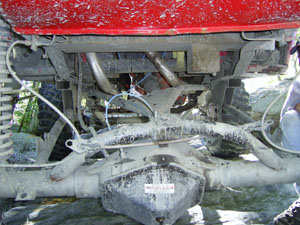 |
Rear suspension FUBAR! |
|
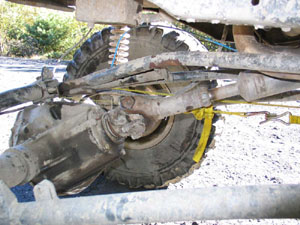 |
Not good! |
Temporarily unseating the bead ,
“burping” some air out, is also a frequent annoyance. In wet and
muddy conditions it allows water and crud into the tires and emptying 100 lbs
of stinky swamp-water from your rims after a day of wheeling is no fun.
The solution is to use a beadlock
wheel – a wheel specifically designed to clamp down on the tire’s
bead, physically retaining it in place. There are a variety of different methods
of accomplishing this bead-locking action, and dozens of different beadlock
wheels available on the market. Most, however, have one thing in common –
they only lock the outer bead of the tire to the wheel.
Why double beadlocks?
Granted, when you loose a bead it
is most often the outer bead that blows. But inner beads can and do blow as
well – I’ve blown plenty myself and even blown both at once. Not
only that, but re-seating an inner bead in the field is more of a PITA than
an outer bead, often requiring removal of the wheel.
Trying to re-seat a rear inner bead
with your rig nose-high on a steep, rocky climb, a 60” HI-lift jack max'ed
out on an angle, balancing on a rock, is not only a pain but pretty damn dangerous
too. Take it from me! |
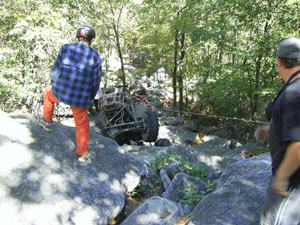 |
On the rope! |
|
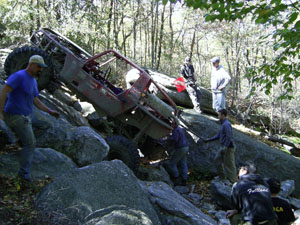 |
A great spot to wheel... |
|
 |
... but not such a great spot to be trying to re-seat a bead! |
That’s why I decided that if
I was going to invest in beadlock rims, I wanted them to lock both beads.
Why "Hummer Style"?
Because of the difficulties of fitting
a traditional bead-locking ring on the inside of a wheel while clearing brake
and steering components , a different approach is required for double beadlocks.
This is known as the “internal” beadlock or “Hummer style”
(named after the US Military AMG HMMWV or "Hummer" that popularized
the design). This approach is completely different from normal, external beadlocks
and works like this: |
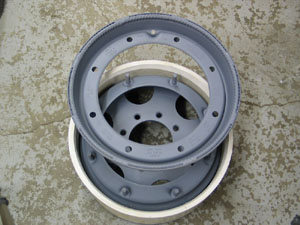 |
The rim itself
comes in 2 pieces - a larger inner-half and a smaller outer-half. The
two halves of the rim bolt together using studs and nuts - 8 or 12 depending
on the version. |
|
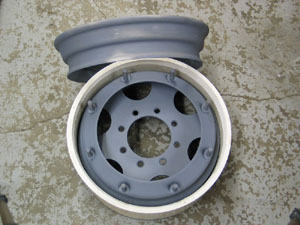 |
Each half of
the rim has a bead seat where the tire's bead seats. Here you can see
the outer-half standing up next to the inner-half. |
|
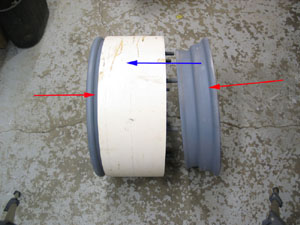 |
The bead locking
action comes from the use of a "beadlock insert". The original
Hummer rims used either rubber or magnesium inserts - Dean's version uses
a section of PVC pipe.
Regardless of the material
used, the method is the same. The beadlock insert is placed inside the
tire and then the tire-and-insert are slipped over the inner half of the
rim. The outer half of the rim is then bolted to the inner half. Each
of the tire's beads sits on a bead-seat on one of the halves (as indicated
by the red arrows). When the outer half is bolted onto the inner half
and tightened down, the two halves are drawn together (as indicated by
the blue arrow) sandwiching the rim halves, tire beads, and insert together
effectively pinching or trapping the tire's beads between rim and insert.
Don't worry if this isn't 100%
clear at this time - it will be by the end of the article. |
Any Reason Not to Use Hummer rims?
So we know the "Hummer" design is a clever and effective way to lock both beads. But are there any reasons we may not want to choose Hummer beadlocks? Well, there are three factors to consider before making a decision - they are:
- Rim width
- Rim diameter
- Backspacing
Rim Width
Original Hummer rims are only 8.25" wide bead-seat to bead-seat. That makes them on the narrow side for use with the largest of tires (original Hummer tires were only 36 x 12.50 (bias ply version) or 37 x 12.50 (radial version)). My particular tire of choice is a 42 x 15.00 Super Swamper TSL, which has a recommended rim mounting width of 9.75" - just a little more than the Hummer rim's 8.25 inches. However - many years of experience accumulated by many different folks running up to 44" tires on Hummer rims has proven that there are no disastrous consequences to using rims a little narrower than recommended (for off-road use only - never deviate from manufacturer's recommendations concerning on-road use). The only reported consequence of using a narrower than specified rim is that, at very low (single digit) pressures, the tire may tend to fold under itself more than it would on a wider rim. How much of an issue this is becomes a matter of personal opinion. Many report the result is really only that a large tire on a Hummer rim at 8 0r 9 psi flexes and conforms the way the same tire would at 3psi on a regular, wider rim. I shall be reporting my experience in future updates. Bottom line - this small drawback, for me, did not outweigh the many benefits of using Hummer rims.
