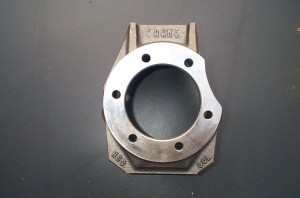 |
The HSC 60 Knuckles
are absolute works of art.
They are designed as replacement
knuckles for Chevy/Dodge style Dana 60s. You can see from the pic
the 6 bolt non-concentric GM spindle bolt pattern, and the semi-circular
"indentation cutout" (arrow0 for the large single piston GM/Dodge
style brakes. |
|
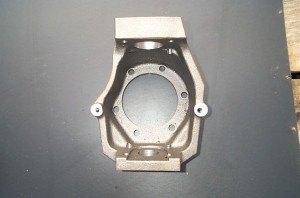 |
Massive chunks of cast Nickel-chromium-molybdenum
alloy steel.
DO NOT confuse the term "cast"
here - it is not short for "cast iron" as it is so frequently
used, it has nothing to do with the material - it is the process by which
the material is made into the useful shape.
This is very important, because
WAY too many people misuse the term, and will be heard saying things like
"I prefer steel to cast, because a cast part like that will just
crack/shatter when it breaks, whereas the steel will bend"
This is, of course, a gross
misunderstanding of the facts, and is completely erroneous. |
|
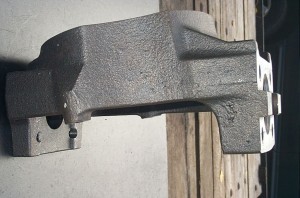 |
The knuckles will physically
fit on Ford axle end forgings (inner knuckles or C's). But the user
would have to swap to GM parts or go custom with:
- brakes
- spindle, wheel bearings,
and hub
- stub axle
Of course, this may be an ideal
upgrade anyway, if you're swapping to 35 spline Cr-Mo axles at the same
time, since you can just swap to Chevy stub shafts. |
|
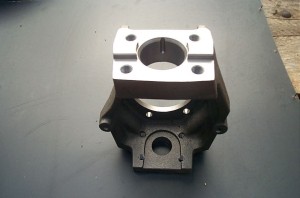 |
The material is ASTM A487.
Nickel-chromium-molybdenum alloy steel. The equivalent SAE
4 digit code for this material that we are more familiar with would be
8630.
That means it's like the chrom-moly
alloy steel we are more familiar with - but with the addition of Nickel
as a further alloying element.
The exact specifications are
as follows:
- Tensile Strength 105-130,000
psi
- Yield Strength 85,000 psi
- Brinell Hardness 235
- Percent Elongation 17%
|
|
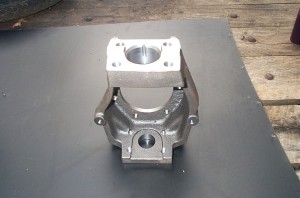 |
Perhaps a quick review of
alloying elements is required:
- Chromium Increases corrosion resistance, hardenability and wear resistance
- Molybdenum Deepens hardening, raises creep strength and hot-hardness, enhances
corrosion resistance and increases wear resistance.
- Nickel Increases strength and toughness
|
|
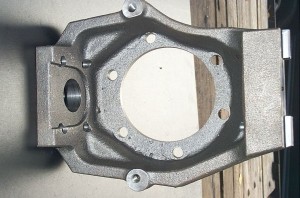 |
Here are some yield strength
numbers for comparison, taken from Taken from the 24th edition of the
Machinery's handbook, table 9 - Typical Properties of Selected Carbon
and Alloy Steels.
1030 being a typical plate
steel.
Recall that Yield Strength
is the point at which a material exhibits a strain increase without increase
in stress. This is the load at which a material has exceeded its elastic
limit and becomes permanently deformed.
1030 normalized 50,000 psi,
annealed 50,000 psi, quenched and tempered (1200°C) 64,000 psi |
|
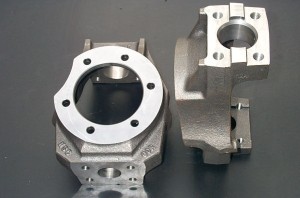 |
Comparing the numbers
for normalized, we see 50kpsi vs 85kpsi - that's a 70% greater yield strength!
