarket. |
SAE 45° Flare Data Table
AN Size (1) |
SAE size (2) |
Threads (3) |
Series
(4) |
Thread (OD) (5) |
Thread (ID) (6) |
Min Torque (7) |
Max Torque (8) |
Hex (9) |
Min hole (10) |
Drill
(11) |
Max hole (12) |
Drill
(13) |
-02 |
1⁄8 |
5/16 - 24 |
UNF |
0.31 |
0.27 |
6 |
7 |
2 |
0.272 |
I |
0.277 |
J |
-03 |
3⁄16 |
3/8 - 24 |
UNF |
0.38 |
0.34 |
8 |
9 |
2 |
0.335 |
Q |
0.340 |
R |
-04 |
1⁄4 |
7/16 - 20 |
UNF |
0.44 |
0.39 |
11 |
12 |
2 |
0.389 |
25/64 |
0.395 |
X |
-05 |
5/16 |
1/2 - 20 |
UNF |
0.50 |
0.45 |
14 |
15 |
2 |
0.452 |
29/64 |
0.457 |
- |
-06 |
3/8 |
5-8 - 18 |
UNF |
0.63 |
0.57 |
18 |
20 |
1.1/2 |
0.572 |
9/16 |
0.578 |
37/64 |
-07 |
7/16 |
11/16 - 24 |
UNEF |
0.69 |
0.63 |
25 |
30 |
1.1/2 |
0.647 |
41/64 |
0.652 |
21/32 |
-08 |
1/2 |
3/4 - 16 |
UNF |
0.75 |
0.69 |
36 |
39 |
1.1/2 |
0.689 |
11/16 |
0.696 |
- |
-10 |
5/8 |
7/8 - 14 |
UNF |
0.88 |
0.81 |
57 |
63 |
1.1/2 |
0.806 |
- |
0.814 |
13/16 |
-12 |
3/4 |
1.1/16 -14 |
UNS |
1.06 |
0.99 |
79 |
88 |
1 |
0.992 |
- |
1.000 |
1 |
-14 |
7/8 |
1.1/4 - 12 |
UNF |
1.25 |
1.16 |
94 |
103 |
1 |
1.169 |
1.11/64 |
1.178 |
- |
-16 |
1 |
1.3/8 - 12 |
UNF |
1.38 |
1.29 |
108 |
113 |
1 |
1.294 |
1.9/32 |
1.303 |
- |
- AN "dash" size (in sixteenths of an inch).
- Inch size equivalent, based on (nominal) Tube OD or Hose ID.
- Actual thread size and pitch.
- UN Thread Series.
- Male thread major diameter (OD).
- Female thread major diameter (ID).
- Minimum torque in ft/lbs – note torque values are approximate and will vary depending on coating, cleanliness, and condition of threads.
- Maximum torque in ft/lbs – note torque values are approximate and will vary depending on coating, cleanliness, and condition of threads.
- Number of hex turns from finger tight – alternative tightening spec when torque wrench not practical.
- Minimum size hole to drill for tap (inches) assuming 75% thread depth, class 2B threads, & fitting thread depth of engagement ranging from 1/3 the diameter of the fitting to 1.5 times the diameter of the fitting.
- Nearest drill bit size corresponding to the min size hole.
- Maximum size hole to drill for tap (inches) assuming 75% thread depth, class 2B threads, & fitting thread depth of engagement ranging from 1/3 the diameter of the fitting to 1.5 times the diameter of the fitting.
- Nearest drill bit size corresponding to the max size hole.
|
SAE Inverted Flare
Society of Automotive Engineers 45° Inverted Flare
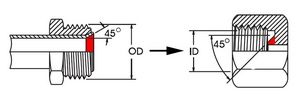 |
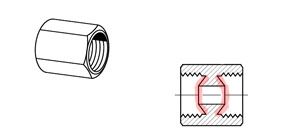
SAE inverted flare coupling, red area indicating the inverted flare seats. |
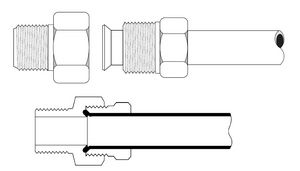
SAE inverted flare connection disassembled above and assembled below. |
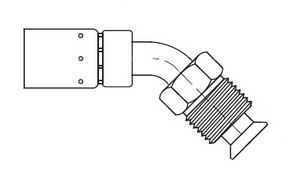
SAE inverted flare male hose-end fitting
. |
Threads |
UN thread form, 60° flank angle, straight (parallel) threads. UNF, UNS, & 16-UN thread series, depending on size. |
Sealing Method & Material |
Metal to metal seal.
Male 45° flare (either machined fitting or loose tube-nut over flared tube) seals against female 45° inverted flare seat.
Steel, brass or aluminum tube nut. |
Sealing Surface Angle |
42°or 45° |
Typical Applications |
Automotive hydraulic brake lines and fittings, power steering, fuel lines and transmission cooler lines. |
Used In |
Hose-ends / adapters / unions. |
Pressure |
2000 psi. |
Vibration |
Excellent vibration resistance. |
Advantages |
- Very low cost.
- Compact.
- Excellent vibration life.
- Short nut affords very close tube bends.
- No thread sealant required, no chance of thread sealant fouling fluid system.
- Straight threads less susceptible to galling on assembly than tapered threads.
- Convenient separate alignment and seal tightening.
|
Disadvantages |
- Machining required to create female seat if creating an SAE 45° Inverted Flare port.
- Flaring tube with hand tools can be tricky, especially in confined spaces.
- Not available as hose-ends from high performance aftermarket.
- Lower pressure capacity than other fitting styles.
|
Standards |
SAE J512 |
Also Known As |
SAE Inverted
Inverted Flare
SAE 45° Inverted Flare
Inverted
IF
SAE IF |
SAE Inverted Flare fittings are very common in OEM automotive plumbing - particularly brake lines - but are also used in fuel, power steering, and automatic transmission cooler lines - for many of the reasons listed in the advantages column above. They are essentially the opposite of SAE 45° Flare fittings - instead of a male cone and female flare there is a male flare and female cone or "inverted flare". The short tube nut required in this design is one of the chief advantages of the style - particularly for forming and bending automotive brake lines (tubing). |
SAE Inverted Flare Data Table
AN Size (1) |
SAE size (2) |
Threads (3) |
Series
(4) |
Thread (OD) (5) |
Thread (ID) (6) |
Min hole (7) |
Drill
(8) |
Max hole (9) |
Drill
(10) |
-02 |
1⁄8 |
5/16 - 24 |
UNF |
0.32 |
0.28 |
0.272 |
I |
0.277 |
J |
-03 |
3⁄16 |
3/8 - 24 |
UNF |
0.38 |
0.34 |
0.335 |
Q |
0.340 |
R |
-04 |
1⁄4 |
7/16 - 24 |
UNS |
0.44 |
0.40 |
0.396 |
X |
0.401 |
Y |
-05 |
5/16 |
1/2 - 20 |
UNF |
0.50 |
0.45 |
0.452 |
29/64 |
0.457 |
|
-06 |
3/8 |
5/8 - 18 |
UNF |
0.63 |
0.57 |
0.572 |
9/16 |
0.578 |
37/64 |
-07 |
7/16 |
11/16 - 18 |
UNS |
0.69 |
0.63 |
0.627 |
5/8 |
0.644 |
41/64 |
-08 |
1/2 |
3/4 - 18 |
UNS |
0.75 |
0.70 |
0.696 |
11/16 |
0.702 |
45/64 |
-10 |
5/8 |
7/8 - 18 |
UNS |
0.88 |
0.82 |
0.821 |
13/16 |
0.827 |
53/64 |
-12 |
3/4 |
1.1/16 - 16 |
16-UN |
1.06 |
1.00 |
1.002 |
1 |
1.009 |
1.1/64 |
- AN "dash" size (in sixteenths of an inch).
