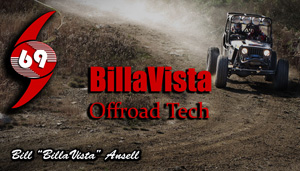 |
Mobile Home Trailer Axles
By Bill "BillaVista" Ansell
Photography: Bill Ansell
Copyright 2008 - Bill Ansell
(click any pic to enlarge)
|
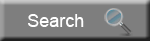 |
Introduction
My first-ever trailer was a rough old home-built piece of junk with what, at the time, I called "wierd, 5-bolt wide-pattern wheel thingey" axles.
I found out later that they were mobile home axles.
Turns out, many home-built and construction-site trailers use mobile home axles as they are cheap and strong and often come with brakes.
The drawback is, they are not really designed (and may not be legal in your area) for long-term use. This means thay are not assembled with service in mind, and replacement parts can be hard to come by. |
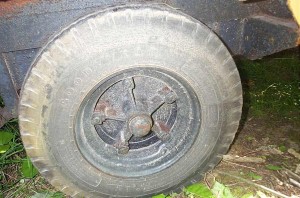 |
There's also not a lot of tech info out there available for them. I can't do anything about the design, or the availability of parts, but I can share what i learned about them while I was running them. |
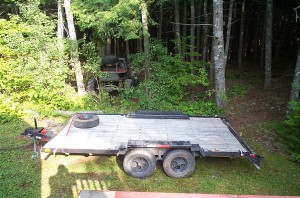 |
This is what my first trailer looked like.
Built in Cape Breton by a coal miner, from scrap metal taken from a WWI battleship. |
|
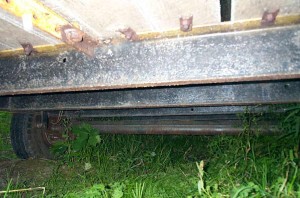 |
Mobile home axles underneath. |
|
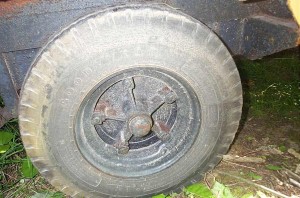 |
This is what the wheel and hub look like assembled.
Let's tear it down and look at the brakes and bearings. |
Disassembly |
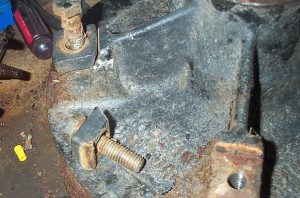 |
The first step is to remove the wheel bolts and little wedge blocks that
clamp the wheel onto the hub.
This close-up shows how it works. |
|
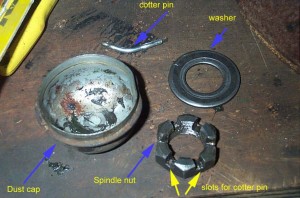 |
Once the tire and rim are removed, you pry off the hubs' grease cap with a
screwdriver, and here's the hardware you have to remove to remove the hub.
It's simply a cotter pin, castellated nut, and washer that bear on the outer
wheel bearing. Remove cotter pin, nut, and washer and the outer
bearing falls out and the hub slides off the spindle. |
|
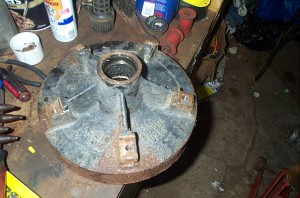 |
You prob can't
see it in the pic, but something I found really interesting, is that the
hub/brake drum assembly has a maximum diameter figure cast into it, the type
you see on normal automotive drums and rotors specifying the limits to which
they can be machined during overhaul.
Now, if these axles are indeed
intended to be one-time use only hauling a mobile home one way....then why
would this be so? I'm having a hard time picturing a mobile home being
hauled so far that along the way, you'd have to stop, remove the home from
the trailer, remove the brakes, have the drums machined, reload everything
and carry on.