Rim Diameter
Original, steel, double-beadlock Hummer rims come in only one diameter - 16.5" If you simply must use a tire with a different diameter they will not work for you. This was a complete non-issue for me as not only do my tires of choice come in 16.5" diameter - but 16.5" is still the rim diameter in which you can get the largest selection of large tires - particularly the Interco tires which I prefer.
Backspacing
Backspacing on original Hummer rims is a massive 7.0". Running them with this much backspacing will likely lead to problems with the rim clearing brakes and steering, the hubs sticking out and being vulnerable, and tires contacting body and suspension components. Not many folks can get away with using rims with 7.0" backspacing. However - there is a solution. Hummer rims can be re-centred with a wide range of backspacing. Problem solved.
Why Dean Reed?
So I knew I wanted internal, “Hummer”, double beadlocks – width and diameter weren't going to be a problem - though I would need someone to re-centre them to my specifications. However, stock Hummer rims, either military surplus or civilian “take-offs”, have some serious limitations. Not least of which are the limited availability of the beadlock inserts and the unreliable/unknown condition of used (especially military surplus) parts.
That narrowed my choices to manufactures of custom Hummer-style double beadlocks - of which there are perhaps three I'm familiar with. One of these, in my humble opinion, is flat out not worth doing business with at all. Another seems to have a better reputation but still appears to have issues with reliability, timeliness, customer satisfaction and I’m sad to say that my own dealings with this company left me with a distinct impression of unprofessional and unreliable.
That only made my decision that much easier – I chose Dean Reed of Performance Cryogenics for the following reasons:
- Quality: I had seen pictures of Dean's craftsmanship in the past, and was highly impressed by it. This guys KNOWS how to wield a welding torch and the results are truly impressive. He also uses the proper machine tools for the job – end mills, lathe, vertical mills and the like. If I wanted someone who used a grinder, a vice and big hammer I might as well do the job myself.
- Price: Dean’s prices are very reasonable – especially considering the quality of the product you’re receiving and the fact that you get any bolt pattern and backspacing you want and a wheel that locks both beads.
- Availability: Dean gave me a timeline and stuck to it. He went over my requirements with me, custom-made what I wanted fast, shipped it fast, and never had to offer an excuse or a story.
- Reputation/Integrity: Of course I did my research first – they don’t call me Billavista for nothing! Nowhere online could I find a dissatisfied customer. Quite the opposite. More importantly, when I spoke with Dean he was completely up-front about what he could and could not do, what my options were, and how long it would take. Extraordinarily, knowing I would be writing this article that would be read by tens of thousands people, he insisted that I understood that I wouldn’t be getting anything special – that I would be getting exactly what any other customer would – no special treatment. At the time he didn’t known that I always insist on this myself – but the fact that he insisted that I understood this – that’s integrity!
- Longevity in the business: Great ideas and innovative products come and go in this industry - and with them many small companies. I was impressed with Dean’s record and that fact that he was a pioneer in custom Hummer double beadlocks and that he’s been doing them for several years now.
OK - that was the thought process - let's see if what I thought turned out to be true.
Review |
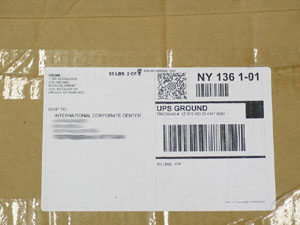 |
They shipped
via UPS ground.
Note the box weight - 55lbs
each. |
|
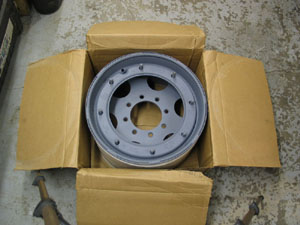 |
Inside the box. |
|
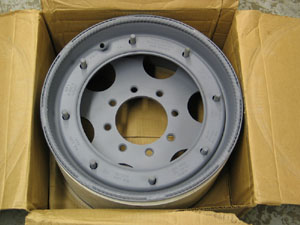 |
Close-up. |
|
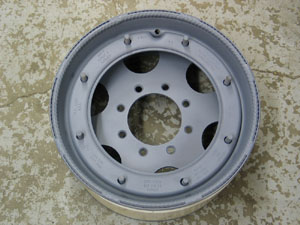 |
As an option
I had Dean add his "rebar rock ring". This modification helps
to stiffen the outer-most lip of the rim and protect it from rock rash.
Rock rings are also available in different cold-rolled steel designs. |
|
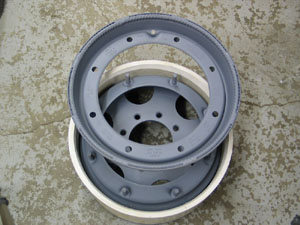 |
The rims come
completely re-furbished, very nicely welded, and primed ready for your
choice of paint.
The quality is evident right
away.
Look at the tolerances between
the re-bar ring and the rim. Go into your shop and try and bend a length
of rebar in a perfect circle like that and see if you don't agree with
what a craftsman Dean is. |
|
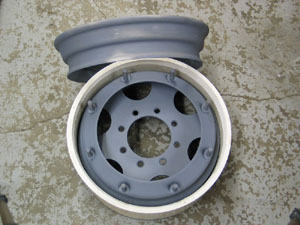 |
Here the outer-half
is removed from the inner-half, leaving the beadlock insert in place on
the inner-half.
All the hardware you receive
is brand new - including the studs that hold the rim halves together.
The studs are 1/2"-NF20
and are 2" long. |
|
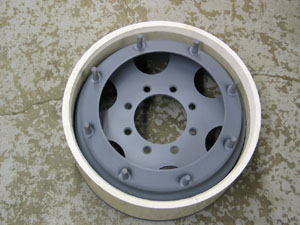 |
The beadlock
inserts are 16" ID, 11/16" thick and 6.75" wide.