- Inch size equivalent, based on (nominal) Tube OD or Hose ID.
- Actual thread size and pitch.
- UN Thread Series.
- Male thread major diameter (OD).
- Female thread major diameter (ID).
- Minimum size hole to drill for tap (inches) assuming 75% thread depth, class 2B threads, & fitting thread depth of engagement ranging from 1/3 the diameter of the fitting to 1.5 times the diameter of the fitting.
- Nearest drill bit size corresponding to the min size hole.
- Maximum size hole to drill for tap (inches) assuming 75% thread depth, class 2B threads, & fitting thread depth of engagement ranging from 1/3 the diameter of the fitting to 1.5 times the diameter of the fitting.
- Nearest drill bit size corresponding to the max size hole.
|
SAE ORS
Society of Automotive Engineers O-ring Face Seal
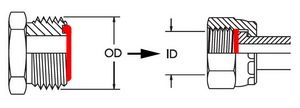 |
Threads |
UN thread form, 60° flank angle, straight (parallel) threads. UNF, UNS, 12-UN, & 16-UN thread series, depending on size. |
Sealing Method & Material |
/-ring captured in end of male fitting seals against flat seat in female swivel nut.
/-ring of rubber, Buna-N, Nitrile, Viton, etc. |
Sealing Surface Angle |
Flat. |
Typical Applications |
Hydraulics. |
Used In |
Port fittings / adapters. |
Pressure |
6000 psi. |
Vibration |
Good vibration resistance. |
Advantages |
- No thread sealant required, no chance of thread sealant fouling fluid system.
- Straight threads less susceptible to galling on assembly than tapered threads.
- Convenient separate alignment and seal tightening.
|
Disadvantages |
- Uncommon.
- Machining required to create female flat /-ring seat if creating an ORS port.
- /-ring more easily lost, pinched, or misaligned on assembly than other designs.
- Not available as hose-ends from high performance aftermarket.
|
Standards |
SAE J1453 / ISO 8434-3 |
Also Known As |
SAE /-ring Face Seal
/-ring Seal
ORFS
/-ring Face Seal
|
SAE ORS Data Table
AN Size (1) |
SAE size (2) |
Threads (3) |
Series
(4) |
Thread (OD) (5) |
Thread (ID) (6) |
Min Torque (7) |
Max Torque (8) |
Min hole (9) |
Drill
(10) |
Max hole (11) |
Drill
(12) |
-04 |
1⁄4 |
9/16 - 18 |
UNF |
0.56 |
0.51 |
10 |
12 |
0.509 |
|
0.515 |
33/64 |
-06 |
3/8 |
11/16 - 16 |
16-UN |
0.69 |
0.63 |
18 |
20 |
0.611 |
39/64 |
0.629 |
5/8 |
-08 |
1/2 |
13/16 - 16 |
16-UN |
0.82 |
0.75 |
32 |
35 |
0.752 |
3/4 |
0.759 |
49/64 |
-10 |
5/8 |
1 - 14 |
UNS |
1.00 |
0.93 |
46 |
50 |
0.931 |
|
0.938 |
15/16 |
-12 |
3/4 |
1.3/16 - 12 |
12-UN |
1.19 |
1.11 |
65 |
70 |
1.106 |
1.7/64 |
1.115 |
|
-16 |
1 |
1.7/16 - 12 |
12-UN |
1.44 |
1.36 |
92 |
100 |
1.354 |
1.11/32 |
1.365 |
1.23/64 |
-20 |
1-1/4 |
1.11/16 - 12 |
12-UN |
1.69 |
1.61 |
125 |
140 |
1.612 |
1.39/64 |
1.619 |
1.5/8 |
-24 |
1-1/2 |
2 - 12 |
12-UN |
2.00 |
1.92 |
150 |
165 |
1.919 |
|
1.928 |
1.15/16 |
- AN "dash" size (in sixteenths of an inch).
- Inch size equivalent, based on (nominal) Tube OD or Hose ID.
- Actual thread size and pitch.
- UN Thread Series.
- Male thread major diameter (OD).
- Female thread major diameter (ID).
- Minimum torque in ft/lbs – note torque values are approximate and will vary depending on coating, cleanliness, and condition of threads.
- Maximum torque in ft/lbs – note torque values are approximate and will vary depending on coating, cleanliness, and condition of threads.
- Minimum size hole to drill for tap (inches) assuming 75% thread depth, class 2B threads, & fitting thread depth of engagement ranging from 1/3 the diameter of the fitting to 1.5 times the diameter of the fitting.
- Nearest drill bit size corresponding to the min size hole.
- Maximum size hole to drill for tap (inches) assuming 75% thread depth, class 2B threads, & fitting thread depth of engagement ranging from 1/3 the diameter of the fitting to 1.5 times the diameter of the fitting.
- Nearest drill bit size corresponding to the max size hole.
|
SAE O-ring Pilot
Society of Automotive Engineers O-ring Pilot
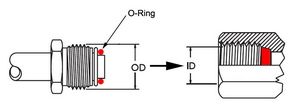 |
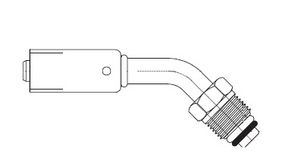
SAE /-ring pilot male hose-end |
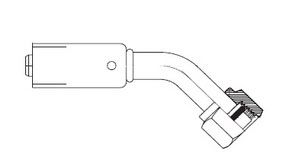
SAE /-ring pilot female hose-end |
Threads |
UN thread form, 60° flank angle, straight (parallel) threads. UNF, UNS, & 16-UN thread series, depending on size. |
Sealing Method & Material |
Male connector captured on tube, tube has flange, pilot, and /-ring
/-ring of rubber, Buna-N, Nitrile, Viton, etc. |
Sealing Surface Angle |
Flat. |
Typical Applications |
Power steering, fuel lines, air conditioning, hydroboost brakes. |
Used In |
Hose-ends / port fittings / adapters. |
Pressure |
|
Vibration |
Good vibration resistance. |
Advantages |
- No thread sealant required, no chance of thread sealant fouling fluid system.
- Straight threads less susceptible to galling on assembly than tapered threads.
- Convenient separate alignment and seal tightening.
|
Disadvantages |
- Few sizes available.
- Not available as hose-ends from high performance aftermarket.
- Machining required to create female flat /-ring seat and pilot bore if creating an O-ring Pilot port.
