|
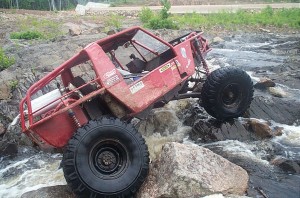 |
The need for
super-low gearing in technical rock crawling and other hardcore wheeling
is no secret and no surprise. Long gone are the days when 100:1
overall gearing was considered as deep as anyone would ever need. |
|
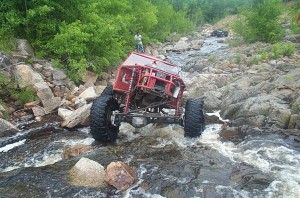 |
More technical courses and more extreme trails demand greater control
and that means low gears - in my opinion there really is no "too
low", BUT... |
...To have a
truly capable rig, you need far more than just a super-low low.
Especially if you want it to be capable, drivable, and fun over a variety
of terrain.
Strangely, what, in my opinion,
is one of the most important aspects of a 4x4s performance is never talked
about. In fact - I've never seen anyone discuss it - the concept
only occurred to me because of experience in another sport.
Many, many moons ago
I used to do a bit of bicycle racing. As you can imagine - gearing
and gear choices are extremely important to the cyclist - especially since
it's your legs that are providing the power. Just as in building
4x4s, serious cyclists build their own gearing by building custom combinations
of sprockets on the front and rear cogs of the bike. Too low or
too high a gearing for the combination of bike, rider, and course - and
it's almost impossible to win. But cyclist know there's much more
to it than that.
So here's the secret to not
only winning bike racing - but to great 4x4 performance as well - the
concept is called "gear stepping". If you've ever ridden
a bicycle you are already familiar with the concept. Take, for example,
your average 18 speed bicycle - it will have 3 sprockets on the front
(crank sprockets) and 6 sprockets on the back (freewheel sprocket) for
a total of 3 x 6 = 18 gears. HOWEVER - not all 18 of these gears are useable
- the progression from one to the other is not linear. Say you start
peddling on the smallest front sprocket and the largest rear sprocket
- this is the lowest and easiest gear the bike has. As you pick
up speed you shift the rear derailleur through the 6 gears on the rear
sprocket. If you were to then shift the rear derailleur back to
the largest while simultaneously shifting the front derailleur to the
next larger sprocket - you would find that the gear this put you in was
not a step higher (harder to peddle) than the last gear you were in -
in fact, it would most likely be a step backwards and be a lower gear.
This is because of the fixed number of teeth on the sprockets which determines
the actual gear ratios available.
So this gear ends up being
unusable, and the experienced cyclist skips it and goes on to another
combination he knows to be a higher gear. In fact, the serious cyclist
will calculate out the ratios achieved by each possible combination, including
the percentage jump from one to the next. The resulting table looks
something like this:
Gear Selection |
Front chain
wheel teeth (drive) |
Rear freewheel
teeth (driven) |
Ratio (drive/driven) |
% jump from
last |
1 |
42 |
24 |
1.75 |
n/a |
2 |
42 |
21 |
2.00 |
14% |
3 |
42 |
19 |
2.21 |
11% |
4 |
42 |
17 |
2.47 |
12% |
5 |
42 |
15 |
2.80 |
13% |
6 |
42 |
13 |
3.23 |
15% |
7 |
52 |
24 |
2.17 |
-33% |
8 |
52 |
21 |
2.48 |
14% |
9 |
52 |
19 |
2.74 |
11% |
10 |
52 |
17 |
3.06 |
12% |
11 |
52 |
15 |
3.47 |
13% |
12 |
52 |
13 |
4.00 |
15% |
By considering this table,
the cyclist can determine which gears are "useable" and which
are not, and furthermore, for a given course, will plan which gears to
use in which order - a plan in which the percentage jump becomes critical
- you don't want to suddenly shift to a gear that is 50% harder as you
would lose your momentum and stall.
Take particular note of the
ratios between 6th gear and 11th gear. Notice that if you were pedalling
along in 6th gear (chain on the small front sprocket and smallest freewheel
sprocket) and then just shift into 7th gear (chain on large front sprocket
and largest freewheel sprocket) it actually gets easier to pedal (gear
ratio goes down instead of up) - we've probably all experienced this,
and it would spell disaster in a race (in a car race - like downshifting
along the straightaway instead of upshifting). Also note, that in
order to "upshift" this bike from 6th gear we have to go all
the way to 11th gear - making gears 7-10 essentially useless, and leaving
our fancy 12 speed bike really an 8 speed. If I was planning to
race this bike, having charted the ratios, I would know my planned shift
pattern would have to be 1-2-3-4-5-6-11-12.
GUESS WHAT?! ALL
of these concepts apply equally well to the 4x4. With multi-speed
transmission and one or more 2 speed transfer-cases we have a wide array
of gear choices, often spread all over the place. The thing is,
we often talk only of our lowest gear and seldom, if ever, does anyone
chart their whole range of possible gear ratios and which are useable
(and in what order).
Well, before I decided to upgrade
my T-cases gear set, I did just that, and then re-did it with the numbers
from the Tera Low kit. The results were dramatic, to say the least
- and convinced me that this was the right route to go - even over
changing to an aftermarket transfer case.
Here are my available gears
before the Tera Low upgrade:
Gear Selection |
Front chain
wheel teeth (drive) |
Rear freewheel
teeth (driven) |
Ratio (drive/driven) |
% jump from
last |
1 |
42 |
24 |
1.75 |
n/a |
2 |
42 |
21 |
2.00 |
14% |
3 |
42 |
19 |
2.21 |
11% |
4 |
42 |
17 |
2.47 |
12% |
5 |
42 |
15 |
2.80 |
13% |
6 |
42 |
13 |
3.23 |
15% |
7 |
52 |
24 |
2.17 |
-33% |
8 |
52 |
21 |
2.48 |
14% |
9 |
52 |
19 |
2.74 |
11% |
10 |
52 |
17 |
3.06 |
12% |
11 |
52 |
15 |
3.47 |
13% |
12 |
52 |
13 |
4.00 |
15% |
(The Wolf's axle ratio of 4.1:1
is not shown because it is consistent for all cases, though it is included
in the calculation of the final ratio; in addition, both the NP 203 and
D20 high (H) and low (L) ratios are 1:1 and 2:1 respectively, and the
SM 465 gears are: 1 - 6.55, 2 - 3.58, 3 - 1.57 4 - 1.00)
Note that 4 of the gears are
completely wasted since the low ratios of the 2 transfer cases in the
Wolf are the same. Note also that 26:1 and 27:1 are so close as
to be indistinguishable, as are 15:1, and 16:1, so if we delete those,
we are left with only the following final ratios:
Final ratio |
% Jump |
4 |
|
6 |
50 |
8 |
33 |
13 |
63 |
15 |
15 |
26 |
73 |
29 |
12 |
54 |
86 |
59 |
9 |
107 |
81 |
Looking at this table, a couple
of things should become immediately apparent:
1) There are still "unusable",
or at least "indistinguishable" gear ratios - experience tells
me anything less than about a
10-15% change is pretty hard to detect and therefore pretty meaningless
- so the actual number of useable gears I have at my disposable, even
with dual transfer cases, is actually pathetically low. Out of a
possible number of combinations totalling 16, I really only have 7 gears
(just like my 12 speed bicycle is really only an 8 speed)
2) On the other side of the
coin, there are some HUGELY wide ratio jumps - from 59:1 to 107:1 for
example, (an 81% jump) - leaving a big gap in drivability - which can
not only kill performance over a variety of terrain (especially as it
changes from gnarly obstacle to mixed trail to easy spots - as most trails
do), but can also make the rig a pain in the a$$ to drive.
