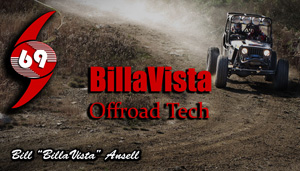 |
Dana 60 High Clearance Steering Arms
By Bill "BillaVista" Ansell
Photography: Bill Ansell
Copyright 2008 - Bill Ansell
(click any pic to enlarge)
|
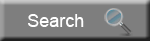 |
Introduction
I have serious issues with my steering.
I always have. I don't know if I'm a terrible driver, or it's just par for the
course - but virtually every run I do I come back with my tie-rod and/or drag
link looking like a long bow or a pretzel. It really came to a head a few weeks
ago, when during a run, I bent the tie rod back pretty badly. Nothing unusual
there, but this time, I did it so badly that when the front axle subsequently
articulated from left-wheel-down to left-wheel-up while simultaneously being
steered right, the drag link/tie rod bracket contacted my track bar bracket
and ripped it in two.
This left me with a very softly-sprung
coil rig with no track bar, virtually no steering whatsoever, and a front axle
dancing laterally back and forth as much as 2 feet. Worse - I had to limp it
out of a tough trail, and then get it on the trailer in that shape! |
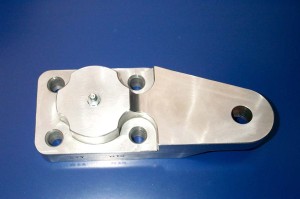 |
ENOUGH!!!! I needed high clearance
steering arms to move the steering linkage up out of harm's way (because let's
face it - it's not likely my driving will improve :-). Also, I want (actually,
desperately need) full hydrostatic (hydraulic) steering one day, so I decided
that eventually I would design that system around these same high clearance
steering arms.
So, off I went, web-shopping for
ultimate Dana 60 High Clearance Steering Arms. I wanted them to be strong, of
course, but also professionally machined. You see, I can flame cut some from
a piece of 1" mild steel myself - but this time, I knew eventually they
would have to stand up to full hydraulic steering - so I needed something a
little better than I could turn out.
It didn't take me long to find them.
At a unique and highly specialized shop, right here in Canada (for once!). Over
The Top (OTT) Industries are a small, highly specialized shop in Vancouver,
BC that, as their web site proclaims, specialize in "steering and gearing".
I talked to Ben Olsen at OTT - what
an enormously nice guy to talk to. He has to be the nicest, most pleasant, most
well-spoken guy I've ever talked to at a 4x4 shop. Great - that's nice...so
you can take him to tea with the Queen....but are his steering arms any good???
Read on....
Part
1 - The Why? |
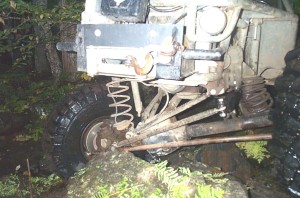 |
From way back, when
I first got the Wolf, I have enjoyed driving it by brail! |
|
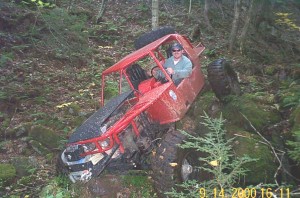 |
And you can see here, a year
later, I've learned nothing, still gleefully smashing the steering into
rocks, grinning like an idiot :-) |
|
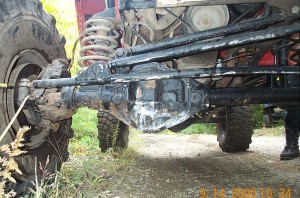 |
So the steering invariably ends
up looking like this after a weekend... |
|
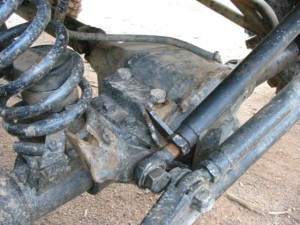 |
...or worse...like this. Tie
rod bent back so far that drag link/tie rod bracket contacted track bar
bracket and ripped it off. |
|
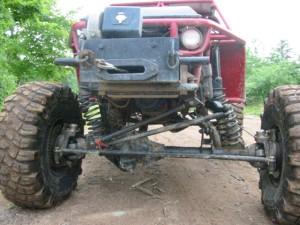 |
Leaving me with virtually no
steering, and an axle all over the place. |
|
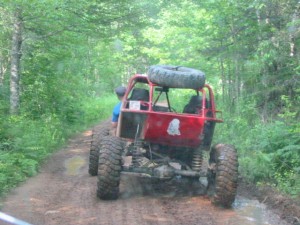 |
Which was a little more challenging
than I'd really like to limp back to the trailer. Without the track bar,
turning the steering wheel just shoved the body off the axle, side to
side.
Sometimes it was all the way
left... |
|
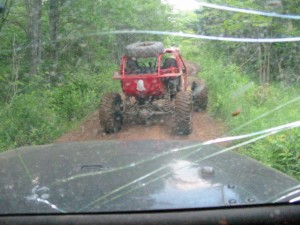 |
...sometimes it was all
the way right!