- /-ring more easily lost, pinched, or misaligned on assembly than other designs.
|
Standards |
|
Also Known As |
Bumped Tube /-ring
O-ring Pilot
O-ring Port |
SAE O-ring Pilot Data Table
AN Size (1) |
SAE size (2) |
Threads (3) |
Series (4) |
Thread (OD) (5) |
Thread (ID) (6) |
Min hole (7) |
Drill (8) |
Max hole (9) |
Drill (10) |
Bead OD (11) |
Pilot Length (long) (12) |
Pilot Length (short) (13) |
-06 |
3/8 |
5/8 - 18 |
UNF |
0.63 |
0.56 |
0.572 |
- |
0.578 |
37/64 |
0.52 |
0.28 |
0.19 |
-08 |
1/2 |
3/4 - 18 |
UNS |
0.75 |
0.69 |
0.696 |
- |
0.702 |
45/64 |
0.64 |
0.39 |
0.19 |
-10 |
5/8 |
7/8 - 18 |
UNS |
0.88 |
0.81 |
0.821 |
- |
0.827 |
53/64 |
0.77 |
0.39 |
0.19 |
-12 |
3/4 |
1.1/16 - 16 |
16-UN |
1.06 |
0.99 |
1.002 |
1 |
1.009 |
1.1/64 |
0.91 |
0.39 |
0.19 |
- AN "dash" size (in sixteenths of an inch).
- Inch size equivalent, based on (nominal) Tube OD or Hose ID.
- Actual thread size and pitch.
- UN Thread Series.
- Male thread major diameter (OD).
- Female thread major diameter (ID).
- Minimum size hole to drill for tap (inches) assuming 75% thread depth, class 2B threads, & fitting thread depth of engagement ranging from 1/3 the diameter of the fitting to 1.5 times the diameter of the fitting.
- Nearest drill bit size corresponding to the min size hole.
- Maximum size hole to drill for tap (inches) assuming 75% thread depth, class 2B threads, & fitting thread depth of engagement ranging from 1/3 the diameter of the fitting to 1.5 times the diameter of the fitting.
- Nearest drill bit size corresponding to the max size hole.
- Outside diameter of the bead on the tube (inches).
- Length of the pilot (inches) - long style.
- Length of the pilot (inches) - short style.
|
BSPT
British Standard Pipe Tapered
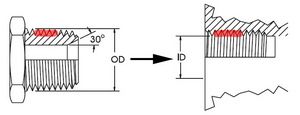 |
Threads |
Whitworth thread form, 55° flank angle, tapered threads. Thread taper is 1° 47' 24" or 1.7899°, or ¾” per foot (1 in 16). |
Sealing Method & Material |
Interference fit of tapered threads at flanks, thread sealant (Teflon tape) must be used. |
Sealing Surface Angle |
N/A. |
Typical Applications |
Hydraulic systems, plumbing. |
Used In |
Port Fittings / adapters / unions. |
Pressure |
5000 psi. |
Vibration |
Fair vibration resistance. |
Advantages |
- Easy to drill and tap ports for, without having to machine a surface or location for a sealing washer or /-ring
|
Disadvantages |
- Supplemental sealant required
- Some risk of sealant contaminating fluid system.
- Tapered threads act as mechanical jack and can crack cast housings when over-tightened.
- Difficult to establish accurate torque ratings due to tapered threads.
- No swivel-action on assembly.
- Shaped fittings such as elbows and Tees can be difficult to tighten so that they are both correctly oriented and tightened sufficiently to seal.
- Poor disassembly / reassembly performance due to inerrant thread damage.
- Any side-load on fitting will cause leaks.
- Can be easily cross-threaded on assembly without realizing it as user assumes tightness is due to tapered thread instead of correctly identifying a cross-threaded condition.
|
Standards |
ISO 7-1 / BS 21 |
Also Known As |
R
Rc
British Standard Taper Pipe
Pipe Taper
Conical Thread
BSPTr
PT
KR |
Interchange |
BSPT male can be screwed into:
- BSPT female - thread sealant required
- BSPP female (not ideal) - thread sealant required
BSPT threads are not compatible with NPT/F threads as the flank angle is different (55° vs. 60 °) and most of the sizes have different thread pitch. However, the 1/2" and 3/4" sizes have the same pitch (all are 14 TPI) and can be used together in a pinch with enough thread sealant. |
BSPT Data Table
AN Size (1) |
SAE size (2) |
Threads - nominal
(3) |
Threads - actual
(inches) (4) |
Thread (OD)
(inches) (5) |
Thread (ID)
(inches) (6) |
Drill (7) |
-02 |
1⁄8 |
1/8 - 28 |
3/8 |
0.37 |
0.33 |
21/64" |
-04 |
1⁄4 |
1/4 - 19 |
1/2 |
0.50 |
0.44 |
7/16" |
-06 |
3/8 |
3/8 - 19 |
5/8 |
0.64 |
0.59 |
37/64" |
-08 |
1/2 |
1/2 - 14 |
3/4 |
0.80 |
0.72 |
23/32" |
-10 |
5/8 |
5/8 - 14 |
7/8 |
0.89 |
0.81 |
25/32 |
-12 |
3/4 |
3/4 - 14 |
1 |
1.02 |
0.94 |
15/16" |
-16 |
1 |
1 - 11 |
1-3/8 |
1.28 |
1.17 |
1-11/64" |
-20 |
1-1/4 |
1.1/4 - 11 |
1-5/8 |
1.62 |
1.52 |
1-33/64" |
-24 |
1-1/2 |
1.1/2 - 11 |
1-7/8 |
1.85 |
1.75 |
1-3/4" |
-32 |
2 |
2 - 11 |
2-3/8 |
2.31 |
2.22 |
2-3/16" |
- AN "dash" size (in sixteenths of an inch).
- Inch size equivalent, based on (nominal) Tube OD or Hose ID.
- Nominal thread size and pitch.
- Actual thread size - approximate. For sizes up to 1", add 1/4" to nominal thread size to get actual size of threads and vice versa.
- Male thread major diameter (OD).
- Female thread major diameter (ID).
- Drill bit size for appropriate tap.
There are no published standard torque values for tightening BSPT fittings. This is because, with tapered threads, the torque required for a secure, leak-free, reliable joint varies with thread quality, condition, & cleanliness, port and fitting materials, and the sealant used.
So how tight do you do it up?
There are a few different methods that are commonly used, you will have to select one appropriate to your situation:
By Torque Spec
Despite what I just said, you may find a torque value given for the components you are using. If you do, and you can fit a torque wrench, go ahead and use the value given. Just be aware of the following pitfalls:
- a fitting that is out of spec and bottoms out in the port before reaching torque.
- a fitting that still leaks even though you have applied the specified torque.
- a fitting that is left pointing in the wrong direction after you reach the specified torque.
By Feel
Many experienced mechanics will simply tighten BSPT fittings until they “feel right”. When backed up by a proper leak-test under safe conditions prior to being put into service, this is a perfectly acceptable method – once you have the experience and have developed the feel. When screwing the fitting in, start by hand, the fitting should gradually get tighter. When you tighten by wrench, the torque should continue to rise smoothly. If it suddenly gets tighter, you may have bottomed the fitting. If it suddenly gets looser you may have stripped the threads and will now want to curse and wish you had selected a different method. Be careful of over tightening fittings into aluminum castings as the tapered threads act as a mechanical jack and can crack the casting – particularly if the thread sealant in use acts as a lubricant which will tend to mask over-tightening until it’s too late.