Weird huh? |
|
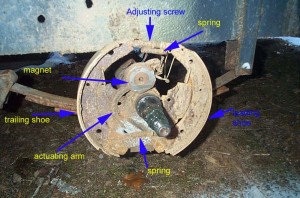 |
Under the hub is the brake assembly. Pretty standard drum brake
components, at least in function (I haven't checked dimensions for
replacement possibilities). |
|
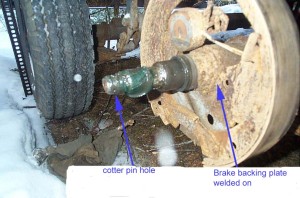 |
However, note that in this pic, the brake "backing plate" is welded - not
bolted to the axle tube, so replacement of the whole brake assembly (rather
than individual parts) will require creative fab work.
Pic also shows
the hole in the threaded spindle through which the cotter pin slides. |
|
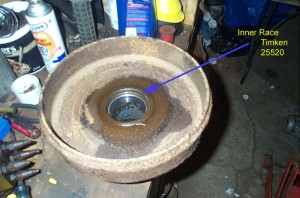 |
back side of the hub / brake drum assembly showing the inner wheel bearing
race. |
Bearings |
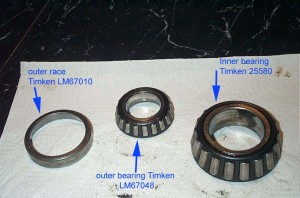 |
Here are the wheel bearings, with Timken numbers.
I had read that these
bearings were non-replaceable or non-serviceable. Well, they are
certainly available, you can order them by part number from any good bearing
shop. Alternatively, the chart below gives some applications you can
quote to the guy at the parts counter to get the same bearing (info taken from www.timkeninfo.com) .
The prices I was just quoted (Mar
2003) by my local suppler, in Canadian $, are
Outer bearing - Timken LM67048 -
$8.65
Outer race - Timken LM670101 -
$4.19
Inner Bearing - Timken 25580 -
$18.10
Inner race - Timken 25520 - $9.10 |
At first I was concerned that they may be considered "unserviceable" due to the
manner in which the bearings and hub are retained. That is to say, I
can foresee problems setting the proper wheel bearing pre-load because of
the lack of adjustability with the single-nut-and-cotter pin setup. Particularly if you look at the large distance between the slots in the
castellated nut in pic#3 above. There's obviously a pretty limited
range of adjustment, because of this large gap, because if it's not quite
right, you have to either tighten down or back off the nut quite a lot (in
big steps) to reach the next slot through which you can fit the cotter pin.
Turns out my fears were unfounded and that this assembly / arrangement is
extremely common on all types of trailer axles. See below for a couple
of procedures on how to adjust them. The short story is, screw on nut
to finger tight, while rotating hub. Continue rotating hub while
tightening another 1/4 turn or so to seat/preload bearing. Back off
nut till loose. Screw up finger tight again, then back off to the
first slot where you can install the cotter pin.
A little more research also turned up the fact that the bearing combo of
inner 25580/25520 and outer LM67048/LM670101 is also very common on 6 and
7000 lb trailer axles. You can find these bearings at any trailer
supply house.
Here's the bearing apps, should you need them:
Outer Bearing
LM67048 $8.65
Applications
1988-2002 Camaro 2.8, 3.1, 5.0. 5.7 Warner T5, T5 World
Class; 5 Spd.; frontCone
85-86 Mercury Capri 2.3, 3.8, 5.0 Warner T5, T5 World
Class; 5 Spd.; frontCone
1988-2000 Pontiac Firebird any engine 5 Spd.Cone
Outer race
LM67010 $4.19
Applications
FORD 1984-85 ESCORT 1.6, 1.9, 2.0, ; MTX-III; 5 Spd.Cup
CHEVROLET 1993-02 CAMARO 3.4 3.8 5.7 Warner T5, T5 World
Class; 5 Spd.; frontCup
FORD 1984-94 ESCORT GT 1.8 MTX-III; 5 Spd.Cup
FORD 1986-90 TAURUS MTX-II; 4 Spd.Cup
FORD 1984-94 TEMPO GL MTX-III; 5 Spd.Cup
PONTIAC 1988-2000 FIREBIRD ; 5 Spd.Cup
Inner bearing
25580 $18.10
Applications
PLYMOUTH 1965 BELVEDERE L6 3.7 3687 Exc. Station Wagon and
Taxi; Cone
PLYMOUTH 1966 BELVEDERE L6 3.7 3687 Exc. Station Wagon and
Taxi; Cone , differential bearing
PLYMOUTH 1966 SATELLITE L6 3.7 3687 Exc. Station Wagon and
Taxi; Cone
Inner race
25520 $ 9.10
Applications
PLYMOUTH 1966 BELVEDERE L6 3.7 3687 Exc. Station Wagon and
Taxi; Cone , differential bearing
FORD 1970 LTD V8 5.0 9.375" ring gear: WDR, WFH axles;
Cup
DODGE 1967 W100 SERIES V8 5.2 8.75" ring gear: 1.75"
pinion shaft OD; Cup
Wheel bearing adjustment procedures:
Method 1
- Clean the
spindle with a rag. (NOTE: The inner surface of the bearing and the spindle
shaft are machined to close tolerances. If the spindle is marred, unclean, or if
the rear bearing is not square with the spindle shaft, the bearings may
temporarily hang up as you slide the hub in place. Once the hub or hub drum is
fully in place on the spindle, slide the outer bearing onto the spindle and into
the hub. (Match the cone of the bearing to the race. DO NOT INSTALL THE BEARINGS
BACKWARD!