The beauty of upgrading the
guts of my T-case with the Low 20 kit is that it not only significantly
improves my overall lowest low, but also has a huge effect on these two
problem areas.
Results coming at the end of
the article.
Dana
20 Teardown |
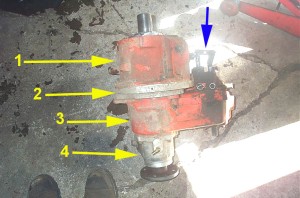 |
You're on your
own for removing the Dana 20 from your vehicle, as there are endless possible
configurations. For example, here you can see my custom transfer
case doubler removed from the Wolf and consisting of:
- NP 203 low range gearbox
- Custom machined aluminium
doubler adapter
- Dana 20 ('79 Jeep CJ7 variety)
- Advance Adapters Dana 20
output kit
For orientation, the blue arrow
in the pic indicates the shift rods of the Dana 20.
|
|
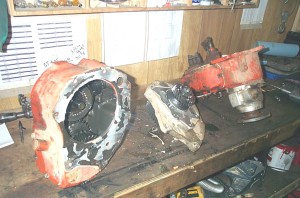 |
In my case, the first task was
to separate the Dana 20 from the rest of the transfer case components.
From left to right we can see the NP 203 low range box, the doubler adapter,
and the separated Dana 20. |
|
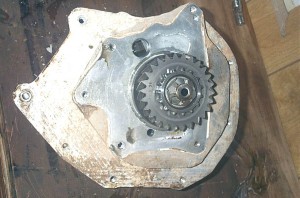 |
This shot shows the Dana
20 input gear attached to the doubler adapter via the output shaft of
the custom machined (shortened and re-splined) 203 output shaft.
In non-doubler installations,
this D20 input gear will be on the transmission's output shaft. |
|
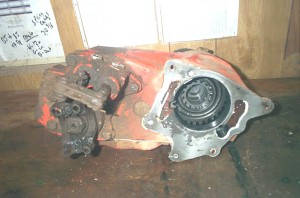 |
Front view of the removed Dana
20. |
|
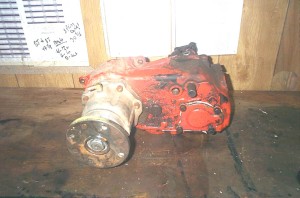 |
Rear view of the Dana 20. |
|
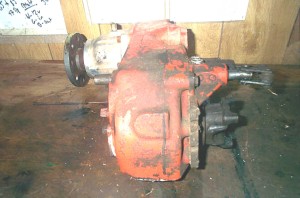 |
Right side view of the Dana
20. |
|
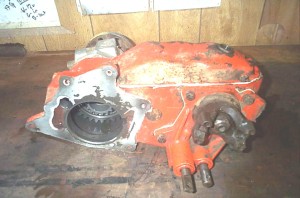 |
To begin the teardown of the
transfer case, place it on a sturdy bench, upside down with the lower cover
facing up, as shown here. |
|
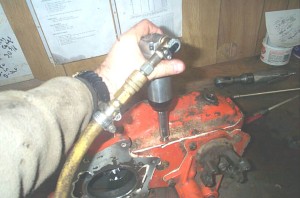 |
Begin by removing the bolts
that hold on the lower cover... |
|
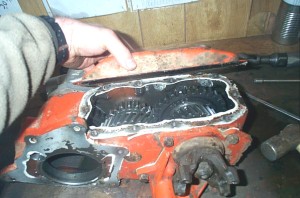 |
...and remove the lower cover. |
|
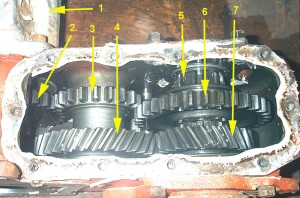 |
Inside the stock Dana 20 we
have:
- Rear output shaft (in this
case, not stock, but Advance Adapters 32 spline kit)
- Rear sliding gear
- Intermediate gear
- Intermediate gear
- Front output shaft
- Front sliding gear
- Front output gear
*not shown in this view is
the main drive gear (input gear) which is still attached to the doubler
adapter at this point (see above) |
|
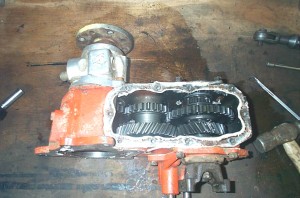 |
As above, from greater distance |
|
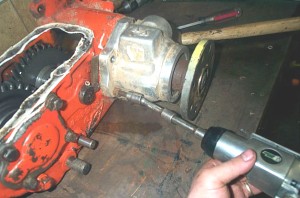 |
Remove rear output shaft housing
assembly. Procedure is similar whether output housing is stock or
aftermarket. |
|
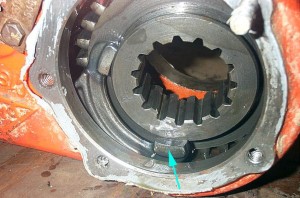 |
Once the rear output shaft assembly
is removed, disconnect the rear sliding gear from the jaws of the rear shift
fork (blue arrow). |
|
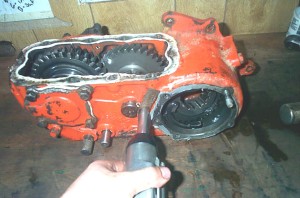 |
Next,on the front of the case,
remove the transfer cases tag (if it's still present) and the lock plate
for the intermediate shaft. |
|
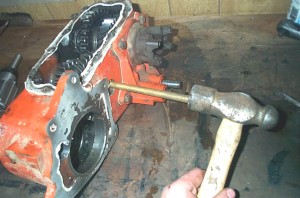 |
From the front of the case,
and using a brass or other soft drift, drive the intermediate shaft to the
rear of the case... |
|
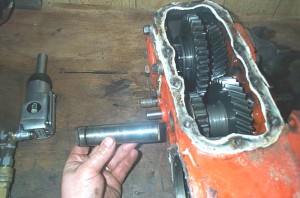 |
...and then remove it from the
case. |
|
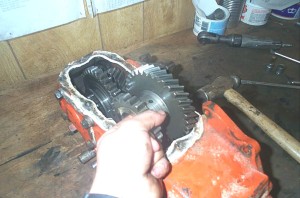 |
Wiggle the rear sliding gear
out of the way (now that it is released from its shift fork) and then lift
the intermediate gear from the case. |
|
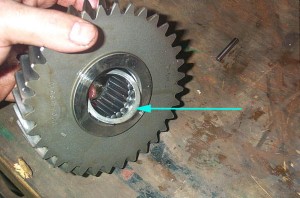 |
Be careful when removing the
intermediate gear, as their are 3 silver bearing spacers (one on each side
(blue arrow) and one in the middle seperating the 2 rows of needle bearings)
in the gear that sandwich the large roller bearings. Remove the gear,
and then remove the bearing spacers and roller bearings and store them carefully
out of the way. |
|
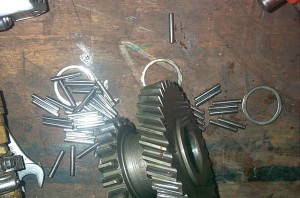 |
If you are not careful - and
you drop or bobble the intermediate gear - this is what you get. |
|
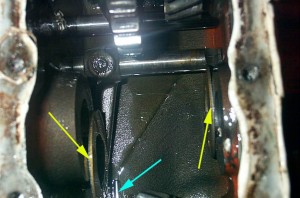 |
Once you have removed the intermediate
gear, there will be 2 thrust washers left in the case (yellow arrows).