By Number of Rotations
As a general guideline, after hand-tight engagement, tighten 2-3 full turns for sizes up to 1 inches for BSPT fittings. You should have between 3.5 and 6 engaged threads. Any number outside of this range may indicate either under or over tightening of the joint or out of tolerance threads. On all shaped fittings, such as elbows and tees, tighten approximately 2 turns past finger tight and orientate the fitting on the third turn. Never back off the thread to orient the fitting after completing the tightening process, as this may cause the fitting to leak.
|
BSPP
British Standard Pipe Parallel
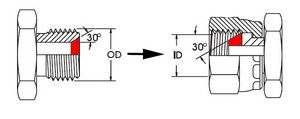 |
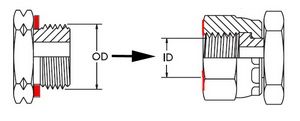 |
Threads |
Whitworth thread form, 55° flank angle, straight (parallel) threads. |
Sealing Method & Material |
Metal-to-metal seal between male flare and female cone; or
Soft sealing washer of plastic, copper, rubber coated steel, etc. |
Sealing Surface Angle |
30° for flare & cone, Flat for washer-style. |
Typical Applications |
Gas and liquid plumbing systems. |
Used In |
Port fittings / adapters. |
Pressure |
5000 psi. |
Vibration |
Fair vibration resistance. |
Advantages |
- No thread sealant required, no chance of thread sealant fouling fluid system.
- Straight threads less susceptible to galling on assembly than tapered threads.
|
Disadvantages |
- Not suited for medium or high pressure applications.
- Uncommon.
- Sealing surfaces for washer must be flat and true.
- Not available as hose-ends from high performance aftermarket.
|
Standards |
ISO 228/1 / BS 2779 |
Also Known As |
British Gas
British Pipe Parallel
Parallel Fastening thread
BSP
BSSPI
BSPF
BSPG
PS
Rp – internal (female) parallel
Rs – external (male) parallel |
Interchange |
A BSPT male can be screwed into a BSPP female, but not the other way around. |
BSPP Data Table
AN Size (1) |
SAE size (2) |
Threads - nominal
(3) |
Threads - actual
(inches) (4) |
Thread (OD)
(inches) (5) |
Thread (ID)
(inches) (6) |
Min Torque
(ft/lbs) (7) |
Max Torque
(ft/lbs) (8) |
Drill (9) |
-02 |
1⁄8 |
1/8 - 28 |
3/8 |
0.38 |
0.34 |
13 |
15 |
11/32 inch |
-04 |
1⁄4 |
1/4 - 19 |
1/2 |
0.51 |
0.47 |
19 |
23 |
29/64" |
-06 |
3/8 |
3/8 - 19 |
5/8 |
0.65 |
0.60 |
33 |
40 |
19/32" |
-08 |
1/2 |
1/2 - 14 |
3/4 |
0.82 |
0.75 |
55 |
70 |
3/4" |
-10 |
5/8 |
5/8 - 14 |
7/8 |
0.90 |
0.82 |
70 |
90 |
53/64" |
-12 |
3/4 |
3/4 - 14 |
1 |
1.04 |
0.97 |
103 |
118 |
31/32" |
-16 |
1 |
1 - 11 |
1-3/8 |
1.30 |
1.21 |
162 |
184 |
1-13/64" |
-20 |
1-1/4 |
1.1/4 - 11 |
1-5/8 |
1.64 |
1.55 |
170 |
192 |
1-35/64" |
-24 |
1-1/2 |
1.1/2 - 11 |
1-7/8 |
1.88 |
1.79 |
258 |
347 |
1-25/32" |
-32 |
2 |
2 - 11 |
2-3/8 |
2.34 |
2.26 |
|
|
2-1/4" |
- AN "dash" size (in sixteenths of an inch).
- Inch size equivalent, based on (nominal) Tube OD or Hose ID.
- Nominal thread size and pitch.
- Actual thread size - approximate. For sizes up to 1", add 1/4" to nominal thread size to get actual size of threads and vice versa.
- Male thread major diameter (OD).
- Female thread major diameter (ID).
- Minimum torque in ft/lbs – note torque values are approximate and will vary depending on coating, cleanliness, and condition of threads.
- Maximum torque in ft/lbs – note torque values are approximate and will vary depending on coating, cleanliness, and condition of threads.
- Drill bit size for appropriate tap.
|
Fitting Gallery |
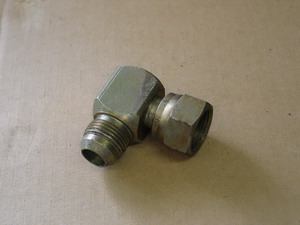 |
Industrial brass AN/SAE 37 90° union. Note the abrupt transition likely to have an adverse effect on fluid flow, pressure drop, and turbulence. |
|
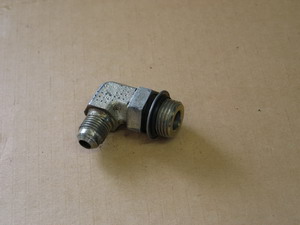 |
Industrial brass ORB to AN/SAE 37 90° adapter.
Note the free-running nut and retaining washer above the /-ring and the parallel threads.
The separate nut and retaining washer allow for fitting alignment separate from seal tightening. The fitting is screwed into the port and aligned to the desired orientation. The fitting is then held in this orientation and the nut tightened down against the washer, compressing the O-ring into the port's boss creating the seal and securing the fitting in place.
This ability to align the fitting to the desired direction, and then tighten it in this orientation is one of the chief benefits of this style of fitting and one of the reasons ORB fittings make such good port fittings. |
|
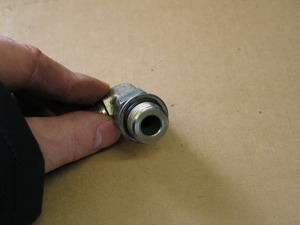 |
ORB. |
|
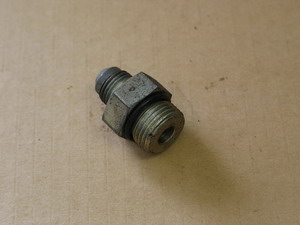 |
Not all ORB fitting have a free-running nut and retaining washer.
This fitting is an ORB to AN/SAE 37 adapter.
Obviously this style does not enjoy the seperate-align-and-tighten feature. |
|
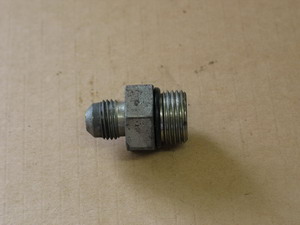 |
ORB to AN/SAE 37 adapter - no free-running nut or retaining washer. |
|
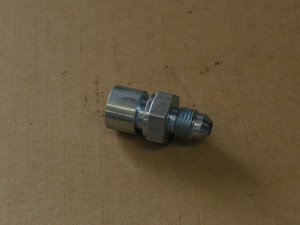 |
Brake line conversion fitting (adapter).
This adapter is from 7/16" SAE inverted flare to -03 AN/SAE 37. |
|
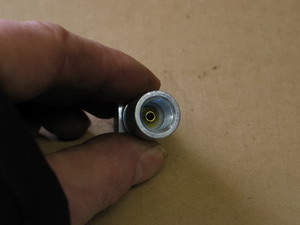 |
Inverted flare seat inside SAE inverted flare to -03 AN/SAE 37 adapter. |
|
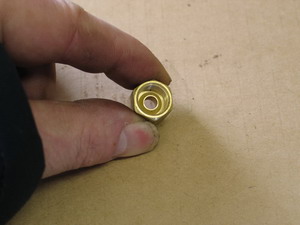 |
Inverted flare seat in SAE inverted flare union - this one for brake lines. |
|
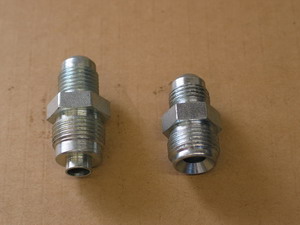 |
Two types of power steering pump outlet / hydroboost brake booster adapters.
