Basic Tire
Tech
What is a tire and what
does it do?
On the face of it, it's
quite simple. A tire is just a rubber air bladder that contains pressurized
air to support the vehicle's weight, right? Well, yes...but it also transmits
acceleration, braking, and cornering forces to the road or trail, and acts as
a spring between the trail and the wheel.
It's able to do all this because
of the way it's constructed. You see, a tire isn't just a rubber balloon - it
has a carcass made of plies (or layers) that give it shape, strength, and stability
(otherwise when filled with air it would just expand in a wobbly and uselessly
round fashion like a balloon tire in a kid's picture). It has a steel bead to
clamp it to the rim with sufficient friction to transmit acceleration and braking
from the rim to the trail and vice versa. It has tread blocks to grip the road
and trail, tread voids to shed mud, snow and water, and it can have cap-plies
or steel belts under the tread to stabilize the tread and reduce punctures.
The plies themselves are made of chords of fibrous material (polyester, fiberglass,
nylon, rayon, steel mesh, kevlar, etc.) woven together and coated with rubber.
It is the plies in a tire that give the tire shape and strength and prevent
it from expanding like a balloon, thus allowing the build-up of load supporting
pressure.
What are the parts?
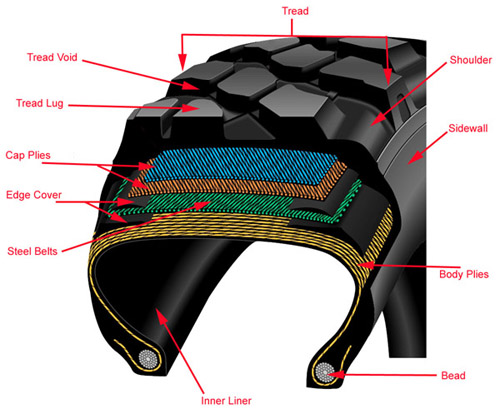
The major parts of a tire are as
follows:
Body: The body,
also known as the carcass or casing, is the core of the tire. Made up of body
plies, it is beneath the tread and inside the sidewalls.
Chords: Lengths
of fibrous material (polyester, kevlar, nylon, etc.) that lie at the heart of
a ply.
Ply: A fibrous,
fabric layer made from chords woven together and coated with rubber.
Body Plies: Layers
of rubber-coated fabric that form the body of the tire.
Cap Plies: Optional
extra layers of fabric used for circumferential reinforcement in high-speed
tires.
Bead: High-strength,
rubber-coated, steel cable that clamps the tire to the rim.
Tread: A compound
of many natural and synthetic rubbers and other components that contacts the
road.
Tread Lug: Raised
segment of the tread.
Tread Void: A
gap or space in the tread to allow the shedding of mud, snow, and water.
Sidewall: The rubber
between the tread and the bead, it provides lateral stability for the tire and
protects the body plies.
Shoulder: The area
where the tread and sidewall meet.
Inner liner: The
innermost rubber layer in a tubeless tire that helps to make it air-tight.
Steel Belts: Belts
of steel mesh that lie under the tread to provide puncture resistance and keep
the tread area flat for maximum road grip.
Edge Cover: Optional
special circumferential reinforcements above the steel belts found in high-speed
tires. Also called belt edge strips.
Essentially, a tire is made as follows:
- The beads are formed from steel
cable
- Body plies are made from rubber-coated fabric cords
- The carcass is made from body plies stretched from bead to bead
- Optional steel belts and/or cap plies are added on top of the casing (depending
on design)
- The tread and sidewall rubber are moulded on
- The inner liner is added.
Dimensions
To have a meaningful discussion about
tires, in addition to knowing the names of all these parts, there are some important
dimensions of a tire that we must know. These are illustrated and described
below:
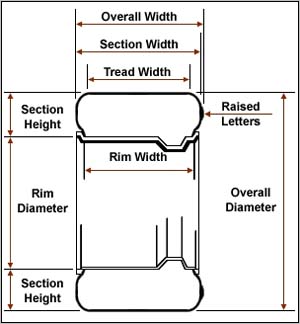 |
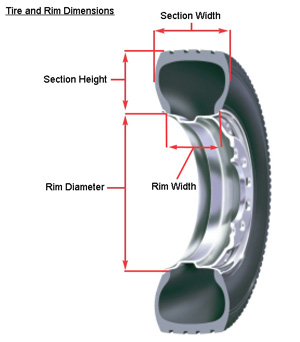 |
Overall Width:
The distance between the sidewalls of a tire when it is, mounted on the design
rim*, inflated, and unloaded; including any protruding side ribs, raised
lettering or decorations.