Make a careful check for any loose needle bearings still in the case (blue
arrow) |
|
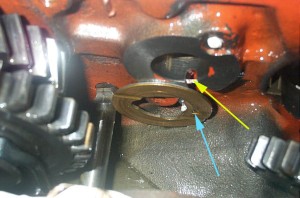 |
Take note of the orientation
of the thrust washers for reassembly time. Each has a small tab (blue
arrow) that indexes with a slot in the case (yellow arrow). |
|
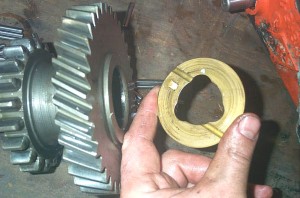 |
This shot shows the inside face
(i.e. the side that faces towards the middle of the case) of the thrust
washer. This is the side that goes up against the intermediate gear
on installation. |
|
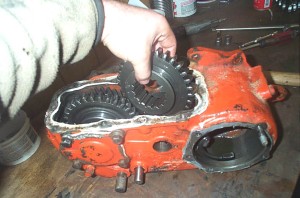 |
Once the intermediate gear is
removed, you have room to reach in and wiggle out the rear sliding gear. |
|
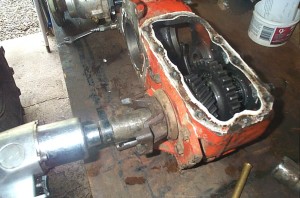 |
Next remove the nut retaining
the front output yoke. |
|
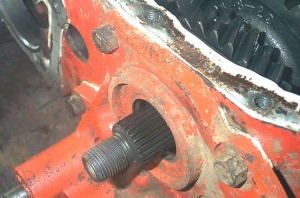 |
Remove the nut, washer, yoke
and shim washer from the shaft and you are left with this. |
|
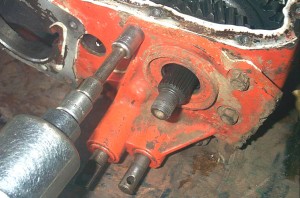 |
Next remove the bolts that hold
the front output housing to the case. |
|
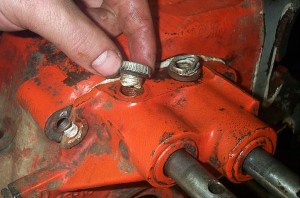 |
Tap or pull both shift rods
to their centre (Neutral) positions. Next, remove the caps covering the
detent balls and springs (also called "poppet balls" - these
springs and round ball bearings are those that keep the shift lever(s)
in the gear you select.)
I found the easiest way to
shift the rods was to insert a small punch through the hole in the end
and use it for leverage. |
|
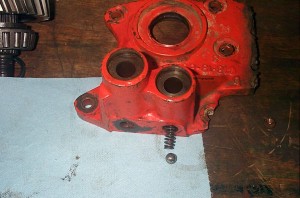 |
This shot shows the poppet ball
and spring in relation to the housing. |
|
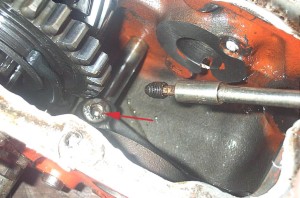 |
Remove the rear output shift
fork set screw with an Allen wrench. |
|
 |
Rotate the rear shift rod 1/4
turn to free it from the shift interlock pill (this is the capsule shaped
pill that rests between the 2 rods, preventing the stock case from being
shifted into 2 different ratios front and rear.) Then, grasp the rear shift
rod cap at the rear of the case with pliers, and twist / pull it free (it
is just a press fit). Then take a brass or other soft punch and drive
the rear shift rod out of the case from the rear. As you drive it
out, catch the detent spring and ball as they come out of their housing. |
|
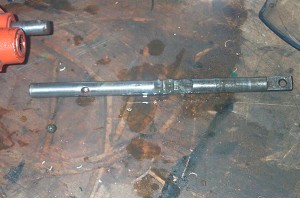 |
Removed shift rod and poppet
ball. Note on the shift rod, from left to right, you see the shift
fork set screw detent, followed by the three gear selection detents.
The interlock detent is not visible in this shot. |
|
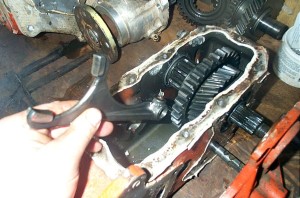 |
With the shift rod removed,
remove the shift fork from the case, noting its orientation for installation. |
|
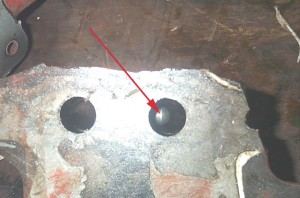 |
Next, remove the front output
housing from the case, catching the front shift rod poppet ball and spring
as you do so. If you look at the shift rod holes in the housing from
the rear (the face that mates to the case) you can see the interlock pill
where it sits in the housing between the shift rods (red arrow). You
may have to tilt the housing side to side so it is visible through the shift
rod holes. |
|
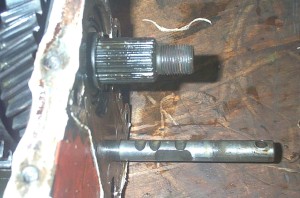 |
You are now left with just the
front shift rod protruding. |
|
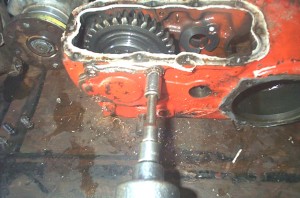 |
Remove the front output shaft
bearing cap from the rear of the case. |
|
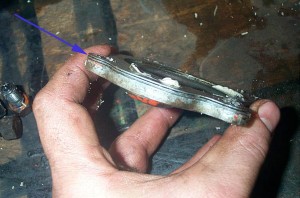 |
Be careful not to lose or damage
the delicate shims between the bearing cap and the case (blue arrow). |
|
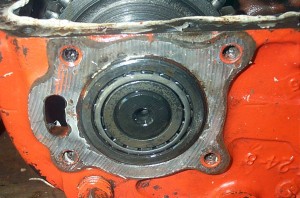 |
Rear of front output shaft,
under bearing cap. |
|
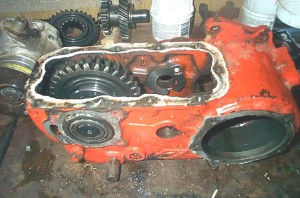 |
You should now be at this stage
here. |
|
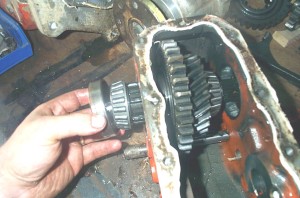 |
Using a hammer and brass or
wooden drift, strike the front of the front output shaft and drive the front
output shaft towards the rear of the case, then remove the bearing cup (race)
from the cone (bearing). |
|
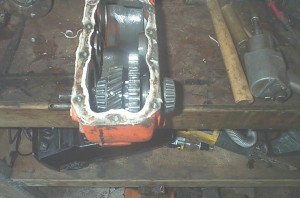 |
You should now have a transfer
case that looks like this |
|
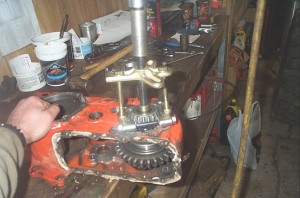 |
Remove the front output shaft