Something HAD to be done -
this was starting to be uncool! |
Part
2 - The Arms
So I did some surfing, did some reading,
did some calling around, and ended up talking to Ben Olson at OTT Industries
in Vancouver, BC, Canada.
The Dana 60 High Clearance Steering
Arms OTT produce stand alone at the top of the pile in my opinion, and that's
why I decided to order them.
What makes them the best choice -
that's what I'll explain in this section |
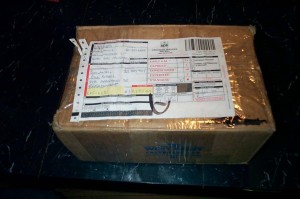 |
First off, Ben
was super to talk to on the phone. We discussed various technical factors
relating to my arms - from wheel backspace concerns to choice of steering
components (rod end / Heim joint or tapered tie rod end).
After I explained exactly what
I wanted and how I planned to run it, the boys at OTT got to work, and
a few days later the package arrived at my doorstop on the other side
of the country. I knew there were goodies inside, because it weighed a
TON, even though it was not very big. |
|
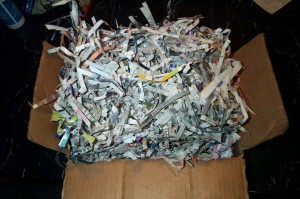 |
So I greedily ripped it open,
and found, much to my chagrin, that OTT had shipped me an extremely heavy
rat's nest!
Just kidding - the arms were
well packaged inside and protected by a bunch of shredded paper. |
|
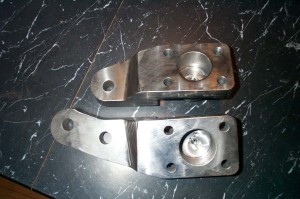 |
Aah - there're the little beauties
now! |
Features of the OTT arms include:
- CNC milled out of a single steel
billet, no welded parts
- Integrated kingpin bushing cap
with grease fitting
- Angle-compensated for steering
axis inclination - allowing maximum possible steering linkage travel
- Precision machined to use stock
Dana knuckle studs and mounting nuts (no long studs and/or bolts required)
- assuring the tightest possible fit, the only way to develop the required
strength for steering from the top of the knuckles.
- Tapered for your choice of 1
ton TRE, high angle drag link ends or straight drilled for rod ends / heim
joints
- Designed to fit virtually any
tire and rim combo possible including stock Hummer rims, large tires and rims
with custom offsets or backspacing.
The following pics illustrate the
arms and their features: |
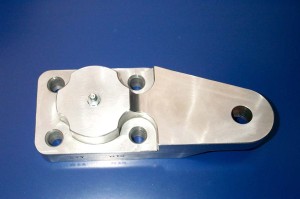 |
They're CNC machined
from a single piece of mild carbon steel on an OKK Vertical Machining
Center. Ben, the crafty bugger, wouldn't give up the exact SAE or ASTM
spec of the steel - no matter how I weaseled or how many angles I tried.
Can't say I blame him - a man's gotta have some trade secrets.
He did give up that it was in the 60-70 000 psi tensile strength range.
This is the driver's side arm.
Despite the 1 piece design, there is ample room to get a socket on each
of the mounting nuts, due to the machined reliefs. |
|
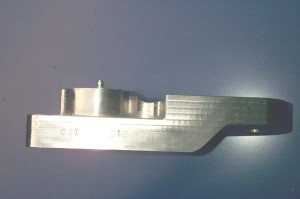
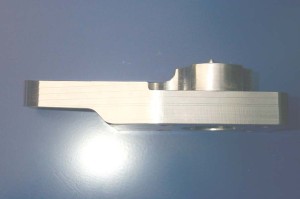
|
These 2 pics are side views
of the driver's side arm, and clearly show the integrated kingpin cap. I
personally really enjoy this feature. Anything that means less parts to
fool with, and more 1 piece simple, brute-strength is good with me! |
|
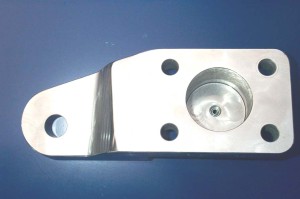 |
Underside shot of the driver's
side arm. You can see that I chose to have the steering linkage holes
in my arms machined for a straight 3/4" SAE bolt, as that is what
I use in my current steering linkage, and I plan to do so with my new
(eventual) hydraulic system also.