Section Width:
The distance between the sidewalls of a tire when it is, mounted on the design
rim*, inflated, and unloaded; exclusive of protruding side ribs, raised
lettering or decorations.
Tread Width:
The width of a tire's tread at the point where it comes into contact with the
road, i.e. the width of the contact patch.
Section Height:
The distance from rim seat to outer tread surface of a mounted, inflated and
unloaded tire.
Rim Diameter:
Diameter of the rim measured at the bead seats.
Rim Width:
Distance between the two opposite inside edges of the bead seats.
Overall Diameter:
The diameter of the inflated tire, mounted on the design rim*, unloaded.
Note: Overall Diameter = Section Height X 2 + Rim Diameter
* Since a tire's section width
and diameter changes depending on the width of the rim on which it is mounted
(the tire gets wider and shorter if mounted on a wide rim, and narrower and taller
if mounted on a narrow rim), each tire is measured on a specific rim width,
called the "design rim". For tires with aspect ratios between 50 and
80, the design rim width is usually 70% of the tire's section width. For tires
with an aspect ratio less than 50, the design rim's width is normally 85% of
the tire's section width.
Aspect Ratio: There is another dimension of a tire
that is useful to know - though strictly speaking it's a calculation rather
than a true dimension. It's know as the tire's Aspect Ratio.
Aspect Ratio = Section
Height divided by Section Width
Aspect Ratio is the relationship
of a tire's height to width when mounted and inflated on a rim of correct size.
Aspect ratios are expressed as a two digit percentage such as 80, 70, 60 etc.
This number, as a percentage, means the height of the tire's sidewall (its Section
Height) is x% of its width. Aspect ratios are also often referred to as the
tire's 'series'. For example, if section height/section width is 0.60 (60%),
the tire is a 60 series tire.
Why do we care about a tire's Aspect
Ratio? Because the height to width relationship determines the shape of the
tire on the rim, and, more importantly, determines the performance characteristics
of the tire. If the sidewall height of a tire is reduced slightly, the sidewall
stiffness is increased greatly. Higher Aspect Ratios deliver greater deflection
under load and a softer ride. Lower aspect ratios deliver a wider footprint,
quicker response, less slip angle, lower flex rate, less deflection and a harsher
ride. Also, typically, a high aspect ratio tire will have a long, narrow footprint,
while a low aspect ratio will have a short, wide footprint. At least that's
all true in the street-car world. Things are a little different for us because
the amount by which we air down our tires overrides the Aspect Ratio in determining
the tire's footprint and responsiveness.
Construction - Radial,
Bias Ply, and Bias Belted
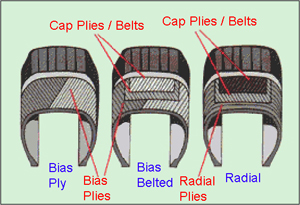
There are 3 basic types of tires,
named for the 3 main ways of constructing a tire, differentiated by the way
the body plies are oriented. They are:
Bias Ply tires,
Radial tires, and
Bias Belted tires.
Bias Ply
The body plies in a bias ply tire
are laid down at an angle (or bias) to the centerline of the tread, and are
stacked one upon the other in a multi-layer criss-cross fashion. These criss-crossing
layers are generally oriented 32 to 40 degrees from the centerline of the tread.
Since the chords that make up the plies are fibers, they are strong in tension
but have no strength in compression. This is why the plies are laid down at
a bias and on top of one another - to give the tire its strength in both directions
- and is also why there are always an even number of body plies in a bias ply
tire. The body plies are frequently made of nylon chords but other materials
can be used. Nylon is very strong but is also very stiff. These stiff, strong
layers must essentially scissor against each other as the tires flexes which
builds heat, causing the tire to run hotter than a radial. Over time, heat degrades
a tire. That said - this building of heat is really only an issue in sustained
road driving at speed. Bias ply tires also do not have cap plies or steel belts
under the tread - as a result, when the tire is loaded by the vehicle the chords
are stretched and the entire body supports the weight. Since there are no other
layers under the tread, the tread tends to be slightly rounded, creating a smaller
contact patch (relative to a same-size radial) that reduces road handling. Because
of our practice of airing down this reduced contact patch is of no concern off-road.