rear bearing from the shaft using a bearing separator and harmonic-balancer
type puller. |
|
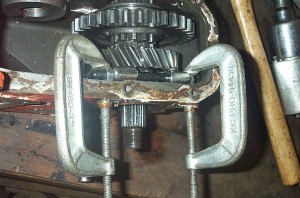 |
Now comes the only slightly
tricky part of the whole disassembly. You have to remove the front
bearing from the front output shaft. I used a small bearing separator
to get behind the bearing, inside the case. I then used 2 small c-clamps
to hold the bearing separator against the front of the case... |
|
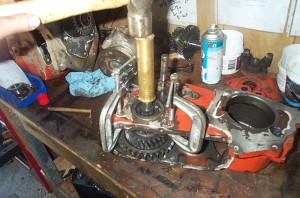 |
... and then used a brass drift
to drive the output shaft back through the case , separating the bearing
from the shaft. |
|
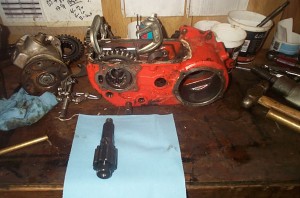 |
The shaft can then be removed
through the rear of the case. |
|
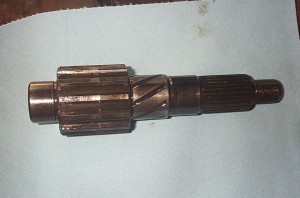 |
Detail of the removed front
output shaft. |
|
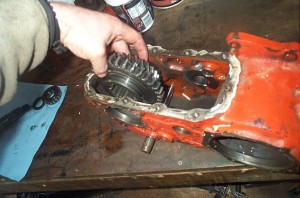 |
Once the shaft is removed, you
can remove the front output gear and front sliding gear from the case. |
|
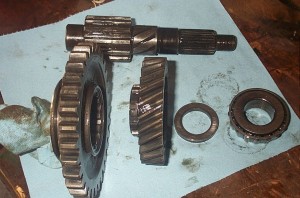 |
Shaft in the background,
foreground showing from left to right (rear of case to front)
- Front sliding gear
- Front output gear
- Washer
- front bearing
|
|
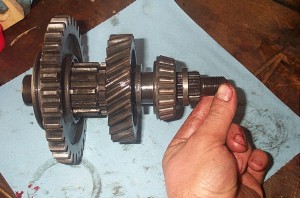 |
Components of front output shaft
assembly in the order in which they are on the shaft when assembled. |
|
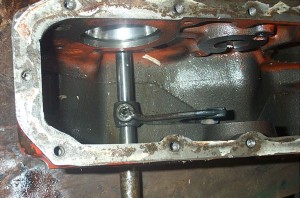 |
Case now looks like this. |
|
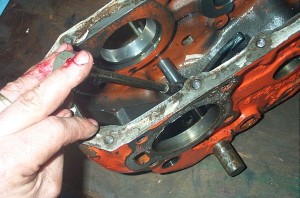 |
Remove front shift rod set screw. |
|
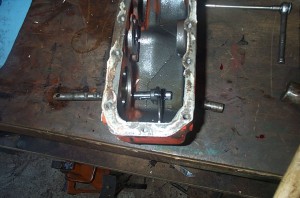 |
Pull shift rod from case, and
disengage the front shift fork from the shift rod. |
|
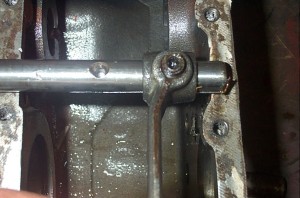 |
Detail of shift rod removed
from case, with shift fork reinstalled. To the left of the shift fork
is the detent into which the set screw must index on assembly. |
|
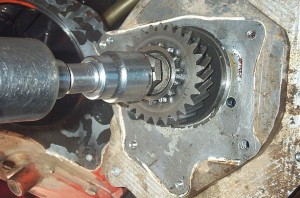 |
The final step of tear-down
is to remove the main drive gear (input gear) from whatever it is attached
to - in my case my doubler adapter. I used an impact wrench to break
the nut loose... |
|
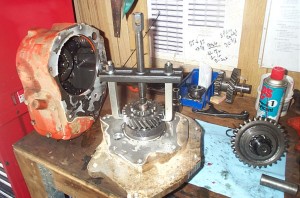 |
... and then a gear / bearing
puller to separate the gear from the shaft. |
|
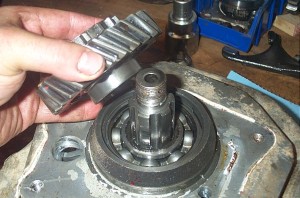 |
Once it is loose, remove the
main drive gear from the shaft. |
Once everything is torn down, carefully
clean and inspect all parts, ready for installation of the Tera Low kit.
You want to thoroughly degrease the case so that any grinding dust created when
you clearance the case for the new rear sliding gear does not get trapped and
form a grinding paste.
Tera
Low Low-20 Kit |
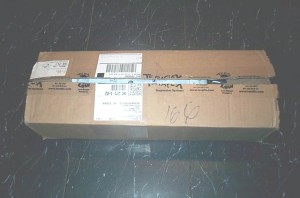 |
The kit arrives
well packaged in a single box. |
|
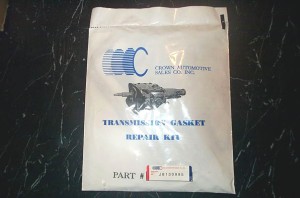 |
It includes a third-party gasket
and seal kit from Crown Automotive - pat number J8130995 for the Jeep D20
application. The seals are useful, but the gaskets are junk - none
of them fit properly and you may as well throw them away right now.
No big deal - you want to use silicone anyway. |
|
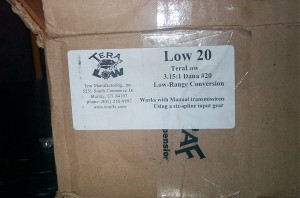 |
Box label and part number. |
|
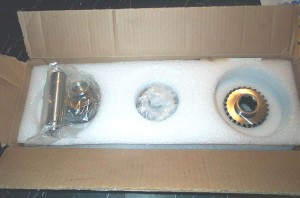 |
The gears are well protected
by form-fitting packing foam. |
|
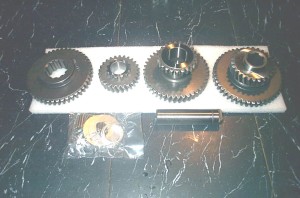 |
The gear set all laid out.
From left to right:
- Rear sliding gear (TL20-E)
- Main drive gear (input gear)
(TL20-A)
- Intermediate gear (TL20-B)
- Front Output gear (TL20-C)
on top of front sliding gear (TL20-D)
In the foreground are the new
intermediate gear thrust washers, needle bearings, and the new intermediate
gear shaft. |
|
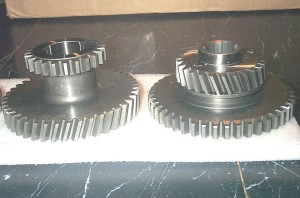 |
Detail of Tera Low intermediate
gear and front gears. |
|
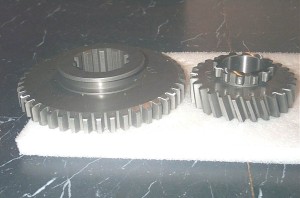 |
Detail of rear sliding gear
and main drive gear. |
|
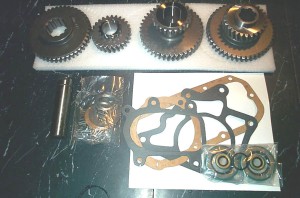 |
The complete kit. |
|
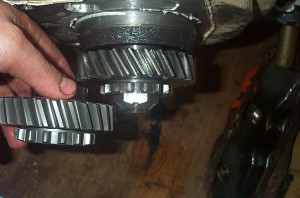 |
Comparison of the old drive
gear installed, and the new Tera Low drive gear in hand. |
Clearance
checking and case grinding |
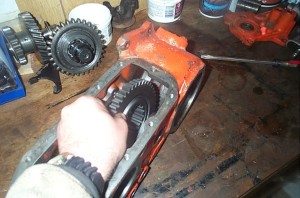 |
Most Dana 20 cases will require
some minor clearance grinding to fit the new, larger rear sliding gear.