The arms can be machined to
accept standard automotive tie rod ends also if you prefer. |
|
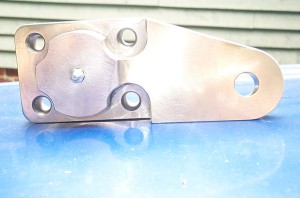 |
Another "plane" view
of the driver's side arm. The tie rod linkage mounting hole is approximately
5.25" from the centre of the kingpin. |
|
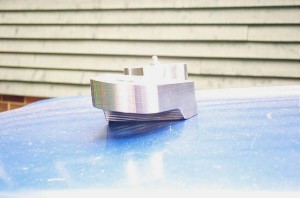
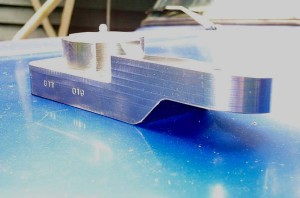
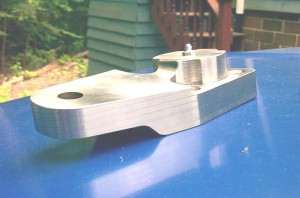
|
These pics show the real
beauty of the OTT arms. They are cleverly designed and machined so that
they compensate for the Dana 60 kingpin inclination (camber) and present
a horizontal mounting plane for the steering linkage ends. This means
that, whether you use TRE's or Heim joints, at static rest with the OTT
arms your steering linkage ends have a flat, horizontal mounting surface,
so that none of their precious misalignment angle is eaten up by the stock
Dana 60 kingpin inclination. That in turn translates into the maximum
possible linkage misalignment during axle articulation, and therefore
the greatest possible wheel travel unencumbered by steering linkage binding.
The clever design also incorporates
a slight rise in the steering arm over the plane of the top of the knuckle,
to accommodate leaf springs in the spring-over-axle configuration, while
still retaining use of stock length mounting studs (for VERY good reasons,
explained later), AND providing the proper mounting depth for those using
tapered stud tie rod ends.
All this, at the same time
as angling in sufficiently to accommodate even 44" tires on stock
hummer rims without interference!!
In other words.....TRICK AS
HELL !! |
|
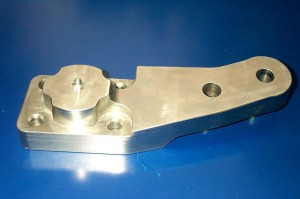 |
This is the passenger's side
arm, machined to accept the tie rod and drag link. |
|
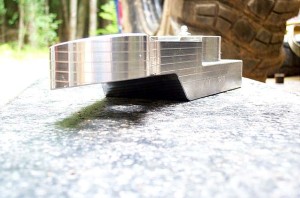
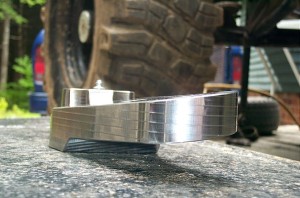
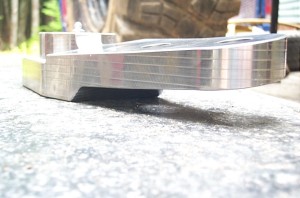
|
The passenger's side arm of
course has all the same features as the driver's side arm, as described
above. |
|
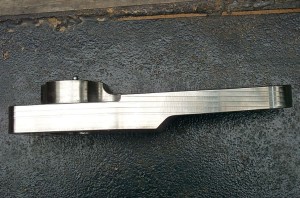 |
Right side view of
the passenger's side arm. |
|
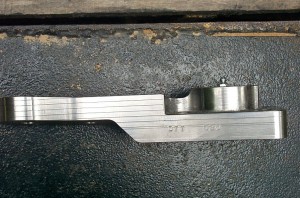 |
Left side view of
the passenger's side arm. |
|
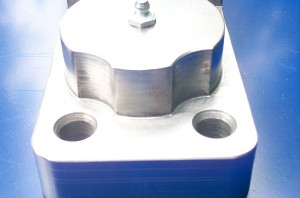 |
Close-up showing the 60°
taper seat for the tapered nuts that secure the arm to the studs installed
in the steering knuckle. |
|
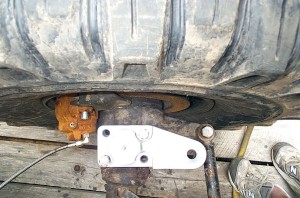 |
Test fit installation of driver's
side arm shows how tie rod hole is slightly aft and inside of stock location. |
|
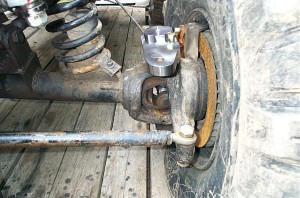 |
This accommodates virtually any size tire combined with any size rim with
any backspacing. This pic shows a 325/85/R16 Michelin XML Military Radial
(approx 38x14.50) mounted on a 16" x 9.5" steel rim with 4.5"
backspace. The OTT arms have been used with stock Hummer rims running 42x15.00
TSLs. |
|
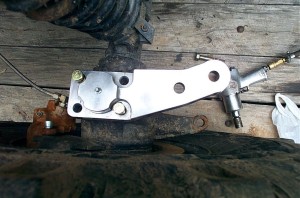 |
Test
fit of the passenger side arm. |
|
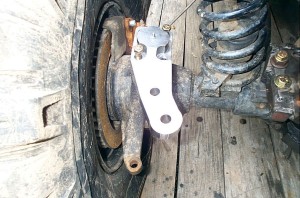 |
The front hole is the drag link hole. |
|
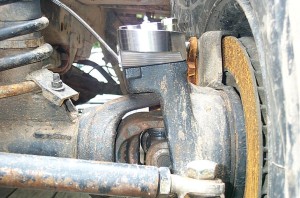 |
Test shot illustrating how the angle of the OTT arms cancel out the stock Dana 60 kingpin
inclination to provide a level mounting plane for your steering linkage
ends. |
|
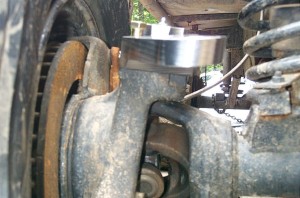 |
Test shot illustrating how the angle of the OTT arms cancel out the stock Dana 60 kingpin
inclination to provide a level mounting plane for your steering linkage
ends. |
Part
3 - Installation and Testing
Before I detail the installation,
I should mention my one "beef' with the OTT arms. My beef is this: there
are absolutely no instructions of any kind included. I know, you're thinking:
"big deal, they're just bolt-on steering arms". And for those of you
smarter than a box of hammers, that may well be true. But I have a gift - if
there's any possible way to screw something up - I WILL find it. And sure enough,
there were several "gotchas" I fell into during my installation.