OEM magnesium inserts are 7"
wide but were designed for use with tires having much thinner beads than
do the large offroad tires we use. Making the insert a little narrower
than stock allows the halves to be bolted together without the use of
longer studs. It also means the clamp nuts that hold the two rim-halves
together can be torqued to spec without crushing the tire's bead too much
or over-stressing the outer rim-half.
Note that the insert is chamfered
from 11/16" thick to about 1/2" at the edges to match the profile
of the OEM magnesium insert. This makes the process of getting it on and
off the inner half of the rim much easier. |
|
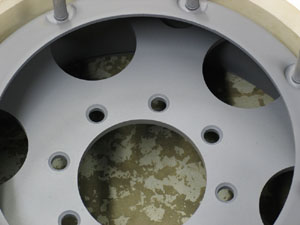 |
The custom centres
are a burly 3/8" thick cold-rolled carbon steel.
The rims come custom re-centred
at your choice of backspacing (up to a max of about 4.75") and any
bolt pattern you desire.
The bolt pattern is perfectly
accurate and all the lug-nut seats are correctly tapered. |
|
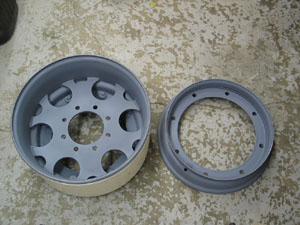 |
Back-side of
both rim halves.
Inner rim-half (left) clearly
showing the new custom centre. |
|
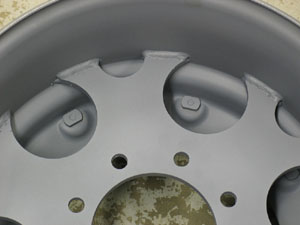 |
You can clearly
see the quality workmanship.
Superb welds, no splatter,
and great paint. |
|
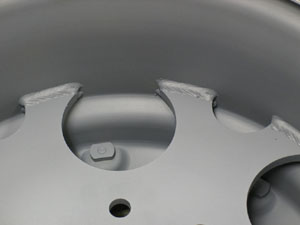 |
Close-up.
I was truly impressed. I expected
them to look like re-furbished military surplus rims.
They do not. They look and
feel like brand new custom rims.
I said in the intro - it's
so rare to get something that simply exceeds your expectations but these
rims did just that. |
|
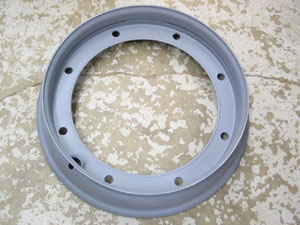 |
Close-up of the
back-side of the outer rim-half. |
|
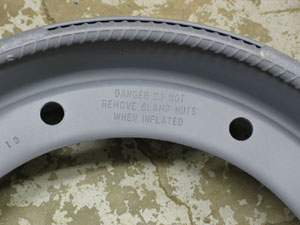 |
All the original
markings are in place.
You can enlarge the pics and
see them for yourself.
This one says: "DANGER
DO NOT REMOVE CLAMP NUTS WHEN INFLATED"
This is critical.
The "clamp nuts" are the nuts that hold the two halves of the
rim together. If you tried to remove them while the tire was holding pressure
the rim would come apart with explosive force.
The danger is real
- so much so that the military use safety cages to disassemble the rims
and many civilian dealerships use a special 5-sided "security nut"
that can't easily be undone without a special tool. |
|
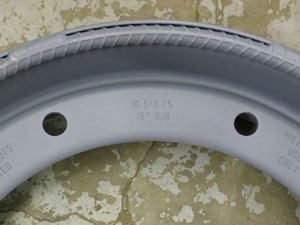 |
"16.5 X
8.25 15° RIM"
Referring to the diameter
and width of the rim, as well as the angle of the bead seats. |
|
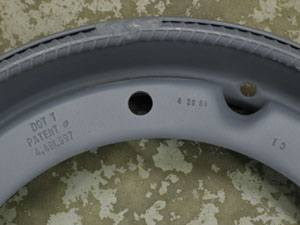 |
The much touted
DOT stamp and a patent number.
Does this mean the rims are
street legal?
I can't really answer that,
as the rims are also clearly stamped with... |
|
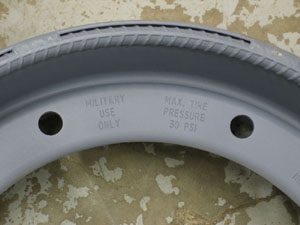 |
..."MILITARY
USE ONLY"
Which stamp trumps the other
will likely depend not only on your local laws but also on who is interpreting
them.
Note the: "MAX
TIRE PRESSURE 30 PSI" |
|
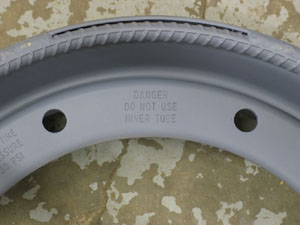 |
"DANGER
DO NOT USE INNER TUBE"
Again - note the quality of
the welds between the rock ring and the rim. |
|
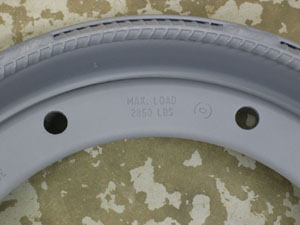 |
"MAX LOAD
2850 LBS"
That's per rim. Even my rock pig isn't that heavy! |
|
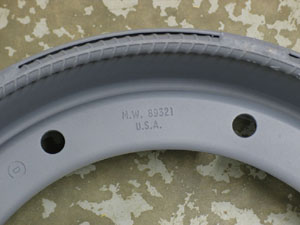 |
"M.W. 89321
U.S.A."
Obviously made in the USA.
No idea what the 'M.W. 89321'
is though. |
|
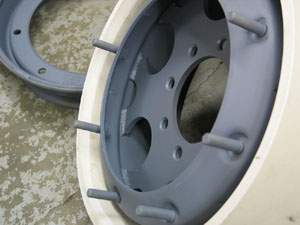 |
Here's a shot
of the inner rim-half showing why the maximum backspacing available with
the re-centre is 4.75".