Place the rear sliding gear in the case and then put the output housing
in place so you can place the sliding gear on the rear output shaft. |
|
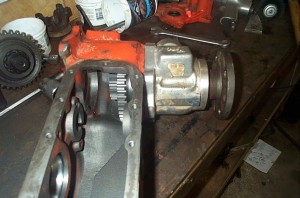 |
You will have to check for clearance
and mark the case for any required grinding through the entire range of
travel of the rear sliding gear - from all the way to the rear of the case,
as shown in this pic... |
|
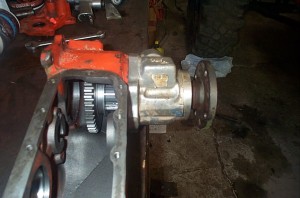 |
... to all the way towards the
front of the case, on the shaft, as shown in this pic. If you don't
do this, you could find yourself clearancing the case, assembling everything,
and THEN finding out that the sliding gear will not slide properly.
Ask me how I know! |
|
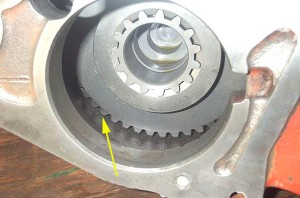 |
Rotate the rear output shaft
and check where clearancing is required between the gear and case.
Yellow arrow shows the general area. |
|
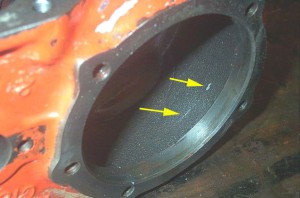 |
After rotating the gear in the
case, the slight contact between the gear teeth and the case left noticeable
marks in the casting flash of the case (yellow arrows), making it easy to
know where to grind. |
|
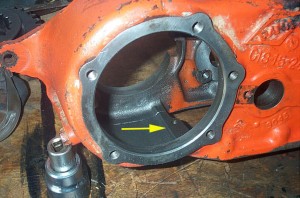 |
This view, from the rear of
the case with rear output housing removed, shows the ridge that needs to
be smoothed out (yellow arrow). |
|
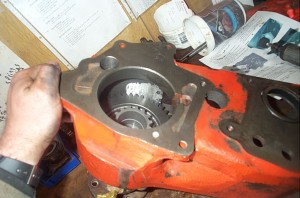 |
Shot of the lip smoothed down
with a die grinder. |
|
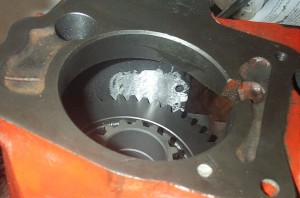 |
Close up shot of same. |
|
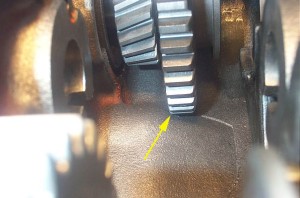 |
With the rear sliding gear all
the way to the front on the rear output shaft, slight grinding of the hump
may be required. Here you can see the gear teeth just contacting. |
|
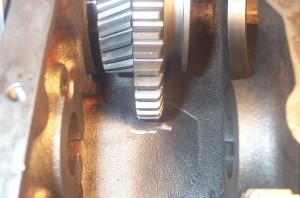 |
Clearance grinding complete |
|
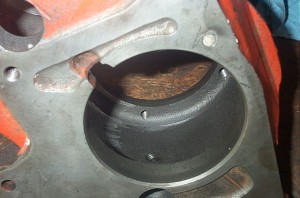 |
Here you can see the final spot
that needed a little clearancing... |
|
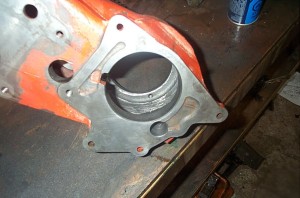 |
... and the finished grinding.
The grinding involved was quite
minimal, and only took a few minutes with a small air-powered die grinder
and a couple of different shaped grinding stones. I used a cone
shaped one and a cylinder shaped one.
When you're done, it is ESSENTIAL
that you thoroughly clean the entire case and any parts in solvent and
dry them. You do not want any grinding dust to find it's way into
the bearings or between the gears. |
Installing the kit
Once you have the old case torn down, clearanced, cleaned and inspected, it's time to install the new gear set.
Installing Main Drive Gear |
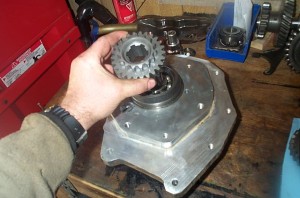 |
The first step is to install the new main drive gear. Place it on the transmission or doubler output shaft. |
|
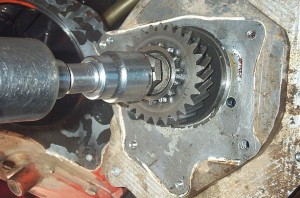 |
Install the washer and nut using thread locking compound, torque to spec,
and if your installation requires it, install a new cotter pin. |
|
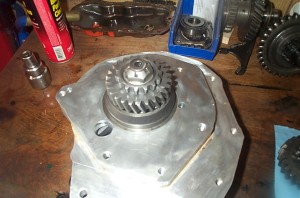 |
My doubler all cleaned up and ready for reassembly. |
|
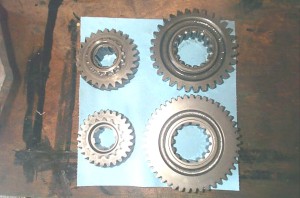 |
Another look at the new gears that go in the case. |
Reassembling the Case |
 |
Place a little RTV sealant on the ends of the shift rod caps and tap them
into their bores in the case. |
|
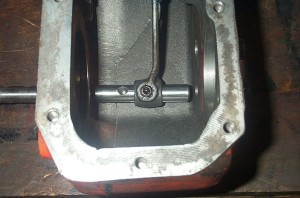 |
Slide the front shift rod part way into the case and slip the front shift
fork over the end and onto the rod. |
|
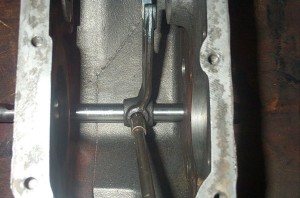 |
Line up the shift fork with the detent in the shift rod and install the
set screw. Tighten to 14 ft lbs. |
|
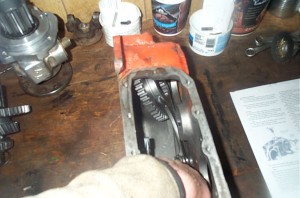 |
Place the rear sliding gear and rear shift fork into the case in their
proper orientation. Make sure the sliding gear is installed the right
way around - with the slot in the sliding gear towards the rear of the case. |
|
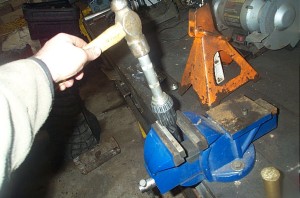 |
Using a bearing driver or press, drive the front output shaft rear roller
bearing in place on the shaft. |
|
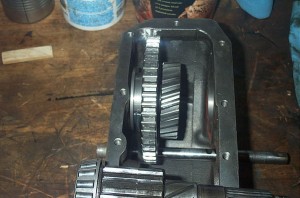 |
Place the front sliding gear and front output gear in place in the case.