On the other hand, since bias body plies run from bead to bead there is no transition
from a circumferential belt to sidewall - the tread and sidewall construction
are the same. As a result, tread can be wrapped around and down the sidewalls
of a bias ply tire for extra traction and protection - the perfect example of
which is the Pitbull Rocker- a tire not offered in radial design.
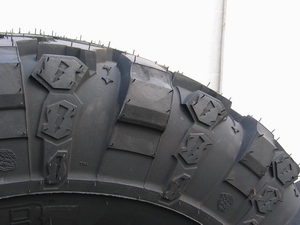
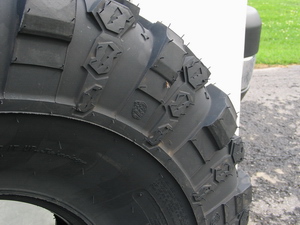
|
Extensive sidewall
tread on the Pitbull Rocker - possible because of its bias ply construction. |
The overlapping, criss-cross plies
of a bias ply tire results in a carcass and sidewall that are thick, stiff,
and strong. This very strong sidewall more easily withstands trail hazards and
punctures than a radial design (where all the chords run in the same direction,
are generally made of weaker, more flexible polyester, and there are fewer plies).
This is not only because the multiple plies result in a great thickness (making
it harder to penetrate completely), but also because of the alternating angles
of the bias ply. If an injury does occur in the sidewall of a bias ply tire
it is much less likely to completely rip or tear (called a "zipper")
than radial tire. Imagine it like this: take 2 wooden boards and glue/bond them
together with the grains running in the same direction. Now strike the top edge
with an axe - they will split readily....the zipper! Now, bond the same two
boards together again, but this time lay one on top of the other at an angle
(a bias) of 30-40 degrees. They will now resist splitting completely when struck
with the axe - just like the overlapping body plies in a bias ply tire (when
abused offroad - not hit with an axe, of course!)
A bias ply tire can be aired down
lower than an equivalent radial tire. This is because the heavy-duty sidewalls
of a bias ply tire also help support the load more than in a radial. Remember
that the plies criss-cross across a bias ply tire. One layer is strong in the
weak direction of another. As the tire is compressed and flattened by the load,
some of the cords are put under tension where the great tensile strength of
nylon results in the sidewall supporting the load in conjunction with the air
pressure inside the tire - the result being we need less air pressure in the
tire to support the load.
Bias ply construction also presents
two additional characteristics - neither of which are of any real concern in
a hardcore trail rig. Due to their weight and lack of steel belts or cap plies,
bias ply tires tend to be less fuel efficient for highway use than radial tires.
Also, nylon has a tendency to take a set when statically loaded, especially
when cold, resulting in the "square tire" syndrome.
Radial
There are two main differences in
the construction of radial tires compared to bias ply tires that account for
their dramatically different on and off-road performance characteristics: the
orientation of the body plies and the addition of steel belts and/or cap plies
under the tread.
In a radial tire the body plies are
laid down perpendicular to the center line of the tread - they appear to radiate
from the center line - hence the name "radial". There are also usually
many fewer body plies than in a bias ply design - up to a maximum of 3 compared
to the up to 16 used in a bias ply tire. In fact, a radial tire needs only one
body ply, and thus is not only less stiff, but runs much cooler, and weighs
less. If more than one body ply is used , successive body plies are layered
over the existing ones with all the chords being parallel. In addition, the
body plie(s) of a radial tire are generally made of polyester which is softer
and not as tough or strong as the nylon common in bias ply tires.
Radial tires also use a wide variety
of cap plies and/or steel belts under the tread. These belts are placed in successive
layers circumferentially around the casing, under the tread. They are independent
from the body plies, are made from a variety of materials (including steel,
fiberglass, and nylon) that are different from the materials used in the body
plies, and so cause a discontinuity where the sidewall and tread meet. Each
belt adds an additional layer in the tread area but leaves the sidewall area
untouched.