In retrospect, I don't believe any
of the issues that I stumbled onto are issues with the product - but merely
screw ups that all could have easily been avoided with an instruction sheet.
Whether they are product issues, my unbelievable ineptitude that could only
happen to me and are therefore of no concern, or just things that you're glad
I messed up and warned you about - you will have to decide for yourself! |
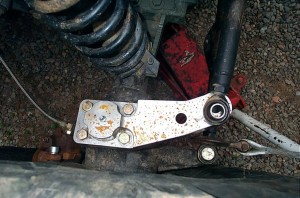 |
The first "gotcha"
greeted me the morning after I initially installed the arms. I had to
order the required GM mounting studs, as my local dealer had none in stock.
As I waited for the studs to come in so I could properly mount the arms
as they were intended, I installed the arms as kingpin caps only, using
regular SAE Grade 8 1/2-20NF bolts. I did this mostly so I could play
around with measuring / test fitting steering linkages, but also secretly
'coz I knew one of my wheeling buddies was coming over and I really wanted
to show them off :-) From this I learned 2 important things.
First, the arms, despite their
beautiful, shiny, machined appearance out of the box are shipped raw,
untreated steel. That means, if they sit outside, and it rains, like of
course it did for me, they will begin to surface rust immediately! Doh! |
|
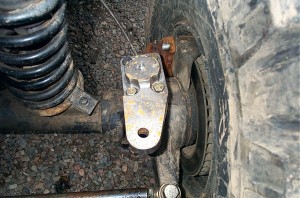 |
The second is: DO NOT use regular
bolts or use an impact wrench to install the arms - even temporarily.
The steel from which they are machined is actually fairly soft - and using
a regular hex head bolt where a stud and tapered nut are specified, ESPECIALLY
if you tighten said improper bolts with an impact wrench (even just to
initial tightness and not final torque) you WILL gall the arms, and chew
up the steel around the tapered seats. Doh!
The solution to the second
"gotcha" is easy - use the correct hardware for installation
(just like the guy who made the arms told you to, silly) and do not use
an impact gun. I simply dressed the area around the holes lightly with
a fine file and I was ok. |
|
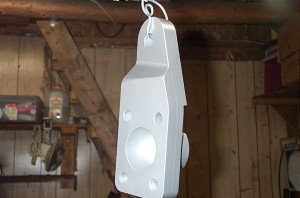 |
The solution to the first
part is easy too. Paint, powder coat or otherwise treat the arms before
installation. No big deal, just wish I had known. I simply removed the
light surface rust with steel wool (where do steel sheep come from - I've
never seen one?) and then painted them with some Bowman Industries industrial
anti-rust coating (I think that's paint to you and me). I used "Detroit
Diesel Silver" |
|
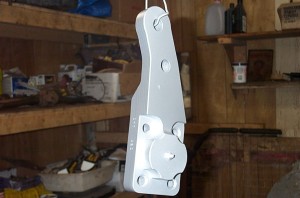 |
Me being the Mr Bean of the
workshop, this, of course, uncovered another "gotcha". The mounting
holes for the four 1/2" knuckle studs are very precisely machined
for an exact fit. This is an EXCELLENT thing, that I'll get into more
in a moment. However, it does mean that if you slap on 3 or 4 coats of
spray paint without covering the holes, you will gum up the holes and
screw up the exact tolerances, which of course you will only realize later
when you are trying to install them. So, when you paint, mask the four
1/2" mounting holes. And here I thought I was being clever by masking
the tip of the grease fitting with a dab of grease! |
Alright - I've made several
references to mounting style / hardware, and it's importance, so let's
get into it.