Make sure the slot in the front sliding gear faces the rear of the case
and engages with the front shift fork. Hold both gears in place in the case... |
|
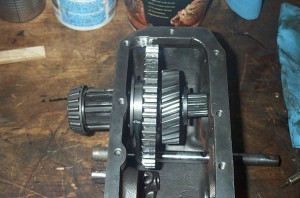 |
... and then slide the front output shaft into the case from the rear
of the case. |
|
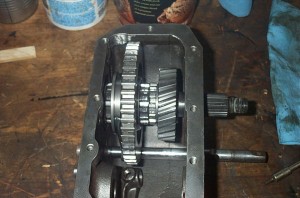 |
The front output shaft and gears in place should look like this. |
|
 |
Using an appropriate driver, drive the front output shaft rear bearing
cup (race) into its bore in the rear of the case. |
|
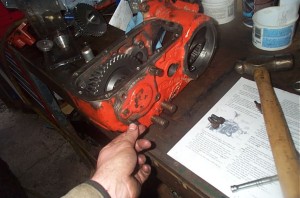 |
Place a thin bead of RTV sealant on the shim closest to the case, then
install the shims and bearing cap and tighten the bolts to 30 ft lbs. |
|
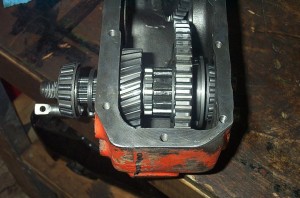 |
Slide the front output shaft washer and front roller bearing onto the
shaft. |
|
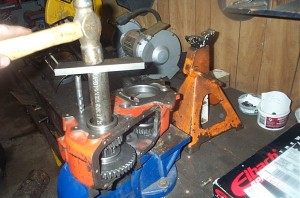 |
Drive the roller bearing into place on the shaft - I used a length of
1.5" Schedule 40 pipe and a steel block. |
|
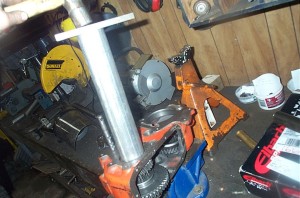 |
Next drive the front output shaft front bearing cup (race) into place
- I used a length of 3" exhaust tube and steel block. |
|
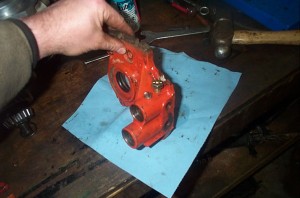 |
Install a new front output shaft yoke seal and new shift rod seals in
the front output housing. |
|
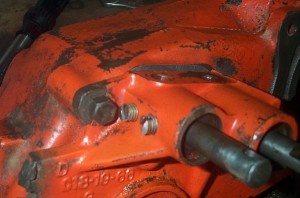 |
Lay a thin (1/8") bead of RTV sealant around the edges of the
case where the front output housing mounts. Place the front shift
rod detent spring in the front output housing, then start the housing
onto the front shift rod (ignore the fact that the rear shift rod is installed
in this pic). Place front poppet ball on top of spring and depress into
housing with a punch, tilt transfer case to slide interlock pill to right
if required, and slide the front output housing into place over the front
shift rod. |
|
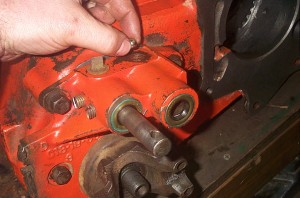 |
Place rear shift rod detent spring and poppet ball into front output housing. |
|
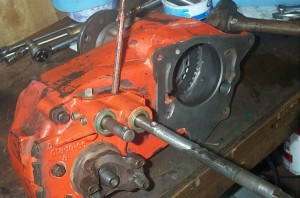 |
Depress poppet ball with punch, and slide rear shift rod into housing
with the shift fork detent facing up. |
|
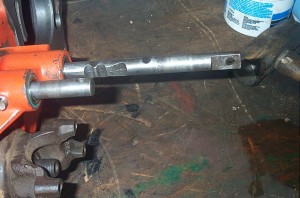 |
Once started past the poppet ball, rotate the rear shift rod 1/4 turn
counterclockwise, as shown, so that poppet ball doesn't hang up on the
detents in the shift rod. |
|
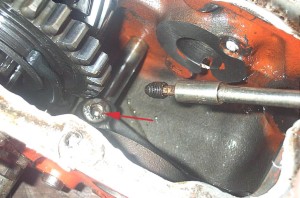 |
Make sure the rear sliding gear and shift fork are positioned properly
in case, and slide rear shift rod into case, and through shift fork.
Align shift fork with shift fork detent in rear shift rod, then tighten
set screw to 14 ft lbs. |
|
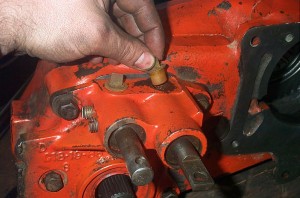 |
Install front output housing
bolts and torque to 30 ft lbs.
Install poppet ball caps.
Check front output shaft end-play
by prying the shaft alternately to the rear and then to the front of the
case. The proper method is to measure the end-play with a dial indicator.
I must admit - I went by "feel". End-play should be between
.001 and .003 inch. If it needs to be adjusted, you do so by adding
or subtracting the shims under the front output shaft rear bearing cap.
Note that there are no extra shims in the kit, so if you need them, you
will have to source them separately. |
|
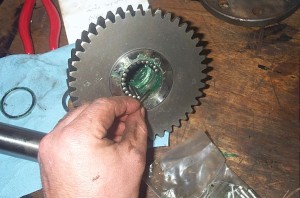 |
Install the needle bearings
in the intermediate gear with grease. Note that there is a row of
needle bearings on each side of the gear, with a bearing spacer / washer
separating the 2 rows in the centre of the gear, as well as one on each
side. |
|
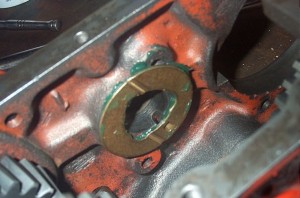 |
Install the intermediate gear
thrust washers in the case with heavy grease, being sure to align the tangs
with the slots in the case. |
|
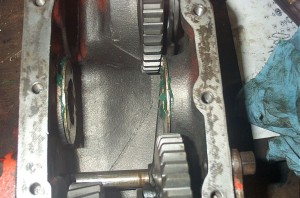 |
The installed thrust washers
should look like this. |
|
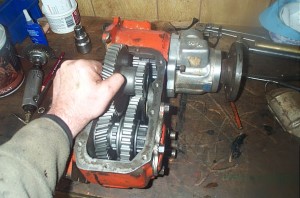 |
Carefully drop the intermediate
gear into place, being careful not to knock the needle bearings, bearing
spacer washers or thrust washers out of place or alignment. It can
be quite tricky and may take a few tries. I found it helpful to rotate
the gear a little as I lowered it into place. |
|
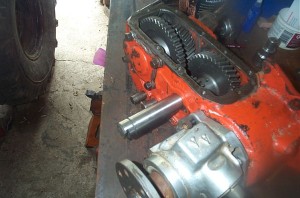 |
Start intermediate gear shaft
into case by hand. |
|
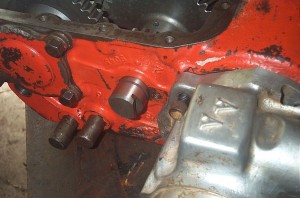 |
Once it begins to get tight,
make sure the groove in the shaft faces the lock plate bolt hole. |
|
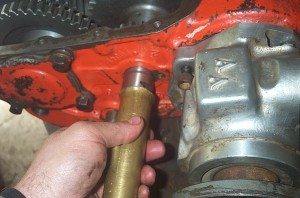 |
Then drive the shaft home with
a brass or other soft drift. |
|
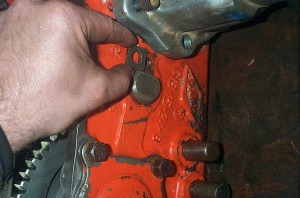 |
Install the lock plate... |
|
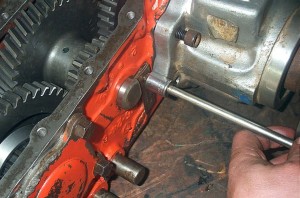 |
...and the transfer case
tag and then install and tighten the lock plate bolt to 14 ft lbs.