It's clear then that this is
a vastly superior material to the plate mild steel or nodular cast-iron
that other alternatives are constructed from. |
|
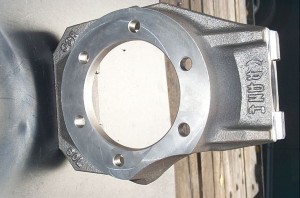 |
In addition to the superior
material, the process of casting the steel eliminates the need to weld any
parts of the knuckle together and therefore eliminates stress risers in
high stress regions. Also, in a fabricated/welded part you have to
be concerned with not only the selection of base steel and welding process
but also what edge treatment is used to eliminate the slag, sharp edge,
and maximize surface finish; what post weld heat treatment/stress relieve
is used to minimize the residual stress from the welding process; and all
of that has to be perfect - every weld, every time - and still you won;t
match the strength and uniformity of a cast alloy steel part. |
|
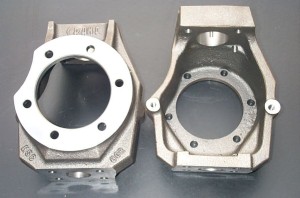 |
The casting also produces
a product with an even, consistent surface finish that is extremely important
in preventing stress raisers at the surface. Remember, stress raisers
lead to the formation of tiny cracks that will eventually lead to fatigue
and failure of the part.
In addition, these knuckles
can easily be welded, whether for customization or emergency trail repair
(like you're ever going to need that!). |
|
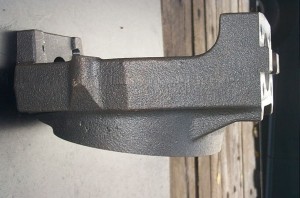 |
And finally, casting the part
allows for optimum, consistent fillet radii in the transition zone between
planes (translation - smooth curves allow stress to flow and not bunch up
and break things) as shown by the blue arrow - without expensive and time
consuming post-production machining. |
|
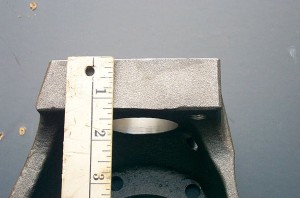 |
So we have so far, a part
that is superior to all other in material and manufacturing process, but
what about design?
Most notably, there is the
huge increase in strength and fatigue life created by the increased web
and flange thickness. A stock Chevy Dana 60 knuckle weighs approximately
16.5 pounds. The Crane knuckles weigh approximately 22 pounds.
When material, process, size
and shape are all taken into account it is extremely reasonable to estimate
that these knuckles are at least twice as strong as stock knuckles. |
|
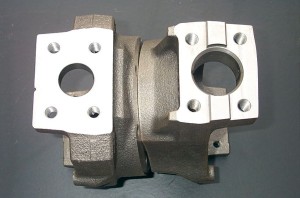 |
The post-casting machine work
is also top notch. |
|
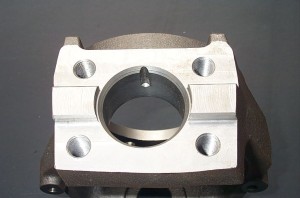 |
But by far the greatest innovation
of the Crane knuckles is the integrated high-steer indexing system.
There is a raised indexing
tab cast into the top of the knuckle. This allows for use of a matching
slot in the underside of the steering arm. If the parts are fit
together closely enough, this ingenious system relieves the fasteners
of the shear load caused by steering forces. |
|
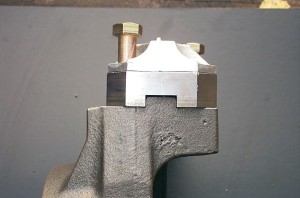 |
This indicates how the steering
arm and knuckle are "indexed" together, creating the strongest
possible joint at this critical place. |
|
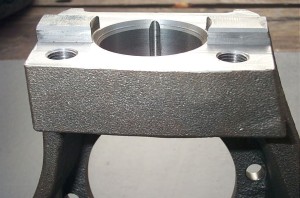 |
The idea is so simple yet
brilliant, it leaves the rest of us smacking our heads and muttering "Why
didn't I think of that?"