Any more and there isn't room
to get a good quality weld on both sides of the centre section. |
|
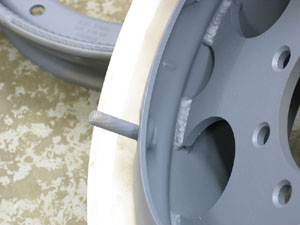 |
Close up of re-centring.
Very nice quality. |
|
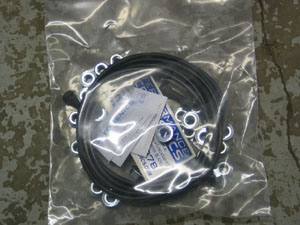 |
The rims ship
with a bag containing all the hardware you need. |
|
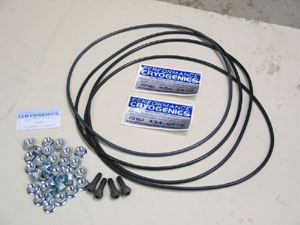 |
It includes four
O-rings (for sealing the two rim halves so they are air-tight); four short,
rubber valve stems; and 32 brand-new, self-locking, flanged clamp-nuts.
Plus a business card
and a couple of stickers for good measure.
The clamp nuts are
1/2"-NF20.
The O-rings are 14.5"
Buna-N (Nitrile) - British Standard part number 458N70 or AS568A "Dash
Number": -458. |
Complete specs are:
Material |
Recommended
Use |
Not
Recommended For |
Mechanical
Properties |
|
|
|
|
Buna-N
(Nitrile)
Standard: 70 Durometer Black
Temperature Range: -35ºF to 250ºF
Least Expensive / Readily Available |
Silicone
Greases / Oils
Water
Petroleum Oils / Fuels
Ethylene Glycol Fluids |
Keytones
(MEK)
Halogenated Hydrocarbons
Auto / Aircraft Brake Fluids
Strong Acids
Sunlight, Ozone, Weathering |
Good
Wear Resistance
Good Compression Set Resistance
Good Short-Term Resilience
Good Permeation Resistance |
|
|
|
|
|
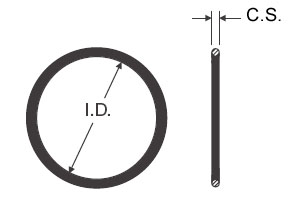 |
BS
Part Number |
AS568A-
Dash # |
Material |
Actual
I.D. (in.) |
Actual
Cross Section (in.) |
Actual
ID (mm) |
Actual
Cross Section (mm) |
Nominal
Reference
I.D. (in.) |
Nominal
Reference
C.S. (in.) |
Nominal
Reference
O.D. (in.) |
458N70 |
-458 |
Nitrile |
14.475
± .070 |
.275
± .006 |
367.67
± 1.78 |
6.99
± 0.15 |
14-1/2 |
1/4 |
15 |
|
The 8-stud bias-ply Hummer rim O-ring
can be purchased directly from Dean and should also be available from any good
O-ring supplier. For example, MCMaster-Carr sells them in a 2-pack, part number
9452K452. |
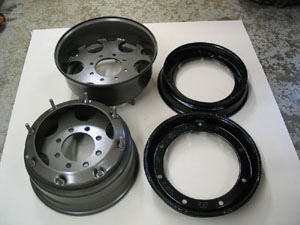 |
Before use, you
must paint the rims any colour, or combination, you desire.
I'd seen folks use a two-tone
approach before - to compliment the two-piece design of the rims - and
I liked the way it looked. |
|
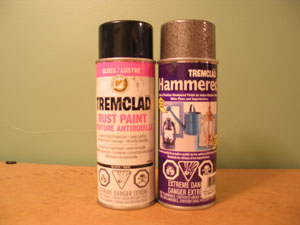 |
I chose "Tremclad"
brand rust paint in "Hammered Finish Charcoal Grey" for the inner
halves and good old "Gloss Black" for the outer halves. |
|
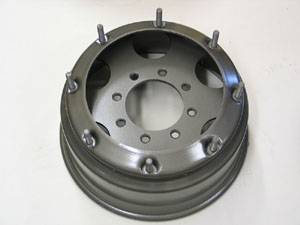 |
I think the "hammered
finish" charcoal grey came out really well - especially for a rattle-can
paint job! |
|
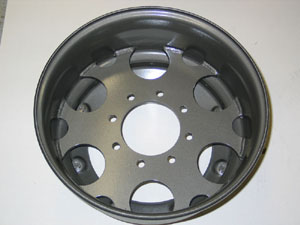 |
Back-side of
inner-half painted. |
|
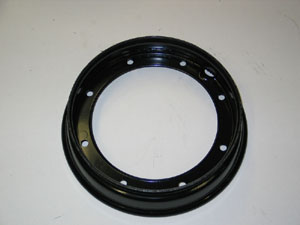 |
Back-side of
outer-half in gloss black. |
|
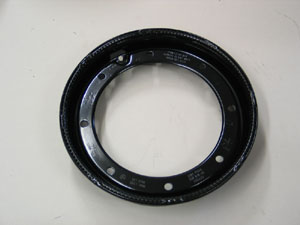 |
Front-side of
outer-half.
I did two coats of each. |
The combination looks really good
together.
Specs
and Dimensions |
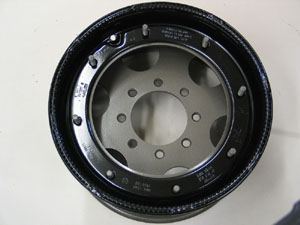 |
The specs on
the rims are:
- Diameter: 16.5"
- Width: 8.25"
- Origin: Military 8-stud
bias-ply HMMWV (Hummer) wheels
- Construction: two-piece,
carbon steel, with rebar rock-ring and custom 3/8" centre.