Check for clearance between
the intermediate gear and the rear shift rod.
Rotate the gear. If there
is any contact seen, heard, or felt between the gear and the front shift
rod, you will have to remove the shift rod and grind a little for clearance. |
|
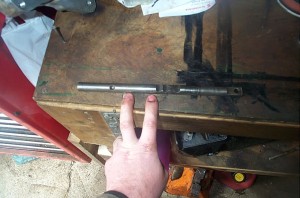 |
The area in question that will
need to be clearanced is shown here between my fingers. |
|
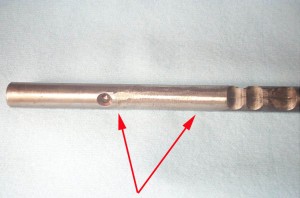 |
The red arrows show the are
where I ground my shift rod slightly for clearance. |
|
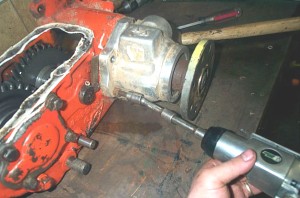 |
Coat rear output housing with
RTV and install, tightening bolts to 30 ft lbs. |
|
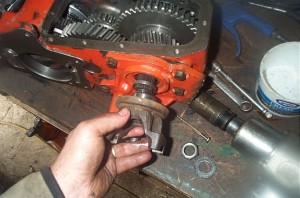 |
Install front output thrust
washer and yoke. |
|
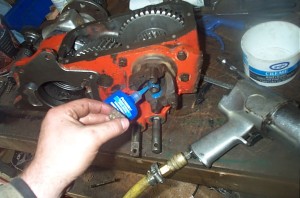 |
Apply thread locking compound. |
|
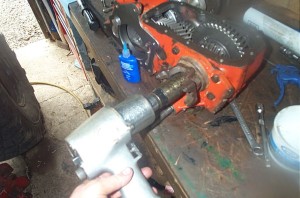 |
Tighten front output shaft
yoke nut to 225-250 ft lbs. |
|
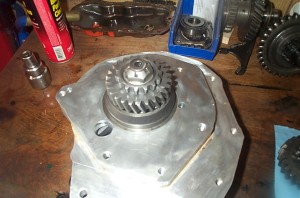 |
In my installation, the next
thing I needed to do was install the doubler adapter with the main drive
gear installed on it, back on the transfer case so I could turn the gears
and check the case assembly and shifting operation before sealing up the
case. |
|
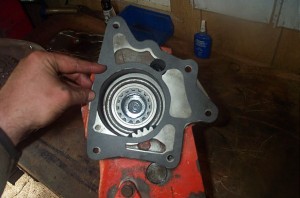 |
This shot shows the poor,
worthless quality of the Crown Automotive gaskets. Useless!! |
|
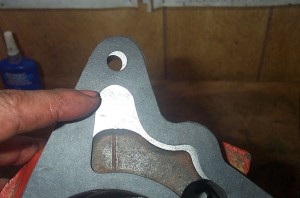 |
I'm not a big fan of gaskets
anyway, and prefer a good, high quality RTV sealant / gasket making compound
- but it's pretty poor when the bolt holes don't even line up. Like
I said at the beginning - might as well just throw them out. |
|
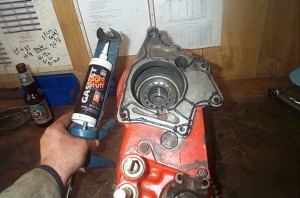 |
This is the stuff you want
to use - either The Right Stuff, or the factory GM RTV - they are the
best two gasketing products I have used .
The last thing to do before
bolting the lower cover back on and filling the case with 80w90 gear oil
is to check the operation. |
Checking Case Operation
To check the case operation and ensure
that you have all the parts in the right place, proceed as follows:
- Assemble the case completely,
except for the bottom inspection cover.
- Place the case upside down on
the bench with the shift rods towards you.
- Place some sort of support (a
chunk of 2x4 worked for me) under the rear output housing so that the rear
output flange can turn freely.
- Arrange the case so that you can
turn the main drive gear (input gear). I accomplished this by bolting
my doubler adapter to the case and turning the NP 203 output gears by hand
- thus driving the input gear of the transfer case.
- Dana 20 shift positions are controlled,
via the shift rods and shift forks, by the positions of the front and rear
sliding gears. For both sliding gears, towards the front of the case
is high gear, in the middle is Neutral, and to the rear of the case is Low
gear. I deleted the interlock pill on reassembly, enabling "twin
stick" operation - i.e. the ability to shift the front and rear outputs
independently.
- With the transfer case installed
the right way up in the vehicle, the following are the shift lever, shift
rod, and sliding gear positions for each gear possibility (interlock pill
removed). Note that these listings are for the case "as installed"
in the vehicle, with the CAN/US drivers position the left of the vehicle.
Note that because the fulcrum of the shift levers is above the shift rods
when the transfer case is installed in the vehicle (i.e. the shift levers
pivot about a point that is above the shift rods), the shift lever positions
are the OPPOSITE of the shift rod positions for high and low gears.
With the transfer case on the bench, make sure you can smoothly shift between
all of the following positions, with no binding, ratcheting, grinding, etc.
It shouldn't be hard to shift - you should be able to do it with strong hand
pressure on a punch or lever inserted into the front shift linkage hole of
each shift rod. You may have to rotate the gears slightly to get the
teeth to line up as you shift.