On the left is an /-ring pilot to AN/SAE 37, without the /-ring installed.
On the right is an SAE inverted flare to AN/SAE 37. |
|
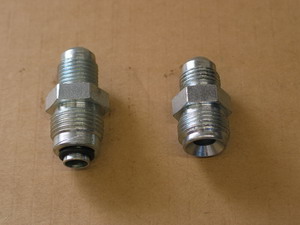 |
On the left is an /-ring pilot to AN/SAE 37, with the /-ring installed.
On the right is an SAE inverted flare to AN/SAE 37. |
|
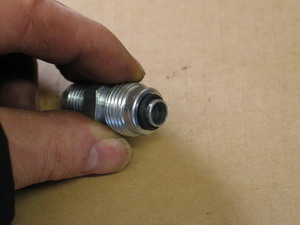 |
/-ring pilot. |
|
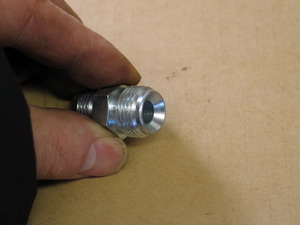 |
SAE Inverted flare.
Note the pronounced 45° flare sealing surface.
Obviously, this is a male fitting. |
|
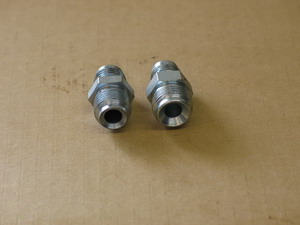 |
Two different sizes of SAE Inverted flare. |
|
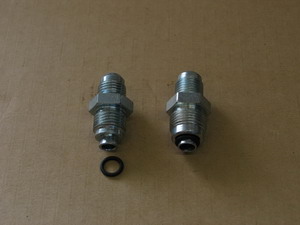 |
Two different sizes of /-ring pilot to AN/SAE 37 adapters. |
|
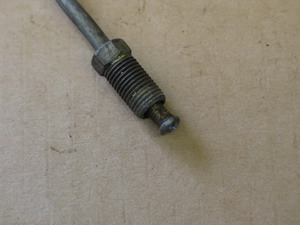 |
This is obviously a brake line.
Q: What type of fitting is it? |
|
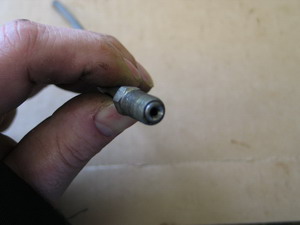 |
A: SAE inverted flare. |
|
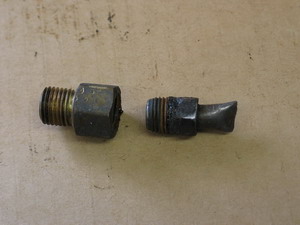 |
NPSM to SAE inverted flare adapter on the left.
This one from a TH400 automatic transmission cooler line.
The NPSM end screws into the TH400 case, the SAE inverted flare is the fitting on the end of the transmission cooler line. |
|
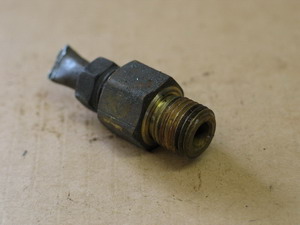 |
NPSM to SAE inverted flare adapter - note the shiny surface under the hex, where the sealing washer was located. |
|
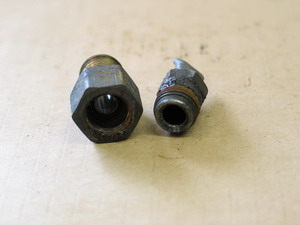 |
SAE inverted flare side of the TH400 transmission cooler line adapter. |
|
 |
NPT to AN/SAE 37 adapters - screwed into NPSM ports in TH400 case with plenty of Teflon tape sealant.
Checking the theory that one can screw an NPT male fitting into an NPSM port and still achieve a satisfactory seal. |
|
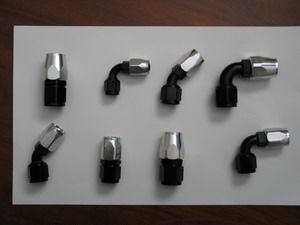 |
Various AN/SAE 37 re-usable (field attachable) hose-ends.
These are Russell Performance "full flow" hose-ends in aluminum. |
How to Identify Fittings
The process of identifying an unknown fitting is a multi-step procedure as detailed below that involves taking some empirical measurements and comparing the results to the data contained in the fitting tables above.
Step 1 - carefully examine the fitting for any markings or a part number that may aid in identification.
Step 2 - examine the fitting for features that will narrow down the possibilities, such as:
- Tapered or straight threads.
- Presence of an O-ring or sealing washer.
- Is the female sealing surface a convex (inverted flare) shape or a concave (flared) shape?
- Is the male sealing surface a convex (inverted flare) shape or a concave (flared) shape?
- Is there a pilot on the end of the fitting?
Step 3 - measure and categorize the threads as follows: |
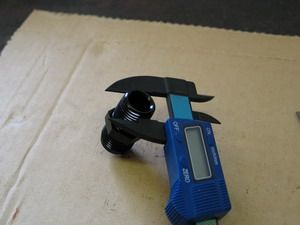 |
Measure the OD of the threads (or the ID in the case of a female fitting) and... |
|
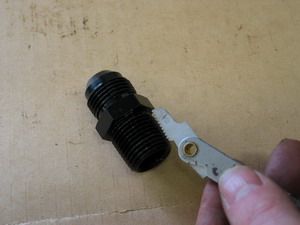 |
... measure the pitch of the threads (or TPI) using a thread gauge. |
In addition to measuring the OD / ID and pitch, if the tools are available, you can also use:
- A thread profile gauge to identify NPT fittings. This is a plastic gauge with thread impressions made in it, into which you can lay a fitting. If the threads match and the fitting sits in the impression perfectly, the gauge will tell you the nominal size of the tapered pipe fitting. This tool can be especially useful for identifying the size of tapered pipe thread fittings, as obviously, being that the threads are tapered, the results obtained from measuring the thread OD or ID will vary depending on where along the length of the thread the measurement is made.
- A port board is another type of gauge that is used to identify male thread size by comparison with known threads.
Step 4 - measure the angle of the sealing surface. Special gauges are available for this purpose. |
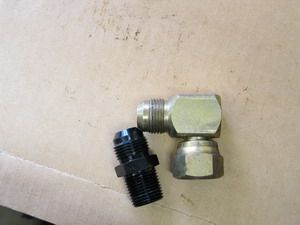 |
However, if you don't have a sealing surface angle gauge, an approximation can be made by comparing the angle of the sealing surface with that of a fitting whose angle is known. |
Step 5 - refer to tables. Using all the data collected in steps 2,3, and 4 - compare these results with the data in the tables above for each style of fitting. You should be able to determine a match at this point.