- At this point you are ready to pre-load the bearings. Whenever you install
new hubs onto an axle, or whenever you install new bearings and races into
existing hubs, you should pre-load the bearings. Pre-loading the bearings
assures that the races in the hub are 100% in place against their machined stop
points and keeps the hub from wobbling after a few miles.
- To pre-load the bearings, install the spindle washer and spindle nut onto the
spindle with the hub and bearings in place. Tighten the spindle nut finger tight
(until snug) and then with channel-lock pliers or a crescent wrench, tighten the
spindle nut another 1/4 turn or to about 15 to 20 ft pounds of torque. Now turn the
hub five to ten revolutions. This will fully seat the races. Now loosen the
spindle nut very loose, then re-snug to finger tight, and engage the nut
retaining device (cotter pin). (Some spindles use a tab washer for the
retaining device)
- After 20 to 40 miles of highway travel, check to see if the hub is loose on
the spindle. Pull the tire in and out a few times. If your hub is loose, you
will need to re-snug the spindle nut and re-engage the nut retaining cotter pin
or tab washer. NOTE: Never reuse the same tab on the tab washer. They are
designed to be used one time only).
- Never run your spindle nut too tight, this will cause your bearings to over heat.
And never run your bearings too loose. A very slightly loose spindle nut will
run adequately, but too loose and the individual rollers may come apart in the
bearings, causing the hub to fracture.
- You are now ready to install your dust cap. A short piece of 2" I.D. water pipe
makes a good tool to install the dust cap.
- If you are installing brakes on a "plain" spindle axle,
use plain dust caps and not "bearing protectors" (Bearing protector refers to
the spring loaded dust cap device with a grease zerk fitting in the piston.)
Bearing protectors add two to four PSI of pressure inside the hub cavity and in
many cases, they cause grease to leak past the seal. If sufficient grease leaks
past the seal on a brake hub drum, it will centrifuge out with some grease
getting on the brake shoes. Grease on your brake shoes will drastically decrease
your braking capacity.
Method 2
If the hub has been removed or bearing adjustment is required,
the following adjustment procedure must be followed:
- After placing the hub, bearings, washers, and spindle nut
back on the axle spindle in reverse order from hub removal, rotate the hub assembly
slowly while tightening the spindle nut to approximately
50 lbs.-ft. (12" wrench or pliers with full hand force).
- Then loosen the spindle nut to remove the torque. Do not
rotate the hub.
- Finger tighten the spindle nut until just snug.
- Back the spindle nut out slightly until the first castellation
lines up with the cotter key hole and insert the cotter pin (or
locking tang in the case of E-Z Lube).
- Bend over the cotter pin legs to secure the nut (or locking
tang in the case of E-Z Lube).
- Nut should be free to move with only restraint being the
cotter pin (or locking tang).