Gear |
Rear
(left) shift rod & sliding gear position |
Rear
(left) shift lever position |
Front
(right) shift rod & sliding gear position |
Front
(right) shift lever position |
Picture |
Rear Low |
rear |
forward |
middle |
middle |
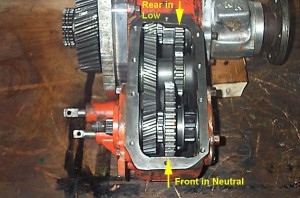 |
Rear High |
forward |
rear |
middle |
middle |
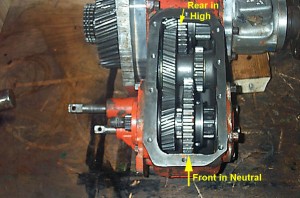 |
Front Low |
middle |
middle |
rear |
forward |
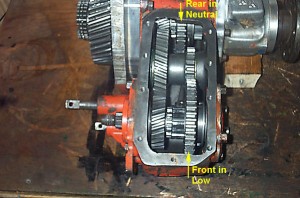 |
Front High |
middle |
middle |
forward |
rear |
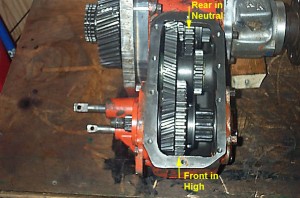 |
4 Low |
rear |
forward |
rear |
forward |
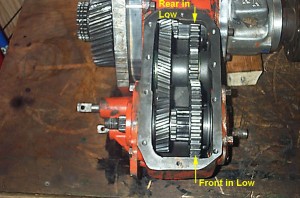 |
4 High |
forward |
rear |
forward |
rear |
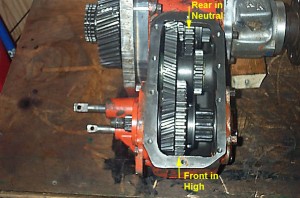 |
Neutral |
middle |
middle |
middle |
middle |
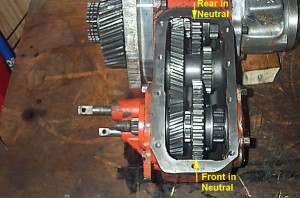 |
|
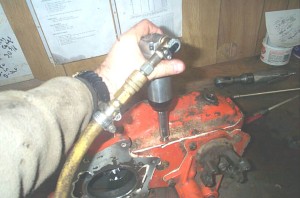 |
Once you are done with checking,
install the lower cover using RTV and torque the cover bolts to 15 ft lbs. |
Installing
the case in the vehicle |
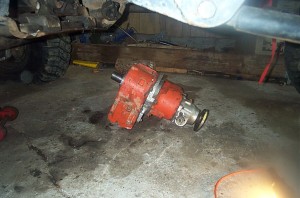 |
This was probably
the hardest part of the whole project. Here you can see my complete
doubler transfer case assembly ready to be installed - it's one heavy
SOB, and pretty tricky to get in place, lined up, and the bolts all started
without cross-threading!.
As with all the other mating
surfaces, you must gasket the transfer case to transmission joint.
This was the one place where a decent gasket would be helpful, as it would
prevent inadvertent smearing of RTV as you jack, strap, and struggle to
get the case installed and lined up. |
|
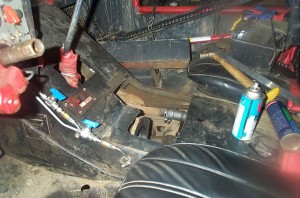 |
I ended up having to cut
a hole in the floor... |
|
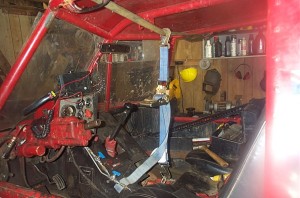 |
...then putting one strap around
the roof of the Wolf, with another ratcheting strap extending vertically
from there, through the hole in the floor, to a chain wrapped around the
transfer case. |
|
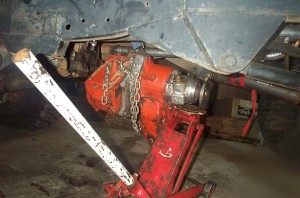 |
Then with a floor jack on the
output housing for additional support and to help clock the case to the
right position, I was able to get it all lined up and installed. |
|
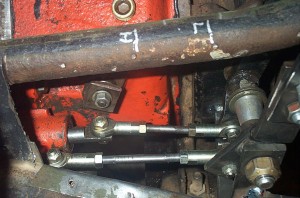 |
Detail of my home-brew
shift linkage. This pic illustrates how, when you shift the lever
forward, you are actually shifting the shift rod to the rear. |
|
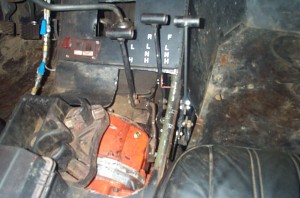 |
From left to right are:
- NP 203 low-range box shifter
- Dana 20 rear axle shifter
- Dana 20 front axle shifter
Note that if you remove the
interlock pill and twin-stick your case, there is the possibility to shift
one axle into low gear and the other into high at the same time.
This will quickly cause serious drivetrain damage (although I did try
it briefly on a soft, loose surface, just to see what it was like.)
Some folks may decide to rig up some sort of extra mechanism to allow
twin -stick shifting while preventing the levers from being more than
one position apart. I didn't bother, as the shift pattern arrangement
would mean that to inadvertently shift into low-high or high-low, one
stick has to be all the way forward, and one all the way to the rear -
which is really obvious, and hard to do accidentally. Also - if
the rig is in low-high or high-low, it's VERY obvious as it hops and spins
and churns in a very unusual manner. |
Results
The most important part - what are
the results of this upgrade?
What you gain is:
- A 58% reduction in lowest achievable
gear ratio – in my case from a low/low of 107.4 to 169.2 !!
- Even in single-case configuration,
a low range lower than any factory/stock ratio.
- If you have a similar doubler
setup - four extra gears (one in each transmission gear), now that the 2 cases
low ranges are no longer identical. i.e. now L/H and H/L are no longer identical.
But the greatest improvement relates
back to what I was saying at the beginning about "gear stepping" or
"ratio spanning".
Recall my original gear table:
Final ratio |
% Jump |
4:1 |
|
6:1 |
50 |
8:1 |
33 |
13:1 |
63 |
15:1 |
15 |
26:1 |
73 |
29:1 |
12 |
54:1 |
86 !!! |
59:1 |
9 |
107:1 |
81 !!! |
What I was really missing was a gear
between my low / low and the next lowest gear. That is, something between 59
and 107, as well as something between the next 2 gears i.e. (29 and 54). I knew
this just from driving the rig - even before charting the math involved.
In other words, my lowest gears (deeper than about 25:1 which is what I use
most on the trail) used to be
27, 29, 54, 59, 107.
Now I have
27, 29, 41, 46, 54, 85, 92, 169
You just don’t get choices
like that with a fancy aftermarket transfer case. If I had, for example a 4.3
low ratio Atlas II, I would have:
27, 28, 63, 115, or in effect, only
3 really usable gear ratios, for twice the price. To me, that is far from the
ideal setup.
In my opinion, it’s all about
3 things:
- Options for different terrains
- Ratio spanning or % jump between ratios; and
- The lowest low you can get
Judged by that criteria, and by real
world budget constraints, with the option of building over time, the low buck
doubler with aftermarket gears in one transfer case comes out as an awesome
option - and one I am extremely pleased with and don't regret one bit.
Testing |
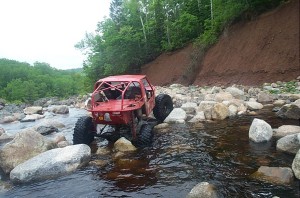 |
The rig is now
much more of a pleasure to drive. Whether you're driving a performance
car, a rock buggy, or pedalling a bicycle - huge jumps in gear ratio suck! |
|
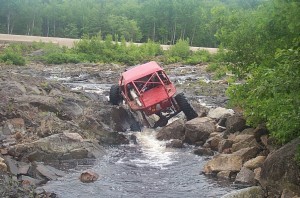 |
In the kind of rocky, slippery
terrain I prefer, shown here, the extra gears, and especially the way
low 169:1 give me great improvement in control and drivability. |
References:
|