Step 6 - verify. Once you have the fitting identified, you can double check your result by attempting to mate the fitting with one of the same size and style as that which you believe it to be.
Hose Assembly Construction
The beauty of creating custom hose assemblies with Russell Performance hose and full-flow hose-ends is that it is extremely easy to do so. Nevertheless, there are a few tips and tricks worth sharing.
The procedure shown below uses Russell Performance Proflex stainless-steel braided hose and ProClassic full-flow hose-ends. |
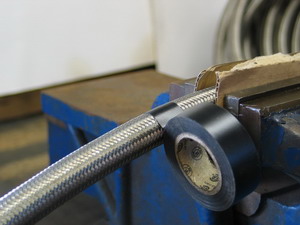 |
Before cutting the hose, wrap twice with electrical tape at the point where the cut is to be made.
I have found electrical tape works best, although you can use other tapes such as masking tape. Avoid using tapes with heavy glue residues, such as duct tape. |
|
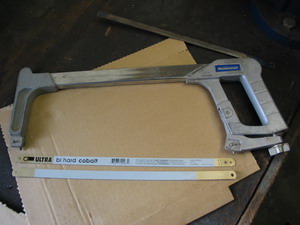 |
There are two ways to cut the hose - either by hand using a hacksaw or by using an abrasive cut-off wheel in an electrical or pneumatic power tool.
It will become immediately apparent which method I favour and why.
However, if you are going to use a hack saw, one tip is to install two blades facing in opposing directions. |
|
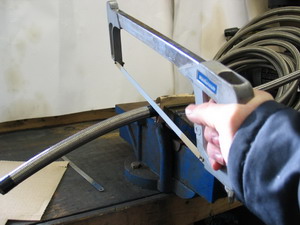 |
With the hose lightly clamped in a vice, make the cut.
Be careful not to over-tighten the vice and crush the hose. |
|
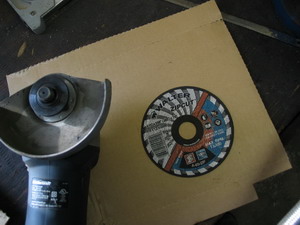 |
If you plan to use a cut-off tool (my preference) the best abrasive cutting wheels are the ultra-thin versions (3/32"). |
|
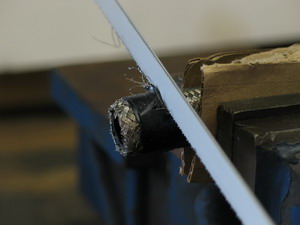 |
Using a hacksaw, I find that no matter what tape I use, what blades I use, or whether there are one or two blades, as soon as I start to cut the outer stainless steel braid begins to go haywire. |
|
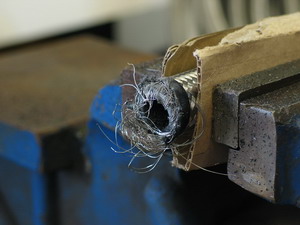 |
Persistence usually leads to a disaster of a finished cut that looks like this.
Obviously this is completely useless and cannot be inserted into a fitting.
You may have better technique or luck, but I prefer to use an abrasive cut-off tool. |
|
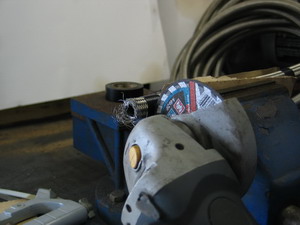 |
The only trick to using the cut-off tool is holding it square to the hose throughout the cut. |
|
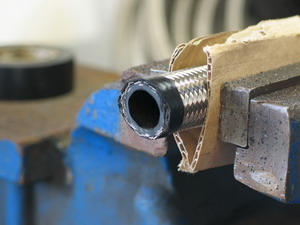 |
Here you can see that I didn't do the best job of that - BUT - you can clearly see the neatness of the cut. |
|
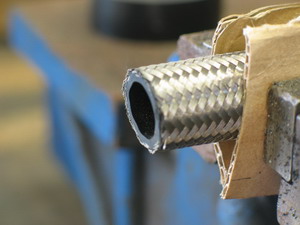 |
With the tape removed, the end of the hose is ready for the hose-end fitting.
One caution you must observe if using the abrasive cut method is this: you must carefully blow out, or otherwise clean out of the hose, any debris created by the cutting process.
If you expand this pic to full size you can clearly see the abrasive dust and debris left behind after the cut is made. I find that it is easy to blow out with compressed air and / or is easily removed with a Q-tip dipped in a little alcohol. Yes, this is an extra step, but I find the quality of cut well worth the effort. |
|
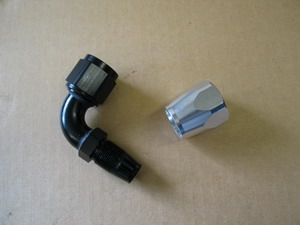 |
With the hose cut and cleaned, it's time to attach the hose-end.
Begin by unscrewing the socket (silver part) from the nipple (black part). |
|
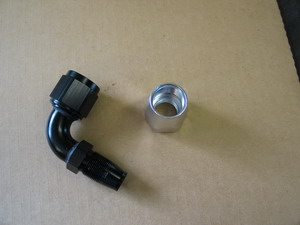 |
Lubricate the threads inside the socket as well as the threads on the nipple with Russell assembly lube. Alternatively you can use a little of the fluid that the system will carry - i.e. clean engine oil or transmission fluid, etc. |
|
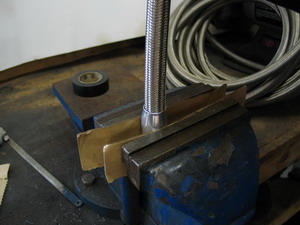 |
The next step is to thread the socket onto the hose.
To avoid crushing the hose, it is best to clamp the socket in the vice and thread the hose into the socket.
The socket threads are left-hand, so screw the hose in counter-clockwise.
Having said that, if the hose is long, screwing it in can be cumbersome... |
|
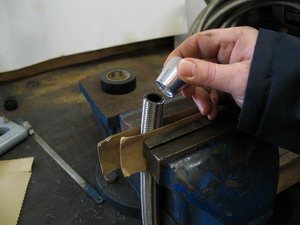 |
... in that case, it can be easier to clamp the hose in the vice and screw the socket on the hose.