This belted radial design, this discontinuity
between sidewall and tread, results in the tread being independent from the
sidewall - the steel belts provide a stable foundation for the tread allowing
the sidewall to be more flexible. In a radial tire sidewall flexing does not
alter tread pattern. As the tire flattens out under loads or impact, the sidewall
plies just bend, adding very little resistance.
The following diagrams illustrate
the difference between bias ply and radial tires in terms of the effect of sidewall
flexing on tread stability and contact patch.
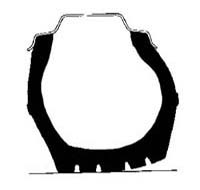
Thick, stiff, bias ply sidewalls, integrated with the tread, mean that
as the sidewall flexes (as in a cornering load) the tread is affected
and the contact patch negatively impacted. |
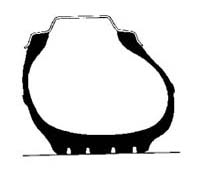
In contrast, the flexible,
independent sidewalls of a radial flex under loads (as in cornering) and
allow the belts to keep the tread flat and stable.
|
The combination of the radial pattern,
softer polyester material, and use of belts (independent tread and sidewall)
gives a radial tire more sidewall flex which allows the tire to absorb road
shock and noise thus producing a much smoother ride. The softer polyester chords
also resist flat-spotting much better than the stiff nylon chords in a bias
ply - especially in the cold. On-road it also results in the load being distributed
equally across the contact area as well as better traction with less heat build
up resulting in longer life and improved fuel economy. By restricting tread
movement during contact with the road, the belt plies improve tread life. In
addition steel belts protect the casing under the tread against high-speed impacts
and punctures.
However, the sidewall is generally
weaker on radial tires than on bias tires when it comes to puncture and damage
resistance. Part of this is due to fewer body plies and less rubber being used,
and part is due to the fact that, in a radial tire, even a small injury can
lead to massive tear because the body plies have all their chords running parallel
to one another.
Also, since the radial sidewall adds
very little stiffness (indeed is designed to be much more flexible), as can
be seen in the distinctive radial tire "bulge", the load is almost
entirely carried by the air and thus radial tires cannot be aired down as low
as bias ply tires carrying the same load.
In addition, the discontinuity between
tread and sidewall in a radial tire is the reason radial tires don't have substantial
sidewall tread. Because the radial design depends on thin, flexible sidewalls
it defeats the purpose to add significant rubber tread to the sidewall, and
doing so would cause a lot of heat buildup from radial sidewall flexing. In
any case, even if some form of tread is added to the sidewall of a radial their
will still be a break in the transition from tread to sidewall.
Other components found in a radial
tire but not in a bias ply are bead chaffers and cap plies - usually built into
performance tires to enhance cornering and stability at high speeds.
Bias Belted
Bias belted tires are a hybrid combination
that have criss-cross bias body plies like a bias ply tire, combined with cap
plies / steel belts like a radial tire. Frequently the belts and body plies
are made from different materials. For example, a polyglass tire may have polyester
plies and fiberglass belts. Bias belted tires have a wider tread area than the
bias ply - providing better traction and stopping power. They also have more
flexible sidewalls than the bias ply, resulting in less internal heat buildup
during driving and consequently greater tread life. On the surface they may
seem like an ideal compromise - a way to combine the benefits of both radial
and bias ply design. However, they of course also combine the weaknesses of
both designs. I believe this is the reason they have never really caught on
and are all but nonexistent in the market place - very few bias belted tires
are manufactured today. This is probably due to the fact that both bias ply
and radial tires fit their niche, accomplish their goals, so well that the potential
consumer of either is not willing to compromise either with a hybrid tire. Those
seeking tough, durable off-road tires with maximum sidewall strength and tread
will choose bias ply tires - those seeking on-road performance, tread-life,
and handling will choose radial tires.
Which One to Choose?
Virtually all street/car tires sold
are radials due to their superior handling, ride quality, and wear. Radial construction
allows the tire to better flex and absorb the irregularities of the road surface.
The radial design also produces much less friction resulting in cooler running
tires and much longer tread life.