More on the closeness of fit
and steering arms later on. |
|
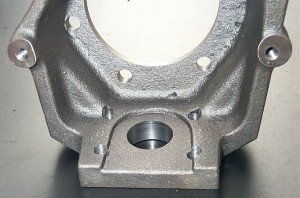 |
Continuing in the theme of
excellent, innovative features that prove that Crane not only listen to
customers needs, but as wheelers themselves understand what we want, the
Crane knuckles have this excellent feature:
Dual steering stops, as indicated
by the arrows. This allows not only finer tuning of turning angles,
which is critical with hydraulic steering and big axles/U-joints (like
my Superiors and CTMs), but also a stronger steering stop system, as two
sides will be working together to prevent further turning at full lock,
in either direction. This is again critical with powerful hydraulic
steering, and is key to preventing binding and possible destruction of
axle yoke, U-joint, and knuckle itself as happens when the knuckles are
over-steered. |
|
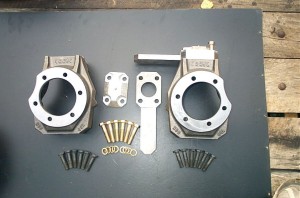 |
Here's a shot of the complete
knuckle and steering arm package from crane.
The knuckles and steering arms
are shipped uncoated, and must be painted or otherwise coated prior to
assembly and installation. |
|
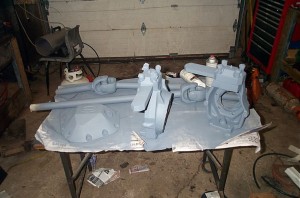 |
I used a 2 step process that
has worked well for me before (and that is all rattle-can - no painting
gear needed).
Step one is to prime the raw
steel parts with a high quality zinc rich self-etching primer. Not
to be confused with cheap grey primer - this stuff is 2-3x more expensive
but is the only stuff that will properly adhere to the raw steel. |
|
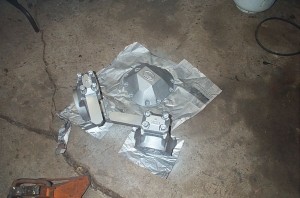 |
And for the top coat I chose
a groovy silver to show off the parts. This is "Detroit Diesel
Silver" industrial coating from Bowman. |
Compared
to the stock knuckles |
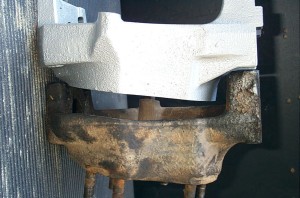 |
The extra beef is immediately
apparent when the stock knuckles are compared side by side. A stock Chevy
Dana 60 knuckle weighs approximately 16.5lbs. The Crane knuckles weigh approximately
22 lbs! |
|
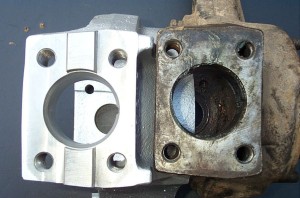 |
The Crane knuckles
also use 9/16-18NF threaded holes for retention of steering arms / upper
kingpin caps.
Assuming a grade 8 fastener,
this represents an increase in available clamping force of about 300 ft/lbs,
an increase in maximum tightening torque capacity of 30 ft/lbs and an
increase in shear strength from about 23,500 lbs to 29,800 lbs, or 21%
per fastener. |
|
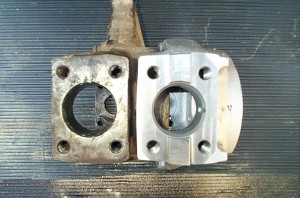 |
The lower bearing retainer threaded
holes are the stock 1/2-20NF and stock spicer bearing caps are used, along
with stock kingpin bearings and rebuild parts. |
|
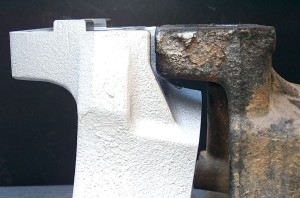 |
The area indicated by the
arrow is the critically stressed area on a Dana 60 steering knuckle.