- Assembly Weight: 56lbs
- Wheel: 44 lbs
- Beadlock insert: 12
lbs
- Backspacing: Customers choice
0 - 4.75" or stock 7.0"
- Bolt Pattern: Customers
choice (shown is standard 1-ton 8x6.5")
- Beadlock insert: Custom
cut and chamfered PVC pipe.
|
Note: Dean also has these rims available
in the 12-stud (radial tire) Hummer rim version. According to Dean, the 12-stud
rims weigh 52 lbs with custom centre and re-bar rock ring, and are rated to
a maximum of 50 psi and 3850 lbs vice the 30 psi and 2850 lbs of the 8-stud
version. |
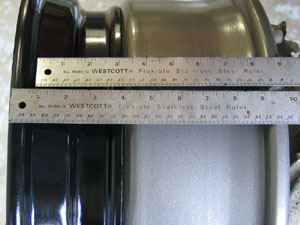 |
This pic clearly
shows the overall width and "standard rim width" of the Hummer
rims. Note that it is common practice to quote a rim's width as the dimension
from bead-seat to bead-seat - which is 8.25" as clearly indicated
by the top ruler.
You may occasionally see a
Hummer rim's width quoted as 9.75" as this is the total width from
edge to edge, as shown by the lower ruler. |
|
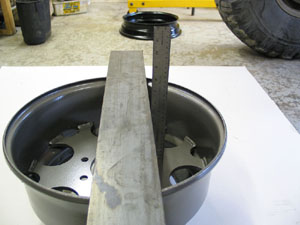 |
Back-spacing
is measured from the back side of the rim's mounting surface to the innermost
edge of the rim, as illustrated here. |
|
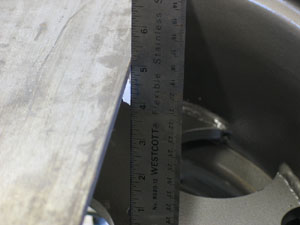 |
4.75"
backspacing. |
Fitment |
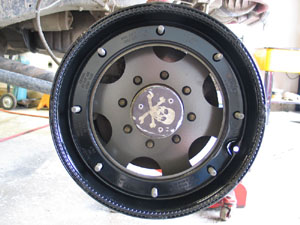 |
With the rim
loosely assembled and installed on the rig it is obvious Dean cut the
bolt pattern and centre-hole perfectly.
With heavy tires and wheels
it's a real advantage to have the hub to rim-centre clearance at close
tolerance as shown here. This helps tremendously in mounting the heavy
tire and rim combination, allowing you to heave the wheel into place on
the hub and then carefully rock it into place over the lugs. |
|
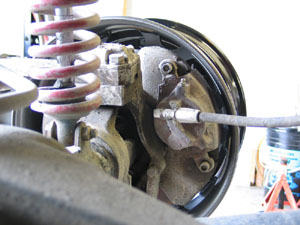 |
The 16.5"
rim diameter gives plenty of clearance for brakes.
This pic shows my Dana-60 front
axle with custom-modified 3/4 ton brakes. |
|
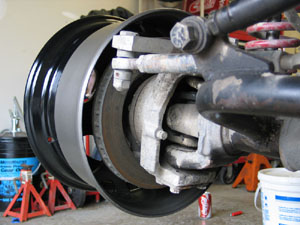 |
Steering arm
clearance is another consideration when deciding rim-width and backspacing
requirements.
In this pic it almost looks
as if steering-arm clearance might be an issue - until... |
|
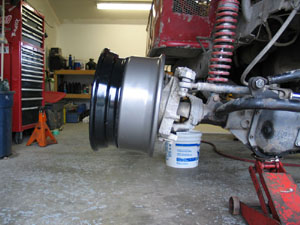 |
...we check the
front view and find that there is plenty of room because of the backspacing. |
|
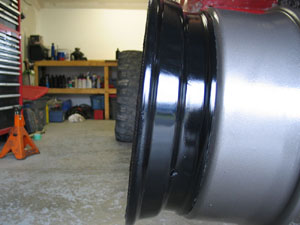 |
I carefully chose
the backspacing I wanted to give me as much clearance as possible between
the rim/tire and the vehicle, without leaving the hub unprotected.
4.75" turned out to be
perfect for me, as the hub stays tucked inside the rim. |
|
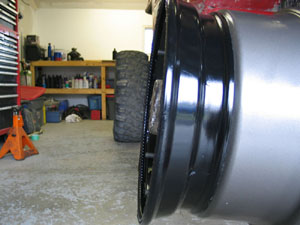 |
Here you can
clearly see the hub, nestled just inside the outer edge of the rock rings
- perfect! |
And just because I care... |
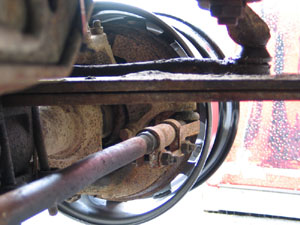 |
...I decide to
also test-fit the new rims on the Dana-60 front axle of my old Ford F-250
tow rig - a rig with stock steering and the notoriously large double-piston
front callipers. |
|
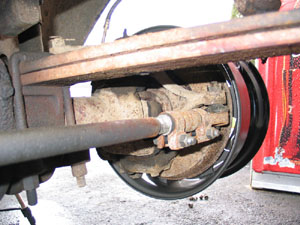 |
Inside
of driver's front - steering clears nicely. |
|
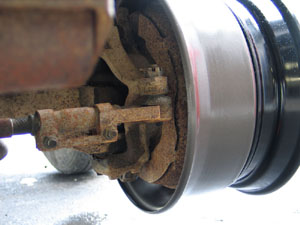 |
Driver's front. |
|
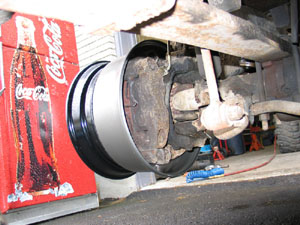 |
The huge disc-brake
callipers fit nicely inside the rim, even with 4.75" of backspacing. |
|
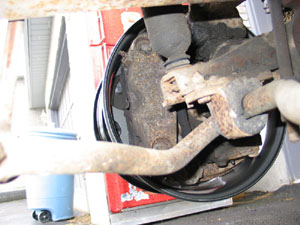 |
No worries at
all. |
Installation |
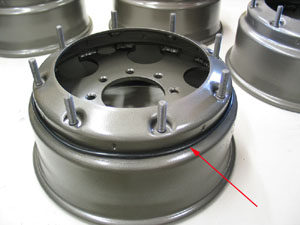 |
Once you have
your rims painted and dry you're ready to assemble them.