Be careful not to crush or deform the hose, and remember to screw the socket on counter-clockwise. |
|
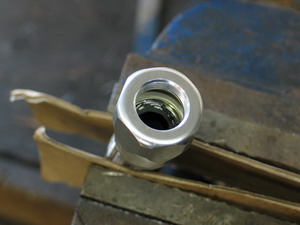 |
Continue to screw the socket on... |
|
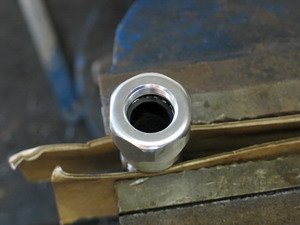 |
...until the hose bottoms inside the socket. You will likely have to use a wrench as the socket tightens on the hose but you don't have to keep screwing until you can't turn it any more. In fact, doing so will damage the hose. |
|
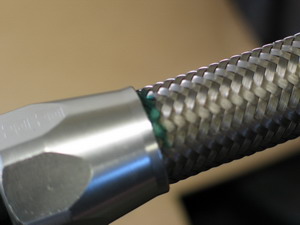 |
With the socket in place on the hose, make an alignment mark on the hose at the end of the socket. |
|
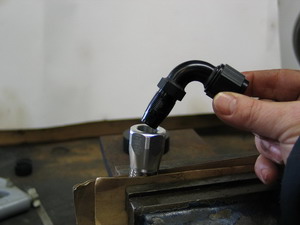 |
With the threads lubed, insert the nipple into the socket. |
|
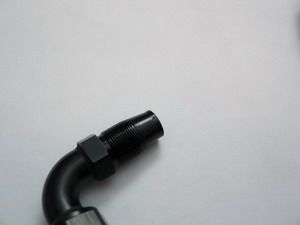 |
The design of the Russell Performance nipple, with taper that flares at the end, makes alignment in hose and socket easy, and eliminates any chance of the dreaded loose flap of rubber in the flow path. |
|
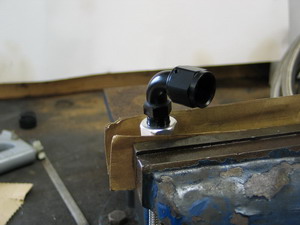 |
With the socket clamped in the vice, tighten the nipple. |
|
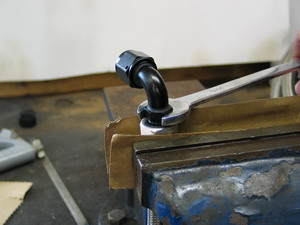 |
As you near the end, you will have to use a wrench.
To avoid marring the finish of the hose-end, it is best to use an aluminum AN wrench. |
|
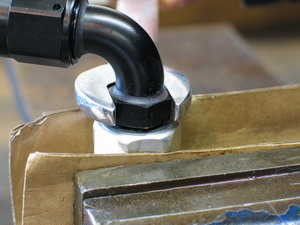 |
As you finish tightening, observe the gap between the hex on the nipple and the socket. |
|
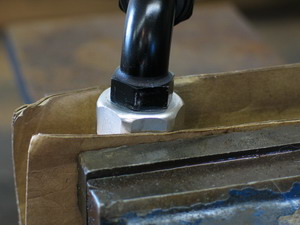 |
On completion, the gap should be no more than 1/16". The nipple may touch the socket, but do not tighten any further than this.
An important note here:
If you are assembling a hose assembly and neither hose-end is straight nor a swivel design, when you tighten the second nipple into its socket, you must align it with the other hose-end at this time.
This is because you must not twist the hose when it is installed in the vehicle, and if neither hose-end is a swivel design, and both hose-ends are angled, there is no other way to align the ends other than with the position of the second nipple in its socket. Fortunately, the 1/16" max gap spec allows for this.
That said, this is an area where having at least one swivel hose-end on each hose assembly can enormously simplify hose assembly construction and installation. |
|
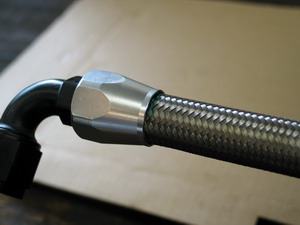 |
With the assembly completed, re-check the alignment mark you made on the hose earlier to ensure the hose hasn't been pushed out of the socket by the nipple being screwed in.
If it has, you will have to disassemble and start again. |
|
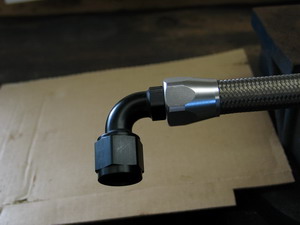 |
The completed hose-end should look like this.
Note the bad-ass look achieved with the combination of the Proflex Hose and ProClassic black/clear hose-ends!
Before being put into service, the hose assembly should be thoroughly cleaned / blown out and inspected. |
|
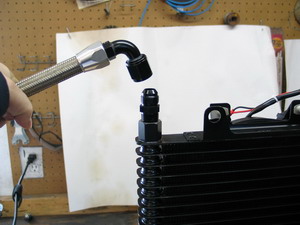 |
The completed hose assembly is very easily installed in the vehicle - one of the many beauties of AN style hose-ends.
Simply place the female hose-end on the adapter... |
|
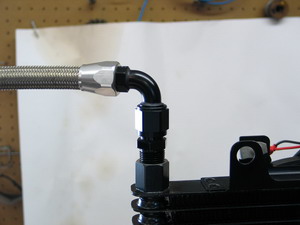 |
... start the threads of the hose-end nut, align the hose, hold the hose in position, and then finish tightening the hose-end nut.
Note again, the cool colour combination of black and silver fittings with black components (in this case an oil cooler), and silver stainless-steel hose! |
Plumbing System Layout & Installation Procedures
The following points are offered as some guidance on procedures and considerations for designing, laying out, and installing a plumbing system. Many of the points are paraphrased from the SAE paper: "Selection, installation and maintenance of hose and assemblies — SAE J1273 October 1996"
Routing: Attention must be given to optimum hose routing to minimize potential problems (kinking or flow restriction due to hose collapse, twisting of the hose, proximity to hot objects or heat sources). Care must be taken to protect hose from wear, snagging, kinking, bending smaller that minimum bend radius, and cutting - any of which can cause premature hose failure. Any hose that has been kinked or bent to a radius smaller than the minimum bend radius, and any hose that has been cut or is cracked or is otherwise damaged, should be removed and discarded. The hose assembly should be routed in such a manner that if a failure does occur, the escaping fluid will not cause personal injury or equipment damage. In addition, routing should be such that it minimizes the chance that hose failure could cause fluid to come in contact with hot surfaces, open flame, or sparks, as a fire or explosion may otherwise result.
Hose installation:
Hose should not be twisted or put in torsion either during the installation or while in service. Sharp or excessive bends may cause the hose to kink or rupture. Be sure to allow enough slack to provide for changes in length which will occur when pressure is applied. This change in length can vary from +2% to -4%. Design the installation so the hose assembly is accessible for inspection and easy removal. Bend radius is important. If you do not have a published spec for your hose, a good working rule is that the minimum bend radius should be five or more times the O.D. of the hose.
Length: When establishing a proper hose length, motion absorption, hose length changes due to pressure, and hose and machine tolerances and movement must be considered.
Hose Cleanliness: During construction and test fitting, it is easy for hose assemblies to become contaminated with dirt and debris. Care must be taken to insure that prior to installation hose assemblies are adequately clean for the application.
Radiant Heat: Hose installation and routing must be such that the hose cannot be heated to a point where it becomes damaged or destroyed by nearby heat sources such as as hot manifolds. This can happen even without direct contact and despite the presence of cool air around the hose.
Pre-Installation Inspection: Prior to installation, a careful examination of the hose and fittings must be performed. All components must be checked for correct style, size, and length. The hose must be examined for cleanliness, obstructions, blisters, cover looseness, kinks, cracks, cuts or any other visible defects. Inspect the fitting and sealing surfaces for burrs, nicks, corrosion or other imperfections. Do not use any component that displays any signs of nonconformance.
Minimum Bend Radius: Installation of a hose at less than the minimum listed bend radius may significantly reduce the hose life. Particular attention must be given to preclude sharp bending at the hose to hose-end juncture. Any bending during installation at less than the minimum bend radius must be avoided.
Twist Angle and Orientation: Hose assembly installation must be such that relative motion of machine components does not produce twisting.