This is where the stress concentrates as the steering forces act to try
to twist the top of the knuckle off. |
|
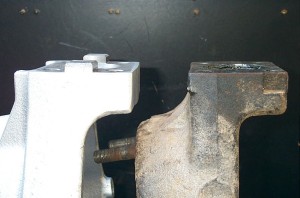 |
Notice not only the significant
increase in material in the Crane knuckle, but also note the radius at
the transition, chosen to minimize stress concentrations in the part. |
|
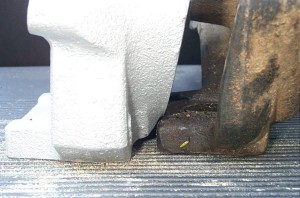 |
Every area possible is beefed
up compared to the stock parts. |
|
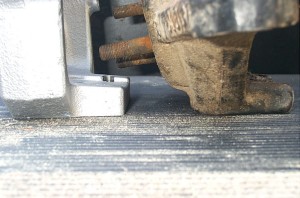 |
Thicker everywhere. |
|
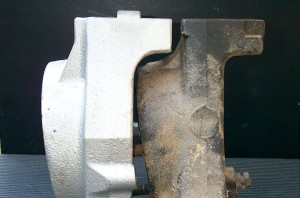 |
Note the extra wide vertical
"rib" , and the beefy steering stop in the Crane knuckle. |
|
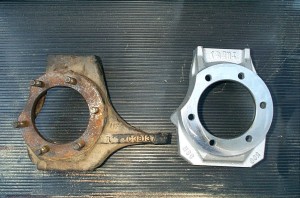 |
For those using high-steer
, the elimination of the useless stock "steering arm" gives
a nice clean appearance to the knuckle. |
|
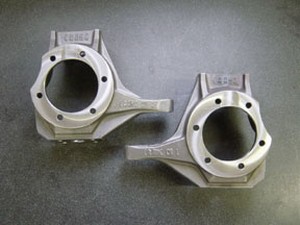 |
However, the Crane knuckles
are available in "classic" form, with stock Chevy location steering
arms and stock 1/2-NF threaded holes for the kingpin cap bolts/studs.
These "classic" 60
knuckles from crane also do not feature the high-steer indexing system,
and can easily be used with any existing dana 60 High Steer Arm. |
The
Steering Arms
Now we come to the Crane Indexed
Steering Arms. These are a brilliant idea, the execution of which is in
need of some improvement. |
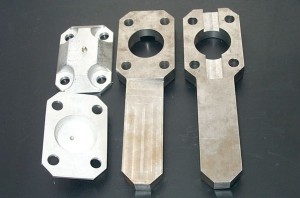 |
Here we see the basic design
of the arm. The arms are machined from a single piece of mild steel
that is initially 1 inch thick.
They fit over the kingpin bushing
and spring, and have a separate cast aluminium cap. The attachment
holes are straight-cut holes for 9/16" bolts. |
|
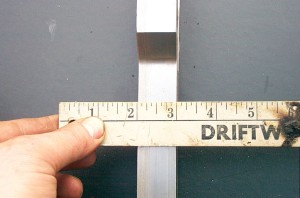 |
Thickest side of
arm is 1 inch thick. |
|
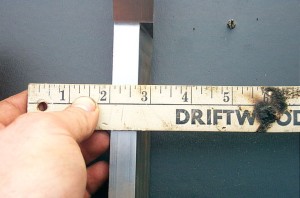 |
Thinnest side of arm is 5/8"
thick. |
|
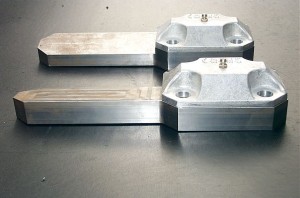 |
They have an angle machined
into the steering arm, that is intended to allow the "cancellation"
of the stock kingpin inclination angle, resulting in a horizontal surface
for the steering linkages rod end attachments. The theory is, that
by doing so, regardless of whether the steering linkage uses Heim joints
or standard automotive tie rod ends - by having the steering arm horizontal
at rest, the least amount of valuable misalignment angle available in
the joint is consumed in it's static mounting position.
This in turn would leave the
greatest amount of misalignment angle available for accommodating suspension
travel without binding the steering linkage. |
|
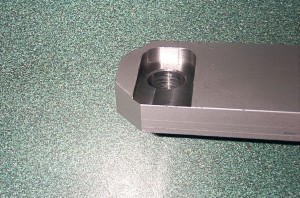 |
The theory is sound, and
a good idea, but the problem is, if you do this, BOTH sides of the steering
arm must remain parallel to one another - which they do not in the Crane
arms. This is because the head of the bolt and the nut must be parallel
to one another, you can't have either trying to seat against an angled
surface (in the case of a TRE, the tapered stud and nut must be perpendicular
to one another - the result is the same) and therefore - the 2 sides
of the arm must be parallel.