Step 1: Install
the O-rings on the inner-halves.
Generously lubricate the O-ring
with tire-soap or soapy-water. Install it on the first ledge of the rim
, one inch below the studs. Ensure it is uniformly positioned and not
twisted. The red arrow shows correct placement. |
|
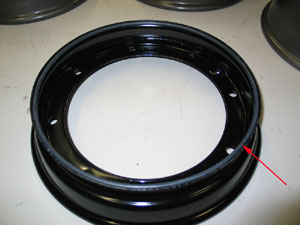 |
The following
two pictures illustrate the corresponding O-ring mating surface on the
outer-rim half. |
|
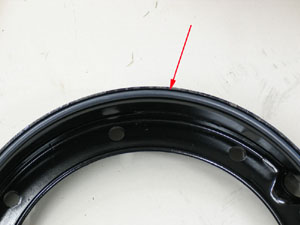 |
This is where
the O-ring will seat when the two rim-halves are bolted together. |
|
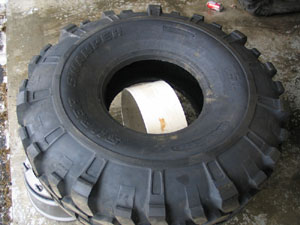 |
Step
2: Insert the beadlock-insert into the tire.
Dean supplies the
inserts as one-piece units. Getting them in the tire can be a bit of a
challenge. The best method is to set the insert on its edge, as shown,
and then place the tire over it. |
|
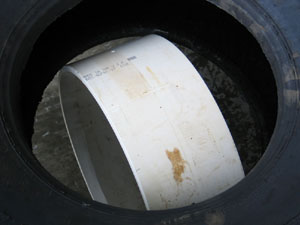 |
In this way the
contact between insert and tire is reduced to just four points and if
you bounce up and down on the tire you should be able to get the insert
to pop in. A buddy can be very helpful when doing this.
With a one-piece insert the
real challenge though is getting it out of the tire again. I've
heard of folks having to resort to strapping the tire to a tree and yanking
or winching the insert out! |
|
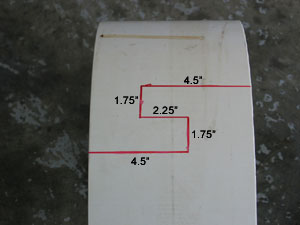 |
For this reason
I decided to convert my inserts into two-piece units by cutting them as
illustrated. |
|
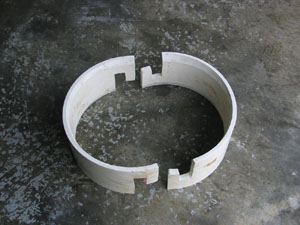 |
This way I get
a two-piece insert that will very easily go into, and come out of, the
tire, but because of the shape of the cuts, cannot come apart once placed
in the tire and installed on the rim.
By using this "jigsaw-puzzle"
pattern to make the cuts I also don't have to fiddle with screws, little
metal plates, and trying to screw two halves together once they're inside
the rim. They literally just snap together.
If you decide to do this -
be sure to cut both sides in the same direction, as shown. If you don't
it's very hard to get the halves back together. |
|
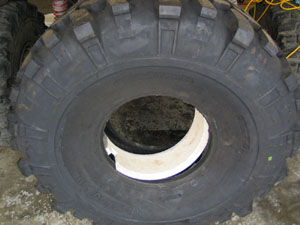 |
With the insert
in two pieces, both halves can easily be placed inside the tire... |
|
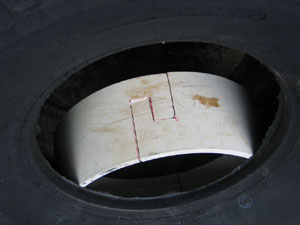 |
...and then fit
back together. |
|
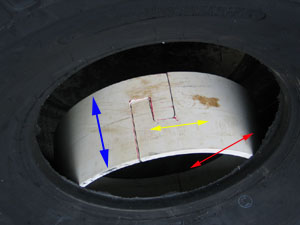 |
Once back together
inside the tire, the insert:
- cannot separate
laterally (blue arrow) because it's clamped together between the rim-halves
- cannot separate radialy
(red arrow) because the rim is in the middle
- cannot separate longitudinally
(yellow arrow) because the shape of the pieces at the join prevent this
|
|
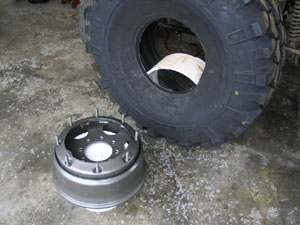 |
With the insert
inside the tire, place the inner rim-half on a bucket so that the back
side of the rim is sufficiently clear of the ground to prevent the tire
from touching the ground when it's laid over the rim.
I used an old drywall-mud pail. |
|
 |
Step
3: Install the tire and insert over the inner rim.
Lift the tire and place it
over the inner rim-half so that the insert slides over the rim as shown. |
|
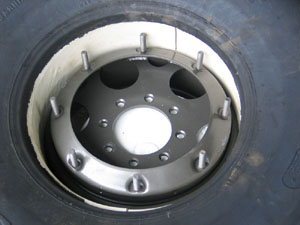 |
Wiggle the tire
around (or carefully use a screwdriver between the tire bead and the beadlock
insert) until the tire is centred on the insert.