First, let me convince you
of why this is such an important consideration.
To begin with, this is one
of, if not THE, most important bolted joint assembly on you rig. Why?
Two reasons, really. One, because obviously the entire steering system,
and therefore your control over the rig depends entirely on this joint.
If it fails, you're in the ditch....or worse, for sure.
Two, because it sees comparatively
large loads for the size and number of fasteners involved. The size and
number of fasteners is limited by design factors of the knuckle (i.e.
there isn't room for more or bigger fasteners), and that is why use of
proper fasteners (made from proper strength and hardened materials), proper
torque spec, and the 60° tapered seat are absolutely critical - just
the way GM engineered it in the first place. Believe me - if they could
have gotten away with simpler holes (non-tapered) and bolts instead of
studs (less parts, easier to install) with the factory parts, they would
have. There's a good reason GM elected to spend the money to engineer
and assemble the way they did, (and why we should retain that design)and
I'll attempt to explain those reasons.
The first thing we need to
do is to understand just how a bolted joint works. This is a huge topic
itself that, according to legendary mechanic "Smokey" Yunick;
"To thoroughly understand it all would require at least 4 specific
engineering degrees and 20 years of hands on experience in each".
Rather than delve too deeply at this point, let's just state some of the
basics. If you want more information, a good place to start is the basic
tutorial from Bolt
Science. For our purposes we must understand that:
- Technically speaking, SAE
(i.e. automotive) fasteners (bolts or studs, and nuts) in a bolted joint
are not designed to carry a shear load. They are designed to clamp the
2 parts together, so that the friction between them carries the load
- or at least the majority of it. In reality - SAE fasteners do do this
but also usually carry some load in shear.
- That in order to carry out
their duty as "clamps", they must deform (stretch) a fairly
precise amount upon installation / tightening so that the resulting
force that tries to return the fastener to its original length achieves
the clamping force. The most common and easiest way of approximately
measuring this stretch (and thereby being assured that the proper clamping
force is achieved) is by measuring the torque with which the fastener
is tightened in the assembly, as this has a direct, mathematical relationship
to the amount of stretch.
- Fasteners of differing "grades",
materials, and construction methods (hardening, tempering etc.) have
vastly different strengths, ranging from SA grade 1 bolts with a yield
strength of 36,000 psi to SAE grade 8 bolts with a yield strength of
130,000 psi. This directly affects the maximum stretch that they can
endure without permanently deforming, and therefore the amount of clamping
force they can develop. We see this as different maximum torque values
for different bolts. Hopefully , we now see this as not just "how
tight do I have to do it up", but rather, "when I tighten
this fastener, how much clamping force can I develop"
- And finally, because of
fastener preload (explained well in the Bolt Science tutorial) a properly
tightened fastener is vastly stronger than a loose sloppy one.
OK, so how big a load are we
talking about then. Let's do some rough, back-of-paper-napkin calculations
to get an idea - if only to get a rough order of magnitude and to convince
ourselves that, yes, we better be pretty darn particular about how we
assemble these joints (that is, with how we bolt the high clearance steering
arms to the top of the knuckles). |
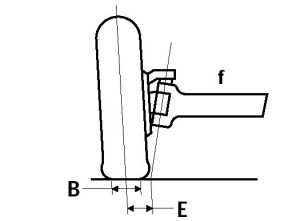 |
Using these diagrams as a
rough guide, we can approximate kingpin torque (KT) by the following equation
:
KT = (W*(mu)*(B^2/8)+E^2)/12
[Note: Some sources state that one should double the result if the steered
axle is driven.]
where:
- KT = kingpin torque in
foot pounds
- W = weight on steered axle
in pounds
- mu = coefficient of friction,
from diagram below, given E/B
- B = nominal tire width in
inches, as per diagram at left
- E = Kingpin offset in inches
at intersection with ground, as per diagram at left.
|
|
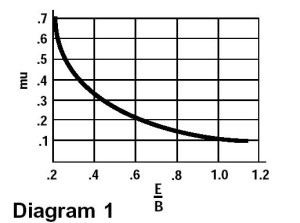 |
Chart for calculating coefficient
of friction between rubber tires and dry concrete given the dimension
( E/B) or kingpin offset / nominal tire width. |
So, if we plug
in the following numbers, using my Wolf as an example:
W=2400 lbs, mu=0.35, B=14",
E=6", we come up with a result on the order of 3500 ft lbs!!
Right - so you can't take that
calculation to the bank, you can't design anything based on it, but hopefully
it convinces you not to do a hack job and just bolt the steering arms
on with any old half-inch fine thread bolts you have lying around.
Which brings me to my final
point about using the proper hardware, specifically the GM studs and nuts.
What is the difference between
a stud and a bolt? In the grossest of terms, the answer is nothing, both
are merely clamping devices, as we have discussed.