But bias ply tires refuse to disappear
from the market. The overlapping, criss-cross reinforcement design of bias ply
tires makes them very durable. Since the sidewall is as strong as the rest of
the body, it can withstand lateral loads, twisting, and bending which would
cause a radial to split - especially in an aired-down tire. This strength and
durability of the bias ply construction is also a benefit in high torque conditions
like when a spinning tire suddenly gets traction. Also because of the one-piece
tread/sidewall design, much more aggressive and functional tread can be added
to the sidewall of a bias ply tire.
The following diagram and table summarize
the strengths and weaknesses of radial and bias ply construction:
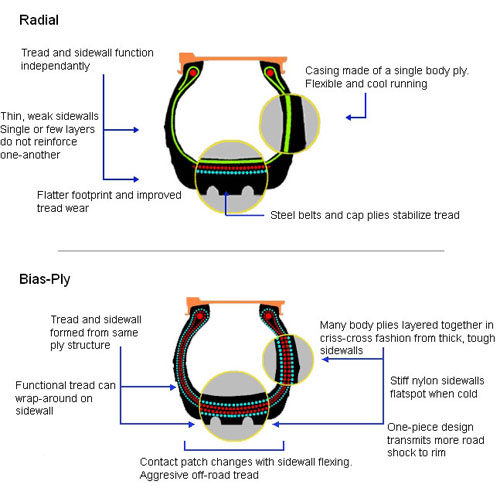 |
Bias
Ply |
Radial |
+ |
- |
+ |
- |
Tough, durable sidewalls. |
Flat spot when statically loaded. |
Don't flat spot when statically
loaded. |
Weak, flexible sidewalls. |
Functional sidewall tread -
sidewall tread blocks help protect the sidewall and add traction to climb
out of ruts and up rocks. |
Stiff when cold. |
Not as affected by cold. |
Susceptible to sidewall splitting
- chords do not reinforce each other. |
Can be aired down lower for
larger footprint and better flotation - stiffer sidewalls bulge less |
Transmit shock. |
Softer ride. |
Weak sidewalls can bulge out
quite far, exposing them to danger. |
Body plies criss-cross and reinforce
each other. |
Integrated sidewall / tread
causes a rounded tread - reducing traction and directional stability (on
street). |
Squarer, flatter tread - better
directional stability (on street). |
No aggressive, functional sidewall
tread. |
Nylon construction stronger
and more abrasion resistant than polyester. |
Sidewall flexing affects tread
contact patch. |
More stable tread, not affected
by sidewall flex. |
Polyester construction not as
tough and abrasion resistant as nylon. |
Can withstand lateral loads
from rocks and roots without splitting. |
Scissoring of bias plies as
sidewalls flex builds heat quickly. |
Better, more stable handling
and cornering. |
Must be maintained at higher
air pressures to carry equivalent load. |
Can survive abuse that would
destroy a radial. |
Require strict attention to
air pressure if run on-road. |
Steel belts give good protection
to tread area. |
Because of separate tread/sidewall
design, susceptible to tread separation (the tread rings or "alligators"
trucks are always shedding on the highway). |
Because of their acknowledged
on-road limitations can be uncompromisingly designed with extremely aggressive
treads for excellent off-road traction. |
If run on-road at high speeds,
susceptible to ply separation because of heat build up. |
Run cooler, longer life. |
|
|
|
Better tread wear, improved
fuel efficiency. |
|
Summary
Bias ply tires are the clear choice
for serious off-roading because of their sidewall strength, aggressive tread,
and ability to be run at low single-digit pressures. For serious, hardcore trail
riding, the strength and durability of the bias ply trumps all - after all,
when you're wheeling brutal terrain miles from nowhere the best tire is the
one that still holds air!
Radials are the best choice for on-road
driving because of their softer ride, improved handling, and longer tread life.
If you drive both on- and off-road
you have to decide which is more important - the road manners of the radial
or the toughness of the bias ply. Me - I'll compromise road manners for trail
performance every time. If you're compromising, whichever you choose, there
are a couple of precautions to note:
- When running a bias ply tire on
the street, strict attention must be paid to tire pressures. The stiff sidewalls
can easily disguise an under-inflated tire. Street driving even slightly under-inflated
bias ply tires can be hazardous because the scissoring body plies already build
a lot of heat - this is exacerbated by under-inflation to the point that the
tires can quickly build enough heat to cause ply separation and catastrophic
tire failure.