Brakes |
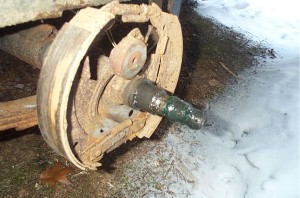 |
As you can see - all my brakes turned out to be complete junk. |
|
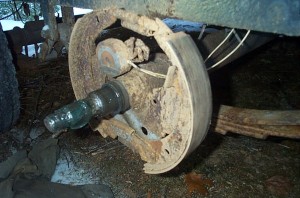 |
About the
Mobile Home axle brakes. I also discovered that mine are 12"x2", and
that this is a common size on 6 and 7000lb conventional trailer axles.
At first, I figured, there's probably no reason I can't fit "regular" 12x2
brake shoes, springs, and the little star adjuster on my mobile home
welded-on backing plate. However, I was not able to verify this for
sure because, by the time you add up the cost of shoes, springs, adjuster,
and magnet...you end up only $12 less than the cost of a complete 6000lb
axle brake assembly - already assembled (no messing with those awful
springs) on a backing plate with new magnet. Yes, this backing plate
is designed to be bolted to the flange on a regular trailer axle, but it
will be simple for me to adapt. I shall simply cut and grind the old
backing plate off, make a 1/8" square steel flange drilled to match the new
backing plate, slide it on the tube. Bolt the backing plate to it,
install and adjust hub, slide brakes to right position, square everything up
(I'm lying here - I'll prob. just eyeball it as usual), and weld on the
custom flange. Certainly can't be any harder than a custom disk brake
conversion on a 4x4 and I've done a few of those. |
Tires
After running the trailer for a while, I finally bit the bullet and bought new tires. It was
a difficult decision to dump so much cash on brand new tires in such an
odd size. However, I was convinced it was the right decision for the
following reasons:
In my recent research I have read a lot of articles and
stories about how it is essential to run properly rated trailer tires when
towing a heavy load like 7-8k lbs. Regular passenger car/truck tires
do not have the required sidewall strength and using them leads to
dangerous blowouts.
Considering how tough the tires are - Goodyear, bias ply,
7 ply tread, 8 ply sidewall, and how much I'll use the trailer, and that
the last set were probably original and on there since the mid 70s, they
should last me about forever.
While an odd size, the local Goodyear commercial tire
place has them in stock, so they can't be that rare or odd
I've read to may towing horror-stories to cut any corners
with the towing gig. These are the right tool for the job, safe, and
are probably not that much, if any more expensive than similarly rated 15"
trailer tires of equivalent quality.
Total bill came to $594 Cdn for four installed, new valve
stems (metal), old tire disposal fee, and taxes. |
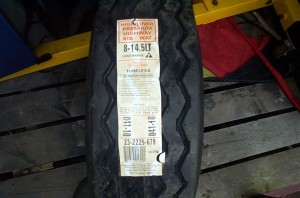 |
Here's the sticker. Made in Brazil...hey those guys sure should know
their rubber....it grows there after all. Yep - that says load range F
!! |
|
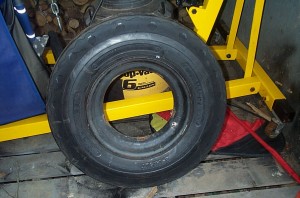 |
Here they are in all their glory |
|
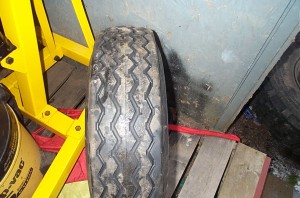 |
Not the sexiest tread, but reminds me of a lot of long-haul 18-wheelers....a
good sign |
|
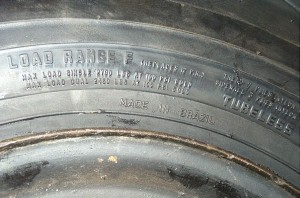 |
WOW - look at that capacity. 2790 lbs each at 100 psi!! |
|
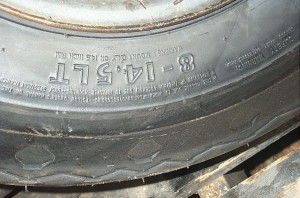 |
See, I wasn't kidding - they're 8-14.5 |
|
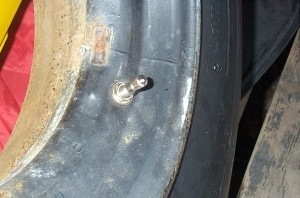 |
Fancy new valve stems. |
|