However, there are some important
differences, which are often critical in highly stressed parts such as
this. They are:
A stud is frequently specified
when one of the clamped-together members is an expensive cast or machined
piece with internal threads - as is the case with the Dana 60 steering
knuckles, especially if the assembly ever requires disassembly for inspection
or maintenance, as is also the case with Dana 60 steering knuckles. This
is because one wishes to avoid stripping the internal threads of the cast
or machined piece at all costs - since repair may prove impossible or
extremely costly. Each time an assembly is disassembled and assembled,
one risks stripping or damaging the internal threads in the cast piece
if a bolt is used. With a stud, one can tighten the stud in place in the
cast piece, then need only remove the nut from the stud in order to dissassemble
the assembly, rather than having to remove the bolt from the cast piece's
internal threads; minimizing the chance of damaging the internal threads
in the cast piece.
Also, in an assembly highly
loaded in shear, as is the case with the steering arm to knuckle joint,
the stud offers us an advantage as it will be full diameter (i.e. non-threaded),
right at the joint interface, where the most stress occurs, giving us
maximum possible strength in the fastener, and more importantly, the tightest
possible precision fit between stud and hole. We desire a tight, precision
fit in order to eliminate slop and play that would contribute to a weak
joint. The OTT arms are a very tight fit on the non-threaded portion of
the studs for this reason. A bolt does not offer us the same advantages,
because either
- a) When tightened to spec
either all, or a portion of, the shank that fills the hole in the steering
arm will be threaded, and therefore a loose fit and weaker; or
- b) If we engineer the length
of the bolt precisely so that the threads end just before the joint
plane, as with a stud, then because the head of the bolt that we tighten
is not free to rotate on the shank of the bolt, when we tighten the
bolt to final torque we can not be sure whether the torque is rising
due to the desired stretch being achieved, or simply because the threads
have ended and the unthreaded shank of the bolt is bottoming against
the internal threads.
Finally, studs can aid us in
the assembly of tight tolerance parts in a way that bolts cannot, allowing
us to set the part on the studs, and then sequentially toghten down the
nuts, clampnig the parts together. Using a bolt in this manned can more
easily lead to cross-threading the bolt in the hole. |
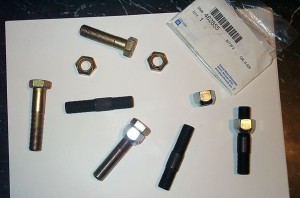 |
Even though I know all that,
the fact that the proper studs (GM part number 462855) are about $14 Canadian
EACH and are ONLY available from GM (since they are the only studs in
existence that I know of that have fine thread on either end), caused
me to try and dream up all manner of crazy home-brew ways to bolt on my
steering arms, some of which you can see pictured at left, along with
the correct GM studs. |
It was a giant stroke of luck
that at the time of this installation, my father, the genius mechanical
engineer, happened to be visiting, so that I could explain each of my
half-baked ideas for him to shoot down, before I had to knuckle under
and go and buy the proper parts. You know that if he hadn't been, I'd
have screwed up again, and a bit further down the page you'd be looking
at my pics of a sheared off steering arm and three broken home-made studs
and a grade 2 bolt with a lug nut welded on! Anyway, the results of our
teamwork are (just in case you're tempted):
- You can't use regular grade
8 bolts - they will not seat properly on the tapered mounting holes,
they have no provision for a tapered interface, and the threads in the
steering arm hole are too loose a fit.
- You can't source a stud
from somewhere else, you won't find one with 1/2-20NF threads both ends.
All the 1/2" studs I found (such as Chevy big block manifold studs)
were coarse thread one end. This will not do, since you can neither
re-cut the internal threads in the steering knuckle to coarse thread,
nor find a 60° taper nut (required to mate to the top of the arm)
in coarse thread - they are all fine thread.
- You can't take a 1/2-20NF
bolt, run a die right down to the head, and then thread it into the
back of a tapered lug nut and think you have cleverly made a "lug
bolt" (embarrassing picture of just such an aberration at left
- bottom middle). When you went to tighten this into the knuckle, the
nut that will rotate on the shank, combined with the head that will
not will conspire to prevent you from achieving proper fastener stretch
and therefore clamping force.
- You can't cut your own 1/2-20NF-threaded-each-end
studs at home using a vice and parts store die set. The tolerances would
never be right, you'd probably end up with threads inside the steering
arm hole, and it would just be a flaky way to assemble the most critical
joint in your rig. You could probably machine your own with the right
tooling, training, and setup time, but by then you're saving nothing.
In other words - you simply
have to use the GM studs and tapered nuts to do the job right.
Why the taper? Well, remember
what I said about wanting to avoid any slop, looseness, or misalignment
in the parts, as this would eventually lead to loosening and failure of
the joint, both through loss of clamping force and subsequent loss of
friction, and also component fretting and eventual failure?