Securement: In many applications, it may be necessary to restrain, protect, or guide the hose to protect it from damage by unnecessary flexing, pressure surges, and contact with other mechanical components. Care must be taken to ensure such restraints do not introduce additional stress or wear points.
Environment: Care must be taken to ensure that the hose and fittings are either compatible with or protected from the environment (that is, surrounding conditions) to which they are exposed. Environmental conditions including but not limited to ultraviolet radiation, sunlight, heat, ozone, moisture, water, salt water, chemicals, and air pollutants can cause degradation and premature failure.
Mechanical Loads: External forces can significantly reduce hose life or cause failure. Mechanical loads which must be considered include excessive flexing, twist, kinking, tensile or side loads, bend radius, and vibration. Use of swivel type fittings or adapters may be required to insure no twist is put into the hose. Some applications, such as plumbing lines secured to long-travel suspension components, may require special testing prior to hose selection and use.
Mix ‘n’ Match: It is unwise at best, often unacceptable, and quite possibly dangerous to mix ‘n’ match hose and fittings from different manufacturers. Often each manufacturer will have its own proprietary methods of construction and assembly. Some are compatible with others and some are not. The best bet is to use quality hose and fittings from a single manufacturer. Reliable, quality companies like Russell Performance make this easy by a) manufacturing a wide variety of hose and fittings and b) clearly stating in their literature which fittings and hose are designed to be used together. This is particularly true if you are crimping or swaging fittings onto hose – each crimping machine will use particular dies designed for particular fittings. Using an inappropriate combination invites failure and the associated dangers of hose assembly failure.
System Checkout: Prior to operational use, all air must be eliminated and the system pressurized to the maximum system pressure (at or below the hose maximum working pressure) and checked for proper function and freedom from leaks. Personnel must stay out of potential hazardous areas during testing. |
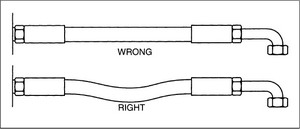 |
When hose installation is straight, allow enough slack in
hose line to provide for length changes which will occur
when pressure is applied. This change in length can vary from +2% to -4%. |
|
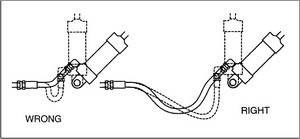 |
Adequate hose length is necessary to accommodate relative movement
between components and to avoid abrasion. |
|
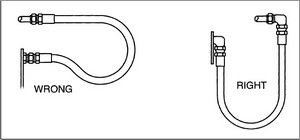 |
When two fittings that are to be joined by a hose are in close proximity, use an angle adapter to avoid having to bend the hose in a tight radius that is less than the the minimum bend radius of the hose. |
|
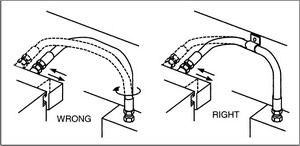 |
When a hose connects components that move in relation to each other and the hose changes direction in more than one plane, avoid twisting of hose by
clamping hose at change of plane. |
|
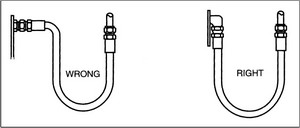 |
Use proper angle adaptors to avoid sharp twists or bends in
hose.
When determining the length of hose assemblies, provide sufficient length to prevent bending strain from localizing at the back
of the hose-end. |
|
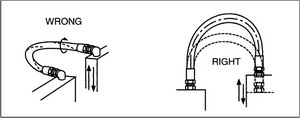 |
When there is relative motion between two parts joined by a hose, prevent twisting and distortion of hose by routing it in a gentle bend in same
plane as the motion of the moving part to which hose is
connected. |
|
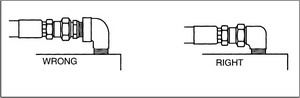 |
Reduce number of joints and potential leak paths by using proper
adaptors. |
|
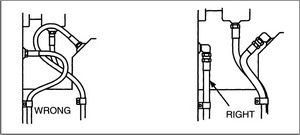 |
Route hose as directly as possible by using 45°, 90°, and other angled adaptors and
fittings. Avoid using excessive hose length. |
|
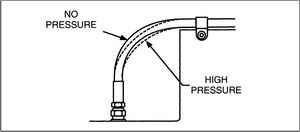 |
To allow for length changes when hose is pressurized, do
not clamp at bends. Curves will absorb changes. Do not
clamp high and low pressure lines together. |
|
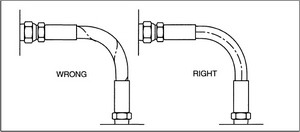 |
When installing hose, make sure it is not twisted. Pressure
applied to a twisted hose can result in hose failure or
loosening of fittings. |
|
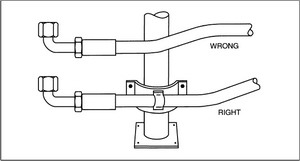 |
High ambient temperatures shorten hose life so make sure
hose is kept away from hot parts. If this is not possible,
insulate hose. |
|
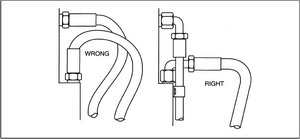 |
Elbows and adaptors should be used to relieve strain on
hose assemblies, and to provide neater installations which will
be more accessible for inspection and maintenance. |
|
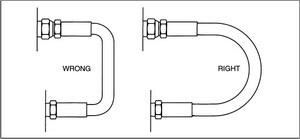 |
To avoid hose collapse and flow restriction, keep hose
bend radii as large as possible. Refer to hose specification
tables for minimum bend radii. |
|
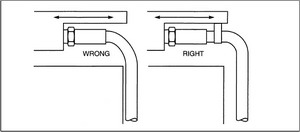 |
Install hose so that it avoids rubbing and
abrasion. Often, clamps are required to support long hose
runs or to keep hose away from moving parts. Use clamps
of the correct size. A clamp too large allows hose to move
inside the clamp and causes abrasion. |
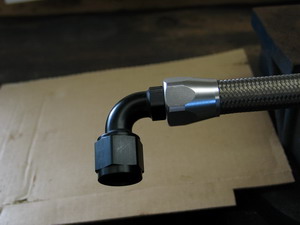 |
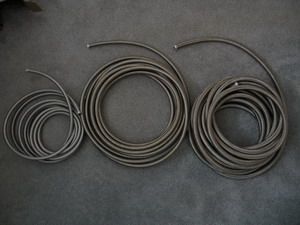 |
References:
- RECOMMENDED PRACTICES FOR HYDRAULIC HOSE ASSEMBLIES — SAE J1273 October 1996
- SAE J516—Hydraulic Hose Fittings
- SAE J517—Hydraulic Hose
- Gren, Robert E., Oberg, E., Jones,
F.D., Horton, H.L., Ryffel, H. H. (Editors). Machinery’s Handbook, 24th
Edition, 1992, (Industrial Press, Inc)
- Smith, Caroll. Carroll Smith's Nuts, Bolts and Fasteners and Plumbing Handbook, 1990, (Motorbooks International)
- Aird, Forbes. High Performance Hardware : Fastener Technology for Auto Racers and Enthusiasts, 1999, (Berkley Pub Group)
- Russell Performance - Advanced Fluid Transfer Systems - 2007-2008 Automotive Catalogue
- Schmidt, Mark. Pipe Thread Types and Designations, 2007, (Colder Products Company Product Control
Engineering)
|
|
|