- Radials tires, of course, also
need correct air pressure on the street. Excessive heat in a radial tire leads
to sidewall cracking, zipper blowouts, and the tread separating from the casing
(those rings of tread, or "alligators" you see on the side of the
highway are most often the result of radial truck tires, especially retreads,
suffering this heat-induced tread separation). Off-road, radials will require
more air pressure than bias ply tires to avoid excessive sidewall bulge which could otherwise lead to sidewall splitting or the sidewall getting pinched between the rim and a
rock.
Tire FAQ
What’s the best way
to replace a single tire or pair of tires on a vehicle?
- Never mix radial and bias ply
tires on the same axle (because of their different handling characteristics
discussed earlier in this article)
- If you have radials on one axle
and bias ply on another, run the radials on the rear
- If you are replacing a pair of
tires, put the new ones on the rear
- If you have to replace just one
tire, pair the new one with the best of the other three and run them on the
rear
What is the maximum weight
it should take to balance my tire?
The industry standard is approx.
2% of the tire weight.
What are tires made of?
The average steel-belted radial
tire is made up of:
- 28% Carbon Black
- 27% Synthetic Rubber
- 14% Natural Rubber
- 10% Steel Wire
- 10% Extender Oil
- 4% Organic Fiber
- 4% Other Petroleum Products
- 3% (S, ZnO, Ti02, etc...)
How round is round?
Generally, a passenger-car tire
is considered round if it has less than 0.030" radial or lateral runout.
An LT tire is considered round if it has less than 0.060" radial and lateral
runout.
Does it matter how I mount
the tire on the rim?
There are two schools of thought
on this.
The first has that you should mount the high-spot of the tire (often indicated
by a red dot) aligned with the low-spot of the rim (often the valve hole, but
may be separately indicated, depending on the wheel in question).
The other method is to mount the lightest spot of the tire (often indicated
by a yellow dot) aligned with the heaviest spot on the rim (the valve).
What effect do different rim widths have on my tires?
The wider the rim, the greater the
section width. Section width increases about 0.4” for each additional
inch of rim width (and vice versa).
A wider rim increases the distance between the beads, which results in a straighter
sidewall, which stiffens it. The straighter sidewall also exposes the rim, making
the wheel more susceptible to damage.
A narrower rim pulls the beads closer
together, curving the sidewalls. This increased curvature allows the sidewall
to flex more readily. It can also help with bead retention at lower air pressures,
although using narrow rims is no substitute for beadlocks.
Why do race teams use Nitrogen
in their tires instead of air?
Race cars, aircraft, and other ultra-high
performance machines use Nitrogen in their tires instead of air because, when
heated or cooled, nitrogen has a much more consistent rate of expansion and
contraction than air.
This is because air contains varying amounts of moisture due to changes in the
relative humidity. This water vapour causes air to be inconsistent in its rate
of expansion and contraction.
What is the difference between
an LT and P tire of the same size?
LT tires that are load range C or
greater tend to be rougher riding and noisier than their P-Metric counterparts
and more expensive since the LTR size equivalent to the P-Metric has heavier
body ply construction and the tread lugs are generally more aggressive.
P and LT tires are also often rated slightly differently. If P-rated tire is
used in an LT application, you need to de-rate the sidewall load capacity by
9% - 10%.
How should I store unmounted
tires?
- Store them on their sides in a
clean, cool, dry, dark, and well-ventilated area (but with a minimum of circulating
air).
- Keep them out of direct sunlight.
- Keep them away from sources of
ozone such as operating welders and electric motors. Store tires away from
the furnace, sump pump, power tools, etc.
- If you must stack them, do so
only to a height where the bottom tire retains its shape, usually no more
than four high.
What about tires on my rig
in storage?
- Store the vehicle on blocks to
remove all weight from the tires.
- If the vehicle cannot be blocked
up, completely unload it so minimum weight will rest on the tires. The surface
should be firm, reasonably level, well drained, and clean.
- Keep tires inflated to recommended
operating pressure.
- Move the vehicle at least every
three months to prevent ozone cracking in the bulge area, to help maintain
oil dispersion within the rubber compounds, and to prevent a "flat spot"
from developing.
|