No matter how well machined
the parts are, if they are to be assembled and disassembled, there obviously
has to be SOME clearance, otherwise you'd never get the parts together
or apart again. The 60° taper seat in both the factory GM and the
OTT steering arms, along with the tapered nuts, are the clever way of
"removing" that clearance, as much as possible. As you tighten
down the nut on the stud, over the steering arm, the tapered seats come
together to achieve the tightest possible union that can still be disassembled
easily. This is the same reason your wheels and lug nuts also use a 60°
taper. |
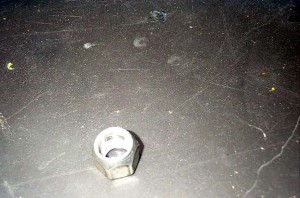 |
Speaking of lug nuts. One
more "gotcha" I wish I had know about in advance. DO NOT use
cheap parts-store 1/2"-20 lug nuts. yes they will have the correct
taper (maybe - depending on quality control I guess), BUT they will NOT
be hard or strong enough. When you attempt to tighten them down on the
very hard GM studs, you will quickly and easily strip the soft, crappy
threads out of them. Ask me how I know, the pic to the left should be
a giant hint! (sorry for the lousy quality). You should use the GM nuts,
or if you must, a hard, high quality nut made in the US/CAN/UK/AUS by
a reputable manufacturer. |
OK, allow me to summarize,
and proceed with the actual installation.
***Use only the specified factory
GM studs and tapered nuts for installation of these steering arms***
Phew - let's get on with it
then! |
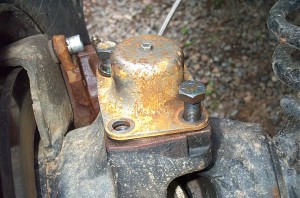 |
Step one, remove existing
kingpin cap (or stock steering arm) bolts / studs. If they've been there
for a while, significant force / heat may be required. See my kingpin
rebuild article for more.
Loosen each one a little at
a time, as the spring tension beneath the cap can be quite high and pop
the cap off with some force.Remove
the cap, spring, spring retainer, and gasket, and clean the mating surface
at the top of the knuckle. Also clean out the threaded holes in the knuckle.
I had recently run a tap through mine during a kingpin rebuild, so merely
blew them clean with compressed air. You may want to run a tap down. |
|
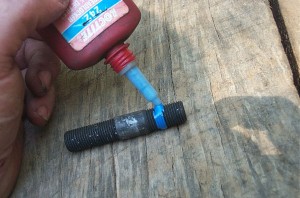 |
Apply thread locking compound
to the SHORT end of the studs. I chose medium strength Loctite Blue (242). |
|
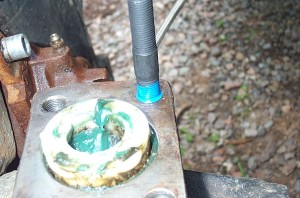 |
Install the studs in the knuckle, preferably torqued to 80 ft .lbs. This may be hard to measure if you don't have a fancy stud-installing tool. |
|
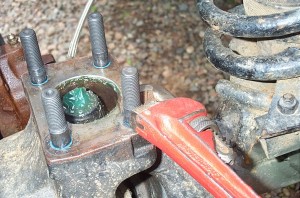 |
I snugged them down tight with a pipe wrench. |
|
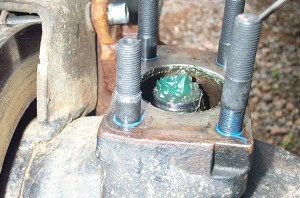 |
Initially, I had tried running
a nut on the stud till it bottomed against the unthreaded shank, but all
that did when I came to tighten the studs into the knuckle was strip the
threads out of the nut. I don't know what the GM studs are made of, but
it is pretty damn hard and tough. This can be seen in the front left stud
in this pic, where you can see the debris of the destroyed nut around the
threads just above the unthreaded shank. The stud itself remained untouched. |
|
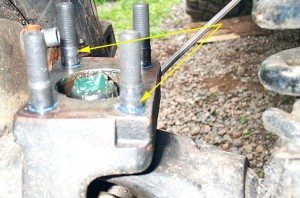 |
You do, however, have to be
careful with using a pipe wrench or similar tool when installing studs,
as the serrated jaws of the tool can mar the stud. I suffered this slightly
in 2 out of the 8 studs I installed, but it was very minor. |
|
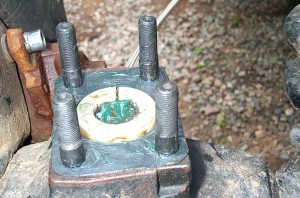 |
When all the studs are installed,
wipe away excess thread locking compound from the knuckle face, grease both
sides of a new gasket, and install the gasket over the studs. |
|
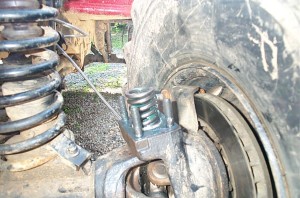 |
Place the spring retainer and
spring back in place on top of the kingpin bushing. |
|
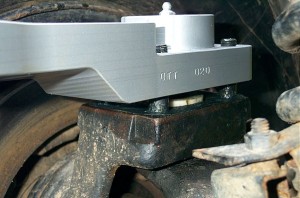 |
Then place the OTT steering
arm over the studs. It will not drop all the way on, one because of the
kingpin spring, but also because of the tight tolerances between stud and
holes. This is where I first learned of my SNAFU of painting the inside
of the mounting holes. It was so tight, I removed the spring, and still
I couldn't really get it on - the clearances are just that tight. This is,
of course, a very good thing when it comes to the ultimate strength of the
assembly. I removed the arm and carefully removed the paint from inside