Check that the O-ring is still
evenly in place and well lubricated. |
|
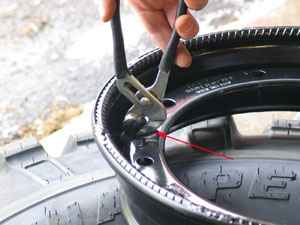 |
Step
4: Install the valve stem
Next, install the valve stem
in the outer-rim. There is, of course, a proper tool for
doing this. Which, of course, I didn't have. It's actually harder than
you might think, but I managed some success by using channel-lock pliers.
By leveraging the curved profile of the pliers against the rim (red arrow)
I was able to get them in place without mangling them too badly. Well
...three out of four isn't bad.
Tip: Have extra valve
stems on hand because, without the proper tool, it's hard to get them
in place without damaging them.
Tip 2: Generously
lubricating the valve stem with WD-40 considerably eases the installation. |
|
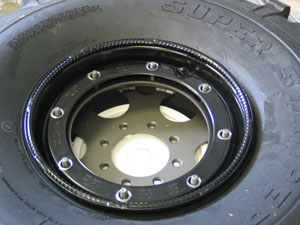 |
Step
5: Install outer rim-half
Place outer rim-half over the
studs and press down to seat it.
This pic shows my 42"
TSLs being mounted and you can see that there is plenty
of room to get the nuts started on the studs. |
|
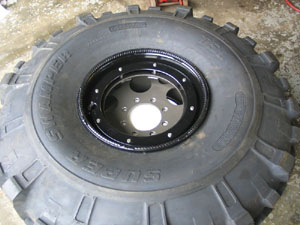 |
I'd heard of
some folks having problems getting the nuts started with larger tires
and I wanted to check this out for myself. I always try and make it a
habit to have as much first-hand experience as possible with what I'm
writing about.
In the interest of bringing
you the best information possible I borrowed a 44" TSL from the good
folks at National 4WD in Burlington, Ontario so that I could test-mount
it and check out the situation for myself.
As you can see, even with a
44" tire I had no troubles having enough threads to start the nuts.
Both 42s and 44s mounted and aired-up easily.
My thanks to the gang at National
4WD ( http://www.national4wd.com / E-mail: sales@national4wd.com) |
|
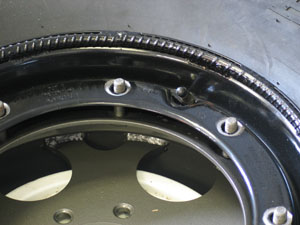 |
This illustrates
the size of the gap between the inner and outer rim-halves before you
torque the nuts down. |
|
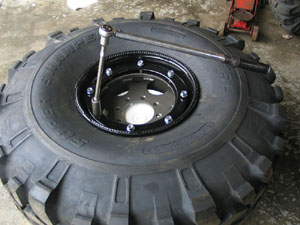 |
Step
6: Install and torque the clamp-nuts
It is very important to tighten
the nuts in several stages, in a star pattern, to evenly clamp the bead
and prevent warping the outer rim-half.
Torque specs are:
8 stud (bias) rim - Tighten
to 55 ft/lbs initially, then final torque to 65 ft/lbs
12 stud (bias and radial) rim
- Tighten to 85 ft/lbs initially, then final torque to 125 ft/lbs.
When finished, the gap between
the rim halves should be no greater than 1.5 thou (0.0015") |
|
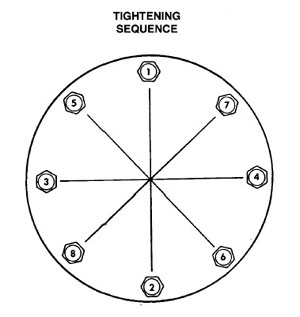 |
It is very important to do
the job properly as the 8 or 12 studs hold the entire wheel assembly together.
This diagram illustrates the proper tightening sequence. |
|
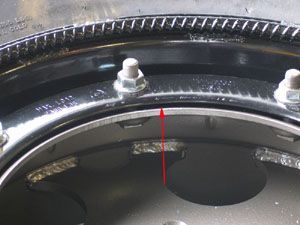 |
Gap reduces as
nuts are tightened.
The spec is 1.5 thou, which
for all practical purposes pretty much means touching. I actually got
out a feeler gauge to check - I think it was probably the first time I'd
ever used a 0.0015 feeler. It is, in technical terms, "very, very
thin".
If you are using 8-stud rims
and tires with extremely thick beads you may find that you reach the final
torque before the gap is less than 1.5 thou. In this case you have a decision
to make: allow a larger than spec gap or slightly over-tighten the nuts. |
|
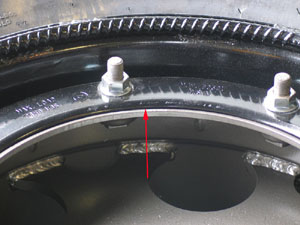 |
Getting closer
- but still far too much gap.
In my case, at 65 ft/lbs there
were just a couple of spots wider than 1.5 thou. I checked the max torque
values for 1/2"NF-20 fasteners and found them to be 53-73 ft/lbs
for Grade 5 and 81-103 ft/lbs for Grade 8.
Not knowing the exact grade
of the studs in question, I still felt quite comfortable going to 75 ft/lbs.
When I did, my gap was within spec. You will have to make your own decision
and proceed at your own risk. |
|
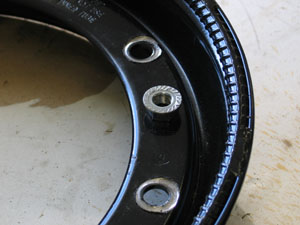 |
The only disadvantage
to the design, that I could find, is illustrated here. Due to the width
of the tire's beads, the torque specs, and the fact that the two rim-halves
must virtually touch: the clamp-nuts tend to gall the outer rim-half surface
quite badly. This is exacerbated by the fact that the underside of the
nuts have an almost "barbed" surface (to assist in preventing
vibrational loosening) - which tends to add to the tendency to chew up
the rim surface.