If you machine an angle into
one side of the arm, as in the Crane arms, you have to cut a slot for
either the nut or the head of the bolt. |
|
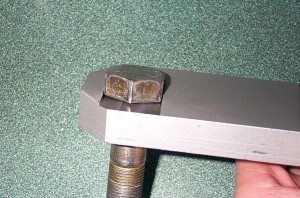 |
This is what I had to do
mount the arms, but is not a particularly good solution for 2 reasons:
- The removal of material
and therefore potential weakening of the arm, right where the concentration
of stress is high and you want it to be strongest. In order to
have parallel surfaces for nut and bolt head, the slot has to be cut
to a depth equal to the thinnest part of the arm - which is only 5/8"
- You can't properly machine
the slot yourself unless you have the proper machine tools. This
complicates the matter slightly from just having to bore the correct
diameter hole.
|
|
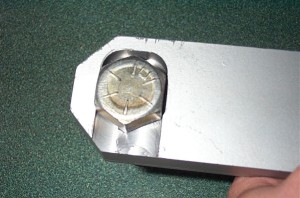 |
The much better way to eliminate
the stock kingpin inclination would be to start with a much thicker piece
of steel and mill both sides the same angle, eliminating the angle, but
leaving full thickness (an inch or so) and both sides of the arm parallel
to one another.
If it were determined that
this approach would involve too great an expense in material and time,
personally I would much prefer to simply have flat 1" thick arms,
rather than having them 5/8" thick around the hole and having to
mill a slot.
There is one neat benefit to
the "machine slot" approach though - you can machine the slot
just big enough for the bolt head and then not require a tool on the head
of the bolt during assembly or disassembly. |
|
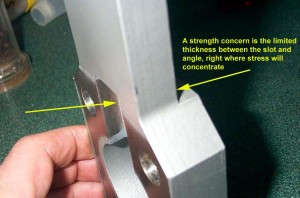 |
Finally, the machined angle
presents one last potential problem area. And that is the very limited
thickness left in the arm, right were the indexing slot overlaps the arm
where it is angled (yellow arrows).
Unfortunately, this happens
right where there is a major section change from the "body"
of the arm to the arm itself. As it is, this will be a highly stressed
area as the steering forces attempt to try and twist the arm off here.
The result is, the machined
angle leaves one side of the arm just 5/8" thick, and then on top
of that, the indexing slot in the arm removes even more material (I forgot
to get an exact measurement, but it's probably about 1/4" deep) leaving
the arm only about 1/2" thick at the thinnest part.
We shall see how they hold
up, but this doesn't seem enough for my tastes, and the prospect of a
steering arm failure on the trail is not a thrilling one. |
|
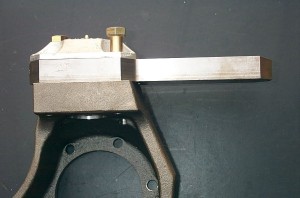 |
Installed on the knuckle
the arms look like this.
This side looks just the job... |
|
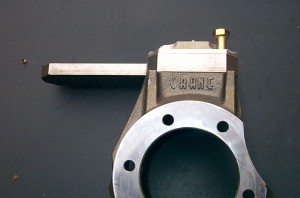 |
...but the "thin"
side looks, well, not as beefy as it could, and probably should, be. |
|
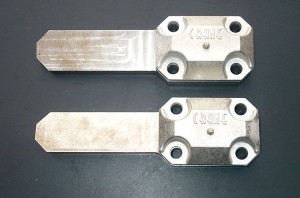 |
As for retention, the arms
themselves are retained with four 9/16-18NF fine thread SAE grade 8 bolts
and lock washers.
The 9/16" bolts are an
upgrade in size from the stock 1/2" fine thread, but the straight
holes in the arm and separate cap result in a lack of a true zero-clearance
fit for the fasteners.
Without either tapered nuts
(as in stock D60 hardware) or tapered, split cone washers (as in D44 style
hardware) there is a possibility of loose fit around the fasteners, leading
to relative motion between arm and knuckle, fatigue, and possible bolt
failure. |
|
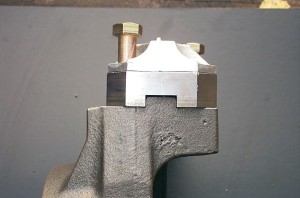 |
Of course - in this regard,
the Crane arm and knuckle combo is unique, and so the normal rules and
concerns don't apply exactly as they do to other arm and knuckle joints.
The ingenious indexing system,
consisting of the cast chrom-moly key on the knuckle and the matching
slot in the steering arm combine to ensure the strongest, slop-free union
possible in a joint of this kind.