the holes, then re-installed it. |
|
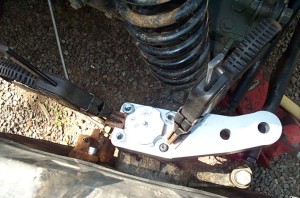 |
The arm only just fits over
the studs, and with the spring, there is almost no room to even start the
nuts, so I used a couple of clamps to cinch it down a bit so that I could
start the nuts on the studs. |
|
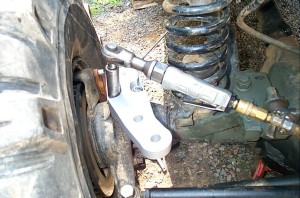 |
Once the nuts are started, I
used an air ratchet (do not use an impact tool - the hammering action is
not good at this point) to sequentially tighten down the nuts, which will
eventually clamp the steering arm down over the studs and in place on the
knuckle. Factory final torque spec is 80 ft/lbs. |
|
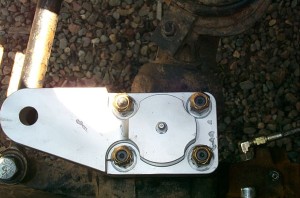 |
Knowing that I darn well did
not want them to loosen, I had what I thought was a bright idea after I
had tightened down the tapered nuts. I thought I would install Bowman grade
8 locking nuts (deformed thread style, often called a "stover"
nut) on top of the tapered nuts. The only thing was, I believe there turned
out to be insufficient threads of the stud exposed to fully engage the ovalated
threads at the top of the locking nut that actually provide the locking
action. There are therefore dubious anti-loosening properties added by doing
what I did. I left them in place however, and consoled myself with the fact
that they at least protect the exposed threads. |
I
fully expect they will loosen and fall off! And with me being Mr Bean
of the workshop - at least one will probably get sucked into the carburetor!
Note the marked up paint from
the clamp used during installation. A by-product of not painting them
early enough so that the paint could harden before I had to install them
the day before a giant annual 3 day wheelin fest!
I expect you are beginning
to see why I remarked earlier that I really would have appreciated some
sort of instruction sheet - even for what appear to be "bolt on"
parts. At least one should be included if these things are going to be
sold to bumbling dim-witted three-thumbed garage monkeys like me!
Of course, being a military
man - I have been rigorously indoctrinated with the mantra "Don't
bring me problems, bring me solutions". So, with that in mind, I
have created an instruction sheet for the OTT High Clearance Steering
Arms, (it's really just a simplified version of this article) that may
be viewed or printed from right here by current or prospective OTT customers.
You guys at OTT: Ben, Rick,
Chris - feel free to save and print these and then include them in the
box when you sell 'em - anything to help out my fellow Canucks! It is
available in PDF
The following pics show the
"final" installation in the Wolf, at least the first iteration.
I was unable to move the tie rod up to the arms, as it would have then
passed directly through where my track bar currently is. As I had hastily
decided to install them the day before a major 3 day event, I simply didn't
have time for the required re-design to make everything work perfectly.
However, I was able to separate the tie rod and drag link, so at least
I can bend the tie rod and just flip it around. Also, the drag link is
raised way up so there is no longer any interference between it and the
track bar bracket, so I am no longer at risk of tearing the track bar
off again.
|
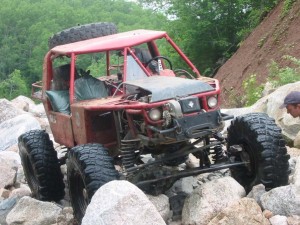 |
I flogged the whole rig hard
for 3 days at our annual Rockathon event, including the new steering arms.
This picture clearly illustrates how much better protected everything
will be when I get the whole steering linkage moved up to the OTT arms.
As it turns out, my steering
box finally blew its guts out on the third day - something I had been
expecting / fearing for quite some time. This has moved up my plan for
full hydraulic steering, so I shall probably next update this article
when I get that all rigged up, so you can see how the OTT arms work with
full hydro.
At the end of the season I
shall also remove the arms and check the roundness of the mounting holes,
and report the results here; as this will tell us a lot about the long
term durability of the arms. |
Conclusion
After the ups and downs of my installation,
and the 3 days of testing, I'm still extremely pleased with my OTT High Clearance
Steering arms, and don't believe you can buy a better steering arm for the Dana
60. |
|
|