I considered using a large,
hardened, flat-washer between clamp-nut and rim, but decided against it
as this would negate some of the positive locking ability of the clamp
nuts.
In the end - I decided that
the most important thing was for the nuts to stay tight and consoled myself
with the fact that the rims should not have to come apart very often. |
|
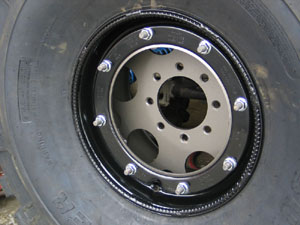 |
Step
7: Air-up the tire
Once the nuts are tightened
down you need only air-up the tire and you're done.
To get a good initial blast
of air to help seat the beads, I removed the valve cores and stuck the
quick-disconnect coupler of my air hose (with no air chuck) directly over
the valve stem .
The tires seated and aired-up
extremely easily. |
|
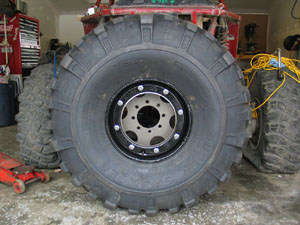 |
Finished tire
and rim assembly, ready to be mounted. |
|
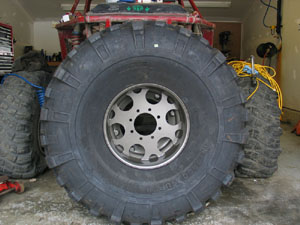 |
View from the
back side. |
|
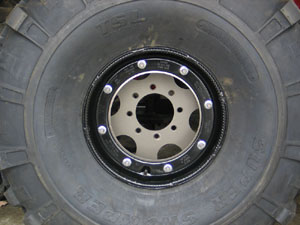 |
Close up. |
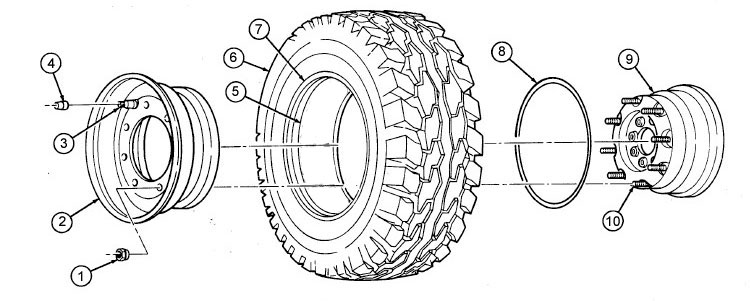 |
Diagram of the
complete assembly:
- Clamp Nut
- Outer Rim-half
- Valve Stem
- Valve Core
- Beadlock Insert
- Tire
- Tire Bead
- O-ring
- Inner Rim-half
- Stud
|
|
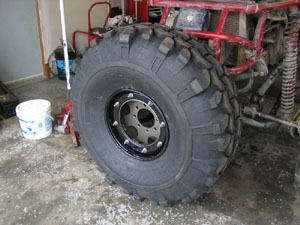 |
An awesome combo
- Super Swamper TSLs and Dean's custom Hummer double beadlocks! |
Update
Since first writing this article
Dean has stopped producing the PVC inserts and has instead moved to a custom,
laser-cut, steel version that he tells me "weighs only half as much, costs
less, and is much cheaper to ship."
I do not have any personal experience
with them but below are a couple of pics that Dean provided. You can get more
information by contacting Dean directly. |
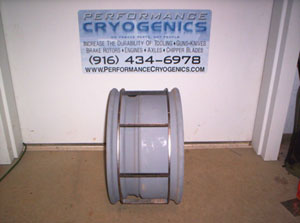 |
|
|
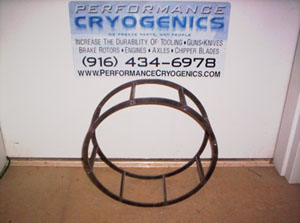 |
|
|
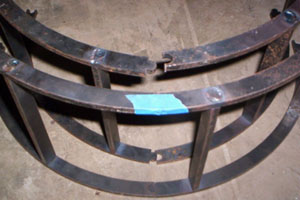 |
|
Conclusion
Custom Hummer beadlocks from Dean
Reed offer several advantages over other more traditional beadlocks and even
stock Hummer beadlocks, such as:
- Inner and outer beads are locked
- DOT stamped
- Available in any bolt-pattern
and a wide variety of backspacing
- Wheels assemble and disassemble
very easily - entire assembly can be broken down and tire changed in the field
with nothing more than a 3/4" socket, a screwdriver, and a pair of pliers
- Available with rock-rings to protect
outer lip of rim from rock damage
- Custom PVC inserts are lighter
than stock magnesium or rubber inserts and also place the weight closer to
the centre of the wheel
- Custom PVC inserts are the right
width for big offroad tires (stock magnesium inserts are near impossible to
install with very thick tire beads and can leak abundantly if you do get them
together)
- Custom PVC inserts have no "run
flat" portion that could damage tires at extremely low off-road pressures.
- Rims do not have 36 or more smaller
bolt heads at the very outside of the rim that can be damaged in the rocks
- If desired, they can easily be
balanced which is not often the case with traditional beadlocks
- Mount any tire available in 16.5"
diameter - from 33" all-terrains up to the bad-boy 44" Super Swampers
- Superb quality and craftsmanship
If you're in the market for quality
beadlocks and can use a 16.5" dia. tire - I really can't recommend Dean's
custom rims highly enough.
References:
For a ton of helpful information,
pictures, specs, and procedures check out Chapter 8 of the US MIlitary Hummer
Manual which I have compiled into one handy PDF document here:
|
|