The official tolerance on the
difference between the key and slot is plus or minus 0.001", with
the slot being just very slightly larger than the key. Technically
this is known as a transitional class fit. |
In practice, the mating between
arm and knuckle key is close, but not what I would describe as "tight".
The arm drops over the key with no persuasion required for assembly.
Once on the knuckle, with key indexed in slot, but no bolts installed,
there is just the teeny-tiniest perceptible wiggle. Install the bolts,
without even tightening them ,and the whole joint is tight and wiggle
free.
I have no practical concerns
that there will be relative motion between the arm and knuckle once installed
and torqued to spec - but, theory says it is possible, particularly if
the bolts loosen somehow. And we are talking about a desire for
the "best" - the ultimate. With that in mind, I would
personally prefer to see the key/slot fit be a true interference fit (with
the slot being 1-3 thou smaller than the key) and the joint require slight
force or heating for assembly. |
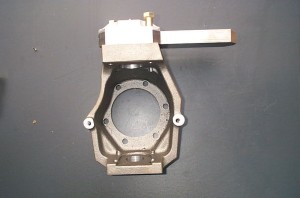 |
So in summary, we have:
Advantages:
- Brilliant indexed system
- exactly what a joint of this nature should have.
- Beefy 9/16" sized hardware
- Cool cast aluminium cap
- 1" thick steel "body"
Areas for improvement:
- Index system fit should
be tighter - a true interference fit
- Arm itself should be no
less than 1" thick at its thinnest point
- If inclination cancelling
angle is to be used, it should be machined into both sides, so arm isn't
thinner on one edge and so that bolt head and nut are parallel.
- For optimum design - fastening
system should incorporate studs and some sort of tapered fit (washer
or nut seat)
Overall a good first design
from Crane, with an innovative and extremely useful indexing system, that
could use some refinements. |
|
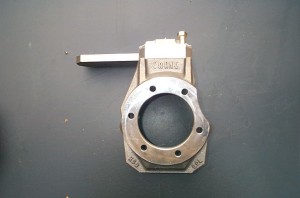 |
*** BREAKING NEWS ***
Here's the really cool thing
- I shared all of these initial opinions of mine with Tim Plamondon, one
of the key players at Crane High Clearance (who is, incidentally, a fourth
or fifth generation pattern maker [that's a dude who makes things from
molten steel!], a heck if a nice guy to talk to, with a keen interest,
super technical ability, and great customer service)
I also shared with him a few
other observations and design ideas I haven;t yet published here, as he
has agreed to work with me in designing and developing the ULTIMATE D60
high steering arm, one that can truly take it's place beside their great
knuckles.
Stay tuned - I will post results,
impressions, and more testing here as the project progresses. |
Installation
As I mentioned in part 2 of the BV-60
article, my intent was never to make this article a detailed installation article
- I'm assuming that we're pretty comfortable with axle R&R at this stage.
However, should you wish to review or study detailed information regarding the
building of a D60 front axle particularly swapping knuckles on a Dana 60 front
axle, that information is readily available in several other articles I have writen. You can check out:
My detailed article that covers the
whole process at:
Dana
60 front axle kingpin rebuild
Or, for more general dana 60 information:
The
original Spicer D60 front axle maintenance manual
The
one ton axle tech manual compiled from US military manuals
The
Dana light axle service manual (torque and setup specs)
The
Dana 60 Bible
With that - here are some pics and
notes from the installation of the Crane knuckles on the BillaVista-60 |
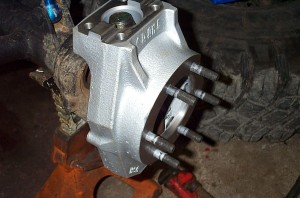 |
The 6 new spindle
studs are installed in the knuckle, and the knuckle installed on the axles
end forging. |
|
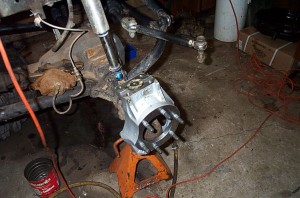 |
Kingpin nylon bushing installed
in top of knuckle. |
|
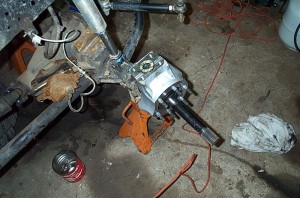 |
Superior cr-mo axle installed. |
|
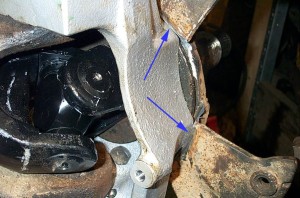 |
Here's a little something
I, as usual, didn't anticipate.
I have a "custom"
front brake setup on my front Dana 60. Instead of the stock brakes,
I use a 3/4 ton calliper and rotor, that requires a custom calliper bracket.
This custom bracket is really nothing more than the grafting together
of 1 ton and 3/4 ton brackets.
However, because if the extra
beef of the Crane knuckles, at assembly time, I found my custom bracket
would no longer fit flush against the spindle, due to slight interference
as indicated by the arrows in the pic at left. |
|
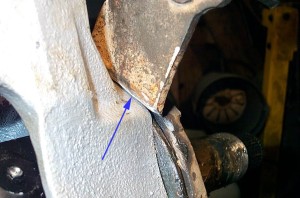 |
Slightly closer view of the
area in question. As you can see in the pic, I ground down the calliper
bracket as much as possible, but in the end... |
|
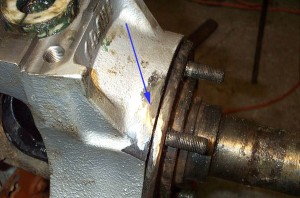 |
I just had to take my 4.5"
mini grinder and "tidy up" the knuckle just a tad.
You know, I discovered you
really don't know what kind of (wo)man you are until you have to take
a grinder to almost $1k worth of brand spanking new chrom-moly knuckles!! |
|
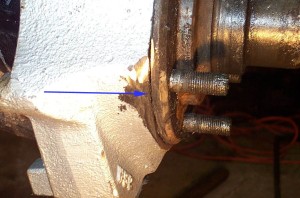 |
But it was really just a
very light smoothing, and I should emphasize, certainly no fault of the
Crane knuckles.
If you have stock 1 ton brakes,
everything will fit like a glove, no grinder required! |
|
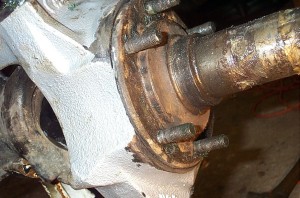 |
But if you do have some sort
of custom brake setup - you should be aware of the possibility....and
prepare yourself psychologically :-)
Here we can see everything
is tidied up nicely and I'm back in business. |
|
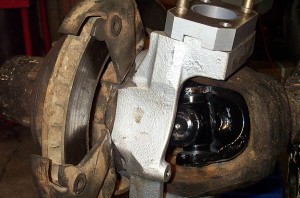 |
Custom brakes fitted up,
big fat Cr-mo knuckles, axle shafts, and U-joints
Ohhhh yeaaaa baby! |
|
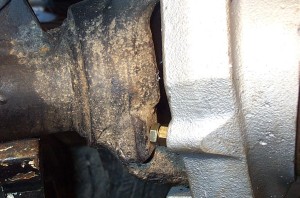 |
Steering stop being adjusted
and tested. I used a grade 8 bolt with an extra nut for locking. |
|
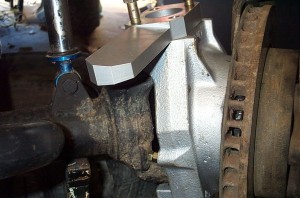 |
Un-machined steering arms being
test-fit. You can clearly see the angle in the arm cancelling the
kingpin axis inclination. |
|
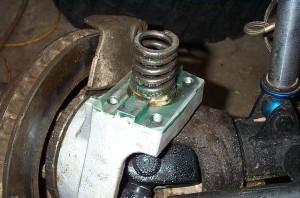 |
Kingpin spring and spring retainer
installed. |
|
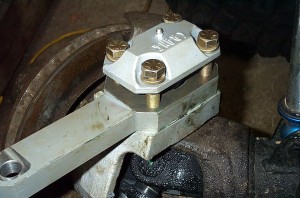 |
Kingpin cap being installed. |
|
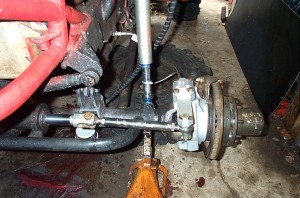 |
The finished package, ready
to rock. |